擠出成型定義
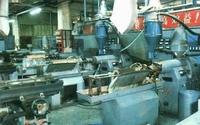
在纖維化學工業中也有用擠出機向噴絲頭供料,以進行熔體紡絲。擠出套用於熱塑性塑膠和橡膠的加工,可進行配料、造粒、膠料過濾等,可連續化生產,製造各種連續製品如管材、型材、板材(或片材)、薄膜、電線電纜包覆、橡膠輪胎胎麵條、內胎胎筒、密封條等,其生產效率高。在合成樹脂生產中,擠出機可作為反應器,連續完成聚合和成型加工,在橡膠工業中壓縮比不同的擠出機可以用來塑煉天然膠.不同材料的擠出機器的壓縮比有些不同.
原理
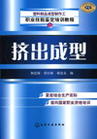
1、擠出方法
按塑化方式:乾法擠出與濕法擠出
按加壓方式:連續擠出與間歇擠出2、特點
生產連續、效率高、操作簡單、套用範圍廣
設備
1、主機擠出系統:由螺桿與料筒組成,是擠出機關鍵部分。其作用是塑化物料,定量、定壓、定溫擠出熔體
傳動系統:驅動螺桿,提高所需的紐矩和轉矩
加熱和冷卻系統:保證塑膠和擠出系統在成型過程中溫度達工藝要求
2、輔機
由機頭、定型裝置、冷卻裝置、牽引裝置、卷取裝置、切割組成
3、控制系統
由電器、儀表和執行機構組成
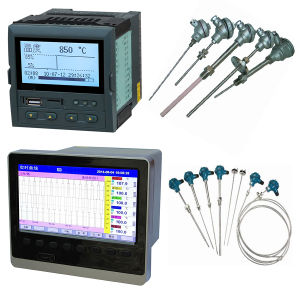
作用:控制主、輔機電動機、以滿足所需轉速和功率;控制主輔機溫度、壓力、流量,保證製品質量;實現擠出機組的自動控制,保證主、輔機協調運行。
概述
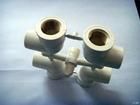
1.擠壓系統擠壓系統包括螺桿、機筒、料斗、機頭、和模具,塑膠通過擠壓系統而塑化成均勻的熔體,並在這一過程中所建立壓力下,被螺桿連續的擠出機頭。
(1)螺桿:是擠塑機的最主要部件,它直接關係到擠塑機的套用範圍和生產率,由高強度耐腐蝕的合金鋼製成。
(2)機筒:是一金屬圓筒,一般用耐熱、耐壓強度較高、堅固耐磨、耐腐蝕的合金鋼或內襯合金鋼的複合鋼管制成。機筒與螺桿配合,實現對塑膠的粉碎、軟化、熔融、塑化、排氣和壓實,並向成型系統連續均勻輸送膠料。一般機筒的長度為其直徑的15~30倍,以使塑膠得到充分加熱和充分塑化為原則。
(3)料斗:料斗底部裝有截斷裝置,以便調整和切斷料流,料斗的側面裝有視孔和標定計量裝置。
(4)機頭和模具:機頭由合金鋼內套和碳素鋼外套構成,機頭內裝有成型模具。機頭的作用是將鏇轉運動的塑膠熔體轉變為平行直線運動,均勻平穩的導入模套中,並賦予塑膠以必要的成型壓力。塑膠在機筒內塑化壓實,經多孔濾板沿一定的流道通過機頭脖頸流入機頭成型模具,模芯模套適當配合,形成截面不斷減小的環形空隙,使塑膠熔體在芯線的周圍形成連續密實的管狀包覆層。為保證機頭內塑膠流道合理,消除積存塑膠的死角,往往安置有分流套筒,為消除塑膠擠出時壓力波動,也有設定均壓環的。機頭上還裝有模具校正和調整的裝置,便於調整和校正模芯和模套的同心度。
擠塑機按照機頭料流方向和螺桿中心線的夾角,將機頭分成斜角機頭(夾角120o)和直角機頭。機頭的外殼是用螺栓固定在機身上,機頭內的模具有模芯坐,並用螺帽固定在機頭進線連線埠,模芯座的前面裝有模芯,模芯及模芯座的中心有孔,用於通過芯線;在機頭前部裝有均壓環,用於均衡壓力;擠包成型部分由模套座和模套組成,模套的位置可由螺栓通過支撐來調節,以調整模套對模芯的相對位置,便於調節擠包層厚度的均勻性。機頭外部裝有加熱裝置和測溫裝置。
