世界鋼鐵工業
正文
鋼鐵工業系指生產生鐵、鋼、鋼材、工業純鐵和鐵合金的工業,是世界所有工業化國家的基礎工業之一。經濟學家通常把鋼產量或人均鋼產量作為衡量各國經濟實力的一項重要指標。產量 煉鐵和煉鋼的大工業生產分別於17世紀20年代和19世紀70年代最先在英國發展起來,以後在聯邦德國、法國、美國、俄國、日本等國陸續得到發展。世界主要鋼鐵生產國曆年鋼產量示於表1(中國的歷年鋼產量見中國近代冶金工業和中國現代鋼鐵工業)。
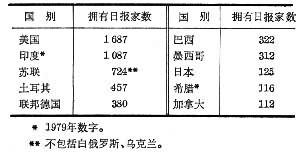
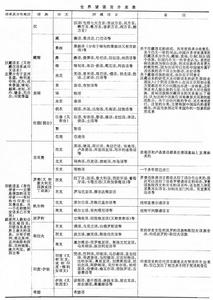
英國的鋼產量在1885年以前、生鐵產量在1889年以前的長時期內,一直居世界首位。美國的鋼產量和生鐵產量分別於1886和1890年躍居世界第一位,並保持了八十多年之久。蘇聯生鐵產量從1970年起居世界首位,鋼產量1971年首次超過美國,1974年以後一直居世界第一。1980年日本鋼產量占第二位,以下依次為美國、聯邦德國、中國、義大利、法國、英國。在主要產鋼國中,日本鋼產量增長速度最快。日本年產鋼量從2000萬噸增加到1億噸只用了13年,蘇聯花了18年,而美國經歷了48年。在相應期間內,鋼產量年平均增長率,日本高達13.8%,蘇聯為8.6%,而美國僅為3.4%。近十幾年來,開發中國家和地區鋼鐵工業發展最快的是南韓,其鋼產量1970年僅為48萬噸,1980年即達860萬噸,十年間平均每年遞增33.4%。其次是巴西,1980年鋼產量達1534萬噸,1971~1980年期間年平均增長率為11%。
生產規模 鋼鐵生產設備和企業規模一直向大型化方向發展。例如,1870年前後英國高爐平均日產生鐵25噸,1969年即增至800噸以上,1979年又增至1370噸。1980年日本高爐平均日產生鐵高達3660噸。1981年6月,全世界2000立方米以上的高爐有126座,3000立方米以上的45座,4000立方米以上的23座,5000立方米以上的3座。日本平均每座氧氣頂吹轉爐的生產能力,1962年7月僅為43萬噸,1972年12月即增至118萬噸,1982年6月又增至140萬噸;世界帶鋼熱連軋機的年產能力,1960年以前建造的,絕大多數在 200萬噸以下,60年代投產的高水平軋機為350~450萬噸,70年代建成的現代化軋機高達500~600萬噸。
近年來的設備大型化和自動化使得鋼鐵聯合企業生產規模迅速增大(表3)。1980年全世界年產鋼 500萬噸以上的鋼鐵廠有50個左右,其中蘇聯14個,日本13個,美國6個。年產鋼量最大的鋼鐵廠是日本鋼管公司福山廠,1976年產鋼達1919萬噸。累計產鋼最多的是蘇聯馬格尼托哥爾斯克鋼鐵公司(實際上為一個鋼鐵廠),至1982年2月共產鋼3.7億噸;其次是新日本鋼鐵公司八幡廠,至1982年初共產鋼 2.2億噸。全世界產量最大的是新日本鋼鐵公司,1973年產鋼4107萬噸,從建廠至1982年初的95年中,累計產鋼達6.5億噸。
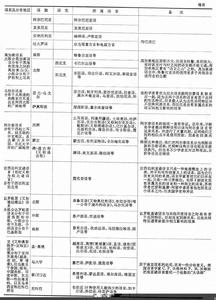
