生產過程
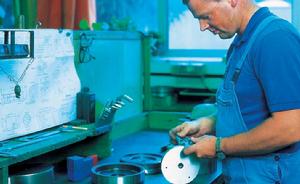
現代工業產品的生產過程系統包括:生產技術準備過程、基本生產過程、輔助生產過程和生產服務過程。以上這些過程又具體體現在:技術準備工作;生產準備工作;原材料的採購、運輸、保管;毛坯的再加工和改制;產品零、組件的加工和檢驗;產品的裝配、調試、檢驗;產品的裝飾、包裝、運輸等工作。
現代工業產品的生產過程也是企業的人力、物力、財力、信息的轉化過程。任何一個產品的形成,都是許多企業共同勞動的成果。在今天,隨著生產組織的專業化和產品的標準化程度的提高,各個企業間互相協作和共同依存的關係比以往都顯得突出和重要。同樣,在一個企業內部也是如此,某一車間生產的“成品”往往是其它車間組織生產的“原材料”。
在非模具專業生產企業中產品專業廠、,模具作為工藝裝備的一部分,在基本產品生產系統中屬於輔助生產過程,是保證基本產品生產不可缺少的組成部分。在模具專業生產企業中,模具做為企業的基本產品,其生產過程始終貫穿於企業的全部生產過程之中。
模具的種類很多,每種模具的結構、要求和用途不同,它們都有特定的生產過程。但是,同屬模具類,它們的生產過程又都具有共性的特點。因此,模具的生產過程可以劃分為五個主要階段:生產技術準備,材料的準備,模具零、組件的加工,裝配調試和試用鑑定。
在上述生產過程中,生產技術準備階段是整個生產的基礎,對於模具的質量、成本、進度和管理都有重大的影響。生產技術準備階段的工作內容包括模具圖樣的設計,工藝技術檔案的編制,材料定額和加工工時定額的制定,模具成本的估價等。
在模具加工過程中,毛坯、零件和組件的質量保證和檢驗是必不可少的環節,在模具生產中通過“三檢制”的實施保證合格製件在生產線上流轉。在模具加工過程中,相關工序和車間之間的轉接是生產連續進行所必要的,在轉接中間和加工不均衡所造成的等待和停歇是模具生產中的突出問題,做為模具生產組織者應該將這部分時間降低到最小程度。
工藝工作
模具工藝工作的主要內容
1、編制工藝檔案。模具工藝檔案主要包括模具零件加工工藝規程、模具裝配工藝要點或工藝規程、原材料清單、外購件清單和外協件清單等。模具工藝技術人員應該在充分理解模具結構、工作原理和要求的情況下,結合本企業冷、熱加工設備條件,企業生產和技術狀態等條件編制模具零件和裝配的工藝檔案。
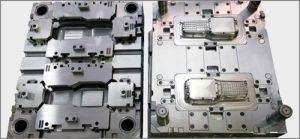
2、二類工具的設計和工藝編制。二類工具二級工具、是指加工和裝配模具中所用的各種專用工具。這些專用的二類工具一般都由模具工藝技術人員負責設計和工藝編制特殊的部分由專門技術人員完成、。二類工具的質量和效率對模具質量和生產進度起著重要的作用。在客觀條件允許下可以利用通用工具改制,注意應該將二類工具的數量和成本降低到客觀允許的最小程度。經常設計的二類工具有非標準的鉸刀和銑刀、各型面檢驗樣板、非標準量規、仿形加工用靠模及電火花成形加工電極、型面檢驗放大圖等。
3、處理加工現場技術問題。解決在模具零件加工和裝配過程中出現的技術、質量和生產管理問題是模具工藝技術人員的經常性工作之一,如解釋工藝檔案和進行技術指導,調整加工方案和方法。
4、參加試模和鑑定工作。各種模具在裝配之後的試沖和試壓是模具生產的重要環節,模具工藝技術人員和其它有關人員通過試沖和試壓,分析技術問題和提出解決方案,並對模具的最終技術質量狀態做出正確的結論。
