工程概述

重慶九龍電力股份有限公司重慶九龍發電廠為一台容量200MW的火力發電廠,於1996年投運,鍋爐出力為670噸/小時,處理煙氣量為830000 Nm3/h(乾態),880000Nm3/h(濕態),煙氣中SO2含量為 8200-10000mg/Nm3,採用石灰石-石膏濕法煙氣脫硫技術,脫硫率要求95%以上,排煙SO2含量滿足國家規範《電廠大氣污染排放標準》要求。本脫硫裝置為EPC建設方式,由中電投遠達環保工程有限公司總承包,脫硫技術採用石灰石-石膏濕法脫硫技術,引進日本國三菱液柱塔脫硫技術,其中的吸收塔內部裝置和循環泵由三菱供貨。
工程從2003年2月正式開工建設,2004年5月順利實現脫硫島受電,2004年11月20日首次通煙,2005年1月30日順利通過168小時試運行。168小時期間脫硫率平均為97.64%。
系統設計情況
本裝置採用石灰石-石膏濕法脫硫技術,引進日本國三菱液柱塔脫硫技術,主要的工藝系統為煙氣系統、吸收塔吸收系統、石灰石磨製系統、石膏脫水系統以及一些輔助的公用系統,如電氣系統、熱控控制系統、工藝水和壓縮空氣系統等。
設計條件下性能與保證值是:
⑴脫硫率:≥95%;
⑵FGD出口煙塵濃度:≤70 mg/Nm3(乾態, 6%O2)
⑶煙囪入口煙氣溫度:≥80℃;
⑷石膏品質石膏純度≥90wt%、含水量≤10wt%
⑸廢水排放量:27t/h;
⑹裝置可用率:≥95%;
⑺石灰石消耗量:12.7 t/h
⑻工藝水消耗量:126.6 t/h
⑼電耗:≤5900kW
主要工藝流程
來自鍋爐引風機的煙氣,經過布置在脫硫島入口處的原煙氣擋板後進入增壓風機,增壓風機採用動葉可調風機,增壓後再進入吸收塔,吸收塔設計為U型塔,分為順流區和逆流區,煙氣先進入順流區,然後再進入逆流區,經過脫硫後,經過除霧器脫除煙氣中的霧滴後進入淨煙道,在吸收塔出口的淨煙道布置有SGH換熱器,將煙氣加熱到82℃以上後通過淨煙道擋板進入煙囪排放。
為保證鍋爐在起動階段和煙氣脫硫設備(FGD)停運期間有煙氣通道,設計了100%旁路煙道,煙氣通過旁路煙道進入煙囪。
吸收塔設計了5台再循環泵,4用1備,按照液氣比要求保持足夠的漿液循環量;設計了2台氧化風機,1用1備,將亞硫酸鈣氧化成硫酸鈣;設計了2層除霧器,以除去煙氣中夾帶的霧滴;設計了6台攪拌器,4檯布置在氧化區,2檯布置在中和區,防止漿液發生沉澱;設計了事故噴淋系統,當FGD入口煙氣溫度過高、緊急停止、吸收塔所有循環泵故障或電壓過低,事故噴淋系統自動投入。
石灰石漿液由石灰石漿液泵送入吸收塔, 石灰石漿液的加入量用調節門自動進行控制,以保持吸收液的pH值於5到6之間。
石膏漿液排出泵將濃度為30%固體的石膏漿液,從吸收塔排出到石膏漿液箱,然後通過石膏漿液泵輸送到石膏皮帶脫水機脫水。
兩座吸收塔公用一個事故罐,在檢修期間,將石膏漿輸送到事故罐儲藏,在設備再起動之前,把漿液送回吸收塔。
調試情況介紹
本工程是遠達環保首台EPC總承包的脫硫裝置工程,也是遠達首次獨立調試的一台脫硫裝置,根據遠達公司的發展要求,為將公司做大,做強,追求卓越的宗旨,公司組成了以工程部副經理為首的專業調試隊伍,按照電力系統啟動規程成立了脫硫啟動試運指揮部,下設分部試運組、整套啟動試運組、驗收檢查組、生產準備組和綜合組。2004年8月19日裝置正式進入調試階段,開始進行設備的單體調試、分系統調試,整套裝置於2004年11月20日達到通煙條件,完成了工藝水及壓縮空氣系統、石灰石輸送及磨製系統、吸收塔漿液循環及氧化系統、煙氣及增壓風機系統(含SGH換熱器)、石膏脫水系統等分系統的調試。
2004年11月20日裝置順利實現首次進煙,但在23日,發現增壓風機動葉不能可靠動作,於2004年11月23日停止熱態調試,檢查風機後發現風機動葉液壓機構漏油嚴重,動葉同步性較差,因此,風機只能返廠處理。經過近一個月的返廠處理後,風機於2005年1月6日返回現場,1月10日系統再次啟動通煙,風機運轉正常,系統遂進入熱態調試。
經過連續13天的熱態調試,整套裝置與2005年1月23日正式進入168小時試運行,於2005年1月30日順利完成168小時試運行。
