控制圖的定義
控制圖(Control Chart)又叫管制圖,是對過程質量特性進行測定、記錄、評估,從而監察過程是否處於控制狀態的一種用統計方法設計的圖。圖上有中心線(CL,CentralLine)、上控制線(UCL,UpperControlLine)和下控制限(LCL,LowerControl Line),並有按時間順序抽取的樣本統計量數值的描點序列。UCL、CL、LCL統稱為控制線(Control Line)。中心線是所控制的統計量的平均值,上下控制界限與中心線相距數倍標準差。多數的製造業套用三倍標準差控制界限,如果有充分的證據也可以使用其它控制界限。若控制圖中的描點落在UCL與LCL之外或描點在UCL和LCL之間的排列不隨機,則表明過程異常。
控制圖的誕生
世界上第一張控制圖誕生於1924年5月16日,是由美國貝爾電話實驗室(BellTelephoneLaboratory)質量課題研究小組過程控制組學術領導人休哈特博士提出的不合格品率p控制圖。隨著控制圖的誕生,控制圖就一直成為科學管理的一個重要工具,特別方面成了一個不可或缺的管理工具。它是一種有控制界限的圖,用來區分引起的原因是偶然的還是系統的,可以提供系統原因存在的資訊,從而判斷生產過於受控狀態。控制圖按其用途可分為兩類,一類是供分析用的控制圖,用來控制生產過程中有關質量特性值的變化情況,看工序是否處於穩定受控狀;再一類的控制圖,主要用於發現生產過程是否出現了異常情況,以預防產生不合格品。控制圖的分類
根據控制圖使用目的的不同,控制圖可分為:分析用控制圖和控制用控制圖。
根據統計數據的類型不同,控制圖可分為:計量控制圖和計數控制圖(包括計件控制圖和計點控制圖)。它們分別適用於不同的生產過程。每類又可細分為具體的控制圖,最初主要包含七種基本圖表。
計量型控制圖包括:
*IX-MR(單值移動極差圖)
*Xbar-R(均值極差圖)
*Xbar-s(均值標準差圖)
計數型控制圖包括:
*P(用於可變樣本量的不合格品率)
*Np(用於固定樣本量的不合格品數)
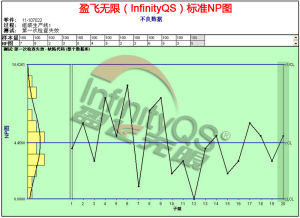
*u(用於可變樣本量的單位缺陷數)
*c(用於固定樣本量的缺陷數)
帕累托圖(排列圖)
帕累托圖(Paretochart)是以義大利經濟學家V.Pareto的名字而命名的。帕累托圖又叫排列圖、主次圖,是按照發生頻率大小順序繪製的直方圖,表示有多少結果是由已確認類型或範疇的原因所造成。
傳統的帕累托圖通過簡單易懂的條形圖格式來進行缺陷代碼的顯示和原因分析。鑒於它的簡便性,帕累托圖一直都沒有被作為一個高效的SPC控制圖分析工具來使用。
由於科技的發展和SPC理論的不斷延伸,帕累托圖已由最開始的單級(一級)帕累托圖發展成為多級(最多6級)帕累托圖。
假設在一條發動機總裝線上要進行產品最終外觀檢測,檢查缺陷數並分類記錄。在下圖中可以看到傳統帕累托圖顯示的結果。圖上清楚地顯示出油漆污點是最多的缺陷問題。
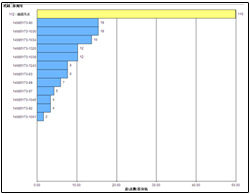
隨著科技發展,在一些專業的SPC軟體中,除了零件型號、過程設備以及測試項目等信息會與最終數據聯繫在一起之外,您還可以加入完全不受數量限制的用戶自定義描述符。數據錄入之後,系統可以將數據按照任意描述符進行分類。在本例中,工程師們也許想知道指定序列號(描述符)發動機是否存在某種特定的缺陷。具體如下圖:
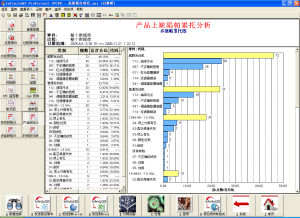
多級圖可以將一個帕累托圖嵌套到另一個帕累托圖中,通過二維視角審視缺陷數量以及它的來源,而管理者也將因此看到,多級帕累托圖會比簡單傳統的帕累托圖帶來更重要的信息。
明確控制圖的“是”與“非”
針對企業的特殊生產條件,如何選擇最適合自己的SPC控制圖?解決這個問題根本在於掌握定義圖表類型的要素有哪些。但在此之前,讓我們先對控制圖下個定義:SPC控制圖究竟是什麼?控制圖是:
1.實時圖表化反饋過程的工具。