2.傳動系統傳動系統的作用是驅動螺桿,供給螺桿在擠出過程中所需要的力矩和轉速,通常由電動機、減速器和軸承等組成。
3.加熱冷卻裝置加熱與冷卻是塑膠擠出過程能夠進行的必要條件。
(1)現在擠塑機通常用的是電加熱,分為電阻加熱和感應加熱,加熱片裝於機身、機脖、機頭各部分。加熱裝置由外部加熱筒內的塑膠,使之升溫,以達到工藝操作所需要的溫度。
(2)冷卻裝置是為了保證塑膠處於工藝要求的溫度範圍而設定的。具體說是為了排除螺桿鏇轉的剪下摩擦產生的多餘熱量,以避免溫度過高使塑膠分解、焦燒或定型困難。機筒冷卻分為水冷與風冷兩種,一般中小型擠塑機採用風冷比較合適,大型則多採用水冷或兩種形式結合冷卻;螺桿冷卻主要採用中心水冷,目的是增加物料固體輸送率,穩定出膠量,同時提高產品質量;但在料斗處的冷卻,一是為了加強對固體物料的輸送作用,防止因升溫使塑膠粒發粘堵塞料口,二是保證傳動部分正常工作。
二、輔助設備
塑膠擠出機組的輔機主要包括放線裝置、校直裝置、預熱裝置、冷卻裝置、牽引裝置、計米器、火花試驗機、收線裝置。擠出機組的用途不同其選配用的輔助設備也不盡相同。如還有切斷器、吹乾器、印字裝置等。
校直裝置:塑膠擠出廢品類型中最常見的一種是偏心,而線芯各種型式的彎曲則是產生絕緣偏心的重要原因之一。在護套擠出中,護套表面的刮傷也往往是由纜芯的彎曲造成的。因此,各種擠塑機組中的校直裝置是必不可少。校直裝置的主要型式有:滾筒式(分為水平式和垂直式);滑輪式(分為單滑輪和滑輪組);絞輪式,兼起拖動、校直、穩定張力等多種作用;壓輪式(分為水平式和垂直式)等。
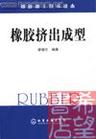
冷卻裝置:成型的塑膠擠包層在離開機頭後,應立即進行冷卻定型,否則會在重力的作用下發生變形。冷卻的方式通常採用水冷卻,並根據水溫不同,分為急冷和緩冷。急冷就是冷水直接冷卻,急冷對塑膠擠包層定型有利,但對結晶高聚物而言,因驟熱冷卻,易在擠包層組織內部殘留內應力,導致使用過程中產生龜裂,一般PVC塑膠層採用急冷。緩冷則是為了減少製品的內應力,在冷卻水槽中分段放置不同溫度的水,使製品逐漸降溫定型,對PE、PP的擠出就採用緩冷進行,即經過熱水、溫水、冷水三段冷卻。
三、控制系統
塑膠擠出機的控制系統包括加熱系統、冷卻系統及工藝參數測量系統,主要由電器、儀表和執行機構(即控制屏和操作台)組成。其主要作用是:控制和調節主輔機的拖動電機,輸出符合工藝要求的轉速和功率,並能使主輔機協調工作;檢測和調節擠塑機中塑膠的溫度、壓力、流量;實現對整個機組的控制或自動控制。
擠出機組的電氣控制大致分為傳動控制和溫度控制兩大部分,實現對擠塑工藝包括溫度、壓力、螺桿轉數、螺桿冷卻、機筒冷卻、製品冷卻和外徑的控制,以及牽引速度、整齊排線和保證收線盤上從空盤到滿盤的恆張力收線控制。
1.擠塑機主機的溫度控制
