概念
深沖是指金屬板材在壓力機的模具上被衝壓成深度大的零件的金屬塑性加工方法。沖裁件的板材厚度在10mm以下,成形件厚度在20mm以下。通常在室溫下進行冷衝壓。變形抗力大、塑性差、板厚,可採用熱衝壓。適用於製造發動機燃燒室、噴管等板材件,生產效率高,容易實現機械化、自動化批量生產的成本低。衝壓成型中,應避免金屬板材產生缺陷。不產生缺陷所能達到的成型極限叫做衝壓成型性。
特點
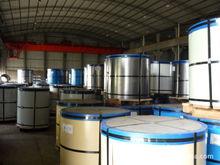
蘇聯發明了用拋物線形沖頭的深沖試驗法。這些試驗方法的優點是,通過試驗,能比一般杯突試驗更清楚地揭示出材料本身決定的杯突值。試樣為圓形坯板,其直徑隨鋼板厚度增加而增大。就是在這種試驗中,潤滑條件和冷軋帶鋼的表面質量也對杯突值具有決定性影響,因此不可能縮小試驗結果的分散度範圍。
與艾氏杯突試驗相反,深沖杯突試驗迄今尚未定出標準。這種方法的缺點在於時問長和材料消耗大。其原因是必須使用各種大直徑的圓形坯板來摸索出極限拉延係數。受材料限定的不同極限拉延係數,分別與上述影響因素的波動值相吻合。第一個缺點對於艾氏杯突試驗是不存在的。而第二個缺點是這兩種試驗方法的共同點。因此,各種拉延試驗方法的優點,是能夠很好地獲得帶鋼的各向異性。
方法分類
AEG杯突試驗法
現代評定帶鋼質量的深沖性能的常用深沖試驗方法的杯突試樣概念,來源於過去的AEG公司交貨規程。在一台標準衝壓機上,用直徑為50毫米的沖頭(沖頭和沖模的圓角半徑各為7毫米)將板厚為0.2~3.5毫米的帶鋼試樣深沖成突杯。沖模直徑隨帶鋼試樣的厚度不同而變化,因此需要約20種沖模直徑。各種直徑D的圓形試樣,均在上述條件下衝壓成突杯。根據能深沖的最大圓形坯料直徑和50毫米的沖頭直徑可算出極限拉延係數,此值便是這種方法衡量成形性能的尺度。這種試驗方法的缺點,在深沖試驗法的概述部分已經作了敘述。
R.D.Butler、B.B.Moreton和D.V.Wilson研究了深沖速度、沖頭半徑與沖頭直徑的比值對極限拉延係數的影響。他們發現:隨著沖頭半徑與沖頭直徑比值的增大和深沖速度的提高,極限拉延係數則明顯下降。
H.W.Swift試驗法
如同AEG一樣,H.W.Swift也提出了用液壓機沖制突杯。他確定沖頭直徑為50.8毫米(2英寸),沖頭的圓角半徑為3.2毫米(1/8英寸)。衝壓機可以施加1176公斤/厘米 (2500磅/平方英寸)的壓力,沖頭速度可達914毫米/分(36英寸/分)。H.W.Swift確定以229毫米/分(9英寸/分)的沖頭速度為標準值。最近曾對試驗條件進行了檢驗並作了修改。與AEG深沖試驗法一樣,需要大量的沖模以適應不同的鋼板厚度。既用恆定的夾緊壓力,也用變化的夾緊壓力進行試驗。H.W.Swift以極限深沖係數作為評定成型性的最佳依據,而他測定的極限深沖係數的精度為1%。
根據含鋁99%的鋁板的試驗結果,他就深沖試驗得出以下結論:
1)用扁平沖頭對處於加工硬化狀態下的材料進行試驗獲得的極限深沖係數,比用半球形沖頭進行試驗所得的極限深沖係數高。原始硬度對極限深沖係數的影響很小。
2)對於未冷加工硬化的或時效硬化的材料,用半球形沖頭試驗所得的極限深沖係數,比用扁平沖頭試驗所得的極限深沖係數高。原始硬度十分重要。
3)除了特殊情況外(例如採用扁平沖頭而又不用潤滑劑),成型性隨硬度減小而提高。這些經驗數值既適用於扁平沖頭,也適用於半球形沖頭。
4)用半球形沖頭試驗時,獲得的結果相互差距較大,而且易於區分。
深沖試驗與生產結果比較
如果在兩種情況下獲得同樣的極限深沖係數,則突杯壁上的縱向應力必須與大型模具中的一樣大。但是,在深沖試驗與大型模具之間,不容易實現完全相似的模擬。雖然可以按比例縮小模具的尺寸,但是在深沖試驗時選用的板厚,往往必須與大模具試驗時使用的板厚相同。這樣就不能實現相似的模擬。而且摩擦係數也隨著模具尺寸和模具與板厚的幾何形狀比例的變化而變化。所以,其他作者首先研究了沖頭直徑對極限深沖係數的影響。在深沖試驗中,對模擬相似性的總偏差很難進行校正,大多數只能有限地得到校正。如果能夠進行模擬試驗的極限深沖係數的換算,則帶鋼試樣的尺寸、楱具尺寸、帶鋼和模具的表面狀態、模擬試驗與大型模具的潤滑條件及夾緊壓力等,相互之間必然存在著一定的關係。