2.設計的目的是告訴操作者什麼時候做什麼或不做什麼。
3.按時間序列展示過程的個性/表現。
4.設計用來區分信號與噪音。
5.偵測均值及/或標準差的變化。
6.用於決定過程是穩定的(可預測的)或失控的(不可預測的)。
控制圖不是:
1.不是能力分析的替代工具。
2.在來料檢驗的過程中很難用到(沒有時間序列)。
3.控制圖不是高效的比較分析工具。
4.不應與運行圖或預控制圖混淆。
控制圖套用“界限”區分過程是否有顯著變化或存在異常事件。由於控制限的設定要以數據為基礎,所以在收集一定量有代表性的數據之前是無法確定控制限的。如果錯誤使用控制限,不但會對使用者造成困擾,而且還會對那些通過圖表監控以實現過程改進的措施起反作用。
控制圖的作用
在生產過程中,產品質量由於受隨機因素和系統因素的影響而產生變差;前者由大量微小的偶然因素疊加而成,後者則是由可辨識的、作用明顯的原因所引起,經採取適當措施可以發現和排除。當一生產過程僅受隨機因素的影響,從而產品的質量特徵的平均值和變差都基本保持穩定時,稱之為處於控制狀態。此時,產品的質量特徵是服從確定機率分布的隨機變數,它的分布(或其中的未知參數)可依據較長時期在穩定狀態下取得的觀測數據用統計方法進行估計。分布確定以後,質量特徵的數學模型隨之確定。為檢驗其後的生產過程是否也處於控制狀態,就需要檢驗上述質量特徵是否符合這種數學模型。為此,每隔一定時間,在生產線上抽取一個大小固定的樣本,計算其質量特徵,若其數值符合這種數學模型,就認為生產過程正常,否則,就認為生產中出現某種系統性變化,或者說過程失去控制。這時,就需要考慮採取包括停產檢查在內的各種措施,以期查明原因並將其排除,以恢復正常生產,不使失控狀態延續而發展下去。通常套用最廣的控制圖是W.A.休哈特在1925年提出的,一般稱之為休哈特控制圖。
如何選擇控制圖
選擇正確的控制圖一方面要清楚,企業希望通過圖表看到哪些內容?即,希望控制圖回答什麼問題?另一方面還要明確,“為什麼要收集這些零件的數據?”這些問題的答案可以為抽樣方案的制定、樣本量以及需要進行任何特殊處理來拓展傳統控制圖功能的特殊需求提供重要支撐。
選擇控制圖需要考慮以下幾個關鍵因素:
A . 樣本量
樣本量是對給定測試的測試值數量。它用收集的數據來代表一個“時間快照”,通常用符號n表示。例如,如果每30分鐘抽取連續3個灌裝瓶的重量,則樣本量為3,抽樣間隔為30分鐘。需要說明的是:樣本量不代表描在圖上的點數。生產中,有三種樣本量需要注意區分:
1.樣本量為1(n=1)
2.樣本量為2到9之間(2≤n≤9)
3.樣本量大於或等於10(n≥10)
當樣本量為1時,應使用單值移動極差圖(IX-MR);樣本量為2到9之間時,應使用均值極差圖(Xbar-Range);樣本量大於或等於10時,則應使用均值標準差圖(Xbar-Sigma)。這三種核心變數控制圖是基礎。絕大多數其他變數控制圖都源於這三種控制圖中的某一種。
B. 過程流數量
如果要分析一個產生多過程流的生產過程,您可以選擇每個過程流用一張控制圖,或者用特殊的圖表將所有過程流放在同一張圖上。這種同時監控多個過程流的圖表叫做組圖(GroupCharts)。
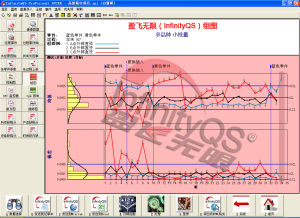
C. 相同特性,不同目標值
相同過程通常都會用來生產不同的產品。大多數情況下,換線意味著改變過程設定,從而生產其他產品。繼續上文所說的灌裝案例,當生產線從50ml瓶裝換至100ml瓶裝,雖然用相同的灌裝頭,但灌裝程式要設定為100ml瓶裝。如果要監控過程保持設定值的能力,那么不管生產什麼產品,都可通過數據對多個設定值進行整合。您只需要通過實際測量值減去設定值就可以了。例如,灌裝量為100.3,則圖表上鵝描點為0.3。通過減去目標值,一張圖可以按時間順序對過程保持設定值的能力進行監控,而無需考慮生產產品的公差值。這類圖叫目標值控制圖。只要這些產品具有相似的波動,多個零件就可以放在同一張圖上。目標值控制圖特別適用於多品種、小批量的生產環境。