FGD系統熱態調試情況
啟動前的檢查
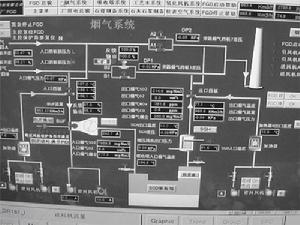
在FGD系統啟動前組織專門人員全面檢查FGD系統各部分,確保系統內無人工作,各設備啟動條件滿足。對煙道及吸收塔內部檢查時要確保煙氣不會進入,各煙氣擋板不進行操作。對各種罐體內部進行檢查要確保內部含氧量足夠。檢查完必須關好人孔門。
進煙熱態情況
主機鍋爐帶滿負荷正常運行,FGD裝置具備投入運行條件。工程首次啟動情況如下:
啟動公用系統
啟動兩台工藝水泵,第三台泵備用,維持系統壓力為0.55Mpa~0.6Mpa。
各冷卻水系統投入運行。啟動一台儀用空壓機,維持系統壓力為0.6Mpa。
啟動製漿系統
根據石灰石漿液箱液位情況,啟動製漿系統:球磨機及其輔助設備。
根據石灰石倉料位情況,啟動石灰石接收系統。
啟動石灰石漿液泵,進行漿液循環。
啟動吸收塔系統
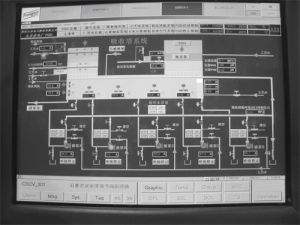
啟動吸收塔攪拌器。順序啟動4台再循環泵,實現吸收塔內漿液循環,投入PH計和密度計運行。
啟動1台氧化風機投入運行,氧化風量在14000Nm3/h左右。
煙氣系統啟動
啟動增壓風機密封風系統;然後啟動增壓風機油站,維持潤滑油壓0.2Mpa,調節油壓力4Mpa左右;系統正常後,開FGD入口擋板;開FGD出口擋板;關閉吸收塔排空擋板;啟動增壓風機;根據煙氣情況,手動調節增壓風機動葉。
石膏脫水系統啟動
啟動濾布沖洗水泵;開啟工藝水給水閥;啟動真空皮帶脫水機;啟動真空泵;開啟皮帶脫水機給料閥;
蒸汽換熱系統啟動
通知主機開啟汽機5抽或輔助蒸汽聯箱的出口蒸汽閥門,給脫硫送蒸汽,壓力穩定在0.2Mpa,溫度為250℃。當凝結水箱液位到高位時,啟動凝結水泵。
系統正常運行後,開始調試吸收塔,調整吸收塔PH值和密度,調節石灰石漿液流量,並及時進行漿液分析。調節BUF動葉角度,使BUF風量與主機煙氣量相匹配。在運行過程中須注意運行中的設備以預防設備故障,注意各運行參數並與設計值比較,發現偏差及時查明原因。要做好數據的記錄以積累經驗。
運行中保證吸收塔液位、PH值和漿液濃度的正常。保持吸收塔液位在正常範圍內。通過調整石灰石漿液供給量使吸收塔漿液的PH值保持在5.0~6.0範圍內。
系統運行中的檢查和維護
對各系統運行中常規檢查和維護包括以下內容:
FGD系統在運行中保持系統的清潔性,對管道的泄漏、固體的沉積、管道結垢及管道污染等現象及時檢查,發現後進行清潔。
轉動設備的潤滑不允許沒有必需的潤滑劑而啟動轉動設備,運行後應常檢查潤滑油位,注意設備的壓力、振動、噪音、溫度及嚴密性。
轉動設備的冷卻中,對電動機、風機、空壓機等設備的空冷狀況經常檢查以防過熱;對水冷設備應確保冷卻水的流量。
所有泵和風機的馬達、軸承溫度的檢查:經常檢查以防超溫。
罐體、管道要經常檢查法蘭、人孔等處的泄漏情況,及時處理。
攪拌器在啟動前必須使漿液浸過攪拌器葉片以上一定高度,葉片在液面上轉動易受大的機械力而遭損壞,或造成軸承的過大磨損。
離心泵在啟動前必須有足夠的液位,其吸入閥應全開。另外泵出口閥未開而長時間運行是不允許的。
泵的循環迴路
大多數輸送漿液的泵在連續運行時形成一個迴路,根據經驗,最主要的是要防止固體沉積於管底,發生沉積時可從以下現象得到反映:即漿液流量隨時間而減小;泵的出口壓力隨時間而增加,但短期內壓力增加不明顯。
若不能維持正常運行的壓力或流量時,必須對管道進行沖洗;沖洗無效時只能移出管子進行機械除去沉積物。 FGD的入口煙道和旁路煙道可能嚴重結灰,這取決於電除塵器的運行情況。一般的結灰不影響FGD的正常運行,當在擋板的運動部件上發生嚴重結灰時對擋板的正常開關有影響,因此應當定期如每個星期開關這些擋板以除灰,當FGD和鍋爐停運時,檢查這些擋板並清理積灰。
氧化空氣管路如需要清洗,不必關閉FGD系統。除霧器可能被石膏漿粒堵塞,這可從除霧器的差壓增大反映出來,此時須加大沖洗力度。氧化空壓機運行時注意檢查油壓、油位、油溫及濾網清潔。石膏脫水系統主要檢查沖洗水系統是否正常。
