內容簡介
實施精益生產是製造類企業提高核心競爭力的有效途徑,本書原作者在多個行業都有豐富的精益生產的實踐經驗,在書中完整敘述和說明了實施精益生產的策劃、運行和維護各方面的細節。
本書內容共3篇9章,論述了精益生產的歷史和現代套用;如何進行戰略業務分析;理解你的產品、工藝和需求;具有連線和平衡工序的生產線布置及工位標識;看板策略;用看板系統管理創新;團隊的建立;實施精益生產過程中的里程碑檢查清單;對精益生產線進行管理。
本書可供製造業的企業領導和生產管理人員全面了解精益生產,並可作為精益生產實施的指導用書。
作者簡介
丹尼斯P.霍布斯(Dennis P.Hobbs),在製藥和電子機械製造工業中從事生產線與人事工作,在生產計畫、庫存控制以及物料和經營管理方面已有30多年的經驗。他畢業於密蘇里大學,獲工商管理學士學位,曾領導實施了兩個MRP系統,後來達到了A級水平。他還曾為製藥業開設、實施和管理過行業認定的供應商認證課程。作為課程開設的導師,他為FDA(美國食品和藥物管理局)GMP(藥品生產質量管理規範)進行過的技術設計有效性的驗證並舉辦過培訓課程、研討會、討論會和交流會。
在過去的10年中,霍布斯先生作為副總裁和高級顧問,致力於精益生產系統的實施和教育。在那段時間裡,作為一位專業教師,他培訓了2500多名精益生產技術方面的生產專業人員。
基礎知識
譯叢序言
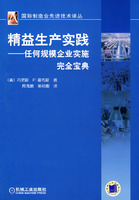
譯者前言
英文版序
關於作者
關於美國生產與庫存管理協會(APICS)
引言
0.1 單件生產與批量生產工時的對比
0.2 雙箱物料看板方法
0.3 需求的精益管理
0.4 更多的術語?
第1篇 實施精益生產體系的好處
第1章 精益生產的歷史和現代套用
1.1 MRP系統的普及及其對組織的影響
1.2 計算機時期前的庫存管理工具
1.3 MRP模式的再思考——“系統不會讓我這樣做的!”
1.4 生產最高目標的尋求
1.5 精益生產模式
1.6 看板管理方法
1.7 精益生產線上一次一件的順序生產
1.8 採用精益生產技術的好處
1.9 精益生產挑戰MRP範例
1.10 邁向精益生產的持續發展
1.11 引入網際網路和電子商務技術
1.12 為什麼要經受改變的痛苦?
第2章 進行戰略業務分析
2.1 戰略業務分析檢查單
2.2SBA重要性能度量法
2.3 生產率改善計畫的成果
2.4 生產提前期對流動資金的影響
2.5 推薦的SBA訪談表
第2篇 將你的設備轉向精益生產的方法
第3章 理解你的產品、工序和需求
3.1 確定最初的精益生產實施範圍
3.2 選定精益生產線的基本零件
3.3 確定生產能力來滿足精益生產所要求的容量
3.4 確定需求量的依據
3.5 工序流的描述和混合產品系列的確定
3.6 影響生產能力的因素
3.7 工序需求量的確定和節拍的建立
3.8 節拍時間的分子和分母
3.9 工序加工基本部分的描述和質量的評價指標
3.10 非增值活動和質量的考慮
3.11 工序總時間的計算
第4章 具有連線和平衡工序的生產線布置及工位標識
4.1 不平衡的結果
4.2 實現平衡的精益方法
4.3 資源需要量的計算
4.4 資源的限定
4.5 資源的具體布局
4.6 對每個工位分配任務
4.7 在制品看板信號傳送的管理方法
4.8 維持工位平衡的規章制度
4.9 將5S加人生產線的設計
第5章 看板策略
5.1 在制品看板
5.2 單卡看板系統
5.3 多卡看板系統
第6章 用看板系統來管理庫存
6.1 看板系統的優點
6.2 看板系統的缺點
