簡介
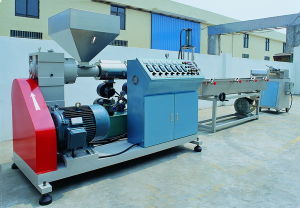
1.擠壓系統擠壓系統包括螺桿、機筒、料斗、機頭、和模具,塑膠通過擠壓系統而塑化成均勻的熔體,並在這一過程中所建立壓力下,被螺桿連續的擠出機頭。
(1) 螺桿:是擠塑機的最主要部件,它直接關係到擠塑機的套用範圍和生產率,由高強度耐腐蝕的合金鋼製成。
(2) 機筒:是一金屬圓筒,一般用耐熱、耐壓強度較高、堅固耐磨、耐腐蝕的合金鋼或內襯合金鋼的複合鋼管制成。機筒與螺桿配合,實現對塑膠的粉碎、軟化、熔融、塑化、排氣和壓實,並向成型系統連續均勻輸送膠料。一般機筒的長度為其直徑的15~30倍,以使塑膠得到充分加熱和充分塑化為原則。
(3) 料斗:料斗底部裝有截斷裝置,以便調整和切斷料流,料斗的側面裝有視孔和標定計量裝置。
(4) 機頭和模具:機頭由合金鋼內套和碳素鋼外套構成,機頭內裝有成型模具。機頭的作用是將鏇轉運動的塑膠熔體轉變為平行直線運動,均勻平穩的導入模套中,並賦予塑膠以必要的成型壓力。塑膠在機筒內塑化壓實,經多孔濾板沿一定的流道通過機頭脖頸流入機頭成型模具,模芯模套適當配合,形成截面不斷減小的環形空隙,使塑膠熔體在芯線的周圍形成連續密實的管狀包覆層。為保證機頭內塑膠流道合理,消除積存塑膠的死角,往往安置有分流套筒,為消除塑膠擠出時壓力波動,也有設定均壓環的。機頭上還裝有模具校正和調整的裝置,便於調整和校正模芯和模套的同心度。
擠塑機按照機頭料流方向和螺桿中心線的夾角,將機頭分成斜角機頭(夾角120o)和直角機頭。機頭的外殼是用螺栓固定在機身上,機頭內的模具有模芯坐,並用螺帽固定在機頭進線連線埠,模芯座的前面裝有模芯,模芯及模芯座的中心有孔,用於通過芯線;在機頭前部裝有均壓環,用於均衡壓力;擠包成型部分由模套座和模套組成,模套的位置可由螺栓通過支撐來調節,以調整模套對模芯的相對位置,便於調節擠包層厚度的均勻性。機頭外部裝有加熱裝置和測溫裝置。
2.傳動系統 傳動系統的作用是驅動螺桿,供給螺桿在擠出過程中所需要的力矩和轉速,通常由電動機、減速器和軸承等組成。
3.加熱冷卻裝置 加熱與冷卻是塑膠擠出過程能夠進行的必要條件。
(1) 現在擠塑機通常用的是電加熱,分為電阻加熱和感應加熱,加熱片裝於機身、機脖、機頭各部分。加熱裝置由外部加熱筒內的塑膠,使之升溫,以達到工藝操作所需要的溫度。
(2) 冷卻裝置是為了保證塑膠處於工藝要求的溫度範圍而設定的。具體說是為了排除螺桿鏇轉的剪下摩擦產生的多餘熱量,以避免溫度過高使塑膠分解、焦燒或定型困難。機筒冷卻分為水冷與風冷兩種,一般中小型擠塑機採用 風冷比較合適,大型則多採用水冷或兩種形式結合冷卻;螺桿冷卻主要採用中心水冷,目的是增加物料固體輸送率,穩定出膠量,同時提高產品質量;但在料斗處的冷卻,一是為了加強對固體物料的輸送作用,防止因升溫使塑膠粒發粘堵塞料口,二是保證傳動部分正常工作。
變頻器對塑膠造粒機的節能影響
塑膠造粒機專用變頻器特點:
■低頻轉矩輸出180%,低頻運行特性良好