電線電纜絕緣和護套的塑膠擠出是根據熱塑性塑膠變形特性,使之處於粘流態進行的。除了要求螺桿和機筒外部加熱,傳到塑膠使之融化擠出,還要考慮螺桿擠出塑膠時其本身的發熱,因此要求主機的溫度應從整體來考慮,既要考慮加熱器加熱的開與關,又要考慮螺桿的擠出熱量外溢的因素予以冷卻,要有有效的冷卻設施。並要求正確合理的確定測量元件熱電偶的位置和安裝方法,能從控溫儀表讀數準確反映主機各段的實際溫度。以及要求溫控儀表的精度與系統配合好,使整個主機溫度控制系統的波動穩定度達到各種塑膠的擠出溫度的要求。
2.擠塑機的壓力控制
為了反映機頭的擠出情況,需要檢測擠出時的機頭壓力,由於國產擠塑機沒有機頭壓力感測器,一般是對螺桿擠出後推力的測量替代機頭壓力的測量,螺桿負荷表(電流表或電壓表)能正確反映擠出壓力的大小。擠出壓力的波動,也是引起擠出質量不穩的重要因素之一,擠出壓力的波動與擠出溫度、冷卻裝置的使用,連續運轉時間的長短等因素密切相關。當發生異常現象時,能排除的迅速排除,必須重新組織生產的則應果斷停機,不但可以避免廢品的增多,更能預防事故的發生。通過檢測的壓力表讀數,就可以知道塑膠在擠出時的壓力狀態,一般取後推力極限值報警控制。
3.螺桿轉速的控制
螺桿轉速的調節與穩定是主機傳動的重要工藝要求之一。螺桿轉速直接決定出膠量和擠出速度,正常生產總希望儘可能實現最高轉速及實現高產,對擠塑機要求螺桿轉速從起動到所需工作轉速時,可供使用的調速範圍要大。而且對轉速的穩定性要求高,因為轉速的波動將導致擠出量的波動,影響擠出質量,所以在牽引線速度沒有變化情況下,就會造成線纜外徑的變化。同理如牽引裝置線速波動大也會造成線纜外徑的變化,螺桿和牽引線速度可通過操作台上相應儀表反映出來,擠出時應密切觀察,確保優質高產。
4.外徑的控制
如上所述為了保證製品線纜外徑的尺寸,除要求控制線芯(纜芯)的尺寸公差外,在擠出溫度、螺桿轉速、牽引裝置線速度等方面應有所控制保證,而外徑的測量控制則綜合反映上述控制的精度和水平。在擠塑機組設備中,特別是高速擠塑生產線上,應配用線上外徑檢測儀,隨時對線纜外徑進行檢測,並且將超差信號反饋以調整牽引或螺桿的轉速,糾正外徑超差。
5.收卷要求的張力控制
為了保證不同線速下的收線,從空盤到滿盤工作的恆張力要求,希望收排線裝置有貯線張力調整機構,或在電氣上考慮恆線速度系統和恆張力系統的收卷等等。
6.整機的電氣自動化控制
這是實現高速擠出生產線應具備的工藝控制要求,主要是:開機溫度聯鎖;工作壓力保護與聯鎖;擠出、牽引兩大部件傳動的比例同步控制;收線與牽引的同步控制;外徑線上檢測與反饋控制;根據各種不同需要組成部件的單機與整機跟蹤的控制。
擠出機分類
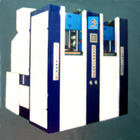
按空間位置:臥式和立式
按螺桿轉速:普通、高速和超高速
可否排氣:排氣式和非排氣式
按裝配結構:整體式和分開式
最常用臥式單螺桿非排氣式整體式擠出機
擠出機的主要零部件
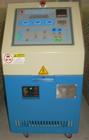
1、評價螺桿性能的標準和設計螺桿應考慮的因素
1)評價螺桿性能標準
①塑化質量:必須滿足質量要求。製品質量與機頭、輔機有關,但與螺桿的塑化質量關係更大,如溫度不均、軸向壓力波動、徑向溫度大、染色等分散不均勻,這都直接影響製品質量。
②產量:在保證質量前提下,通過機頭擠出量。好的螺桿,應具有高的塑化能力
