科技名詞定義
中文名稱:柔性製造系統英文名稱:flexiblemanufacturingsystem;FMS
定義:在成組技術的基礎上,以多台(種)數控工具機或數組柔性製造單元為核心,通過自動化物流系統將其聯接,統一由主控計算機和相關軟體進行控制和管理,組成多品種變批量和混流方式生產的自動化製造系統。
所屬學科:機械工程(一級學科);切削加工工藝與設備(二級學科);自動化製造系統(三級學科)
本內容由全國科學技術名詞審定委員會審定公布
名詞解釋
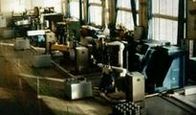
簡稱FMS,是一組數控工具機和其他自動化的工藝設備,由計算機信息控制系統和物料自動儲運系統有機結合的整體。柔性製造系統由加工、物流、信息流三個子系統組成。柔性製造系統是由統一的信息控制系統、物料儲運系統和一組數字控制加工設備組成,能適應加工對象變換的自動化機械製造系統(Flexible Manufacturing System),英文縮寫為FMS。
FMS的工藝基礎是成組技術,它按照成組的加工對象確定工藝過程,選擇相適應的數控加工設備和工件、工具等物料的儲運系統,並由計算機進行控制,故能自動調整並實現一定範圍內多種工件的成批高效生產(即具有“柔性”),並能及時地改變產品以滿足市場需求。
FMS兼有加工製造和部分生產管理兩種功能,因此能綜合地提高生產效益。FMS的工藝範圍正在不斷擴大,可以包括毛坯製造、機械加工、裝配和質量檢驗等。80年代中期投入使用的FMS,大都用於切削加工,也有用於衝壓和焊接的。 採用FMS的主要技術經濟效果是:能按裝配作業配套需要,及時安排所需零件的加工,實現及時生產,從而減少毛坯和在制品的庫存量,及相應的流動資金占用量,縮短生產周期;提高設備的利用率,減少設備數量和廠房面積;減少直接勞動力,在少人看管條件下可實現晝夜24小時的連續“無人化生產”;提高產品質量的一致性。
沒有固定加工順序和生產節拍,適應多品種小批量生產的機械製造系統。英文縮寫FMS。FMS的工藝基礎是成組技術,它按照成組的加工對象確定工藝過程,選擇相適應的數控工具機或工件、工具等物料儲運系統。柔性製造系統以計算機為核心進行系統管理,用無人搬運車進行工件傳送,用數控技術實現自動化加工,用機器人進行自動裝卸,並具有監視切削狀態和精度、診斷和復原等功能,還能在一定範圍內完成一種零件加工到另一種零件加工的自動轉換。
發展概況
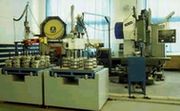
20世紀50年代,為了提高生產率,適用於大批量生產的組合工具機和剛性自動線等專用設備得到很大發展。60年代,隨著小批量高精度加工產品的不斷增加,數控工具機和加工中心進入了鼎盛時期。從70年代起,中小批量多品種的生產成為製造工業的生產特徵。隨著科學技術的發展和產品更新換代速度的加快,中小批量產品的比例還有進一步增大的趨勢。這種情況迫使人們研製以適應中小批量多品種生產為主要目標的柔性製造系統。1963年美國研製成加工多種柴油機零件的數控自動線。1967年英國莫林公司首次提出完整的柔性製造系統的概念,並介紹了Molin-24系統的構想。隨後蘇聯、日本、聯邦德國都相繼研究出這類系統,如蘇聯於1983年公布了加工軸類零件的柔性製造系統ГАСС和“設計製造綜合自動化”系統КАΠΡИ。
1967年,英國莫林斯公司首次根據威廉森提出的FMS基本概念,研製了“系統24”。其主要設備是六台模組化結構的多工序數控工具機,目標是在無人看管條件下,實現晝夜24小時連續加工,但最終由於經濟和技術上的困難而未全部建成。
