線材軋制
正文
線材俗稱“盤條”或“盤元”。線材軋制的特點是總的延伸率大,軋件的溫降快。因此,線材軋機的機架數目多,最多的達到27架,軋制速度快,每秒鐘高達100多米。銅線坯、鋁線坯主要用於拔制,電線用絲材。鋼線材的用途較廣,除大量用作拔絲原料外,還直接作為建築材料和製作機械零件。線材品種繁多,按鋼種可分為碳素鋼線材和合金鋼線材,而碳素鋼線材又有軟線和硬線之分。按斷面形狀分,線材絕大部分為圓形,少量為方形、六角形等。多數直徑為5.5~13mm;也有大到38mm的和50mm的,稱“成卷棒材”。
軋制線材用的原料有軋制坯和連鑄坯兩種,一般的斷面尺寸為80×80~130×130mm,長度為3~22m,坯料單重由幾十公斤到二噸半。坯料的尺寸主要根據軋機的形式、最高軋制速度、每條軋線機架總數和採用的平均延伸係數來確定。
最早出現的活套式線材軋機是1838年建成的二列式軋機,第一列為一架三輥粗軋機,第二列為五架精軋機。此後,經歷了平立輥連續式、多列式、半連續式以及適合於生產合金鋼線材的小活套無張力多列式等形式線材軋機,到1966年,美國設計建造了摩根式45°無扭整體機座的高速線材軋機,成為高速線材軋機的主要形式。70年代世界上已有45°無扭線材軋機約100套(見表)。
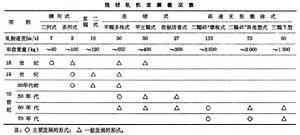
軋機布置 線材軋機多為二輥式,布置形式很多,主要有如下四種:
橫列式 軋機架數一般不超過15架,布置成二列或多列式如圖1a、 b,以穿梭和活套方式軋制。使用橫列式軋機勞動強度大、終軋溫度低、頭尾溫差大、產品質量低。但投資少,靈活性大,適合於多品種小批量生產。
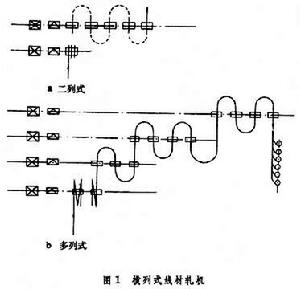
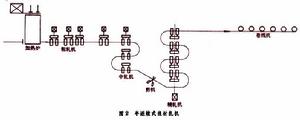
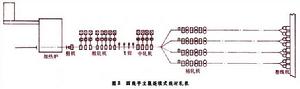
45°無扭線材軋機的特點是精軋機組為無扭整體機座,精軋機組之後,布置有控制冷卻線。整體機座由8~10個輥組組成,集體傳動,輥組配置極為緊湊(圖4),並採用懸臂式小直徑碳化鎢軋輥。由於高速塑性變形產生的熱量,精軋不但不降溫,反可升溫,所以線材終軋溫度可高達1000℃,頭尾溫差也小。這樣既可加大坯料的斷面尺寸和單重,又可提高線材的尺寸精度、表面質量和軋機的生產能力。這是60年代以來軋鋼技術發展的一項重大成就,改變了世界上線材生產面貌,1979年中國上海第二鋼鐵廠建造了45°無扭精軋機組(圖5)。
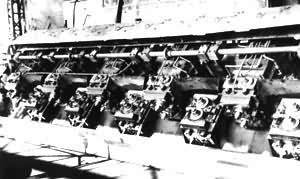
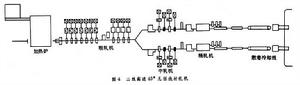
線材生產工藝流程 首先將鋼坯進行無損探傷,表面清理並經稱量後送入加熱爐加熱,沿鋼坯全長的加熱溫度應均勻一致,然後進行軋制。產品尺寸不同,孔型與軋制速度也不一樣,生產φ5.5~12.7mm線材的孔型系統見圖6。軋後經控制冷卻、檢查與打捆,最後收集入庫。銅線坯、鋁線坯的生產工藝與鋼線坯的生產工藝基本相似,但坯料尺寸、加熱溫度及孔型等不同。現廣泛套用連鑄連軋生產銅及鋁線坯。(見彩圖)
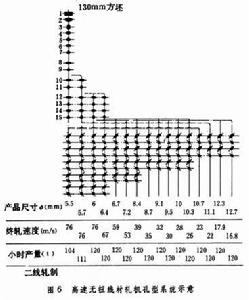
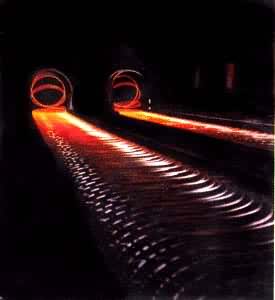
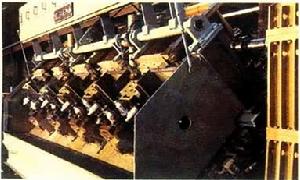
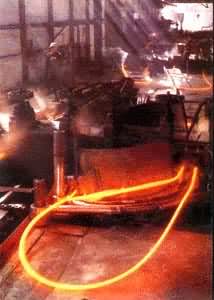
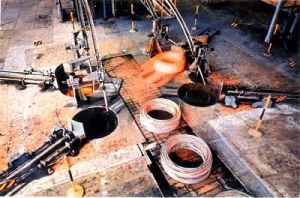
王廷溥主編:《軋鋼工藝學》,冶金工業出版社,北京,1981。