③名義比功率單耗:每擠1Kg塑膠消耗的產量即P/Q(功率/產量),保證質量下,單耗越少越好。
④適應性:對加工不同塑膠、匹配不同機頭和不同製品的適應能力。但一般適應性強,往往塑化效率低。
⑤製造難易:必須易製造、成本低
2)設計螺桿應考慮
①物料特性及加工時的幾何形狀、尺寸、溫度狀況。由於不同物料物理特性不同,因此加工性能不同,對螺桿結構和幾何參數有不同要求。
②口模的幾何形式和機頭阻力特性。螺桿形狀要與他們相匹配。
料筒的結構形式和加熱冷卻情況。如在加料段料筒內壁加工出錐度和縱向溝槽並冷卻,則提高固體輸送效率,螺桿在設計時應考慮提高熔融速率、均化能力,使之與加料段輸送相匹配。
③螺桿轉速
④擠出機用途:作混煉、造粒和餵料等作用,螺桿結構有所不同
2、常規全螺紋三段螺桿設計
指螺桿由加料段、壓縮段、均化段三段螺紋組成,其擠出過程完全依靠螺紋的形式來完成的一種螺桿。
1)螺桿類型確定
按螺槽深度從加料段較深向均化段較淺的過渡情況分:
①漸變型:螺槽深度變化在較長距離逐漸變淺。用於無定型、熱敏性塑膠加工、也可用結晶型。
②突變型:用於熔點突變、粘度低的塑膠。如PA、PE、PP,不適於PVC等熱敏性塑膠
2)螺桿直徑
已經標準化,其大小一般根據所加工製品的斷面尺寸、加工塑膠種類、所需擠出量確定
3)螺桿長徑比L/Db
長徑比越大,則塑膠在料筒中停留時間越長,塑化更充分、均勻,以保證製品質
單螺桿擠出機技術參數和型號
1、單螺桿擠出機技術參數
螺桿直徑Db:指大徑,系列標準20、30、45、65、90、120、150、165、200、250、300
螺桿長徑比L/Db:螺桿工作部分長度與螺桿直徑比值
螺桿轉速範圍:nmin-nmaxr/min
驅動螺桿電機功率P:KW
擠出機生產能力Q:每小時擠出的塑膠量
比流量每小時每轉一周擠出機生產能力
名義比功率每小時加工kg塑膠所需電機功率
2、型號
SL-150表示螺桿直徑為150mm,長徑比為20:1塑膠擠出
擠出工藝參數
1、溫度
擠出成型溫度有料筒溫度、塑膠溫度、螺桿溫度,一般我們測料筒溫度。溫度由加熱冷卻系統控制,由於螺桿結構、加熱冷卻系統不穩定、螺桿轉速變化等原因使擠出物料溫度在徑向和軸向都存在波動,從而影響製品質量,製品各點強度不一樣,產生殘餘應力,表面灰暗無光澤。為保證製品質量,溫度應穩定。
2、壓力
由於螺桿和料筒結構,機頭、過濾網、過濾板的阻力,使塑膠內部存在壓力。壓力變化如圖,壓力同樣存在波動。
3、擠出速率
單位時間內由擠出機口模擠出的塑膠質量或長度。影響擠出速率因素:機頭阻力、螺桿與料筒結構、螺桿轉速、加熱、冷卻系統、塑膠特性。但當產品已定,擠出速率僅與螺桿轉速有關。擠出速率也存在波動,影響製品幾何形狀和尺寸。
溫度、壓力、擠出速率都存在波動現象,為了保證製品質量,應正確設計螺桿、控制好加熱冷卻系統和螺桿轉速穩定性,以減少參數波動。
擠出成型工藝
一般根據所加工聚合物的類型和製品或半成品的形狀,選定擠出機、機頭和口模,以及定型和牽引等相應的輔助裝置,然後確定擠出工藝條件如螺桿轉速、機頭壓力、物料溫度,以及定型溫度、牽引速度等。在擠出過程中,物料一般都要經過塑煉,但定型方法則有所不同。例如,擠出的塑膠常需冷卻定型,使其固化,而擠出橡膠的半成品,則尚需進一步硫化。採用不同的擠出設備和工藝,可得到不同的製品。