同年,美國的懷特·森斯特蘭公司建成 Omniline I系統,它由八台加工中心和兩台多軸鑽床組成,工件被裝在托盤上的夾具中,按固定順序以一定節拍在各工具機間傳送和進行加工。這種柔性自動化設備適於少品種、大批量生產中使用,在形式上與傳統的自動生產線相似,所以也叫柔性自動線。日本、前蘇聯、德國等也都在60年代末至70年代初,先後開展了FMS的研製工作。
1976年,日本發那科公司展出了由加工中心和工業機器人組成的柔性製造單元(簡稱FMC),為發展FMS提供了重要的設備形式。柔性製造單元(FMC)一般由1~2台數控工具機與物料傳送裝置組成,有獨立的工件儲存站和單元控制系統,能在工具機上自動裝卸工件,甚至自動檢測工件,可實現有限工序的連續生產,適於多品種小批量生產套用。
70年代末期,FMS在技術上和數量上都有較大發展,80年代初期已進入實用階段,其中以由3~5台設備組成的FMS為最多,但也有規模更龐大的系統投入使用。
1982年,日本發那科公司建成自動化電機加工車間,由60個柔性製造單元(包括50個工業機器人)和一個立體倉庫組成,另有兩台自動引導台車傳送毛坯和工件,此外還有一個無人化電機裝配車間,它們都能連續24小時運轉。
這種自動化和無人化車間,是向實現計算機集成的自動化工廠邁出的重要一步。與此同時,還出現了若干僅具有FMS基本特徵,但自動化程度不很完善的經濟型FMS,使FMS的設計思想和技術成就得到普及套用。
組成部分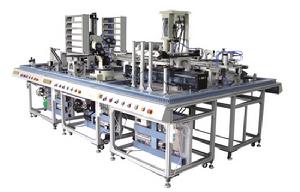
系統的組成:(1)中央管理和控制計算機 (2)物流控制裝置 (3)自動化倉庫 (4)無人輸送台 (5)製造單元 (6)中央刀具庫(7)夾具站 (8)信息傳輸網路 (9)隨行工作檯
系統的功能:1)以成組技術為核心的對零件分析編組的功能。2)以微型計算機為核心的編排作業計畫的智慧型功能。3)以加工中心為核心,自動換刀、換工件的加工功能。4)以托盤和運輸系統為核心的工件存放與運輸功能。5)以各種自動檢測裝置為核心的自動測量、定位與保護功能
多工位數控加工系統 傳統的數控系統的功能基本上靠固定的邏輯線路來實現,如需要擴充或改變功能則必須更改硬體邏輯,靈活性較差。柔性製造系統採用計算機控制的加工中心,這種數控裝置適應性強,能在硬體基本不變的情況下,通過修改軟體來改變或擴充其功能。加工中心一般都具有換刀裝置,工件一次裝夾後能連續地完成鑽、鏜、銑、鉸、鍃等多種工序加工。如果用多台加工中心組成柔性製造系統,便可以任意順序自動完成多種工件的多工位加工。
自動化物料流輸送系統 它包括存儲、輸送和搬運三個子系統,其功能為:自動地以任意順序存取工件和刀具;自動地按可變的自由節拍完成柔性製造系統中各個生產裝置的連線;自動地實現輸送裝置和加工設備之間的連線。柔性製造系統中的工件輸送系統與其他製造系統中的工件輸送系統有很大區別,它不是按固定節拍將工件從某一工位輸送到下一工位,而是既不按固定節拍又不按固定順序輸送工件,甚至有時是將幾種工件混雜在一起輸送。在這種系統中一般都設定儲料庫,以調節各個工位上所需加工時間的差異。工件輸送系統有直線輸送、環形輸送和閉環輸送三種基本類型。①直線輸送:輸送裝置沿工具機一邊布置,或從兩排工具機中間通過。輸送工具可以是各種類型的傳送帶和運送小車,主要用於順序傳送。這種輸送裝置本身的存儲容量很小,常需設定中間儲料庫。②環形輸送:工具機布置在環形輸送線的外側。輸送工具除有各種類型的滾子傳送帶和運送小車外,還有架空單軌懸吊式輸送器。在封閉環形輸送線中常設定若干支路,作為儲存工件和改變輸送線路之用,便於實現隨機傳送,具有較大的靈活性。③閉環輸送:整個傳送帶由許多隨行夾具和托板組成,藉助托板上的編碼器能自動識別地址,從而可以任意編排工件的傳送順序。除這三種基本方式外,還有工業機器人,它主要用於中等尺寸的零件輸送和搬運。
