連軋機控制系統
正文
由連軋機組、檢測儀表控制裝置和電子計算機組成的對鋼鋁等材料的加工尺寸進行控制的塑性加工過程控制系統。早期的連軋機因軋制速度低,對產品質量要求也不高,用人工控制尚能生產。人們對產品質量和產量的要求日益提高,如軋制每卷重45噸的冷連軋薄帶鋼卷,要求厚度公差為±(5~50)微米,冷連軋機最高軋速達40米/秒以上,熱連軋年產量達 500萬噸以上,冷連軋年產達 100萬噸以上。這樣的任務再用人工控制已不可能完成。20世紀60年代後期,連軋機開始採用計算機控制,70年代以來發展較快。例如中國武漢鋼鐵公司70年代末投產的1700毫米帶鋼熱連軋機,500米長的軋制生產線全部採用計算機控制。控制功能主要包括軋件跟蹤、計算機操作指導和對軋制過程各種參數設定、連續檢測、控制和最優管理。下圖為五機架冷連軋機利用17台計算機組成集散控制系統,在主控制台的控制下,分為過程監控、操作監控和設備監控三級,包括各種自動檢測儀表、電子裝置、液壓裝置等組成的局部控制系統。按功能來分,整套軋機控制系統分為速度調節系統、壓下位置控制系統、軋制力調節系統、張力調節系統、厚度調節系統,以及自動制動系統、彎輥數字控制系統、板型控制系統、側導板自動控制系統、自動換輥系統、進出料自動控制系統等。從上卷、穿帶、軋制參數設定直到軋制厚度控制和數據記錄列印等已全部實現自動化。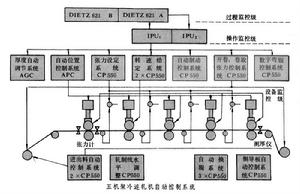
壓下位置控制系統 用以快速準確地調節軋機輥縫的開口度。現代大型軋機的軋輥機構重達幾十噸,為了適應高速軋制的快速回響需要,一般採用液壓伺服調節系統。它由微型計算機或電子調節線路、電液伺服閥、能產生上千噸壓力的大型液壓缸、精密位移感測器等組成,其位置調節解析度機達1~2微米,回響頻寬一般為8~12赫。
軋制力調節系統 主要用以補償軋輥偏心所造成的軋制力波動。由測壓頭或油壓測量感測器測出軋制力值,再將其變換為電信號,輸入微型機或電子調節線路去調節液壓壓下位置,使壓下系統能跟隨軋輥的偏心運動而實現軋制力的補償調節,減少由於軋制力波動所造成的周期性厚度偏差。軋制力調節系統的設定值一般由張力或厚度調節系統給定。
張力調節系統 用於調節各軋機間帶鋼的張力並使其保持穩定。冷軋機處於大張力軋制狀態時,各架軋機間的帶鋼張力可達10噸以上。過大的張力波動會造成斷帶或疊軋等事故。一般用張力輥直接檢測機架間的帶鋼張力,由電子計算機通過調節後一機架的液壓壓下位置來達到調節張力的目的。如果機架間張力低於工藝控制數學模型所選定的最佳張力給定值,則可以增大後一架軋機的輥縫開口度,使軋出帶鋼的體積流量增大,由此產生的帶鋼彈性張力積分效應便使機架間帶鋼張力隨之升高,達到給定值。如果軋機控制系統中具有軋制力調節系統,則張力調節系統的調節量就被輸出作為軋制力調節系統的給定值,同樣也能達到調節和穩定張力的目的。開卷機和卷取機產生的帶鋼張力,通過調節其傳動電機張力電流的方法來加以調節。在張力設定值不變的情況下,鋼卷直徑隨著軋制進程不斷發生變化。因此,由計算機組成的張力調節系統也要不斷計算,得出新的張力電流給定值,以保持開卷機和卷取機的張力穩定。
厚度調節系統 用以保證連軋機軋出的帶鋼在整個長度範圍內均勻一致或達到預定的厚度範圍。調節系統一般分為入口段厚度和出口段厚度調節兩個部分。
