連軋機控制系統
正文
由連軋機組、檢測儀表控制裝置和電子計算機組成的對鋼鋁等材料的加工尺寸進行控制的塑性加工過程控制系統。早期的連軋機因軋制速度低,對產品質量要求也不高,用人工控制尚能生產。人們對產品質量和產量的要求日益提高,如軋制每卷重45噸的冷連軋薄帶鋼卷,要求厚度公差為±(5~50)微米,冷連軋機最高軋速達40米/秒以上,熱連軋年產量達 500萬噸以上,冷連軋年產達 100萬噸以上。這樣的任務再用人工控制已不可能完成。20世紀60年代後期,連軋機開始採用計算機控制,70年代以來發展較快。例如中國武漢鋼鐵公司70年代末投產的1700毫米帶鋼熱連軋機,500米長的軋制生產線全部採用計算機控制。控制功能主要包括軋件跟蹤、計算機操作指導和對軋制過程各種參數設定、連續檢測、控制和最優管理。下圖為五機架冷連軋機利用17台計算機組成集散控制系統,在主控制台的控制下,分為過程監控、操作監控和設備監控三級,包括各種自動檢測儀表、電子裝置、液壓裝置等組成的局部控制系統。按功能來分,整套軋機控制系統分為速度調節系統、壓下位置控制系統、軋制力調節系統、張力調節系統、厚度調節系統,以及自動制動系統、彎輥數字控制系統、板型控制系統、側導板自動控制系統、自動換輥系統、進出料自動控制系統等。從上卷、穿帶、軋制參數設定直到軋制厚度控制和數據記錄列印等已全部實現自動化。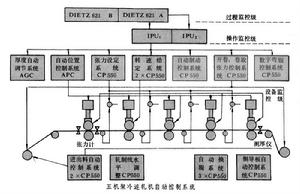
壓下位置控制系統 用以快速準確地調節軋機輥縫的開口度。現代大型軋機的軋輥機構重達幾十噸,為了適應高速軋制的快速回響需要,一般採用液壓伺服調節系統。它由微型計算機或電子調節線路、電液伺服閥、能產生上千噸壓力的大型液壓缸、精密位移感測器等組成,其位置調節解析度機達1~2微米,回響頻寬一般為8~12赫。
軋制力調節系統 主要用以補償軋輥偏心所造成的軋制力波動。由測壓頭或油壓測量感測器測出軋制力值,再將其變換為電信號,輸入微型機或電子調節線路去調節液壓壓下位置,使壓下系統能跟隨軋輥的偏心運動而實現軋制力的補償調節,減少由於軋制力波動所造成的周期性厚度偏差。軋制力調節系統的設定值一般由張力或厚度調節系統給定。
張力調節系統 用於調節各軋機間帶鋼的張力並使其保持穩定。冷軋機處於大張力軋制狀態時,各架軋機間的帶鋼張力可達10噸以上。過大的張力波動會造成斷帶或疊軋等事故。一般用張力輥直接檢測機架間的帶鋼張力,由電子計算機通過調節後一機架的液壓壓下位置來達到調節張力的目的。如果機架間張力低於工藝控制數學模型所選定的最佳張力給定值,則可以增大後一架軋機的輥縫開口度,使軋出帶鋼的體積流量增大,由此產生的帶鋼彈性張力積分效應便使機架間帶鋼張力隨之升高,達到給定值。如果軋機控制系統中具有軋制力調節系統,則張力調節系統的調節量就被輸出作為軋制力調節系統的給定值,同樣也能達到調節和穩定張力的目的。開卷機和卷取機產生的帶鋼張力,通過調節其傳動電機張力電流的方法來加以調節。在張力設定值不變的情況下,鋼卷直徑隨著軋制進程不斷發生變化。因此,由計算機組成的張力調節系統也要不斷計算,得出新的張力電流給定值,以保持開卷機和卷取機的張力穩定。
厚度調節系統 用以保證連軋機軋出的帶鋼在整個長度範圍內均勻一致或達到預定的厚度範圍。調節系統一般分為入口段厚度和出口段厚度調節兩個部分。
①軋機入口段的厚度調節系統 帶鋼坯料剛開始軋入軋機時,材料加工硬化尚不顯著,容易產生塑性變形,因此由坯料帶入的大部分厚度不均勻偏差都儘量在入口段厚度調節系統中加以消除。通常在軋機入口處裝設γ射線測厚計,測量進入軋機的帶鋼厚度,並將測得的厚度偏差信號送至計算機。計算機根據模型計算所得出的帶鋼塑性係數,可以算出第一架軋機液壓壓下位置的前饋調節量。如果計算機計算模型準確,則部分來料厚度偏差可以通過前饋調節補償克服。剩餘厚度偏差由裝在第一架和第二架軋機間的γ射線測厚計測出,並通過信號反饋調節來進一步消除。這一帶鋼厚度偏差信號同時也可用於實現第二架軋機的前饋厚度調節。
②軋機出口段的厚度調節系統 經過入口段調節以後,帶鋼厚度偏差已經大部分被克服。為了進一步提高軋出帶鋼的質量,使厚度公差保持在±(5~10)微米以內,最後在第4、第5架軋機上再設定厚度精調系統。帶鋼經過前幾架軋機軋制,加工硬化效應使帶鋼塑性係數增大,帶鋼變得很硬,很難依靠調節軋機的壓下位置來精調厚度,所以一般套用軋機出口處的γ射線測厚計所測得的厚度偏差作為反饋信號來調節第4、第5架軋機的張力。把改變張力作為主要的調節手段,而把改變軋制力作為輔助的調節手段。
展望 用戶不僅對帶鋼長度方向的尺寸要求嚴格,對橫向尺寸公差的要求也日益提高,因此帶鋼橫截面板形的測量和控制系統也開始套用。它通過測量帶鋼橫向分段張力的方法來計算板形,並對液壓彎輥裝置反饋控制以調節板形。另外,壓下負荷分配的合理選擇,對改進板形也有一定的成效。70年代以來,又出現了全連續式的冷連軋機,在入口側加了焊接鋼卷的焊機和存儲鋼帶的活套車。由電子計算機控制整個軋制過程,可自動改變軋制規格和軋機的設定值。軋後由飛剪下斷、分卷,軋制每卷鋼帶時無需穿帶和甩尾,能節省換卷間隙時間,消除鋼卷頭尾厚度超出公差的廢品,提高帶材軋制精度和收得率。80年代的連軋機自動控制系統趨於採用多級計算機控制,把軋鋼自動控制系統與工廠或公司的自動控制系統相聯,構成一個大系統,套用大系統理論和系統工程的方法和技術,實現整個工廠或公司的最優控制和管理。
參考書目
G.F.Bryant,Automation of tandem Mills, The Iron &Steel Institute,London,1973.
孫一康:《熱軋帶鋼計算機控制數學模型》,冶金工業出版社,北京,1980。