發展簡史
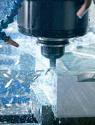
1907年美國人F.W.泰勒研究了切削速度對刀具壽命的影響,發表了著名的泰勒公式。1915年,俄國人烏薩喬夫將熱電偶插到靠近切削刃的小孔中測得了刀具表面的溫度(常稱人工熱電偶法),並用實驗方法找出這一溫度同切削條件間的關係1924~1926年,英國人E.G.赫伯特、美國人H.肖爾和德國人K.科特文各自獨立地利用刀具同工件間自然產生熱電勢的原理測出了平均溫度(常稱自然熱電偶法)。
1938-1940年美國人H.厄恩斯特和M.E.麥錢特利用高速攝影機通過顯微鏡拍攝了切屑形成過程,並且用摩擦力分析和解釋了斷續切屑和連續切屑的形成機理。40年代以來,各國學者系統地總結和發展了前人的研究成果,充分利用近代技術和先進的測試手段,取得了很多新成就,發表了大量的論文和專著。例如,美國人S.拉馬林加姆和J.T.布萊克於1972年通過掃描電鏡利用微型切削裝置對切屑形成作了動態觀察,得到用位錯力學解釋切屑形成的實驗根據。
形成和變形
1、切屑形成機理
從力學的角度來看,根據簡化了的模型,金屬切屑的形成過程與用刀具把一疊卡片1、2、3、4、……等推到1、2、3、4、……等位置的情形相似,卡片之間相互滑移即表示金屬切削區域的剪下變形經過這種變形以後,切屑從刀具前面上流過時又在刀、屑界面處產生進一步的摩擦變形。通常,切屑的厚度比切削厚度大,而切屑的長度比切削長度短,這種現象就叫切屑變形。金屬被刀具前面所擠壓而產生的剪下變形是金屬切削過程的特徵。由於工件材料刀具和切削條件不同,切屑的變形程度也不同,因此可以得到各種類型的切屑。
切屑的形成過程是被切削層金屬受到刀具前面的擠壓作用,迫使其產生彈性變形,當剪下應力達到金屬材料屈服強度時,產生塑性變形。隨著刀具前刀面相對工件的繼續推擠,與切削刃接觸的材料發生斷裂而使切削層材料變為切屑。
切屑的變形和形成過程實際上經歷了彈性變形、塑性變形、擠裂、切離四個階段。
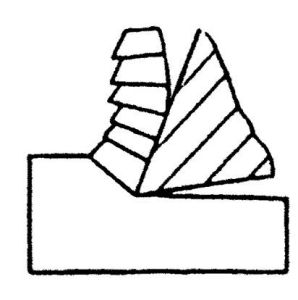
2、切屑的類型
(1)帶狀切屑
外形特徵:它的內表面是光滑的,外表面是毛茸茸的。
形成條件:用大前角的刀具、較高的切削速度和較小的進給量 切削塑性材料。
優 點:切削過程平穩,切削力波動較小,已加工表面粗糙度較小。
缺 點:切屑連續不斷,不太安全或可能擦傷已加工表面,因此要採取斷屑措施。
(2)擠裂(節狀)切屑
外形特徵:刀屑接觸面有裂紋,外表面是鋸齒形。 形成條件:採用較低的切削速度和較大的進給量,刀具前角較小,粗加工中等硬度的鋼材料 特點:切削力波動較大,工件表面較粗糙 。
(3)崩碎切屑:在切削鑄鐵和黃銅等脆性材料時,切削層金屬發生彈性變形以後,一般不經 過塑性變形就突然崩落,形成不規則的碎塊狀屑片,即為崩碎切屑。
當刀具前角小、進給量大時易產生這種切屑,產生崩碎切屑時,切削熱和切削力都集中在主切削刃和刀尖附近,刀具易崩刃、刀尖易磨損,並容易產生振動,影響表面質量。
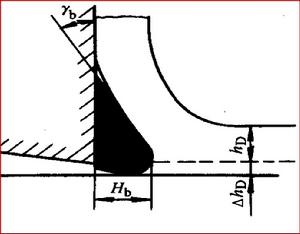
3、積屑瘤
在用低、中速連續切削一般鋼材或其他塑性材料時,切屑同刀具前面之間存在著摩擦,如果切屑上緊靠刀具前面的薄層在較高壓強和溫度的作用下,同切屑基體分離而粘結在刀具前面上,再經層層重疊粘結,在刀尖附近往往會堆積成一塊經過劇烈變形的楔狀切屑材料,叫做積屑瘤。
積屑瘤的硬度較基體材料高一倍以上,實際上可代替刀刃切削。積屑瘤的底部較穩定,頂部同工件和切屑沒有明顯的分界線,容易破碎和脫落,一部分隨切屑帶走,一部分殘留在加工表面上,從而使工件變得粗糙。所以在精加工時一定要設法避免或抑制積屑瘤的形成。積屑瘤的產生、成長和脫落是一個周期性的動態過程(據測定它的脫落頻率為30~170次/秒),它使刀具的實際前角和切削深度也隨之發生變化,引起切削力波動,影響加工穩定性。在一般情況下,當切削速度很低或很高時,因沒有產生積屑瘤的必要條件(較大的切屑與刀具前面間的摩擦力和一定的溫度),不產生積屑瘤。