①軋機入口段的厚度調節系統 帶鋼坯料剛開始軋入軋機時,材料加工硬化尚不顯著,容易產生塑性變形,因此由坯料帶入的大部分厚度不均勻偏差都儘量在入口段厚度調節系統中加以消除。通常在軋機入口處裝設γ射線測厚計,測量進入軋機的帶鋼厚度,並將測得的厚度偏差信號送至計算機。計算機根據模型計算所得出的帶鋼塑性係數,可以算出第一架軋機液壓壓下位置的前饋調節量。如果計算機計算模型準確,則部分來料厚度偏差可以通過前饋調節補償克服。剩餘厚度偏差由裝在第一架和第二架軋機間的γ射線測厚計測出,並通過信號反饋調節來進一步消除。這一帶鋼厚度偏差信號同時也可用於實現第二架軋機的前饋厚度調節。
②軋機出口段的厚度調節系統 經過入口段調節以後,帶鋼厚度偏差已經大部分被克服。為了進一步提高軋出帶鋼的質量,使厚度公差保持在±(5~10)微米以內,最後在第4、第5架軋機上再設定厚度精調系統。帶鋼經過前幾架軋機軋制,加工硬化效應使帶鋼塑性係數增大,帶鋼變得很硬,很難依靠調節軋機的壓下位置來精調厚度,所以一般套用軋機出口處的γ射線測厚計所測得的厚度偏差作為反饋信號來調節第4、第5架軋機的張力。把改變張力作為主要的調節手段,而把改變軋制力作為輔助的調節手段。
展望 用戶不僅對帶鋼長度方向的尺寸要求嚴格,對橫向尺寸公差的要求也日益提高,因此帶鋼橫截面板形的測量和控制系統也開始套用。它通過測量帶鋼橫向分段張力的方法來計算板形,並對液壓彎輥裝置反饋控制以調節板形。另外,壓下負荷分配的合理選擇,對改進板形也有一定的成效。70年代以來,又出現了全連續式的冷連軋機,在入口側加了焊接鋼卷的焊機和存儲鋼帶的活套車。由電子計算機控制整個軋制過程,可自動改變軋制規格和軋機的設定值。軋後由飛剪下斷、分卷,軋制每卷鋼帶時無需穿帶和甩尾,能節省換卷間隙時間,消除鋼卷頭尾厚度超出公差的廢品,提高帶材軋制精度和收得率。80年代的連軋機自動控制系統趨於採用多級計算機控制,把軋鋼自動控制系統與工廠或公司的自動控制系統相聯,構成一個大系統,套用大系統理論和系統工程的方法和技術,實現整個工廠或公司的最優控制和管理。
冷連軋
用熱軋鋼卷為原料,經酸洗去除氧化皮後進行冷連軋,其成品為軋硬卷,由於連續冷變形引起的冷作硬化使軋硬卷的強度、硬度上升、韌塑指標下降,因此衝壓性能將惡化,只能用於簡單變形的零件。軋硬卷可作為熱鍍鋅廠的原料,因為熱鍍鋅機組均設定有退火線。軋硬卷重一般在6~13.5噸,鋼卷內徑為610mm。一般冷連軋板、卷均應經過連續退火(CAPL機組)或罩式爐退火消除冷作硬化及軋制應力,達到相應標準規定的力學性能指標。
冷軋鋼板的表面質量、外觀、尺寸精度均優於熱軋板,且其產品厚度右軋薄至0.18mm左右,因此深受廣大用戶青睞。
以冷軋鋼卷為基板進行產品的深加工,成為高附加值產品。如電鍍鋅、熱鍍鋅、耐指紋電鍍鋅、彩塗鋼板卷及減振複合鋼板、PVC復膜鋼板等,使這些產品具有美觀、高抗腐蝕等優良品質,得到了廣泛套用。
冷軋鋼卷經退火後必須進行精整,包括切頭、尾、切邊、矯平、平整、重卷、或縱剪下板等。冷軋產品廣泛套用於汽車製造、家電產品、儀表開關、建築、辦公家具等行業。鋼板捆包後的每包重量為3~5噸。平整分卷重一般為3~10噸/卷。鋼卷內徑610mm。
冷連軋機組
機組特點1、大壓下率:3.0mm厚的帶鋼經五個機架一次軋制到0.3mm,可以覆蓋大部分鍍鋅基板的需求。
2、全連續:從開卷到卷取實現全連續生產,為此,機組配置有自動焊機、入口活套、出口飛剪和雙工位卷取機。
3、高精度:為保證產品厚度精度和良好板形,生產線的五個機架全部配置為六輥全液壓(AGC)軋機。
4、低投入:整條生產線的投資相當於兩條高配置六輥可逆軋機的投資,或只有進口同類生產線的1/4(按噸鋼產能計算)。
