金屬力學性能的表征
正文
表征金屬在力的作用下的行為的衡量指標,都屬於金屬力學性能所研究的範疇。諸如不同載荷所造成的可逆變形(彈性)、不可逆變形(塑性)、斷裂(脆性斷裂、韌性斷裂、疲勞斷裂等)以及金屬抵抗形變和斷裂能力的衡量指標,如強度、塑性、韌度(脆性)、硬度等(見金屬力學性能測試技術)。金屬的力學性能是零件或結構件設計的依據,也是選擇、評價材料和制訂工藝規程的重要參量;在金屬研究上,它們是合金成分設計、顯微組織結構控制所要達到的目標之一,也是反映金屬內部組織結構變化的重要表征參量。
金屬力學性能隨受載方式、應力狀態、溫度及接觸介質的不同而異。受載方式可以是靜載荷、衝擊載荷、循環載荷等。應力狀態可以是拉、壓、剪、彎、扭及它們的複合,以及集中應力和多軸應力等。溫度可以是室溫、低溫與高溫。接觸介質可以是空氣、其他氣體、水、鹽水或腐蝕介質。在不同使用條件下,材料具有不同的力學行為和失效現象,因而必須有相應的力學性能指標表征。下面便是描述金屬材料力學性能的表征參量,對其中已設專條的,在本條中就從略了。
強度 金屬抵抗永久變形和斷裂的能力的總稱。以光滑拉伸試樣為例,在漸增載荷作用下,材料的典型拉伸應力-應變曲線如圖1所示。反映金屬材料強度的性能指標有如下幾項。

彈性極限(σE) 見彈性和滯彈性。
屈服強度(σs) 當應力超過彈性極限後繼續載入,有的金屬便會發生“物理屈服”現象,即在應力不增大的情況下,塑性應變不斷增長到一定值(圖1a曲線上的s點)以後應力-應變才同時以非常數比例繼續增長。這個保持基本恆定的應力(屈服平台應力)稱為屈服點σs,有時也通稱為屈服強度。對於無明顯物理屈服現象的金屬,則以產生限量的小量塑性應變時的應力作為條件屈服強度。如經常採用的條件屈服強度σ0.3 即為產生0.2%殘餘應變時的應力(圖1b)。它和上述規定比例極限σp以及彈性極限σE只是塑性變形量上不同而已,並無本質的差別,均是金屬對微量或小量塑性變形抗力的表征。因此,有一種根據不同的需要,選用不同的塑性應變數來表征微量塑性變形階段材料強度的趨勢,如σ0.001、σ0.01、σ0.1和σ0.3 等。屈服強度是設計承受靜載機件或構件的主要依據。
抗拉強度(σb) 超過屈服強度以後應力繼續增加時應變也不斷增長。當應力達到最高點時,對於韌性金屬而言,會在拉伸試樣上發生局部“縮頸”,而使橫截面積減小,因而承載能力開始下降。我們把最高名義應力σ稱為抗拉強度(σb)。對於脆性材料,例如灰口鑄鐵,當應力達到最高點時,試棒即斷裂,此最高應力也稱抗拉強度。可見抗拉強度對於韌性金屬是表征其極限均勻塑性變形的抗力,即塑性失穩的起始應力。對於脆性金屬,抗拉強度則表征其斷裂抗力。不論對韌性金屬還是脆性金屬,由於與σb所對應的載荷是金屬在單向靜拉伸時試樣(或工件)所能承受的最大載荷,因此習慣上也把σb稱為強度極限(UTS)。抗拉強度常作為評定金屬的依據,對於脆性金屬也是設計的依據。
斷裂強度sK(或σn) 通常,金屬的實際斷裂強度sK(或σn)是由試樣斷裂時的載荷除以試樣斷裂處實際橫截面積而求得的。只有根據試樣的實際斷裂情況才能確定它的意義。對於在彈性階段脆斷的金屬,sK相當於σb,也相當於σs;對於均勻塑變後即斷裂的金屬,則sK相當於真實抗拉強度sB;對於頸縮後斷裂的金屬,則sK實際上主要反映金屬對剪下斷裂抗力的大小。sK的數值要受試驗機系統剛性的影響,同一金屬,在不同試驗機上試驗,可得到不同的sK值。
塑性 金屬的塑性又稱范性, 為其在斷裂前可以承受的塑性變形的總量。常用的塑性指標是光滑試樣拉伸試驗所得到的伸長率,即拉斷後試棒伸長的百分數 δ =

