初軋和鋼坯軋制
正文
在初軋機上把鋼錠軋製成板坯、方坯和異型坯,並破壞鋼錠的鑄造組織的過程稱為初軋。也可配有鋼坯軋機,將大斷面的初軋坯進一步軋成各種小斷面的鋼坯。初軋機和鋼坯軋機的規格以“軋輥的公稱直徑”表示(見軋機)。初軋機已有 110多年的發展歷史。60年代以來,在技術上有較大的發展,水平二輥可逆式工作機座的輥徑有些已增大到1370mm,個別達到1500mm,主電動機容量增大到9000~14000千瓦,最大鋼錠重量近50噸,每台軋機的年生產能力可達350~600萬噸。一些國家建成了帶有立輥的板坯初軋機,有的能生產最大寬度為2300mm的板坯。初軋 初軋的鋼錠應先在均熱爐內加熱,並應採取熱裝爐,先進的裝爐錠溫可達850℃以上。在頭幾道軋次時鋼錠表面變形易形成“魚尾”,現已採取多種控制措施。初軋的道次較多,而初軋機上的孔型數量有限,所以採用共用性大的平孔或箱形孔。板坯立軋時軋輥的開口度很大,高達2700mm,壓下裝置的調整速度快達每秒鐘300mm。軋製成鋼坯後,以火焰進行四面清理,有時還設冷態清理。剪下採用多刀少切和最佳配尺方法,可提高成坯率。鋼坯在冷卻後,對要求嚴格的無縫管坯等需進行矯直、拋丸清理、探傷和修磨等精整工作。對一些特種鋼坯需進行緩冷等熱處理。初軋機按結構和生產坯料可分為方坯初軋機、方坯-板坯初軋機和板坯初軋機三種,均為可逆式軋機。
方坯初軋機 開口度較小,可生產方形、矩形、異形和圓形等鋼坯,初軋機除機前有帶翻鉤的推床外,還附加有輔助的翻鋼裝置。
方坯-板坯初軋機 既可生產方坯,又可生產板坯。廣泛採用的是大開口度初軋機,可生產工字鋼用的異形坯。為使軋輥有足夠的強度,輥徑一般大於1000mm,開口度取決於所生產的板坯的寬度,70年代最大可生產寬1850mm的板坯。
板坯初軋機 專門用於生產板坯。除水平輥以外,在機前或機後有立輥,用於齊邊和控制坯寬。在初軋機後常設生產小鋼坯的連軋機。
鋼坯軋制 在初軋機後面配置鋼坯軋機,可生產斷面為50×50至240×240mm方坯,直徑為80~270mm的圓坯,寬度在 450mm以下的薄板坯等。鋼坯生產最初採用非連續軋制方式的單機架或幾個機架組成。連軋技術發展後,開始用集體傳動的4~6個水平輥機架為一組的連續式鋼坯軋機,軋件要經扭轉後餵入下一機架,可生產方坯和薄板坯,也生產圓坯。立輥機架問世後,有了單獨傳動的立輥和水平輥機架交替配置的連續式鋼坯軋機,使軋件不需扭轉,提高了鋼坯的表面質量及尺寸精度,並有利於生產圓坯。在生產供軋制直徑 140mm以下的鋼管用的小斷面圓坯時,初軋坯表面一般要先經火焰清理。
視產品規格與生產能力,配置一組或兩組連續式鋼坯軋機(圖1)。兩組時,可用斷面較大的初軋坯(達360×360mm)和高的軋制速度(達每秒鐘5~7米),年生產能力可達300~500萬噸。當需生產大斷面圓鋼(∮250~350mm)時,可在一組連續式鋼坯軋機前安裝一架水平二輥可逆式粗軋機。
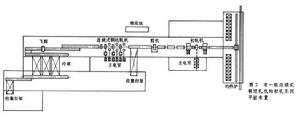