企業建設 增大鋼鐵生產能力的方式有三種:新建企業、擴建和改造原有企業。近二十年來,日本、南韓和巴西等國和地區主要靠新建大型鋼鐵企業大幅度地提高鋼鐵生產能力,而蘇聯和美國等,則以擴建和改造原有企業為主,以新建企業為輔。過去大型鋼鐵廠大多建在靠近鐵礦和煤礦或靠近其中之一的地方,或建在靠近鋼材消費市場的地方。近二十多年來,日本、義大利、荷蘭、法國、南韓等國或地區在沒有煤鐵資源的沿海建造了大型鋼鐵廠,如日本共建成21個沿海鋼鐵廠,其中年產鋼500萬噸以上的多達13個(見彩圖) 採用電爐-連鑄機-小軋機的小鋼廠,則多建在廢鋼充足、靠近用戶的中小城市。
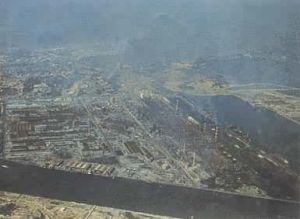
生產技術 隨著世界經濟和科學技術的發展,對鋼鐵需求量日益增長,對鋼材質量要求越來越高,加上資源條件的變化,生產技術不斷發展。
高爐 高爐煉鐵在煉鐵生產中一直占主導地位,並向著大型化、自動化和高效率的方向發展。70年代中期高爐大型化達到了高峰,1976年日本新日本鋼鐵公司大分廠投產的 2號高爐(內容積5070立方米)是世界最大的高爐,蘇聯計畫在第十一個五年計畫期間(1981~1985)將建成5580立方米巨型高爐。在操作技術上,通過改善入爐原料質量,提高熱風溫度和爐頂壓力,採用噴吹技術,回收利用二次能源,從而達到高產、優質、低耗。
在主要產鋼國家中日本和義大利的焦比最低 (500公斤/噸以下),1981年日本鋼管公司福山廠3號高爐創燃料比 396公斤的世界紀錄;大中型高爐最佳利用係數一般為每晝夜2.0~2.3噸/米3 。80年代初高爐主要在節能、回收利用二次能源、提高爐體壽命和自動化水平、加強環境保護等方面改進生產工藝技術和裝備。由於高品位優質鐵礦日益減少,選礦量增多,熟料比提高,除不斷提高燒結質量外,球團比重也日益增加。直接還原煉鐵,特別是以煤為還原劑的直接還原技術將得到進一步發展。
煉鋼 在煉鋼生產中,氧氣頂吹轉爐煉鋼發展迅速尤以日本、聯邦德國、法國等國家發展較快。1970年世界氧氣頂吹轉爐鋼的產量超過平爐鋼而居各種煉鋼方法的首位。80年代初,轉爐鋼和電爐鋼的比例不斷增加,平爐作為傳統的主要煉鋼設備正在逐漸退出歷史舞台。氧氣頂吹轉爐的容量不斷擴大,1982年世界大於200噸的轉爐的生產能力約占氧氣頂吹轉爐總的生產能力(5.28億噸)一半以上。目前世界最大的氧氣頂吹轉爐是聯邦德國奧古斯特·蒂森鋼鐵公司的400噸轉爐。同時,氧氣頂吹轉爐煉鋼技術已臻完善,各項技術經濟指標達到了相當先進的水平,每公稱噸位年產量達1.5萬噸以上;爐齡一般為1000~2000爐,最高達 10110爐;耐火材料單耗為2~5公斤/噸鋼,最先進的僅為0.57公斤/噸鋼;煉鋼工序能耗降至很低,有些轉爐還實現了“零能”或“負能”煉鋼。普遍採用計算機控制冶煉過程,一些國家的轉爐實現了全自動化煉鋼。氧氣頂吹轉爐冶煉的鋼種不斷擴大,與爐外精煉相結合可以生產許多特殊鋼和合金鋼。日本約62%、聯幫德國約40%的特殊鋼、美國約45%的合金鋼都是用氧氣頂吹轉爐生產的。1980年世界氧氣頂吹轉爐鋼產量占鋼總產量的55%以上。
