正文
現代煉鐵的主要方法,鋼鐵生產中的重要環節。這種方法是由古代豎爐煉鐵發展、改進而成的。儘管世界各國研究發展了很多新的煉鐵法,但由於高爐煉鐵技術經濟指標良好,工藝簡單,生產量大,勞動生產率高,能耗低,這種方法生產的鐵仍占世界鐵總產量的95%以上。
高爐生產時從爐頂裝入鐵礦石、焦炭、造渣用熔劑(石灰石),從位於爐子下部沿爐周的風口吹入經預熱的空氣。在高溫下焦炭(有的高爐也噴吹煤粉、重油、天然氣等輔助燃料)中的碳同鼓入空氣中的氧燃燒生成的一氧化碳和氫氣,在爐內上升過程中除去鐵礦石中的氧,從而還原得到鐵。煉出的鐵水從鐵口放出。鐵礦石中不還原的雜質和石灰石等熔劑結合生成爐渣,從渣口排出。產生的煤氣從爐頂導出,經除塵後,作為熱風爐、加熱爐、焦爐、鍋爐等的燃料。高爐冶煉流程見圖。
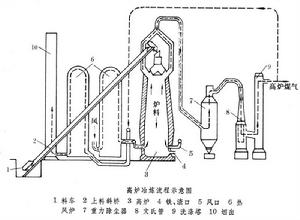
早期高爐使用木炭或煤作燃料,18世紀改用焦炭,19世紀中葉改冷風為熱風(見冶金史)。20世紀初高爐使用煤氣內燃機式和蒸汽渦輪式鼓風機後,高爐煉鐵得到迅速發展。20世紀初美國的大型高爐日產生鐵量達 450噸,焦比1000公斤/噸生鐵左右。70年代初,日本建成4197米 高爐,日產生鐵超過1萬噸,燃料比低於 500公斤/噸生鐵。中國在清朝末年開始發展現代鋼鐵工業。1890年開始籌建漢陽鐵廠,1號高爐(248米 ,日產鐵100噸)於1894年5月投產。1908年組成包括大冶鐵礦和萍鄉煤礦的漢冶萍公司。1980年,中國高爐總容積約8萬米 ,其中1000米 以上的26座。1980年全國產鐵3802萬噸,居世界第四位。
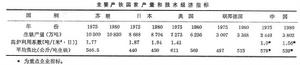
70年代末全世界2000米 以上高爐已超過120座,其中日本占1/3,中國有四座。全世界4000米 以上高爐已超過20座,其中日本15座,中國有1座在建設中。
50年代以來,中國鋼鐵工業發展較快,高爐煉鐵技術也有很大發展,主要表現在:①綜合採用精料、上下部調劑、高壓爐頂、高風溫、富氧鼓風、噴吹輔助燃料(煤粉和重油等)等強化冶煉和節約能耗新技術,特別在噴吹煤粉上有獨到之處。1980年中國重點企業高爐平均利用係數為1.56噸/(米 ·日),焦比為539公斤/噸生鐵;②綜合利用含釩鈦的鐵礦石取得了突破性進展,含稀土的鐵礦石的利用也取得了較大的進展。
高爐冶煉主要技術經濟指標分述如下:
高爐利用係數 每立方米高爐有效容積一晝夜生產生鐵的噸數,是衡量高爐生產效率的指標。比如1000米 高爐,日產2000噸生鐵,則利用係數為 2噸/(米 ·日)。
焦比 每煉一噸生鐵所消耗的焦炭量,用公斤/噸生鐵表示。高爐焦比在 80年代初一般為450~550公斤/噸生鐵,先進的為 380~400公斤/噸生鐵。焦炭價格昂貴,降低焦比可降低生鐵成本。
燃料比 高爐採用噴吹煤粉、重油或天然氣後,折合每煉一噸生鐵所消耗的燃料總量。每噸生鐵的噴煤量和噴油量分別稱為煤比和油比。此時燃料比等於焦比加煤比加油比。根據噴吹的煤和油置換比的不同,分別折合成焦炭(公斤),再和焦比相加稱為綜合焦比。燃料比和綜合焦比是判別冶煉一噸生鐵總燃料消耗量的一個重要指標。
冶煉強度 每晝夜高爐燃燒的焦炭量與高爐容積的比值,是表示高爐強化程度的指標,單位為噸/(米 ·日)。
休風率 休風時間占全年日曆時間的百分數。降低休風率是高爐增產的重要途徑。一般高爐休風率低於2%。
生鐵合格率 化學成分符合規定要求的生鐵量占全部生鐵產量的百分數,是評價高爐優質生產的主要指標。