4、抑制或消除積屑瘤的措施
(1)採用低速或高速切削,由於切削速度是通過切削溫度影響積屑瘤的,以切削45鋼為例,在低速vc<3m/min和較高速度vc≥60m/min範圍內,摩擦係數都較小,故不易形成積屑瘤;
(2)採用高潤滑性的切削液,使摩擦和粘結減少;
(3)適當減少進給量、增大刀具前角、減小切削變形;
(4)適當的熱處理來提高工件材料的硬度、降低塑性、減小加工硬化傾向。
技術要點
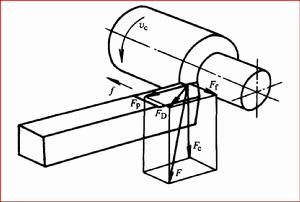
切削力
切削時刀具的前面和後面上都承受法向力和摩擦力,這些力組成合力F,在外圓車削時,一般將這個切削合力F分解成三個互相垂直的分力:切向力F──它在切削速度方向上垂直於刀具基面,常稱主切削力;徑向力F──在平行於基面的平面內,與進給方向垂直,又稱推力;軸向力F──在平行於基面的平面內,與進給方向平行,又稱進給力。一般情況下,由於刀具的幾何參數刃磨質量和磨損情況的不同和切削條件的改變,F對F的比值在很大的範圍內變化。
切削過程中實際切削力的大小,可以利用測力儀測出。測力儀的種類很多,較常用的是電阻絲式和壓電晶體式測力儀。測力儀經過標定以後就可測出切削過程中各個分力的大小。
切削熱
切削金屬時,由於切屑剪下變形所作的功和刀具前面、後面摩擦所作的功都轉變為熱,這種熱叫切削熱。使用切削液時,刀具、工件和切屑上的切削熱主要由切削液帶走;不用切削液時,切削熱主要由切屑、工件和刀具帶走或傳出,其中切屑帶走的熱量最大,傳向刀具的熱量雖小,但前面和後面上的溫度卻影響著切削過程和刀具的磨損情況,所以了解切削溫度的變化規律是十分必要的。
切削溫度
切削過程中切削區各處的溫度是不同的,形成一個溫度場切屑和工件的溫度分布,這個溫度場影響切屑變形、積屑瘤的大小、加工表面質量、加工精度和刀具的磨損等,還影響切削速度的提高。一般說來,切削區的金屬經過剪下變形以後成為切屑,隨之又進一步與刀具前面發生劇烈摩擦,所以溫度場中溫度分布的最高點不是在正壓力最大的刃口處,而是在前面上距刃口一段距離的地方。切削區的溫度分布情況,須用人工熱電偶法或紅外測溫法等測出。用自然熱電偶法測出的溫度僅是切削區的平均溫度。
刀具磨損
具在切削時的磨損是切削熱和機械摩擦所產生的物理作用和化學作用的綜合結果。刀具磨損表現為在刀具後面上出現的磨損帶、缺口和崩刃等,前面上常出現的月牙窪狀的磨損,副後面上有時出現的氧化坑和溝紋狀磨損等。當這些磨損擴展到一定程度以後就引起刀具失效,不能繼續使用。刀具逐漸磨損的因素,通常有磨料磨損、粘著磨損、擴散磨損、氧化磨損、熱裂磨損和塑性變形等。在不同的切削條件下,尤其是在不同切削速度的條件下,刀具受上述一種或幾種磨損機理的作用。例如,在較低切削速度下,刀具一般都因磨料磨損或粘著磨損而破損;在較高速度下,容易產生擴散磨損、氧化磨損和塑性變形。
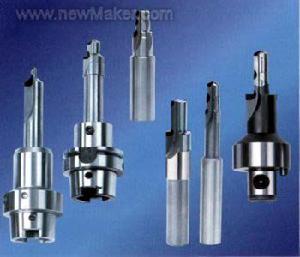
刀具壽命
刀具由開始切削達到刀具壽命判據以前所經過的切削時間叫做刀具壽命(曾稱刀具耐用度),刀具壽命判據一般採用刀具磨損量的某個預定值,也可以把某一現象的出現作為判據,如振動激化、加工表面粗糙度惡化,斷屑不良和崩刃等。達到刀具壽命後,應將刀具重磨、轉位或廢棄。刀具在廢棄前的各次刀具壽命之和稱為刀具總壽命。生產中常根據加工條件按最低生產成本或最高生產率的原則,來確定刀具壽命和擬定工時定額。切削加工性