繼氧氣頂吹轉爐煉鋼問世後,60年代後期出現氧氣底吹轉爐煉鋼。目前世界最大的氧氣底吹轉爐是1977年日本川崎鋼鐵公司千葉廠投產的兩座 235噸氧氣底吹轉爐,年產能力為400萬噸。兼有氧氣頂吹和氧氣底吹轉爐優點的“複合吹煉轉爐煉鋼”於1979年首先在日本投入工業生產,顯示出更大的技術經濟優勢,受到各國重視,發展十分迅速。為了使氧氣轉爐經濟地生產低硫鋼、低磷鋼,鐵水預處理技術發展很快,套用相當普遍,實現了在混鐵車中同時脫磷、硫、矽的技術,可使鐵水中磷降至<0.01%、硫≤0.002%、矽接近於零。
20世紀50年代以來,電弧爐煉鋼產量顯著增加,電爐鋼產量占鋼總產量的比例由1950年的 6.9%上升到1980年的21%。目前世界最大容量的電弧爐是美國西北鋼和線材公司 360噸的超高功率電爐。大中型爐的單位壓變器容量進一步提高 (≥700千伏安/噸鋼),同時採用氧-油燒嘴和水冷爐壁、水冷爐蓋,實現快速熔煉。爐外精煉和噴射冶金技術的迅速發展,使電弧爐煉鋼工藝發生了很大變化,縮短了冶煉時間,提高了鋼的質量。目前真空脫氣RH裝置的最大處理容量為 300噸(美國國家鋼鐵公司威爾頓廠和日本新日本鋼鐵公司大分廠);DH裝置的最大處理容量達 400噸(聯邦德國奧古斯特·蒂森鋼鐵公司布魯克豪森廠)。爐外精煉設備中,美國阿姆科公司巴特勒廠的 175噸AOD爐,蘇聯引進的兩座150噸ASEA-SKF爐,瑞典烏德霍姆公司德耶福爾斯廠70噸的CLU爐是同類設備中最大的。近幾年來發展了超高功率電爐泡沫渣長弧冶煉、複合水冷電極和電爐廢氣預熱廢鋼等新技術。同時出現了等離子電弧爐、直流電弧爐和連續裝料電爐。
連續鑄鋼 在世界範圍內得到了普遍重視,技術上比較成熟,發展很快。世界連鑄比由1970年的6%增加到1980年的30%,1981年丹麥(95.8%)、芬蘭(91.9%)、日本(70.7%)的連鑄比居世界前三名。1982年世界連鑄機達到1100多套,年產能力超過了 2億噸。為了與高效、大容量的煉鋼設備相匹配,連鑄機正日趨大型化,鑄坯斷面不斷擴大。目前生產的最大方坯為450×450毫米(蘇聯),最大扁坯為700×355毫米(英國),最大圓坯為φ 450毫米(美國),最寬板坯為2640×304毫米(美國)。在機型方面,立式和立彎式連鑄機比例逐漸下降,弧型連鑄機比例上升,水平連鑄機正在興起。80年代初連鑄發展主要側重於提高注速和作業率,改善鑄坯質量和擴大品種。
軋鋼 60年代以來,為適應大高爐、大氧氣轉爐的發展,軋鋼生產在大型化、高速化、連續化和自動化方面取得顯著進展(見金屬塑性加工)。初軋機軋輥直徑最大達1500毫米,年產能力達600萬噸,板坯初軋機最高年產量達700萬噸;帶鋼熱連軋機最大輥身長度為2500毫米,最高年產能力達 600萬噸;帶鋼冷連軋機最大輥身長度2500毫米,最高年產能力達250萬噸;最大的UOE成型焊管機可生產外徑1626毫米的管子。線材軋機最高軋制速度達 102米/秒;帶鋼冷連軋機的速度達41.7米/秒。在熱軋、冷軋帶鋼軋機和線材軋機上普遍實現了連軋,還發展了連續式型鋼軋機和連續式鋼管軋機;出現了“無頭軋制”的全連續式帶鋼冷軋機;連續酸洗、退火和精整作業線逐步推廣;連續鑄軋機組不斷增加。各種高剛度軋機相繼問世。自動化水平越來越高,許多軋鋼車間實現了某個工序或幾個工序的自動化。