5、高效益:與可逆軋機相比,由於厚控精度和成材率提高和人員成本降低,噸鋼成本可以降低50元。
三、技術性能
設備型號
帶鋼寬度(mm)
帶鋼厚度(mm)
軋制力(T)
軋制速度
(m/min)
年產量(T)
YW-WLZ1450
900-1250
0.2~1.2
1800
600
500000
YW-WZ1250
800-1100
0.2~1.2
1500
600
400000
YW-WZ1050
600-900
0.2~1.2
1100
600
300000
四、技術特點:
1、生產線全數字直流調速,張力閉環控制、速度自動控制;
2、五機架全液壓(AGC)自動厚度控制,包括預控AGC、監控AGC和流量AGC;
3、工作輥正負彎輥,中間輥正彎輥及橫移控制;軋輥分段冷卻控制;
4、基礎自動化和過程自動化完備,採用西門子PLC;
5、採用雙開卷、閃光對焊、臥式活套;
6、採用雙工位CAROSAL卷取機
7、系統數據採集、顯示、存儲和輸出系統,包括故障診斷和報警;
8、主機全部採用六輥軋機;
9、具備過焊縫自動降速、減張等功能
10、軋輥快速換輥;
11、軋輥全部採用油氣潤滑;
12、採用先進平床+鐵磁過濾工藝潤滑
五、設備組成:
機械設備主要有上/卸卷小車、開卷機、夾送矯直機、焊機、活套、張力輥、對中裝置、五機架全六輥液壓AGC軋機、快速換輥車、飛剪、卷取機和助卷器等;另外還包括電控系統、液壓系統、工藝潤滑系統、油氣潤滑和稀油潤滑系統等。
六、工藝流程:
上卷—→開卷—→夾送、矯直—→焊接—→活套—→測厚—→五機架連軋
—→測厚—→飛剪—→卷取—→卸卷
熱連軋
熱連軋是一種生產鋼材的方式,用連鑄板坯或初軋板坯作原料,經步進式加熱爐加熱,高壓水除磷後進入粗軋機,粗軋料經切頭、尾、再進入精軋機,實施計算機控制軋制,終軋後即經過層流冷卻(計算機控制冷卻速率)和卷取機卷取、成為直髮捲。直髮捲的頭、尾往往呈舌狀及魚尾狀,厚度、[1]寬度精度較差,邊部常存在浪形、折邊、塔形等缺陷。其卷重較重、鋼卷內徑為760mm。熱連軋機組
熱連軋機(Hotcontinuousrollingmill)是生產熱軋卷板的軋鋼設備,熱連軋作業線裝備通常包括:步進式連續加熱爐,高壓水除鱗置,帶立輥四輥可逆式萬能粗軋機,飛剪,由6架串列布置的四輥軋機組成的精軋機組,卷取機,層流冷卻裝置,成品收集設備和各種運輸輥道。熱連軋生產過程:鋼坯通過加熱出爐後,通過高壓水除鱗去除氧化鐵皮,進入四輥可逆式粗軋機進行開坯,軋製成適合連軋機組軋制的中間坯料.開坯過程中立輥保證鋼板精確的寬度,中間坯經飛剪剪頭後,進入連軋機組.一次軋製成所需的規格,最後由卷取機收卷。.軋制過程中,粗、精軋機均有高壓水對鋼板進行二次除鱗。
熱連軋機組通常採用全線自動化控制,並採用液壓AGC厚度自動控制、強力彎輥系統、快速換輥等新技術。上世紀八十年代,熱連軋生產廣泛採用薄板坯連鑄連軋技術,從煉鋼,連鑄經均熱後坯料直接進入軋線。形成短流程、能耗低、生產效率高的工藝特點,使熱帶鋼軋制進入了新的時期。
近年來,熱軋複合板技術的發展,成功在熱連軋機組生產不鏽鋼複合卷板,以滿足市場對不鏽鋼複合卷帶的需求,成為熱連軋生產增加了新的品種。
參考書目
G.F.Bryant,Automation of tandem Mills, The Iron &Steel Institute,London,1973.
孫一康:《熱軋帶鋼計算機控制數學模型》,冶金工業出版社,北京,1980。