計算機信息流控制系統 信息流控制系統的主要設備為計算機,與直接數控系統相似,通常具有A、B兩級或A、B、C三級計算機分級控制的結構形式。在A級中安排有大型通用計算機,並包含有零件自動編程系統,其主要職能是:將套用某種程式語言編寫的零件源程式處理成加工目的程式;完成管理控制,如分析原材料價格、記錄生產歷史資料、編制管理報告、綜合市場信息、核算經濟指標等。在B級中安排有中小型通用計算機,其主要職能是:將來自A級計算機的數據分發到各台數控或計算機數控裝置和輸送裝置上去,並協調其工作,同時還對每台工具機進行生產狀態分析和判斷,並根據情況發出修改控制參數的指令。在 C級中安排有小型計算機、微型機或專用數控裝置,其主要職能是:執行來自上一級計算機的命令,直接控制工具機加工,收集並處理檢測數據,向上級計算機反映各台工具機的生產狀態。
工藝說明
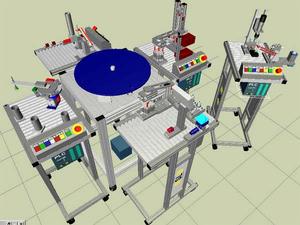
典型的柔性製造系統由數字控制加工設備、物料儲運系統和信息控制系統組成。加工設備主要採用加工中心和數控車床,前者用於加工箱體類和板類零件,後者則用於加工軸類和盤類零件。中、大批量少品種生產中所用的FMS,常採用可更換主軸箱的加工中心,以獲得更高的生產效率。 儲存和搬運系統搬運的的物料有毛坯、工件、刀具、夾具、檢具和切屑等;儲存物料的方法有平面布置的托盤庫,也有儲存量較大的桁道式立體倉庫。
毛坯一般先由工人裝入托盤上的夾具中,並儲存在自動倉庫中的特定區域內,然後由自動搬運系統根據物料管理計算機的指令送到指定的工位。固定軌道式台車和傳送滾道適用於按工藝順序排列設備的FMS,自動引導台車搬送物料的順序則與設備排列位置無關,具有較大靈活性。
工業機器人可在有限的範圍內為1~4台工具機輸送和裝卸工件,對於較大的工件常利用托盤自動交換裝置(簡稱APC)來傳送,也可採用在軌道上行走的機器人,同時完成工件的傳送和裝卸。 磨損了的刀具可以逐個從刀庫中取出更換,也可由備用的子刀庫取代裝滿待換刀具的刀庫。車床卡盤的卡爪、特種夾具和專用加工中心的主軸箱也可以自動更換。切屑運送和處理系統是保證 FMS連續正常工作的必要條件,一般根據切屑的形狀、排除量和處理要求來選擇經濟的結構方案。
FMS信息控制系統的結構組成形式很多,但一般多採用群控方式的遞階系統。第一級為各個工藝設備的計算機數控裝置(CNC),實現各的口工過程的控制;第二級為群控計算機,負責把來自第三級計算機的生產計畫和數控指令等信息,分配給第一級中有關設備的數控裝置,同時把它們的運轉狀況信息上報給上級計算機;第三級是FMS的主計算機(控制計算機),其功能是制訂生產作業計畫,實施FMS運行狀態的管理,及各種數據的管理;第四級是全廠的管理計算機。
性能完善的軟體是實現FMS功能的基礎,除支持計算機工作的系統軟體外,數量更多的是根據使用要求和用戶經驗所發展的專門套用軟體,大體上包括控制軟體(控制工具機、物料儲運系統、檢驗裝置和監視系統)、計畫管理軟體(調度管理、質量管理、庫存管理、工裝管理等)和數據管理軟體(仿真、檢索和各種資料庫)等。
為保證FMS的連續自動運轉,須對刀具和切削過程進行監視,可能採用的方法有:測量工具機主軸電機輸出的電流功率,或主軸的扭矩;利用感測器拾取刀具破裂的信號;利用接觸測頭直接測量刀具的刀刃尺寸或工件加工面尺寸的變化;累積計算刀具的切削時間以進行刀具壽命管理。此外,還可利用接觸測頭來測量工具機熱變形和工件安裝誤差,並據此對其進行補償。