軋鋼能耗不斷下降,初軋機均熱爐熱能單耗降至 2.52萬大卡/噸鋼(日本神戶鋼鐵公司加古川廠);帶鋼熱連軋機加熱爐熱能單耗達到 9.41萬大卡/噸鋼(日本新日本鋼鐵公司室蘭廠)。成材率迅速提高,1981年日本綜合成材率為90%。80年代初,軋鋼生產技術的發展主要圍繞著節能、提高成材率和改善質量、擴大品種,為此,積極發展控制軋制和控制冷卻技術,改進軋機設備,開發節能新工藝。在新建軋機的同時,加速進行老軋機的改造。
重要原料──鐵礦石 70年代後期,全世界鐵礦石總儲量約為3500億噸,其中富礦儲量約為1500億噸(以上均不包括中國的儲量)。蘇聯鐵礦石儲量占世界總儲量的近三分之一,居世界首位,以下依次是巴西、玻利維亞、加拿大和澳大利亞。這五國鐵礦石儲量之和占世界總儲量的90%左右。蘇聯70年代各年的鐵礦石產量為1.95~2.46億噸,占同期世界年總產量的四分之一強,是最大的鐵礦石生產國。澳大利亞、巴西、美國、中國、加拿大的鐵礦石產量依次占第二至第六位。
鐵礦石資源豐富是發展鋼鐵工業的重要條件,而隨著重型列車、巨型礦石船和裝卸機的發展,許多國家,特別是靠海的國家,雖然缺乏鐵礦石資源,也可以獲得充足的優質鐵礦石。因此,既有全靠本國鐵礦發展鋼鐵生產的國家,如蘇聯、澳大利亞和瑞典等,又有基本上全靠進口或部分靠進口鐵礦石發展鋼鐵工業的國家,如日本和美國等。主要鋼鐵生產國大多不是主要的鐵礦石生產國,其鐵礦石自給率甚低,而且越來越低。輸出鐵礦石的國家和地區主要有澳大利亞、巴西、加拿大、蘇聯、瑞典、賴比瑞亞、印度和南非。礦石消費量與生鐵產量之比稱為礦鐵比(ore/iron ratio)。對於全世界的礦鐵比,可按鐵礦產量與生鐵產量來計算。
全世界平均的礦鐵比總的趨勢是下降的,50年代末高於2.00,60年代末降為1.80左右,70年代末又降至1.70左右。礦鐵比越低,表明進入高爐的廢石越少,渣量越少,燃料消耗量越低,煉鐵生產的綜合經濟效益越大。在富鐵礦所占比例逐漸減小的情況下,要降低礦鐵比,需要在選礦、燒結和球團等方面作大量的工作,並不斷提高煉鐵生產技術水平。70年代主要產鐵國中,日本的礦鐵比最低,僅為1.42~1.47;聯邦德國次之,為1.42~1.59;法國最高,達2.00~2.64。
國際貿易 早在1806年,英國生鐵總產量中就有20%銷售到國外。隨著鋼鐵工業和大型輪船的發展,鋼鐵國際貿易量迅速增加。1955年全世界鋼鐵出口量為2612萬噸,1973年增至1.07億噸,70年代後期保持在1.2億噸左右。70年代全世界年平均鋼鐵出口量,若折算成鋼,約為年平均鋼產量的四分之一,日本的為25.4~44.5%,聯邦德國35.5~59.5%,法國40.8~59.2%,比利時-盧森堡的最大,高達90%以上。鋼鐵出口額占總出口額的比重,最大的是日本,為12.1~19.4%。過去,英國、美國和聯邦德國的鋼鐵出口量先後居世界第一位。從60年代末期以來,日本一直是最大的鋼鐵出口國,其次是聯邦德國、比利時-盧森堡和法國。這五國70年代鋼鐵出口量之和占世界總量的60%以上,其中日本占世界總量的20.0~30.1%。