■輸出頻率最大600Hz,可控制高速電機
■全方位的偵測保護功能(過壓、欠壓、過載)瞬間停電再起動
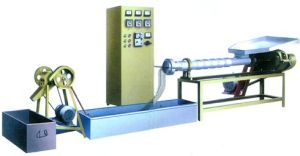
■加速、減速、動轉中失速防止等保護功能
■電機動態參數自動識別功能,保證系統的穩定性和精確性
■高速停機時回響快
■豐富靈活的輸入、輸出接口和控制方式,通用性強
■採用SMT全貼裝生產及三防漆處理工藝,產品穩定度高
■全系列採用最新西門子IGBT功率器件,確保品質的高質量
裝置設備
輔助設備
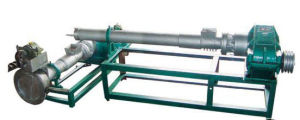
校直裝置:塑膠擠出廢品類型中最常見的一種是偏心,而線芯各種型式的彎曲則是產生絕緣偏心的重要原因之一。在護套擠出中,護套表面的刮傷也往往是由纜芯的彎曲造成的。因此,各種擠塑機組中的校直裝置是必不可少。校直裝置的主要型式有:滾筒式(分為水平式和垂直式);滑輪式(分為單滑輪和滑輪組);絞輪式,兼起拖動、校直、穩定張力等多種作用;壓輪式(分為水平式和垂直式)等。
預熱裝置
纜芯預熱對於絕緣擠出和護套擠出都是必要的。對於絕緣層,尤其是薄層絕緣,不能允許氣孔的存在,線芯在擠
包前通過高溫預熱可以徹底清除表面的水份、油污。對於護套擠出來講,其主要作用在於烘乾纜芯,防止由於潮氣(或繞包墊層的濕氣)的作用使護套中出現氣孔的可能。預熱還可防止擠出中塑膠因驟冷而殘留內壓力的作用。在擠塑膠過程中,預熱可消除冷線進入高溫機頭,在模口處與塑膠接觸時形成的懸殊溫差,避免塑膠溫度的波動而導致擠出壓力的波動,從而穩定擠出量,保證擠出質量。擠塑機組中均採用電加熱線芯預熱裝置,要求有足夠的容量並保證升溫迅速,使線芯預熱和纜芯烘乾效率高。預熱溫度受放線速度的制約,一般與機頭溫度相仿即可。冷卻裝置
成型的塑料擠包層在離開機頭後,應立即進行冷卻定型,否則會在重力的作用下發生變形。冷卻的方式通常採用水冷卻,並根據水溫不同,分為急冷和緩冷。急冷就是冷水直接冷卻,急冷對塑膠擠包層定型有利,但對結晶高聚物而言,因驟熱冷卻,易在擠包層組織內部殘留內應力,導致使用過程中產生龜裂,一般PVC塑膠層採用急冷。緩冷則是為了減少製品的內應力,在冷卻水槽中分段放置不同溫度的水,使製品逐漸降溫定型,對PE、PP的擠出就採用緩冷進行,即經過熱水、溫水、冷水三段冷卻。
控制系統
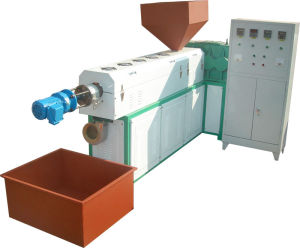
擠出機組的電氣控制大致分為傳動控制和溫度控制兩大部分,實現對擠塑工藝包括溫度、壓力、螺桿轉數、螺桿冷卻、機筒冷卻、製品冷卻和外徑的控制,以及牽引速度、整齊排線和保證收線盤上從空盤到滿盤的恆張力收線控制。
1. 擠塑機主機的溫度控制
電線電纜絕緣和護套的塑膠擠出是根據熱塑性塑膠變形特性,使之處於粘流態進行的。除了要求螺桿和機筒外部加熱,傳到塑膠使之融化擠出,還要考慮螺桿擠出塑膠時其本身的發熱,因此要求主機的溫度應從整體來考慮,既要考慮加熱器加熱的開與關,又要考慮螺桿的擠出熱量外溢的因素予以冷卻,要有有效的冷卻設施。並要求正確合理的確定測量元件熱電偶的位置和安裝方法,能從控溫儀表讀數準確反映主機各段的實際溫度。以及要求溫控儀表的精度與系統配合好,使整個主機溫度控制系統的波動穩定度達到各種塑膠的擠出溫度的要求。