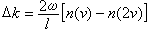
超塑性 一般工業用金屬的室溫塑性大都在百分之幾到百分之幾十的範圍。而某些金屬在特定的組織狀態下(主要是超細晶粒)、特定的溫度範圍內和一定的變形速度下表現出極高的塑性,伸長率可達百分之幾百甚至百分之幾千,這種現象稱為“超塑性”。它顯然有利於塑性加工。超塑性首先在Al-Zn合金中發現,套用也較廣泛。近年來在鐵基、鐵鎳基合金以及鈦合金等方面也開展了大量研究,在工業中已得到套用。
真應力-真應變曲線和形變強化 大多數金屬(尤其是韌性金屬),當外加應力達到屈服極限後,欲使變形繼續,必須繼續增加外力,即金屬的塑性變形抗力隨塑性變形量的增加而增加,如圖1所示。這種現象稱為形變強化或加工硬化。金屬的形變強化從屈服極限開始直至斷裂為止的過程中都存在,但是在圖1所示的條件應力-應變曲線上,並不能真實反映金屬的形變強化,這是由於在這種曲線上,各點應力均是以該點的載荷除以試樣的原始截面積來表示的,未考慮截面收縮;因此,塑性變形量越大,條件應力和試樣上所承受的真實應力的偏差也越大;“縮頸”後,由於局部區域截面積的急劇減少,這種偏差更大,出現應力超過σb後,強度隨應變的增加而降低的情況。真實力-真應變曲線能全面描述金屬從彈性變形開始直至斷裂的全過程的應力-應變關係,如圖2所示。其中真應力s是由曲線上各點的瞬時載荷除以試樣相應截面積求得,真應變ε是由瞬時試樣伸長的微分值dι與瞬時試樣長度ι之比的積分求得,即



金屬的韌性隨載入速度的提高、溫度的降低、應力集中程度的加劇而下降。衝擊韌性試驗,就是綜合套用較高衝擊速度和缺口試棒的應力集中,來測定金屬從變形到斷裂所消耗的衝擊能量的大小,即韌性的高低。
中國常用的衝擊韌性試驗是用一個 U型缺口方試棒, 將其置於支座上, 然後用擺錘落下將其一次沖斷。用沖斷試棒所消耗的衝擊功除以試棒缺口根部截面積所得商值(單位為kgf·m/cm2),定義為衝擊韌度(aK)。有些國家則常用帶V型缺口的試棒,直接以沖斷試棒所消耗的衝擊功作為夏氏衝擊韌度(CVN值),而不將此衝擊功除以試棒缺口截面積。不論aK或 CVN都是在特定條件下測得的衝擊值。應該注意的是,衝擊韌性試驗和某些承受反覆衝擊載荷的零件服役條件不同,對於這些零件,它們的服役性能套用小能量多次衝擊(或衝擊疲勞)試驗來衡量。
一次衝擊試驗也常用於評定材料的冷脆傾向。即將金屬在一系列不同的試驗溫度下進行一次衝擊試驗 (即所謂”系列衝擊試驗”),而後確定反映材料冷脆傾向的冷脆轉化溫度。對於aK試驗一般採用能量法即
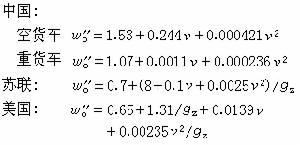