柔性製造系統按工具機與搬運系統的相互關係可分為直線型、循環型、網路型和單元型。加工工件品種少、柔性要求小的製造系統多採用直線布局,雖然加工順序不能改變,但管理容易;單元型具有較大柔性,易於擴展,但調度作業的程式設計比較複雜。
柔性製造系統未來將向發展各種工藝內容的柔性製造單元和小型FMS;完善FMS的自動化功能;擴大FMS完成的作業內容,並與計算機輔助設計和輔助製造技術(CAD/CAM)相結合,向全盤自動化工廠方向發展。
工作原理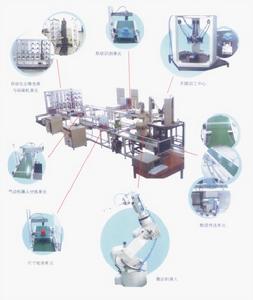
英國的Molin-24系統和日本東芝公司的FMS屬於典型的柔性製造系統。圖1是Molin-24系統的平面布置和控制原理圖。在巷道式工件貯存架的一邊排列著數控工具機群(共7台),另一邊則是向標準料車上安裝坯料的工件安裝台。工人按照計算機發出的指令將坯料安裝在料車上。此後,線上計算機 IBM1130(字長16位、記憶體4K、並附有容量為 500K的磁碟)控制兩台莫林自動傳送機。
傳送機(2)將工件傳送到巷道式工件貯存架,然後再由傳送機(1)將工件傳送到各台數控工具機的安裝工位。在毛坯供應庫里,按照計算機發出的指令將需要加工的工件毛坯準備好,並附上圖紙,放在毛坯供應庫的托板上。Molin-24可製造規格為300×300毫米以內的多種產品,適合於從幾件到百件的小批量生產,一天能製造產品 2000~20000件。非線上大型管理計算機以10天或更長的時間為單位,把這一期間內應加工零件的產品號、生產件數、坯料尺寸、切削作業的種類、數控紙帶編號等信息記入主暫存器中。同時編制日加工計畫,使工具機負荷均衡,儘量減少工具機窩工。日加工計畫同樣也存儲在主暫存器中,並可製成穿孔卡片作為線上計算機的輸入。
線上計算機向毛坯供應庫、工件安裝台、傳送機(1)、(2)及數控工具機發出指令,進行一系列管理控制。管理控制的順序是:在對編號為n的產品進行加工的前一天,行式印表機就將產量、坯料代碼與尺寸、料車上應安放坯料的件數、數控工具機代碼、數控加工程式代碼、刀具代碼、加工時間等列印出來。同時在毛坯供應庫中顯示出相應的信號,操作人員根據這個指示,將坯料裝入編有代碼的箱中,放在箱架上。
此後,代碼便自動進入計算機並被存儲起來,以備第二天加工時套用。次日,線上計算機便按照日計畫發出指令,控制傳送機(2)將箱子從供應庫箱架上取出並送至工件安裝台。當產品編號為n的箱子從供應庫送至安裝台後,安裝人員在規定的時間內將工件安裝在料車上,並撥好規定的代碼,向計算機發出回答信號,計算機遂對輸料車進行控制。料車由傳送機(2)輸送到靠近數控工具機的貯存架上暫存起來。加工時,傳送機(1)則根據計算機發來的指令從貯存架上抽出料車並裝到相應的數控工具機上。同時,該系統還能根據計算機指令選擇相應的數控加工穿孔帶和刀具。數控裝置中的插補器是用數字微分分析器構成的,數控帶必須每25毫秒向插補器提供一個插補段信息。
日本東芝公司自1983年起開始研製FMS。這種系統配備有兩台計算機,用於自動安排作業、生產計畫和工藝管理,控制自動輸送裝置、自動監控裝置、自動化倉庫和15台計算機數控加工中心。
關鍵技術
在進行柔性製造系統的設計、規劃時,主要涉及以下幾個關鍵技術,包括:柔性製造系統的監控和管理系統,柔性製造系統的物流系統,柔性製造系統的刀具傳輸和管理系統,柔 性製造系統的聯網技術,柔性製造系統的輔助系統設計等。
1.柔性製造系統的監控和管理系統
2.柔性製造系統的物流系統