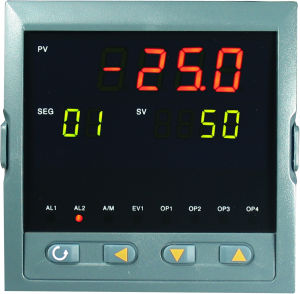
2. 擠塑機的壓力控制
為了反映機頭的擠出情況,需要檢測擠出時的機頭壓力,由於國產擠塑機沒有機頭壓力感測器,一般是對螺桿擠出後推力的測量替代機頭壓力的測量,螺桿負荷表(電流表或電壓表)能正確反映擠出壓力的大小。擠出壓力的波動,也是引起擠出質量不穩的重要因素之一,擠出壓力的波動與擠出溫度、冷卻裝置的使用,連續運轉時間的長短等因素密切相關。當發生異常現象時,能排除的迅速排除,必須重新組織生產的則應果斷停機,不但可以避免廢品的增多,更能預防事故的發生。通過檢測的壓力表讀數,就可以知道塑膠在擠出時的壓力狀態,一般取後推力極限值報警控制。
3. 螺桿轉速的控制
螺桿轉速的調節與穩定是主機傳動的重要工藝要求之一。螺桿轉速直接決定出膠量和擠出速度,正常生產總希望儘可能實現最高轉速及實現高產,對擠塑機要求螺桿轉速從起動到所需工作轉速時,可供使用的調速範圍要大。而且對轉速的穩定性要求高,因為轉速的波動將導致擠出量的波動,影響擠出質量,所以在牽引線速度沒有變化情況下,就會造成線纜外徑的變化。同理如牽引裝置線速波動大也會造成線纜外徑的變化,螺桿和牽引線速度可通過操作台上相應儀表反映出來,擠出時應密切觀察,確保優質高產。
4. 外徑的控制
如上所述為了保證製品線纜外徑的尺寸,除要求控制線芯(纜芯)的尺寸公差外,在擠出溫度、螺桿轉速、牽引裝置線速度等方面應有所控制保證,而外徑的測量控制則綜合反映上述控制的精度和水平。在擠塑機組設備中,特別是高速擠塑生產線上,應配用線上外徑檢測儀,隨時對線纜外徑進行檢測,並且將超差信號反饋以調整牽引或螺桿的轉速,糾正外徑超差。
5. 收卷要求的張力控制
為了保證不同線速下的收線,從空盤到滿盤工作的恆張力要求,希望收排線裝置有貯線張力調整機構,或在電氣上考慮恆線速度系統和恆張力系統的收卷等等。
6. 整機的電氣自動化控制
這是實現高速擠出生產線應具備的工藝控制要求,主要是:開機溫度聯鎖;工作壓力保護與聯鎖;擠出、牽引兩大部件傳動的比例同步控制;收線與牽引的同步控制;外徑線上檢測與反饋控制;根據各種不同需要組成部件的單機與整機跟蹤的控制。
節能
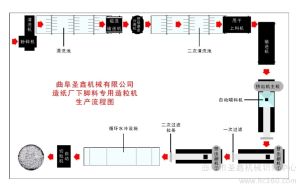
動力部分節能
大多採用變頻器,節能方式是通過節約電機的余耗能,例如電機的實際功率是50Hz,而你在生產中實際上只需要3
0Hz就足夠生產了,那些多餘的能耗就白白浪費了,變頻器就是改變電機的功率輸出達到節能的效果。加熱部分節能
加熱部分節能大多是採用電磁加熱器節能,節能率約是老式電阻圈的30%-70%。
1.相比電阻加熱,電磁加熱器多了一層保溫層,熱能利用率增加。
2.相比電阻加熱,電磁加熱器直接作用於料管加熱,減少了熱傳遞熱能損耗。