工藝檔案
具裝配工藝規程的編制,對於一般模具只需編制裝配要點,而模具的具體裝配程式可由模具裝配鉗工自行掌握,只有對大型複雜模具,才編制較詳細的裝配工藝規程。
一般模具加工工藝規程編制的程式,其中有些工作可以交叉進行。
1、模具工藝性分析。在充分理解模具結構、用途、工作原理和技術要求下分析各種零件在模具中的作用和技術要求,分析模具材料、零件形狀、尺寸和精度要求等工藝性是否合理,找出加工的技術難點,提出合理加工方案和技術保證措施。
2、確定毛坯形式。根據零件的材料類別、零件的作用和要求等確定哪些零件分屬於自製件、外購件和外協件,分別填寫外購件清單和外協件清單。對於自製件應確定毛坯形式,如原型材、鑄造件、鍛造件、焊接件和半成品件等,並填寫毛坯備料清單。
3、二類工具的設計和工藝編制。專用二類工具的設計原則應該符合模具生產的特點。
4、工藝規程內容的填寫。模具工藝規程內容的填寫,應該文字簡捷、明確、符合工廠用語。對於重要關鍵工序的技術要求和保證措施、檢驗方法做出必要的說明,根據需要畫出工序加工簡圖。
生產特點
模具作為一種高壽命的專用工藝裝備,有以下生產特點:
1、屬於單件、多品種生產。模具是高壽命專用工藝裝備,每副模具只能生產某一特定形狀、尺寸和精度的製件,這就決定了模具生產屬於單件、多品種生產規程的性質。
2、客觀要求模具生產周期短。當前由於新產品更新換代的加快和市場的競爭,客觀上要求模具生產周期越來越短。模具的生產管理、設計和工藝工作都應該適應客觀要求。
3、模具生產的成套性。當某個製件需要多副模具來加工時,各副模具之間往往互相牽連和影響,只有最終製件合格,這一系列模具才算合格。因此,在生產和計畫安排上必須充分考慮這一特點。
4、試模和試修。由於模具生產的上述特點和模具設計的經驗性,模具在裝配後必須通過試沖或試壓,最後確定是否合格;同時,有些部位需要試修才能最後確定。因此,在生產進度安排上必須留有一定的試模周期。
5、模具加工向機械化、精密化和自動化方向發展。目前產品零件對模具精度的要求越來越高,高精度、高壽命、高效率的模具越來越多。而加工精度主要取決於加工工具機精度、加工工藝條件、測量手段和方法。目前,精密成型磨床、CNC高精度平面磨床、精密數控電火花線切割工具機、高精度連續軌跡坐標磨床以及三坐標測量機的使用越來越普遍,使模具加工向高技術密集型發展。
工藝特點
1、模具加工時儘量採用萬能通用工具機、通用刀量具和儀器,儘可能減少專用二類工具的數量。
2、在模具設計和製造時較多採用“實配法”、“同鏜法”等,使得模具零件的互換性降低,這是保證加工精度、減小加工難度的有效措施。隨著加工技術手段的提高,互換性程度將會提高。
3、在製造工序安排上,工序應相對集中,以保證模具加工質量和進度,簡化管理和減少工序周轉時間。
精度剛度
模具精度
機械產品的精度包括:尺寸精度、形狀精度、位置精度和表面粗糙度。機械產品在工作狀態和非工作狀態的精度不同,又分為動態精度和靜態精度模具的精度主要體現在模具工作零件的精度和相關部位的配合精度。模具工作部位的精度高於產品製件的精度。沖裁模刃口尺寸的精度要高於產品製件的精度。沖裁凸模和凹模間沖裁間隙的數值大小和均勻一致性也是主要精度參數之一。平時測量出的精度都是非工作狀態下進行的如沖裁間隙、,即靜態精度。而在工作狀態時,受到工作條件的影響,其靜態精度數值都發生了變化,這時稱為動態精度,這種動態沖裁間隙才是真正有實際意義的。一般模具的精度也應與產品製件的精度相協調,同時也受模具加工技術手段的制約。隨著模具加工技術手段的提高,模具精度會有大的提高,模具工作零件的互換性生產將成為現實。