鋼鐵國際貿易中,鋼鐵出口量減進口量後的淨流向,一般是由已開發國家或次已開發國家流向次已開發國家或開發中國家;由生產成本低的國家流向生產成本高的國家,但有些生產成本高的國家;其政府為了獲得外匯和發展本國鋼鐵工業,而制訂補貼的政策鼓勵出口鋼鐵。曾是最大鋼鐵出口國的美國,70年代竟成了最大的鋼鐵進口國,每年平均淨進口鋼鐵1270萬噸,占全世界年平均總進口量的11.7%。
鋼消費量 一般以所消費鋼材折算成的鋼量──鋼消費當量(apparent steel consumption)表示。人均鋼消費當量在一定程度上反映了一個國家或地區的經濟發展程度和生活水平。世界各地區和各國的鋼消費水平差別很大。70年代全世界平均每人每年消費鋼156~184公斤,北美高達550~704公斤,蘇聯和東歐為438~576公斤,而非洲只有26~38公斤。日本、瑞典等工業已開發國家平均每人每年用鋼600~700公斤,日本1973年高達802公斤,而許多開發中國家僅幾十公斤,有的甚至只有1~2公斤。因此,雖然開發中國家人口占全世界人口的70%左右,但其總的鋼消費當量占全世界的比重較低,如1979年僅占20%左右。但是,近年來其總消費量的平均增長速度比已開發國家要快。一般地說,各國或地區當人均年國內生產總值在4000美元(按60年代中期平均匯率換算為1980年價格,下同)以下時,隨著人均年國內生產總值的增加,人均年鋼消費當量近似於直線地迅速增長;國民經濟進一步發展時,人均鋼消費當量的增長速度減慢;而當經濟發展到人均國內生產總值高於6000美元時,人均年鋼消費當量增長更少,有的國家甚至反而下降了(見圖)。
發展歷程
發展歷程總體上,中國鋼鐵工業可以大致劃分為三個階段:第一階段(1949~1978年)為“以鋼為綱”的發展階段,第二階段(1978~2000年)為穩步快速發展階段,第三階段(2001年至今)為加速發展階段。一以鋼為綱時期
1949年新中國成立時,中國鋼鐵工業的基礎十分薄弱,全國幾乎沒有一家完整的鋼鐵聯合企業。新中國成立後,鋼鐵工業開始逐步得到恢復和發展,在蘇聯援助下建設了鞍鋼、武鋼、包鋼等鋼鐵廠,鋼鐵工業逐步建設發展形成了“三大”、“五中”、“十八小”的格局。隨著“三線建設”的鋪開,在西南、西北建設了攀鋼、酒鋼、成都無縫管廠等一批新的鋼鐵企業,初步形成了新中國的鋼鐵工業布局。
考慮到鋼鐵工業在國民經濟中的重要地位,國家確立了“以鋼為綱”的工業發展指導方針,提出了“大躍進”、“全民大煉鋼鐵”、“超英趕美”等口號。因此,在這一階段中國鋼鐵工業就走上了一條以追求產值、產量增長速度為目標的粗放型的發展道路。經過全國上下的努力,在這一階段中國鋼鐵工業的產量和產值都有了較大幅度的增長。1978年,鋼鐵產量為3178萬噸,占世界鋼產量的4.5%,居世界第4位。據統計,1952~1978年期間,鋼鐵工業產量平均每年遞增12.9%,產值每年遞增11.8%,實現利稅每年遞增9.67%,
二穩步快速時期
在這一階段,中國鋼鐵工業發展遇到了兩次重要機遇。1978年,黨的十一屆三中全會後,中國實行改革開放政策,為利用國外的資金、技術和資源創造了條件。1992年,黨的十四大確立了建設社會主義市場經濟體制的改革方向,極大地激發了企業的活力。中國鋼鐵工業面對良好的發展機遇鋼鐵工業