指零件被切削加工成合格品的難易程度。它根據具體加工對象和要求,可用刀具壽命的長短、加工表面質量的好壞、金屬切除率的高低、切削功率的大小和斷屑的難易程度等作為判據。在生產和實驗研究中,常以作為某種材料的切削加工性的指標,它的含義是:當刀具壽命為分鐘時,切削該材料所允許的切削速度。越高,表示加工性越好,一般取60、30、20或10分鐘。
加工表面質量
通常包括表面粗糙度加工硬化殘餘應力、表面裂紋和金相顯微組織變化等。切削加工中影響加工表面質量的因素很多,例如刀具的刀尖圓弧半徑進給量和積屑瘤等是影響表面粗糙度的主要因素,刀具的刃口鈍圓半徑和磨損及切削條件是影響加工硬化和殘餘應力的主要因素。因此,生產中常通過改變刀具的幾何形狀和選擇合理的切削條件來提高加工表面質量。
切削振動
切削過程中,刀具與工件之間經常會產生自由振動、強迫振動或自激振動(顫振)等類型的機械振動。自由振動是由工具機零部件受到某些突然衝擊所引起,它會逐漸衰減。強迫振動是由工具機內部或外部持續的交變干擾力(如不平衡的工具機運動件、斷續切削等)所引起,它對切削產生的影響取決於干擾力的大小及其頻率。自激振動是由於刀具與工件之間受到突然干擾力(如切削中遇到硬點)而引起初始振動,使刀具前角、后角和切削速度等發生變化,以及產生振型耦合等,並從穩態作用的能源中獲得周期性作用的能源,促進並維持振動。通常,根據切削條件可能產生各種原生型自激振動,從而在加工表面上留下的振紋,又會產生更為常見的再生型自激振動。上述各種振動通常都會影響加刀表面質量,降低工具機和刀具的壽命,降低生產率,並引起噪聲,極為有害,必須設法消除或減輕。
切屑控制
指控制切屑的形狀和長短。通過控制切屑的捲曲半徑和排出方向,使切屑碰撞到工件或刀具上,而使切屑的捲曲半徑被迫加大,促使切屑中的應力也逐漸增加,直至折斷切屑的捲曲半徑可以通過改變切屑的厚度、在刀具前面上磨製卷屑槽或斷屑台來控制,其排出方向則主要靠選擇合理的主偏角和刃傾角來控制。現代人們已能用兩位或三位數字編碼的方式來表示各種切屑的形狀,通常認為短弧形切屑是合理的斷屑形狀。

也稱冷卻潤滑液,用於減少切削過程中的摩擦和降低切削溫度,以提高刀具壽命、加工質量和生產效率。常用的切削液有切削油、乳化液和化學切削液3類。
生產套用
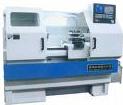
在設計和使用工具機和刀具時,需要套用切削原理中有關切削力、切削溫度和刀具切削性能方面的數據。例如,在確定工具機主軸的最大扭矩和剛性等基本參數時,要套用切削力的數據,在發展高切削性能的新材料時,需掌握刀具磨損和破損的規律,在切削加工中分析熱變形對加工精度的影響時,要研究切削溫度及其分布;在自動生產線和數字控制工具機上,為了使工具機能正常地穩定工作,甚至實現無人化操作,更要套用有關切屑形成及其控制方面的研究成果,並在加工中實現刀具磨損的自動補償和刀具破損的自動報警。
為此,各國研製了品種繁多的線上檢測刀具磨損和破損的感測器,其中大多數是利用切削力或扭矩、切削溫度、刀具磨損作為感測信號。此外,為了充分利用工具機,提高加工經濟性和發展計算機輔助製造(CAM),常需要套用切削條件、刀具幾何形狀和刀具壽命等的最佳化數據。因此,金屬切削原理這門學科在生產中的套用日益廣泛,各國都通過切削試驗或現場採集積累了大量的切削數據,並用數學模型來表述刀具壽命、切削力、功率和加工表面粗糙度等同切削條件之間的關係,然後存入計算機,建立金屬切削資料庫或編製成切削數據手冊,供用戶查用。
通用操作規程
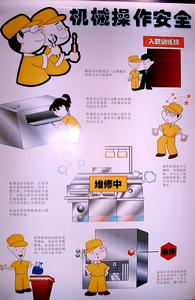
一、操作者必須經過考試合格,持有本工具機的《設備操作證》方可操作本工具機。
二、工作前認真作到:
1、仔細閱讀交接班記錄,了解上一班工具機的運轉情況和存在問題。
2、檢查工具機、工作檯、導軌以及各主要滑動面,如有障礙物、工具、鐵屑、雜質等,必須清理、擦拭乾淨、上油。