影響模具精度的主要因素有:
1、產品製件精度。產品製件的精度越高,模具工作零件的精度就越高。模具精度的高低不僅對產品製件的精度有直接影響,而且對模具的生產周期、生產成本都有很大的影響。
2、模具加工技術手段的水平。模具加工設備的加工精度和設備的自動化程度是保證模具精度的基本條件。今後,模具精度更大地依賴模具加工技術手段的高低。
3、模具裝配鉗工的技術水平。模具的最終精度很大程度依賴裝配調試來完成,模具光整表面的表面粗糙度數值主要依賴模具鉗工來完成,因此,模具鉗工技術水平是影響模具精度的重要因素。
4、模具製造的生產方式和管理水平。模具工作刃口尺寸在模具設計和生產時,是採用“實配法”還是“分別製造法”,是影響模具精度的重要方面。對於高精度模具,只有採用“分別製造法”才能滿足高精度的要求和實現互換性生產。
模具剛度
對於高速衝壓模、大型件衝壓成型模、精密塑膠模和大型塑膠模,不僅要求精度高,還應有良好的剛度。這類模具工作負荷較大,當出現較大的彈性變形時,不僅要影響模具的動態精度,而且關係到模具能否繼續正常工作。因此在模具設計中,在滿足強度要求時,對於模具生產成本也應得到保證,同時在製造時也要避免由於加工不當造成的附加變形。
生產成本
影響模具生產成本的主要因素有:
1、模具結構的複雜程度和模具功能的高低。現代科學技術的發展使得模具向高精度和多功能自動化方向發展,相應使模具生產成本提高。
2、模具精度和剛度的高低。模具的精度和剛度越高,模具生產成本也越高。模具精度和剛度應該與客觀需要的產品製件的要求、生產批量的要求相適應。
3、模具材料的選擇。模具費用中,材料費在模具生產成本中約占25%~30%,特別是因模具工作零件材料類別的不同,相差較大。所以,應該正確選擇模具材料,使模具工作零件的材料類別首先應該和要求的模具壽命相協調,同時應採取各種措施充分發揮材料的效能
4、模具加工設備。模具加工設備向高效、高精度、高自動化、多功能發展,這使模具成本相應提高。但是,這些是維持和發展模具生產所必需的,應該充分發揮這些設備的效能,提高設備的使用效率。
5、模具的標準化程度和企業生產的專門化程度。這些都是制約模具成本和生產周期的重要因素,應通過模具工業體系的改革,有計畫、有步驟地解決。
模具加工
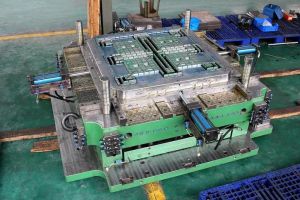
1)外形表面
外形表面是指構成模具零件基本外形特徵的表面。
一般,外形表面是模具零件的外沿表面,這些外沿表面多為由平面組成的矩形體或由圓柱面、圓錐面組成的鏇轉體,有時也包含二維曲面和三維曲面。
2)成形表面
成形表面是指在模具中直接決定產品零件形狀、尺寸、精度的表面及與這些表面協調的相關表面。例如沖裁模中的凹模、凸模工作表面及與工作表面協調相關的卸料板、固定板等型孔表面。圖7-3所示的彎曲模凸模的成型表面就是指由R4.8、R7.8、86°、33°等尺寸構成的二維曲面。