粒料
聚合物與各種添加劑混合後,送入擠出機中熔化,並進一步混合均勻。通過多孔口模,形成多根條料,再切斷成粒料。切斷有熱切粒和冷切粒之分。前者條料離口模後,一邊用空氣或水冷卻,一邊立即用鏇轉刀切斷。後者是將條料全部冷卻後,再送入切粒機切粒。
片材和薄膜
凡厚度在0.25mm以上,長度比寬度大很多的扁平製品稱片材;厚度小於0.25mm者稱薄膜。如將扁平口模出來的膜狀物,通過一表面十分光潔的冷卻轉鼓冷卻定型,即可製得平膜,此法也稱擠出流延法。這是製造聚丙烯薄膜常用方法。如果將所得平膜送入拉幅機,在縱向及橫向同時拉伸4~10倍(也可先縱向拉伸,再橫向拉伸),則可製得雙軸定向薄膜。由於拉伸時,大分子取向,因此薄膜強度很高,但透水、透氣性有所降低。常用於製造聚丙烯和聚酯薄膜。如物料內加發泡劑,並採用特殊螺桿和口模,也可製得低發泡沫塑膠板材。
包覆線
當金屬裸線通過一個T形口模時,熔融塑膠即圍繞裸線而形成包覆層(圖3[包覆線用機頭]),包覆線被冷卻卷繞後,即得各種電線電纜製品。
管材擠出工藝
設備:擠出機、機頭、定型裝置、冷卻槽、牽引設備和切割設備
1、成型
由擠出模具實現。熔體經過濾網和過濾板,分流區、壓縮區、成型區而成為管狀物。
2、定型
方法:內徑定徑與外徑定徑(內壓法與真空法)
3、管材擠出工藝條件控制
溫度:料筒、機頭和口模溫度,是影響塑化和製品質量的主要因素。擠出管材溫度一般較低,粘度高,有利於定型。
擠出速率:影響產量和質量,其值決定於螺桿轉速
牽引速度:影響管材壁厚和直徑的的精確性,要與擠出速度相適應。
壓縮空氣壓力:內壓法壓力0.02~0.05MPa
吹塑薄膜法成型工藝
1、擠出與吹脹
設備:擠出機及機頭、冷卻裝置、夾板、牽引輥、導向輥、卷取裝置。
2、吹塑薄膜擠出工藝條件
溫度:料筒、機頭和機頸溫度。溫度過高,薄膜發脆,抗拉強度下降;過高,抗拉強度低、表面光澤差、透明度下降、有熔接痕。
吹脹比與牽伸比:吹脹比—管膜直徑與口模之比(2-3);牽伸比—薄膜伸長倍數(4-6)。
冷卻速度:由冷卻裝置調節。冷凍線—吹脹管膜上已冷卻定型的線;冷凍線越遠,冷卻速度越慢,薄膜橫向易撕裂。
工藝套用
採用幾台擠出機,同時供應幾種塑膠,再通過共用機頭擠出,形成一個整體的複合製品。例如用A、B、C三種塑膠共擠出,可生產各種複合薄膜、複合片材、板材、型材和管材。
膠料過濾
在製造薄壁橡膠製品時,為了防止製品發生漏氣、漏水,膠料不能含有雜質,一般在加入硫化劑前用擠出機過濾膠料,即在機頭處放置一層或多層濾網,以濾去塑化物料中雜質。
輪胎胎面和內胎製造胎面分整體擠出和分層擠出。整體擠出可用一台擠出機將一種膠料經扁平口模擠出;也可用兩種膠料(胎冠料和胎側料)兩台擠出機共擠出,在共擠出機頭內結合成一個整體胎面。分層擠出則用兩台擠出機分別將兩種膠料擠成胎冠和胎側,再在運輸帶上進行熱貼合,並經多圓盤活絡輥壓為整體。內胎擠出和管子擠出相似,胎筒擠成後,經切斷,再接頭成型。
熔體紡絲
一些粘度大的樹脂在熔體紡絲時,常用擠出機來熔融物料。熔好的物料直接經過過濾器進入噴絲頭,或用噴絲泵打入噴絲頭。