3.相比電阻加熱,電磁加熱器的加熱速度要快四分之一以上,減少了加熱時間。
4.相比電阻加熱,電磁加熱器的加熱速度快,生產效率就提高了,讓電機處在飽和狀態,使其減少了,高功率低需求造成的電能損耗。
以上四點就是電磁加熱器,為什麼能在塑膠造粒機上節能高達30%-70%的原因。
功能用途
功能
採用特殊的螺桿設計及不同配置,適用於生產PP、PE、PS、ABS、PA、PVC、PC、POM、EVA、LCP、PET、PMMA等多種塑膠的再生及混色造粒。減速箱採用高扭矩的設計,實現了無噪音運轉平穩等性能。螺桿,料筒經特殊的硬化處理,具有耐磨,混煉性能好,高產量的特性,真空排氣或普通排氣口的設計,能在生產過程中將水分,廢氣排走,使出料更穩定,膠粒更結實,保證了產品優良品質。
圖片
塑膠造粒機主要用於加工廢舊塑膠薄膜(工業包裝膜、農業地膜、大棚膜、啤酒包、手提袋等)、編織袋、農用方便袋、盆、桶、飲料瓶、家具、日常用品等,適用於大部分常見的廢舊塑膠,是廢舊塑膠再生行業用途最廣,使用最廣泛,最受用戶歡迎的塑膠再生加工機械。
特點
1、所有回收料經分類和破碎清洗後不需甩乾或烘、曬乾,即可生產,乾濕兩用。
2、從原料破碎、清洗、進料到製成顆粒均為自動化。
3、充分利用高壓摩擦不間斷升溫系統,自動加熱生產,避免了連續加熱,省電節能。
4、採用分體全自動配電系統,確保電機安全正常運轉。
5、螺桿料筒均採用進口高強度優質碳素結構鋼製造,經久耐用。
6、機器外觀美觀大方。可根據客戶要求配色噴漆。
正確操作
1.造粒機操作之預備作業:用於擠出成型的塑膠應注意其枯燥疑問,首要原材料應到達所需求的枯燥需求,必要時需作進一步枯燥。並將質料過篩除掉結塊團粒和機械雜質。
2.造粒機操作時,查看設備中水、電、氣各體系是不是正常,保證水、氣路疏通、不漏,電器體系是不是正常,加熱體系、溫度操控、各種外表是不是作業牢靠;輔機空車低速試作業,調查設備是不是作業正常;發動定型台真空泵,調查作業是不是正常;各種設備滑潤部位加油光滑。如發現毛病及時掃除。
3.裝機頭及定型套。依據商品的種類、尺度,選好機頭標準。按下列次序將機頭裝好。
4.造粒機操作之開車。
5.恆溫之後即可開車,開車前應將機頭和造粒機法蘭螺栓再擰緊一次,以消除螺栓與機頭熱膨脹的不一樣,緊機頭螺栓的次序是對角擰緊,用力要均勻。緊機頭法蘭螺母時,需求附近鬆緊共同,否則要跑料。
6.造粒機操作時,選按“預備開車”鈕,再接“開車”鈕,然後緩慢鏇轉螺桿轉速調理鏇鈕,螺桿轉速慢速發動。然後再逐步加速,一起少數加料。加料時要密切注意主機電流表及各種指示表頭的指示改變狀況。螺桿扭矩不能跨越紅標。造粒機操作時,塑膠型材被擠出之前,任何人均不得站於口模正前方,以避免因螺栓拉斷或因質料濕潤放泡等緣由此發作傷害事故。塑膠從機頭口模擠出後,即需將擠出物漸漸冷卻並引上牽引設備和定型模,並開動這些設備。然後依據操控外表的指示值和對擠出製品的需求。將各部分作相應的調整,以使整個擠出操作到達正常狀況。並依據需求加足料,雙螺桿造粒機操作選用計量加料器均勻等速地加料。