一般,成形表面的形狀比較複雜、尺寸精度較高和表面粗糙度數值較小,而且多有熱處理要求,各相關零件的成形表面的一致性和協調性都有比較嚴格的要求。成形表面的加工是模具工藝工作的重點和難點之一。
3)結構表面
結構表面是指在模具中起定位、導向、定距、限位、聯接、驅動等作用的表面。圖7-3所示的彎曲模凸模的兩個的圓柱銷孔等表面就屬於結構表面,它是和模柄相連的定位和固定表面。
結構表面在模具中,對於保證各個零件間的相關尺寸和位置精度,對於聯接和相互運動的可靠性起著十分重要的作用。結構表面的形狀是各種各樣的,而且不同零件的材料及熱處理要求也不相同。在工藝安排中,要根據各個零件結構表面的作用及與其它相關零件的關係區別對待。
2、各類表面的加工分析
1)外形表面的加工
各種模具零件的加工都從外形表面加工開始,並為成形表面和結構表面的後續加工奠定基礎。在模具零件的毛坯設計和加工中,應使外形表面的加工餘量適當,避免材料浪費和減少後續加工工作量。對於鍛件和鑄件毛坯,在毛坯加工階段應進行必要的退火和時效熱處理,以減小材料內應力和為後續加工做好金相組織準備。
在模具零件的外形表面中,有的表面是後續加工的劃線面和劃線、尺寸加工的基準面,有的是零件間相聯的接合面、模具的分型面、模具和工具機聯接的安裝面。對於將作為劃線面、基準面、接合面、分型面、安裝面的平面外形表面,表面粗糙度Ra≤0.8μm,其餘平面外形表面Ra=6.3μm即可。平面外形表面的形位精度要求有平面的平面度和平面間的平行度和垂直度要求。這些形位精度要求,有的是在模具設計中已經規定和要求的,有的是由於零件加工工藝的需要,必須在加工中保證的。
平面外形表面的加工可以在牛頭刨床、立銑床、龍門刨床上進行刨削和銑削加工,以去除毛坯上的大部分加工餘量。從生產效率上考慮,大型平面多採用龍門刨床刨削加工;中型平面多採用牛頭刨床刨削加工;中、小型平面多採用立銑床銑削加工。通過上述加工可得到平面外形表面的基本形狀和尺寸,但是平面的表面比較粗糙,平行度和垂直度都比較低,再通過後續工序的平面磨削來達到規定的尺寸和表面粗糙度、平行度、垂直度要求。對於相鄰表面的垂直度要求,一般在平面磨床上利用專用夾具定位夾緊後磨削,以保證垂直度要求,精度檢查可以通過直角尺來測量。對於外形表面為矩形和方形的複雜形面的鑲塊和拼塊,一般應進行六個平面的平面磨削,並達到平行度和垂直度要求,以保證後續劃線、加工、測量的需要。
對於外圓柱體或圓錐體的外形表面,在車床上進行車削加工,一般通過一次裝卡,在車削外鏇轉表面的同時車削端面,並可以在中心部位進行鑽孔、鉸孔、鏜孔,以保證各相關表面的同軸度、垂直度等要求。對於尺寸和質量較大的零件,多採用在立式車床上加工,這樣既便於找正和裝卡,又易於保證加工精度;對於中、小型零件多採用普通車床進行加工;對於細長軸類零件,由於剛度較差,應該採取兩端裝卡和支承的辦法來進行車削;對於母線為曲線的鏇轉體零件,多採用數控車床來加工,用型面樣板進行檢查。
2)成形表面的加工
成形表面的分類方法很多,從模具製造工藝的角度考慮有以下幾種情況:
1、按成形表面的實體材料,分為外型面和內型面。
2、當內型面為通孔時,稱為型孔;當內型面為盲孔時,稱為型腔。
3、按型面的截面幾何形狀特徵不同,又分成圓形截面和異形截面曲面。
4、按曲面的可變坐標點數量不同,又分成二維曲面平面曲面、和三維曲面立體曲面。
對於成形表面的加工方法,按照加工的機理不同,可以分成三大類:
1、依靠機械力切削加工的金屬切削加工方法是最古老、套用最廣泛的加工方法,也是模具零件加工的基本方法。
2、利用電能、熱能、光能、化學能做動力的特種加工方法,是一種新型的、有極大發展前途的加工方法,它在模具零件加工中所占地位越來越重要。
3、最後是採用精密鑄造、擠壓成形、超塑成形方法的專門加工,它在某種特定條件下顯示了獨特的優越性。
成形表面不僅尺寸精度要求高,而且表面粗糙度要求也很高。因此,成形表面的加工又分成兩大步驟:
1、尺寸加工,通過各種不同的方法達到設計圖樣所要求的尺寸精度和位置精度。
2、通過研磨和拋光的光整加工,使成形表面達到設計圖樣所要求的表面粗糙度和形狀精度,這對於成形表面尤為重要。
3)結構表面的加工
模具零件的結構表面,由於它們的作用不同,因此形狀也都各異,但是多數為簡單的幾何形狀。從加工方法看,採用一般的金屬切削加工方法都能實現。結構表面中除平面、斜面、圓柱面、圓錐面以外,還有不同截面形狀的通槽、半通槽、不同形狀的台階孔,這些多在工具銑床上進行加工。
對於大、中型平板類零件,中間部位有較大通孔時,劃線後在立銑床上用立銑刀銑削加工,四壁之間以圓弧相聯,圓弧尺寸取決於立銑刀直徑。當在插床上插削中間較大的通孔時,應事先做好預孔,插削後四壁之間呈直角聯接。對於台階形的方孔和異形孔以及方形和異形盲孔,必須在立銑床上或工具銑床上用立銑刀銑削加工,使型孔各垂直平面以圓弧面相。
保管方法
在保管模具時,要注意以下幾點:
1、儲存模具的模具庫,應通風良好,防止潮濕,並便於存放及取出。
2、儲存模具時,應分類存放並擺放整齊。
3、對於小型模具應放在架上保管,大、中型模具應放在架底層或進口處,底面應墊以枕木並墊平。
4、模具存放前,應擦拭乾淨,並在導柱頂端的貯油孔中注入潤滑油後蓋上紙片,以防灰塵及雜物落入導套內影響導向精度。
5、在凸模與凹模刃口及型腔處、導套導柱接觸面上塗以防鏽油,以防長期存放後生鏽。
6、模具在存放時,應在上、下模之間墊以限位木塊特別是大、中型模具、,以避免卸料裝置長期受壓而失效。
7、模具上、下模應整體裝配後存放,決不能拆開存放,以免損壞工作零件。
8、對於長期不使用的模具,應經常檢查其保存完好程度,若發現銹斑或灰塵應及時處理。
發展趨勢
中國模具製造程度已有較大進步。我國塑膠模具增長迅速,比重不斷提高。近年來,我國塑膠模具發展迅速。
據前瞻網《2014-2018年中國模具製造行業產銷需求預測與轉型升級分析報告》調查數據顯示,目前,塑膠模具在整個模具行業中所占比重約為30%,在模具進出口中的比重高達50~70%。隨著中國機械、汽車、家電、電子信息和2006、2008年同期塑膠橡膠模具在模具進出口中所占的比重。
據了解,製造一款普通轎車約需200多件內飾件模具,而製造保險槓、儀錶盤、油箱、方向盤等所需的大中型塑膠模具僅約50%能夠滿足。而塑膠建材大量替代傳統材料也成為所趨,預計2010年全國塑膠門窗和塑管普及率將達到30%~50%,塑膠排水管市場占有率將超過50%,這些都會大大增加對模具的需求。據專家預測,模具市場的總體趨熱是平穩向上的,在未來的模具市場中,塑膠模具的發展速度將高於其它模具,在模具行業中的比例將逐步提高。
模具材料及表面處理技術