,加快了鋼鐵工業現代化建設的步伐。在這一階段,除了建設上海寶鋼、天津無縫鋼管廠等具備世界先進水平的現代化大型鋼鐵企業外,又對一些老的大型鋼鐵企業進行了技術改造和升級,例如鞍鋼、武鋼、首鋼、包鋼等企業。1981年,中國與澳大利亞科伯斯公司通過簽訂補償貿易契約的方式,首次實現了改革開放以後利用外方資金和技術對鞍鋼焦化總廠瀝青焦車間進行改造。1987年,國家計委批准了鞍鋼、武鋼、梅山(1998年後被併入寶鋼集團)、本鋼、萊鋼5個企業利用外資的項目建議書。通過技術引進、消化和吸收,中國鋼鐵企業工藝裝備的現代化水平得到不斷提升。另外,一些非國有企業也進入到鋼鐵行業,例如,沙鋼、海鑫等,並且發展迅速。同時,1992年之前,中國鋼鐵企業進行了一系列的探索,從放權讓利到承包經營責任制,希望通過企業改革釋放強大的內在發展動力,實現了鋼產量5000萬噸和億噸兩次突破。1986年,中國鋼產量(粗鋼)超過了5000萬噸,達到5221萬噸。1996年中國鋼產量(粗鋼)首次超過1億噸,達到10124萬噸,占世界鋼產量的13.5%,超過日本和美國成為世界第一產鋼大國。2000年,中國鋼產量為12850萬噸。
三加速發展時期
十五”期間,中國鋼鐵工業更是實現了持續高速發展。粗鋼產量從2000年的1.3億噸,到2003年中國粗鋼產量超過2億噸,到2005年,粗鋼產量達到3.6億噸,成為全球第一個粗鋼產量突破3億噸的國家,再到2006年粗鋼產量達到4.2億噸,連續實現了鋼產量2億噸、3億噸和4億噸的三次跨越。2001~2007年期間,鋼產量年均增長率為21.04%,其中,2001、2003、2004和2005年這四年年增長率都是保持在20%以上,2005年鋼產量同上年相比增長率更是創紀錄的高達30.42%,同時,中國鋼鐵工業在整個工業中也占據著重要的地位。2006年,中國規模以上鋼鐵企業實現銷售收入25735億元,在39個工業行業中排名第2位,僅低於通信設備、計算機及其他電子設備製造業;實現利潤總額1367億元,在39個工業行業中排名第3位,僅低於石油和天然氣開採業,電力、熱力的生產和供應業。
取得成就
鋼鐵工業基於鋼鐵工業在國民經濟和國防建設中的特殊地位,中國從建國開始就一貫高度重視發展鋼鐵工業。在黨和國家三代領導核心的正確指引下,在全國人民的全力支持下,冶金戰線全體職工奮發圖強,克服重重困難,取得了舉世矚目的偉大成就。
產量高速增長
產量高速增長,成為世界第一,徹底告別了鋼材供不應求的時代。1949年中國鋼產量只有15.8萬噸,還不及現在半天的產量,居世界第26位。1979年改革開放後鋼產量持續快速增長,1996年首次超過1億噸大關,躍居世界第1位,數量上基本滿足了國民經濟的需要,扭轉了長達40年的被動局面。1999年達到1.22億噸,連續四年居世界各國之首,占世界鋼產量的比重從1949年的不到0.1%提高到15.8%,坐定了產鋼大國的地位。
技術裝備水平提高