試運期間,吸收塔中的PH值、吸收塔和水力鏇流器底流的漿液密度、吸收塔漿液和石膏漿液中的CaCO3含量、吸收塔漿液中的CaSO3•1/2H2O含量每天至少測量一次。
FGD整套啟動調試及168小時試運行情況簡介
2004年11月20日,脫硫裝置順利實現首次通煙。通煙之後,發現增壓風機動葉調節不能滿足開度要求,其現象是動葉角度無論是開到70%還是20%,風機流量沒有變化,電機電流沒有變化。於11月22日停止風機運行後檢查,發現增壓風機有漏油現象發生,經過廠家人員現場檢查後,回裝動葉調節裝置導致動葉角度發生了位移,動葉相互發生了碰撞而被迫返廠處理。
2005年1月6日,返廠處理好的增壓風機返回到現場,恢復後,於2005年1月11日系統再次啟動,首先進行了檢查增壓風機性能的測試工作,根據廠家提供的風機性能曲線,風機動葉角度開度範圍為-30~+30度,檢查了風機動葉角度開度在-15度角度(25%)、+5度(58.3%)、+12度(70%)情況,風機流量、出口壓力、電機電流均滿足設計要求。
2005年1月15日,經過試運指揮部同意後,開始做關閉旁路擋板的試驗,鍋爐負荷為100%滿負荷,根據旁路擋板前後的壓差調節BUF動葉角度,找到了BUF動葉角度開度與鍋爐負荷的曲線關係,為動葉自動投入做好技術準備。
2005年1月17日,開始測試原、淨煙氣中的二氧化硫濃度、煙氣壓力、煙氣流速、溫度、HF、HCL和水分等物質成分。1月21日測量全部完成後,進行了煙氣分析儀的標定工作。在此期間同時進行了吸收塔的熱態調試,測量漿液成分,分析石膏成分、調整漿液濃度和酸鹼度,控制吸收塔水量平衡等調試工作。
真空皮帶脫水機投入運行了進口皮帶機,該設備運行狀況良好。
系統於2005年1月23日下午16點正式進入168小時試運行,經過連續7天的運行,鍋爐負荷為100%滿負荷,BUF風機風量平均為830000Nm3/h,煙氣含硫量平均在7706.74mg/ Nm3,脫硫率平均97.64%,石膏純度大於90%,吸收塔入口溫度平均154℃,SGH出口溫度平均大於82℃,工藝水耗量平均約110噸/小時;石灰石耗量平均11.6噸/小時,系統運行穩定,各項指標達到設計要求。
168小時運行主要參數的平均值如下:
煙氣流量:830000Nm3/h;
脫硫效率:97.64%;
FGD入口含硫量:8706.74mg/Nm3;
FGD出口含硫量:188.7mg/Nm3;
增壓風機電流:244A;
增壓風機出口壓力;2900Pa;
吸收塔液位:8000mm;
吸收塔PH值:5.7
石膏排出泵出口含固量:30%;
石灰石消耗量:11.6t/h;
工藝水的水耗量:110t/h;
廢水排放量:31t/h;
石膏純度:94.67%
結論
球磨機系統運行正常,出力滿足設計要求,能夠保證裝置需漿要求。
吸收塔系統運行良好,達到了設計要求,滿足了裝置運行要求。
煙氣系統運行良好,達到了設計要求,滿足裝置運行要求。
脫水系統運行良好,滿足裝置運行要求。
公用系統運行良好,滿足裝置運行要求。
(1) 保護投入率100%
(2) 自動投入率100%
(3) 儀表投入率100%
(4) 調試的質量檢驗分項目合格率100%。
(5) 試運的質量檢驗整體優良率≥95%
(6)完成168小時試運的啟動次數1次。
問題與建議
通過整套裝置調試情況來看,有以下一些問題出現,需要進行處理消缺:
1石膏漿液泵出力問題
石膏漿液泵設計流量為170噸/小時;但實際該泵在投運後流量較低,沒有達到設計流量,將其流量與從吸收塔進石膏漿液箱的流量來比較,估計該泵出口流量約50噸/小時,不能滿足漿液流量平衡,同時,該泵進入石膏鏇流器的壓力小於設計壓力,設計壓力為0.185Mpa,實際壓力只有0.15Mpa,導致石膏鏇流器的分離效果較低,造成這種現象的原因可能是漿液泵壓力不夠或管道過小。應根據實際情況,進行修改。
2濾液水泵出力問題
濾液水泵設計流量為40噸/小時;但實際該泵在投運後流量較低,沒有達到設計流量,實際流量約27噸/小時,實際廢水排放約31噸/小時,廢水排放不能滿足平衡,分析原因可能是漿液泵壓力不夠或設備問題等原因。應根據實際情況,進行修改。