6.3 看板經理的工作職責
第3篇 對生產線啟動、日常運行和性能的檢測進行項目管理
第7章 團隊的建立
7.1 對改變的支持
7.2 向精益生產的轉變過程
7.3 對項目團隊提供具體的方便
7.4 項目管理的結構
7.5 所需信息概要
第8章 實施精益生產過程中的里程碑檢查清單
8.1 精益生產管理方法的軟體要求
8.2 里程碑1:初始化和項目啟動
8.3里程碑2:掌握產品、工藝和物料
8.4里程碑3:最後的檢查
8.5 里程碑4:工廠的設計
8.6 里程碑5:生產線開始啟動
8.7 里程碑6:內部化
8.8 精益生產對組織的影響
第9章 對精益生產線進行管理
9.1 對生產線的產出量進行管理來滿足顧客的需要
9.2 顧客回響工作準則的建立
9.3 使精益生產線局部最佳化以滿足每天的需求量
9.4 柔性的操作人員
9.5 對柔性給予報償
9.6 對線性績效給予報償
9.7 改變的阻力
精益生產有哪些步驟
精益生產的研究者總結出精益生產實施成功的五個步驟:
1、選擇要改進的關鍵流程
精益生產方式不是一蹴而就的,它強調持續的改進。首先應該先選擇關鍵的流程,力爭把它建立成一條樣板線。
2、畫出價值流程圖
價值流程圖是一種用來描述物流和信息流的方法。在繪製完目前狀態的價值流程圖後,可以描繪出一個精益遠景圖(Future Lean Vision)。在這個過程中,更多的圖示用來表示連續的流程,各種類型的拉動系統,均衡生產以及縮短工裝更換時間,生產周期被細分為增值時間和非增值時間。
3、開展持續改進研討會
精益遠景圖必須付諸實施,否則規劃得再巧妙的圖表也只是廢紙一張。實施計畫中包括什麼(What),什麼時候(When)和誰來負責(Who),並且在實施過程中設立評審節點。這樣,全體員工都參與到全員生產性維護系統中。在價值流程圖、精益遠景圖的指導下,流程上的各個獨立的改善項目被賦予了新的意義,使員工十分明確實施該項目的意義。持續改進生產流程的方法主要有以下幾種:消除質量檢測環節和返工現象;消除零件不必要的移動;消滅庫存;合理安排生產計畫;減少生產準備時間;消除停機時間;提高勞動利用率。
4、營造企業文化
雖然在車間現場發生的顯著改進,能引發隨後一系列企業文化變革,但是如果想當然地認為由於車間平面布置和生產操作方式上的改進,就能自動建立和推進積極的文化改變,這顯然是不現實的。文化的變革要比生產現場的改進難度更大,兩者都是必須完成並且是相輔相成的。許多項目的實施經驗證明,項目成功的關鍵是公司領導要身體力行地把生產方式的改善和企業文化的演變結合起來。
傳統企業向精益化生產方向轉變,不是單純地採用相應的“看板”工具及先進的生產管理技術就可以完成,而必須使全體員工的理念發生改變。精益化生產之所以產生於日本,而不是誕生在美國,其原因也正因為兩國的企業文化有相當大的不同。
5、推廣到整個企業
精益生產利用各種工業工程技術來消除浪費,著眼於整個生產流程,而不只是個別或幾個工序。所以,樣板線的成功要推廣到整個企業,使操作工序縮短,推動式生產系統被以顧客為導向的拉動式生產系統所替代。
總而言之,精益生產是一個永無止境的精益求精的過程,它致力於改進生產流程和流程中的每一道工序,盡最大可能消除價值鏈中一切不能增加價值的活動,提高勞動利用率,消滅浪費,按照顧客訂單生產的同時也最大限度的降低庫存。
由傳統企業向精益企業的轉變不可能一蹴而就,需要付出一定的代價,並且有時候還可能出現意想不到的問題。但是,企業只要堅定不移走精益之路,大多數在6個月內,有的甚至還不到3個月,就可以收回全部改造成本,並且享受精益生產帶來的好處。