冶金工業積極貫徹“利用國內外兩種資源和資金,開發國內外兩個市場”的方針,加大現代化建設的步伐,建設了上海寶鋼、天津鋼管等具有世界先進水平的現代化大型鋼鐵企業;同時,對鞍鋼、武鋼、首鋼、包鋼、攀鋼等老企業進行了技術改造。目前,中國冶金工業達到世界先進水平的裝備提高到30%左右。CSP世界上只有20餘套,而中國已在珠江鋼廠、邯鋼和包鋼擁有3套。中國鋼鐵企業技術水平雖然總體上落後於世界先進水平,但20世紀90年代以來,新建的大型燒結廠、大型高爐、煉鋼鐵水預處理和爐外精煉、連鑄、熱連軋、冷軋及塗鍍層生產線、冷軋矽鋼生產線、高速線材軋機、小型棒材連軋機等一大批企業的部分裝備基本上達到國際先進水平。
提高市場占有率
工藝技術結構、產品結構不斷最佳化,產品質量顯著提高,提高了市場占有率。1978年,全國鋼產量中落後的平爐煉鋼占35.5%,目前已降到1%以下。標誌著鋼鐵工業綜合技術水平的連鑄比由1978年的3.5%提高到現在的82%,已接近世界平均83%的水平(2000年10月開始當月連鑄比已超過84%),正朝著高效連鑄方向發展。建國之初,中國只能冶煉100多個鋼種和軋制400多個規格的鋼材,經過50年的發展與建設,目前已能冶煉包括高溫合金、精密合金在內的1000多個鋼種,軋制4萬多個品種規格的鋼材。板管帶比由1978年的32.3%提高到現在的42%左右。國內長期短缺的薄鋼板產量由1978年的133萬噸增加到2000年的405萬噸,自給率達到90%以上,其中石油鋼管的國內市場占有率達到70%至80%。
冶金工業技術進步
鋼鐵工業
冶金科技和教育全面發展,極大地促進了冶金工業的技術進步。中國有冶金科研機構79個,工程技術和科研人員32.5萬人。同時建立了包括高等教育、職業教育和成人教育在內的冶金人才培養體系。目前中國有冶金普通高校13所,其中本科院校8所,每年為冶金行業培養本科生、碩士生、博士生1.5萬人。中國還自己培養了許多國內外知名的冶金科技專家、兩院院士。改革開放20多年來,全行業獲科技成果1萬多項。截止1998年底,申請專利7813項,授權專利5984項。
行業經濟效益提高
創造出在全國有影響的先進管理經驗,促進了行業經濟效益的提高。20世紀80年代首鋼的內部承包制,使該企業成為當時工業企業改革的排頭兵。寶鋼創造了“科學、精幹、高效”的現代化管理體系。90年代初,武鋼走“質量效益之路”;邯鋼又創造了“模擬市場核算,實行成本否決”的先進管理經驗。近年來,又有了濟鋼“系統節能降耗”,唐鋼“對標挖潛”和水鋼、宣鋼“扭虧脫困”等一批先進典型。技術進步和管理創新,促進了經濟效益的不斷提高。生產成本降低率每年都達到3%左右,1999年達到6%,有利地消化了因鋼材不斷降價造成的損失,使中國鋼材價格與國際市場趨於同步,提高了將來進入WTO的競爭力。
1978年冶金行業實現利稅50億元,1998年達到197億元,1999年達到242億元,2000年1月至11月已經實現357億元,預計全年400億元,創造了兩年利稅翻番的佳績。從建國到2000年,冶金行業累計實現利稅5260億元,為國家創造了巨大的物質財富。[1]
相關規劃
“十二五”規劃[2]工信部網站11月7日正式公布《鋼鐵工業“十二五”發展規劃》。規劃提出,“十二五”末,鋼鐵工業結構調整取得明顯進展,基本形成比較合理的生產力布局,資源保障程度顯著提高,部分企業具備較強的國際市場競爭力和影響力,初步實現鋼鐵工業由大到強的轉變。