3.柔性製造系統的刀具管理系統
4.柔性製造系統的通信
5.柔性製造系統的輔助系統 FMS的輔助系統包括清洗工作站、切削液自動排放和集中回收處理及集中供液、氣等設施組成。
製造方法
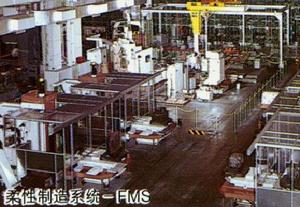
1、細胞生產方式:與傳統的大批量生產方式比較,細胞生產方式有兩個特點,一個是規模小(生產線短,操作人員少),另一個是標準化之後的小生產細胞可以簡單複製。由於這兩個特點,細胞生產方式能夠實現(1)簡單應對產量的變化,通過複製一個或以上的細胞就能夠滿足細胞生產能力整數倍的生產需求;(2)減少場地占用,細胞是可以簡單複製的(細胞生產線可以在一天內搭建完成),因此不需要的時候可以簡單拆除,節省場地;(3)每一個細胞的作業人數少,降低了平衡工位間作業時間的難度,工位間作業時間差異小,生產效率高;(4)通過合理組合員工,即由能力相當的員工組合成細胞,可以發揮員工最高的作業能力水平。如果能夠根據每一個細胞的產能給予相應的獎勵,還有利於促成細胞間的良性競爭。細胞生產線的形式是多樣的,有O形,也有U形,有餐檯形,也有推車形等等。
2、一人生產方式:我們看到過這樣的情形,某產品的裝配時間總共不足10分鐘,但是它還是被安排在一條數十米長的流水線上,而裝配工作則由線上的數十人來完成,每個人的作業時間不過10、20秒。針對這樣一些作業時間相對較短、產量不大的產品,如果能夠打破常規(流水線生產),改由每一個員工單獨完成整個產品裝配任務的話,我們將獲得意想不到的效果。同時,由於工作績效(品質、效率、成本)與員工個人直接相關,一人生產方式除了具有細胞生產的優點之外,還能夠大大地提高員工的品質意識、成本意識和競爭意識,促進員工成長。
3、一個流生產方式:一個流生產方式是這樣實現的,即取消機器間的台車,並通過合理的工序安排和機器間滑板的設定讓產品在機器間單個流動起來。它的好處是,(1)極大地減少了中間產品庫存,減少資金和場地的占用;(2)消除機器間的無謂搬運,減少對搬運工具的依賴;(3)當產品發生品質問題時,可以及時將信息反饋到前部,避免造成大量中間產品的報廢。一個流生產方式不僅適用於機械加工,也適用於產品裝配的過程。
4、柔性設備的利用:一種叫做柔性管的產品(有塑膠的也有金屬的)開始受到青睞。從前,許多企業都會外購標準流水線用作生產,現在卻逐步被自己拼裝的簡易柔性生產線取代。比較而言,柔性生產線首先可降低設備投資70-90%以上,其次,設備安裝不需要專業人員,一般員工即可快速地在一個周末完成安裝,第三,不需要時可以隨時拆除,提高場地利用效率。
5、台車生產方式:我們經常看到一個產品在製造過程中,從一條線上轉移到另一條線上,轉移工具就是台車。著眼於搬動及轉移過程中的損耗,有人提出了台車生產線,即在台車上完成所有的裝配任務。
6、固定線和變動線方式:根據某產品產量的變動情況,設定兩類生產線,一類是滿足某一相對固定最的固定生產線,另一類是用來滿足變動部分的變動生產線。通常,傳統的生產設備被用作固定線,而柔性設備或細胞生產方式等被用作變動生產線。為了徹底降低成本,在日本變動線往往招用勞務公司派遣的零時工(Part-Time)來應對,不需要時可以隨時退回。
柔性製造總的趨勢是,生產線越來越短,越來越簡,設備投資越來越少;中間庫存越來越少,場地利用率越來越高,成本越來越低;生產周期越來越短,交貨速度越來越快;各類損耗越來越少,效率越來越高。可見,實現柔性製造可以大大地降低生產成本,強化企業的競爭力。既然柔性製造是一種全新的和高境界的製造理念,因此它值得我們以持續改善的精神去思考去創造。[1]