生鐵成本 是從經濟方面衡量高爐作業的指標。
參考書目
東北工學院煉鐵教研室:《高爐煉鐵》,中冊,冶金工業出版社,北京,1978。
《中國煉鐵三十年》編輯小組:《中國煉鐵三十年》,冶金工業出版社,北京,1981。
相關知識
煉鐵的原理
(怎樣從鐵礦石中煉出鐵)用還原劑將鐵礦石中的鐵氧化物還原成金屬鐵。鐵氧化物(Fe2O3、Fe3O4、FeO)+還原劑(C、CO、H2)鐵(Fe)
反應的化學方程式分別為Fe2O3+3CO=2Fe+3CO2,Fe3O4+4CO=3Fe+4CO2(反應條件——高溫)等
煉鐵的方法
(1)直接還原法(非高爐煉鐵法)
(2)高爐煉鐵法(主要方法)
原料作用
(1)鐵礦石:(一般為赤鐵礦、磁鐵礦)提供鐵元素。
冶煉一噸鐵大約需要1.5—2噸礦石。
(2)焦炭:提供熱量;提供還原劑;作料柱的骨架。
冶煉一噸鐵大約需要500Kg焦炭。
反應方程式C(焦炭)+O2=CO2
C焦炭+CO2=2CO
(3)熔劑:(石灰石、白雲石、螢石)
使爐渣熔化為液體;去除有害元素硫(S)、除去雜質
(4)空氣:為焦碳燃燒提供氧、提供熱量
操作規程
1 高爐內襯耐火材料、填料、泥漿等,應符合設計要求,且不得低於國家標準的有關規定。
2風口平台應有一定的坡度,並考慮排水要求,寬度應滿足生產和檢修的需要,上面應鋪設耐火材料。
3 爐基周圍應保持清潔乾燥,不應積水和堆積廢料。爐基水槽應保持暢通。
4 風口、渣口及水套,應牢固、嚴密,不應泄漏煤氣;進出水管,應有固定支撐;風口二套,渣口二、三套,也應有各自的固定支撐。
5 高爐應安裝環繞爐身的檢修平台,平台與爐殼之間應留有間隙,檢修平台之間宜設兩個走梯。走梯不應設在渣口、鐵口上方。
6 為防止停電時斷水,高爐應有事故供水設施。
7 冷卻件安裝之前,套用直徑為水管內徑0.75~0.8倍的球進行通球試驗,然後按設計要求進行水壓試驗,同時以0.75kg的木錘敲擊。經10min的水壓試驗無滲漏現象,壓力降不大於3%,方可使用。
8 爐體冷卻系統,應按長壽、安全的要求設計,保證各部位冷卻強度足夠,分部位按不同水壓供水,冷卻器管道或空腔的流速及流量適宜。並應滿足下列要求:
——冷卻水壓力比熱風壓力至少大0.05MPa;
——總管測壓點的水壓,比該點到最上一層冷卻器的水壓應至少大0.1MPa;
——高爐風口、渣口水壓油設計確定;
——供水分配管應保留足夠的備用水頭,供高爐後期生產及冷卻器由雙聯(多聯)改為單聯時使用;
——應制定因冷卻水壓降低,高爐減風或休風后的具體操作規程。
9 熱電偶應對整個爐底進行自動、連續測溫,其結果應正確顯示於中控室(值班室)。採用強制通風冷卻爐底時,爐基溫度不宜高於250℃;應有備用鼓風機,鼓風機運轉情況應顯示於高爐中控室。採用水冷卻爐底時,爐基溫度不宜高於200℃。
10 採用汽化冷卻時,汽包應安裝在冷卻器以上足夠高的位置,以利循環。汽包的容量,應能在最大熱負荷下1h內保證正常生產,而不必另外供水。
11 汽包的設計、製作及使用,應遵守下列規定:
——每個汽包應有至少兩個安全閥和兩個放散管,放散管出口應指向安全區;
——汽包的液位、壓力等參數應準確顯示在值班室,額定蒸發量大於4t/h時,應裝水位自動調節器;蒸發量大於2t/h時,應裝高、低水位警報器,其信號應引至值班室;
——汽化冷卻水管的連線不應直角拐彎,焊縫應嚴密,不應逆向使用水管(進、出水管不能反向使用);
——汽化冷卻應使用軟水,水質應符合GB1576的規定。