規劃還提出,強化技術創新與技術改造、淘汰落後產能、最佳化產業布局、增強資源保障能力、加快兼併重組。結合兼併重組和淘汰落後,在不增加生產能力的前提下,有保有壓,最佳化產業布局;通過兼併重組大幅度減少鋼鐵企業數量,國內排名前10位的鋼鐵企業集團鋼產量占全國總量的比例由48.6%提高到60%左右,力爭是當地居民利得財富。
產能控制有保有壓
產業布局方面,規劃提出,產能過剩地區的盲目擴張得到抑制,建成湛江、防城港鋼鐵精品基地,從根本上解決“北鋼南運”問題。結合兼併重組和淘汰落後,在不增加生產能力的前提下,圍繞提高產品質量和降低物流成本,統籌考慮市場需求、交通運輸、環境容量和鐵礦、煤炭、供水、電力等資源能源保障條件,有保有壓,最佳化產業布局。
環渤海、長三角地區原則上不再布局新建鋼鐵基地。河北、山東、江蘇、遼寧、山西等鋼鐵規模較大的地區通過兼併重組、淘汰落後,減量調整區域內產業布局。湖南、湖北、河南、安徽、江西等中部地區省份不增加鋼鐵產能總量。西部地區部分市場相對獨立區域,立足資源優勢,承接產業轉移,結合區域差別化政策,適度發展鋼鐵工業。東南沿海鋼鐵基地建設則繼續推進,“十二五”期間,加快建設湛江、防城港沿海鋼鐵精品基地,推進福建寧德鋼鐵基地建設。
與城市發展不協調的鋼廠需要轉型或搬遷。對於經濟支撐作用下降和資源環境矛盾突出的鋼鐵企業,實施轉型或搬遷改造。綜合實力弱、技術水平低的企業應實行轉型,發展鋼鐵服務業或其他產業。有實力、有技術、有特色的城市鋼廠,結合人員安置等因素有序實施環保搬遷,嚴禁借搬遷之名擴大鋼鐵生產能力。
產業集中度提高
鋼鐵工業“十二五”期間產業集中度將進一步提高。規劃提出,大幅度減少鋼鐵企業數量,國內排名前10位的鋼鐵企業集團鋼產量占全國總量的比例由48.6%提高到60%左右。加快鋼鐵企業兼併重組步伐,鼓勵社會資本參與國有鋼企兼併重組,重點支持優勢大型鋼鐵企業開展跨地區、跨所有制兼併重組,加強鋼鐵企業信託網建設。
寶鋼、鞍鋼、武鋼、首鋼等大型鋼鐵企業集團將發揮帶動作用,形成3~5家具有核心競爭力和較強國際影響力的企業集團。鞍鋼與攀鋼、本鋼、三鋼等企業,寶鋼與廣東鋼鐵企業,武鋼與雲南、廣西鋼鐵企業,首鋼與吉林、貴州、山西等地鋼鐵企業兼併重組將得到重點推進完善。區域兼併重組方面,將形成6~7家具有較強市場競爭力的企業集團。
為提高鐵礦石資源保障能力,規劃鼓勵鋼鐵企業建立與資源所在國利益共享的對外資源開發機制,實施投資區域多元化,在具有資源優勢國家和地區以及周邊國家,有序建立穩定、可靠的鐵礦石、鉻礦、錳礦、焦煤等原燃料供應基地和運輸保障體系;還將重點建設一批廢鋼加工示範基地,研究制定進口廢鋼的優惠政策措施,在海外建立廢鋼回收加工配送基地。
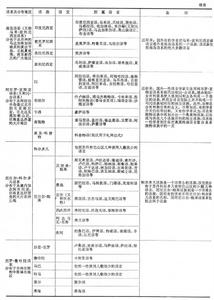
肯尼斯·沃倫著,童慎耀譯:《世界鋼鐵》,1975年第1版,遼寧人民出版社,瀋陽,1979。
(日本)鉄鋼佮計委員會:《鉄鋼佮計要覧》,1965~1982年版,東京。
冶金部情報研究總所:《國內外鋼鐵統計1949~1978年》,冶金工業出版社,北京,1981。
中國金屬學會:《美國冶金工業概況》綜合部分,冶金工業出版社,北京,1978。