7.裝拆機頭、螺桿等粗笨部件,造粒機操作時應注意的安全項目有:電、熱、機械的轉變和粗笨部件的裝卸
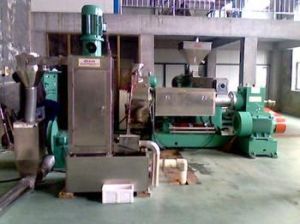
8.造粒機操作之開車,通常可依據擠出物料的外觀來判別,當口模出料均勻且塑優傑出可進行牽引人定型套。塑化程度的判別需憑經歷。即外表有光澤、無雜質、無發泡、焦料和變色,用手將擠出料擠細到必定水平不呈現毛刺、裂口,有必定彈性,此刻闡明物料塑化傑出。若塑化不良則可恰當調整螺桿轉速、機筒和機頭溫度,直至到達需求。應按技術需求定時查看各種技術參數是不是正常。並填寫技術記載單。按質量檢驗標準查看型材商品的質量,發現疑問及時採納處理辦法。
9.造粒機操作之泊車,將造粒機內的塑膠擠光,造粒機操作中止加料。顯露螺桿時,封閉機筒和機頭電源,中止加熱。使螺桿和輔機中止作業。封閉造粒機及輔機電源。
10.安裝機頭。整理多孔板及機頭的各個部件。整理時為避免損壞機頭內外表,3翻開機頭聯接法蘭。機頭內的剩餘料使用鋼律、鋼片進行整理,然後用砂紙將粘附在機頭內的塑膠磨除,並打光,塗上機油或矽油防鏽。拆下機頭後,螺桿、機筒的整理。重新發動主機,加泊車料(或破碎料)清潔螺桿、機筒,此刻螺桿選用低速(sr/min左右)以削減磨損。待泊車料碾成粉狀徹底擠出後,可用壓縮空氣從加料口,排氣口重複吹出殘留粒料和粉料,直至機筒內確實無殘存料後,降螺桿轉速至零,中止造粒機,封閉總電源及冷水總閥門。
模具
塑膠造粒機模具分為手動和電動,造粒機需經常換網用以去掉雜質,擠出模具一般為18孔,過濾網阻塞後擠出機壓力很大,原始手動換網會比較累,可使用電動模具,用電動機代替人工,省時省力。
故障排除
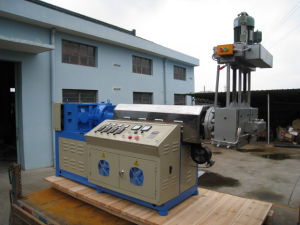
原因:料斗進料不連續;進料口有異物堵塞或產生“架橋”;螺槽內掉入金屬堅硬物堵塞螺槽,不能正常送料;
處理方法:增加進料量使螺桿送料連續穩定;停機排除料口中的異物消除“架橋”現象;如果確認有金屬異物掉進螺槽中,應立即停機拆卸螺桿,排除金屬異物。
原因:主電動機的電源未接通;加熱升溫時間不足,或其一加熱器不工作,從而造成扭矩過大使得電機過載。
處理方法:檢查主機電路是否接通,接通電源;檢查各段溫度顯示,確認預熱升溫時間,檢查各加熱器是否已損壞或者有接觸不良現象,並排除。
原因:原料不夠乾淨帶有雜質;進料速度過快使得螺桿擠出不穩定;塑化溫度不夠螺桿擠出成問題。
處理方法:把原料清洗乾淨再進料或者更換過濾網;減少進料量使塑化穩定螺桿順利擠出;提高塑化溫度(溫度不宜過高,以防燒傷塑膠,影響生產質量)。
⒋主電動機轉動,但螺桿不轉
原因:傳動V頻寬松,磨損打滑;安全鍵寬鬆脫落或者斷開。
處理方法:調整V帶中心距,拉緊皮帶,或者更換新的V帶;檢查安全鍵,分析斷裂原因,並更換安全鍵。
操作細則
一、目的
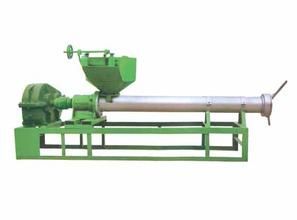
二、適用範圍