3、檢查工作檯,導軌及主要滑動面有無新的拉、研、碰傷,如有應通知班組長或設備員一起查看,並作好記錄。
4、檢查安全防護、制動(止動)、限位和換向等裝置應齊全完好。
5、檢查機械、液壓、氣動等操作手柄、伐門、開關等應處於非工作的位置上。
6、檢查各刀架應處於非工作位置。
7、檢查電器配電箱應關閉牢靠,電氣接地良好。
8、檢查潤滑系統儲油部位的油量應符合規定,封閉良好。油標、油窗、油杯、油嘴、油線、油氈、油管和分油器等應齊全完好,安裝正確。按潤滑指示圖表規定作人工加油或機動(手位)泵打油,查看油窗是否來油。
9、停車一個班以上的工具機,應按說明書規定及液體靜壓裝置使用規定(詳見附錄Ⅰ)的開車程式和要求作空動轉試車3~5分鐘。檢查:
① 操縱手柄、伐門、開關等是否靈活、準確、可靠。
② 安全防護、制動(止動)、聯鎖、夾緊機構等裝置是否起作用。
③ 校對機構運動是否有足夠行程,調正並固定限位、定程擋鐵和換向碰塊等。
④ 由機動泵或手拉泵潤滑部位是否有油,潤滑是否良好。
⑤ 機械、液壓、靜壓、氣動、靠模、仿形等裝置的動作、工作循環、溫升、聲音等是否正常。壓力(液壓、氣壓)是否符合規定。確認一切正常後,方可開始工作。
凡連班交接班的設備,交接班人應一起按上述(9條)規定進行檢查,待交接班清楚後,交班人方可離去。凡隔班接班的設備,如發現上一班有嚴重違犯操作規程現象,必須通知班組長或設備員一起查看,並作好記錄,否則按本班違犯操作規程處理。
在設備檢修或調整之後,也必須按上述(9條)規定詳細檢查設備,認為一切無誤後方可開始工作。
三、工作中認真作到:
1、 堅守崗位,精心操作,不做與工作無關的事。因事離開工具機時要停車,關閉電源、氣源。
2、 按工藝規定進行加工。不準任意加大進刀量、磨削量和切(磨)削速度。不準超規範、超負荷、超重量使用工具機。不準精機粗用和大機小用。
3、 刀具、工件應裝夾正確、緊固牢靠。裝卸時不得碰傷工具機。找正刀具、工件不準重錘敲打。不準用加長搬手柄增加力矩的方法緊固刀具、 工件。
4、 不準在工具機主軸錐孔、尾座套筒錐孔及其他工具安裝孔內,安裝與其錐度或孔徑不符、表面有刻痕和不清潔的頂針、刀具、刀套等。
5、 傳動及進給機構的機械變速、刀具與工件的裝夾、調正以及工件的工序間的人工測量等均應在切削、磨削終止,刀具、磨具退離工件後停車進行。
6、 應保持刀具、磨具的鋒利,如變鈍或崩裂應及時磨鋒或更換。
7、 切削、磨削中,刀具、磨具未離開工件,不準停車。
8、 不準擅自拆卸工具機上的安全防護裝置,缺少安全防護裝置的工具機不準工作。
9、 液壓系統除節流伐外其他液壓伐不準私自調整。
10、工具機上特別是導軌面和工作檯面,不準直接放置工具,工件及其他雜物。
11、經常清除工具機上的鐵屑、油污,保持導軌面、滑動面、轉動面、定位基準面和工作檯面清潔。
12、密切注意工具機運轉情況,潤滑情況,如發現動作失靈、震動、發熱、爬行、噪音、異味、碰傷等異常現象,應立即停車檢查,排除故障後,方可繼續工作。
13、工具機發生事故時應立即按總停按鈕,保持事故現場,報告有關部門分析處理。
14、不準在工具機上焊接和補焊工件。
四、工作後認真作到:
1、 將機械、液壓、氣動等操作手柄、伐門、開關等板到非工作位置上。
2、 停止工具機運轉,切斷電源、氣源。
3、 清除鐵屑,清掃工作現場,認真擦淨工具機。導軌面、轉動及滑動面、定位基準面、工作檯面等處加油保養。
4、 認真將班中發現的工具機問題,填到交接班記錄本上,做好交班工作。
1:http://www.158jixie.com/Metal-cutting-machine/
2:http://www.36021.com/Html/hyyj/ao/i/
化學與物理術語(一)
通過對化學和物理的了解,來明白生活中的細節,從而使我們更好的明白一些事物。 |