模具工業要上水平,材料套用是關鍵。因選材和用材不當,致使模具過早失效,大約占失效模具的45%以上。,因此,選用優質鋼材和套用表面處理技術來提高模具的壽命就顯得十分必要。在模具材料方面新型冷作模具鋼有65Nb、O12A1、CG-2等;模具鋼品種規格多樣化、產品精細化、製品化,儘量縮短供貨時間亦是重要發展趨勢。
在模具表面處理方面,其主要趨勢是:由滲入單一元素向多元素共滲、複合滲發展;由一般擴散向CVD、PVD、PCVD、離子滲入、離子注入等方向發展;可採用的鍍膜有:TiC、TiN、CrN、Cr7C3、W2C等,同時熱處理手段由大氣熱處理向真空熱處理髮展。另外,目前對雷射強化、輝光離子氮化技術、鏡面拋光的模具表面工程技術也受到廣泛的關注。冶煉時要求採用真空脫氣、氬氣保護鑄錠、垂直連鑄連軋、柔鍛等一系列先進工藝,使鏡面模具鋼具內部缺陷少、雜質粒度細、彌散程度高、金屬晶粒度細、均勻度好等一系列優點,以達到拋光至鏡面的模具鋼的要求。
設計製造技術
當代模具的設計與製造廣泛採用計算機輔助設計與製造(CAD/CAM),設計過程程式化和自動化,使用程式、模具擬成形過程、採用互動式設計方法,發揮人和計算機的各自特長。設計與製造之間的直接傳輸便於設計中的反覆修正改變。模具設計與加工方法的發展主要有以下幾方面:
①模具軟體功能集成化
模具軟體功能的集成化要求軟體的功能模組比較齊全,同時各功能模組採用同一數據模型,以實現信息的綜合管理與共享,從而支持模具設計、製造、裝配、檢驗、測試及生產管理的全過程,達到實現最佳效益的目的。集成化軟體較高的軟體還包括:UG、CATIA和Pro/E等。而新一代模具CAD/CAM軟體技術,新一代模具軟體以立體的思想、直觀的感覺來設計模具結構,所生成的三維結構信息能方便地用於模具可製造性評價和數控加工,這就要求模具軟體在三維參數化特徵造型、成型過程模擬、數控加工過程仿真及信息交流和組織與管理方面達到相當完善的程度並有較高集成化水平。
②快速原型法和快速制模技術(RPM/RMT)
該技術是一項集雷射、材料、信息及控制等技術於一體的先進制造技術,其突出特點就是能直接根據產品的CAD數據快捷地製造出具有一定結構和功能的原型甚至產品,而不需要任何工裝夾具,而迭加形成三維實體。RPM技術與RMT技術的結合,將是傳統快速制模技術進一步深入發展的方向。RPM技術與陶瓷型精密鑄造相結合。為模具型腔精鑄成型提供了新途徑。套用RPM/RMT技術從模具的概念設計到製造完成,僅為傳統加工方法所需時間的1/3和成本的1/4左右,因而具有廣闊的發展前景。
③高速銑削技術
高速銑削是目前切削技術中套用最多的一種工藝技術,是一種以高主軸轉速、快速進給、較小的切削深度和間距為加工特徵的高效、高精度數控加工方式。高速銑削具有工件溫度低、切削力小、加工平穩、質量好、效率高(為普遍銑削加工的5~10倍)及可加工硬質材料(<60HRC)等諸多優點,高速銑削工具機(HSM)一般主要用於大、中型模具加工,如汽車覆蓋件模具、變速箱體壓鑄模、大型注塑模等曲面加工,其曲面加工精度可達0.01mm。因而在模具加工中日益受到重視。
專業化生產及標準化
專業化生產是現代工業生產的重要特徵之一,國外工業先進的國家模具專業化生產已達75%以上。。這種專業化小模具廠易於管理,反應靈活,易於提高產品質量和經濟效率,有較強的競爭力。標準化是實現模具專業化生產的基本前提,能系統提高整個模具行業技術水平和經濟效益的重要手段,是機械製造業向深層次發展必由之路。