僅適用該公司生產的TPR∕EVA∕PVC/色母/無囟電纜料/橡膠高填充工程料等生產線設備的作業指導。
三、專項職責
由使用單位指定的設備專項操作員和維護保養員不得違規操作,並必須熟練的操作設備,要監督無關人員不得靠近和亂動與損壞設備的職責。
四、作業細則
⒈依次打開電源,設定溫度和注意加溫是否正常。
⒉清理料斗等機組,進出水管,檢查各齒輪油,機油,高溫黃油的油位和潤滑狀態,新機的齒輪油最遲半年更換一次,活動部位每周至少添加一次潤滑油。
⒊溫度快到設定溫度時,準備物料並依次啟動主電機。
⒋擠出機的溫度必須達到設定溫度,開啟餵料裝置才能倒入清洗料或原料清洗螺桿內的殘留物,直至新料擠出來,然後暫停擠料,快速到位地安裝好過濾板和模頭。方可合上模頭,合上模頭後開啟造粒機主螺桿電機,操作人員此時遠離模頭,以防模頭硬料堵塞爆裂傷人,直到模頭擠出絲料,然後合上切粒罩並連線切料刀架和鎖緊。⒌以上操作到位後依次按順序開啟所有風機>;振動篩>;切粒機>;主機的運作。
⒍正常出粒時調節切粒機,進行變頻調速調整顆粒大小。螺桿在出料前必須讓切粒機不停地轉動,如果是水冷噴霧式切粒,切粒罩要先通水,最後開啟主機進行正式生產。
⒎啟動擠出主機並由慢而快地根據粒子大小需求調節主機和切粒機的變頻調速,只有達到二者協調,才能使切出的粒子更好地均勻和粒子的出量最大化。
⒏停止作業操作順序與開機生產操作順序相反,先關主機驅動,然後依次關閉輔機電源,最後快速的清理模頭,以防模頭冷卻堵塞(特別注意:每班次作業停機後模頭出料孔和過濾板必須完全清孔才能再次安裝生產,否則模頭因堵塞有爆炸之危險)。
五、注意事項
⒈嚴禁無關人員和設備操作員交談,只準單人操作電控面板上的按鈕指令;
⒉定期檢測電線電路的絕緣效果,時刻注意機器警示牌上的警告內容;
⒊配電櫃未斷電前,嚴禁非專業人員打開櫃門,嚴禁在切粒機完全靜止前調整刀具;
⒋活動部位及料斗堵塞時,切勿用手或鐵棍,而只能用塑膠棍去小心處理;
⒌接觸高溫部位時,小心燙傷,捏合機工作時,嚴禁工作人員上半身伸入桶內探視或扒料;
⒍工作中如停電應對各電機電路切斷並及時清理完機記憶體料,物料碳化後影響下次生產;
⒎機器出現故障時,要在第一時間內停止機器運作,不得自行主張。並通知和等待機修人員來排查維修或電話指導維修;
⒏防止一切的因素導致機器損壞和工傷事故的發生;嚴格按照規範的操作方法來進行操作,減少故障或事故的發生。9.操作人員填料時,一定要看好,料中不要進雜物,掌握好溫度。
10.如果一開機時,料不成條出現粘模頭的現象,是模頭溫度過高,等稍一冷卻即可正常,一般情況下不用停機。
11.水溫一般應在50---60℃,低了容易斷條,超出容易粘連,初開機時最好加一半熱水,如沒有條件,切粒時可用人向切粒機內輸送一段時間,等水溫升高后再讓其自動切粒,以免斷條,水溫超過60℃後,需向內循環加入冷水,以保持溫度。12.切粒時一定要將條拉均後才能入兌輥,否則將損壞切粒機。如排氣孔向外爭劇冒料,證明雜質已堵住了過濾網,此時須速停機更換網片,網片可選用40---60目。