連續式鋼坯軋機的機架多選用普通框架式牌坊,輥徑根據軋件斷面,一般選擇在950~500mm的範圍內。在平立輥交替的機組中,為保持軋制線位置不變,立輥與水平輥均能分別作垂直及水平移動,以便迅速更換軋槽。為了提高軋機作業率,還採用橫移式快速換輥裝置。高產量的連軋機後設有飛剪機,將長軋件切成所需的長度。生產圓鋼時,尚需有熱鋸機鋸切分段;生產鋼坯時,多採用翻轉步進齒條式冷床,以提高平直度。對軟鋼一類鋼種的冷卻,也可經水冷處理。70年代以來,為提高方、圓坯的質量,都採用冷矯直機與無損探傷作業線以及各種清理表面缺陷的設備。對於質量要求更嚴的直徑大於140mm的管坯,則部分或全部採用無心車床進行剝皮;一般採用拋丸除鱗,有的還配置機械化的強力砂輪修磨設備,以清除局部缺陷,或作全面修磨。
在一些中小型鋼鐵企業中,也採用650mm、500mm等橫列式三輥鋼坯軋機,將小鋼錠和大鋼坯軋成小斷面的方坯、薄板坯及無縫管坯。這種軋機多用共軛孔型,由交流主電動機驅動。這種軋機造價低,適合於中小型廠的需要;但能耗大,收得率低,產品質量也較差。
中國設計建造的板坯初軋機 中國在60年代中期設計建造的1150mm板坯初軋機(圖2),水平軋輥直徑為1150mm,輥身長度為2100mm,開口度為1900mm,軋輥經萬向接軸由 2台容量為4600kW、轉速為40/80rpm的直流電動機直接傳動,機前設有立輥,其軋輥直徑為950mm,輥身長為2100mm,由設在機架頂部的2台容量為1500kW,轉速為60/120rpm立式主電動機傳動。軋機前後設有推床,機前推床安有鉤式翻鋼機,供水平輥立軋時翻鋼。年生產能力約為 350萬噸。使用鋼錠的最大重量為27噸,可生產厚120~250mm,寬至1600mm,長至9000mm的板坯。鋼錠由煉鋼車間熱送至與主跨間呈“丁”字形布置的均熱爐跨間,加熱到約1250℃。均熱爐為上部單側燒嘴式,每坑最大裝入量150噸。用鋼繩傳動的側翻運錠車將加熱好的鋼錠送至受料輥道上,借液壓驅動的迴轉裝置將鋼錠調頭、然後送往軋機上軋成板坯。軋成的板坯在剪下力為2500噸的液壓剪機上切除頭尾,並剪下成定尺。剪機前預留有清理板坯四個面的火焰清理機。在收集輥道處設有液壓板垛,用推鋼機將板垛推到鋼繩拖動的75噸板垛運輸車上,運往板坯跨間,收集輥道後還預留有板坯水冷裝置。
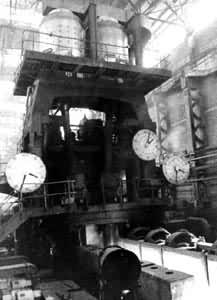
目前,有些新型初軋機從均熱爐加熱開始到軋制、精整和冷卻,整個生產過程都採用計算機控制,並配置與全廠生產管理相聯繫的計算機系統。
初軋生產技術的發展,降低了能耗,提高了收得率。最好指標已近97%。主要措施有:提高沸騰鋼的比例,上鑄鋼錠時採用防濺筒以減少表面結疤;鎮靜鋼掛絕熱板、加發熱劑以減少切頭;鋼錠採用凹型底盤澆注;沸騰鋼錠用大頭進鋼軋制,改變軋制壓下制度,以減少底部魚尾段長度;沸騰鋼採用瓶口模和機械封頂以減少縮孔;合理剪下以減少切損和發展半鎮靜鋼等。為了提高軋機產量,普遍採用多錠串軋。雙錠串軋與單錠軋制相比,總軋制時間可縮短25~30%,軋機產量可提高10~30%。此外,採用液芯裝爐法,可節省均熱爐的燃耗。直送軋制和熱裝爐等節能措施也有所發展。(見彩圖)
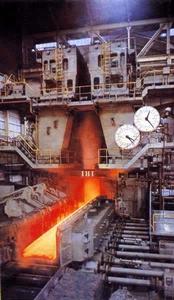
王廷溥主編:《軋鋼工藝學》,冶金工業出版社,北京,1981。