工藝簡介
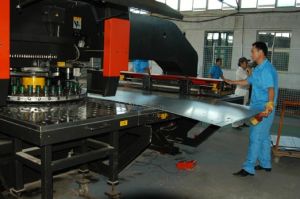
歷史沿革
1.衝壓技術發展的特徵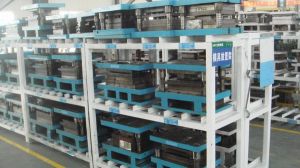
衝壓技術的真正發展,始於汽車的工業化生產。20世紀初,美國福特汽車的工業化生產大大推動了沖術的研究和發展。研究工作基本上在板料成形技術和成形性兩方面同時展開,關鍵問題是破裂、起皺與回彈,涉及可成形性預估、成形方法的創新,以及成形過程的分析與控制。但在20世紀的大部分時間裡,對衝壓技術的掌握基本上是經驗型的。分析工具是經典的成形力學理論,能求解的問題十分有限。研究的重點是板材衝壓性能及成形力學,遠不能滿足汽車工業的需求。60年代是衝壓技術發展的重要時期,各種新的成形技術相繼出現。尤其是成形極限圖(fld)的提出,推動了板材性能、成形理論、成形工藝和質量控制的協調發展,成為衝壓技術發展史上的一個里程碑。
由於80年代有限元方法及cad技術的先期發展,使90年代以數值模擬仿真為中心的和計算機套用技術在衝壓領域得以迅速發展並走向實用化,成為材料變形行為研究和工藝過程設計的有力工具。汽車衝壓技術真正進入了分析階段,傳統的板成形技術開始從經驗走向科學化。
縱觀上世紀的發展歷程可見:
(1)衝壓性能的研究和改進是與衝壓技術的發展相輔相承的。
(2)汽車、飛機等工業的飛速發展,以及能源因素都是衝壓技術發展的主要推動力。進入新世紀,環境因素及相關的法律約束日益突出,汽車輕量化設計和製造成為當前的重要課題。
(3)成形過程數位化仿真技術的發展,推動傳統衝壓技術走向科學化,進入先進制造技術行列。
(4)衝壓技術的發展涉及材料、能源、模具、設備等各方面。工藝方法的創新及其過程的科學分析與控制是技術發展的核心;模具技術是衝壓技術發展的體現,是決定產品製造周期、成本、質量的重要因素。
2、先進成形技術的發展
衝壓技術的發展與材料和結構密切相關。預計未來10-15年,環境要求和日益嚴格的環保法律,將促使汽車材料和結構發生很大變化。為了減少城市co2的排放量,汽車力求輕量化,其最突出的發展方向是提高所用材料的比強度和比剛度及發展高效的輕量化結構。現代車身結構中,高強度鋼約占25%。目前在繼續開發超高強度鋼的同時,結合發展新的“高效結構”和製造技術,爭取使車身重量減少20%以上。但更引人關注的努力方向是擴大鋁、鎂等低密度合金材料在汽車上的套用。
歐美正在研究開發未來型的鋁車身家用小汽車,可使重量減輕40-50%,耗油僅為現行小汽車平均值的三分之一。目前的主要問題是開發低成本鋁合金,發
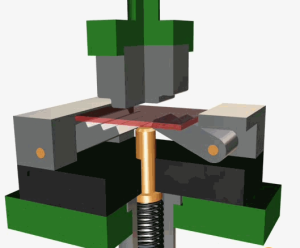
自1991年以來,鎂的產量每5年增加1倍,是很有前途的未來材料,預計2003年後鎂的套用將有明顯上升,包括大的車身外部零件。
複合板材料在汽車、飛機、醫藥、食品、化工、日用品等方面也均有廣闊套用前景。
此外烘烤硬化板、表面改性板等改性材料。80年代,歐美研究鍍鋅板的衝壓技術;90年代,重點研究雷射拼焊板的衝壓及各種擠壓管坯型材的精密成形技術。鋁型材骨架件的用量也在不斷增加。
結構整體化是重要的發展趨勢,不僅對於飛機,未來汽車也將擴大套用。
隨著新材料和新結構的擴大套用,迫切需要發展相應的低成本衝壓成形技術。當前的研究重點:
鋁合金覆蓋件等車身零件的衝壓技術。國外已有實用的工藝及模具設計數據資料。
(2)多種厚度雷射拼焊板坯的衝壓技術。
(3)擠壓管坯的內高壓成形技術。
(4)複合板的成形技術等。
對於飛機工業來說,鈦合金、鋁鋰合金複雜形狀零件及鋁合金特殊結構件的成形技術是當前的研究重點。
以液體直接或間接作為半模或感測應介質的各種液壓成形技術,屬於半模成形或軟模成形,有很多優點(已有近60年歷史),是飛機鈑金零件的主要製造方法。近十多年來在高壓源及高壓密封問題解決後,得以迅速發展,在汽車工業中獲得重要套用。液壓成形包括液壓橡皮囊成形、充液拉深成形和內高壓脹管成形。液壓橡皮成形已從航空工業的傳統套用擴大到汽車的複雜內外板件的成形,在100-140mpa的壓力下,成形質量很好,適用於試製和小批量生產。新興的內高壓成形技術已經實用化、工業化,生產發動機的支架、排氣管、凸輪軸及框架件等,達到了很好的效率和效益預計液壓成形、拼焊毛坯衝壓成形及雷射焊接裝配將是未來汽車輕量化的三項關鍵技術。
此外粘介質壓力成形、磁脈衝成形,以及各種無模成形技術的研究也有很大進展,顯現出越來越多的工藝柔性。
3.數位化成形技術的發展
先進成形技術是在傳統成形技術的基礎上,以計算機為支柱,綜合利用信息、電子、材料、能源、環境工程等各項高新技術及現代管理技術,有利於最終實現產品全生命期綜合最佳化的衝壓成形技術,是能越大程度地達到“精、省、淨”目標,獲得高綜合效益的成形技術。
發展先進成形技術的關鍵在於:
大力發展衝壓成形過程的計算機分析仿真技術(cae)。
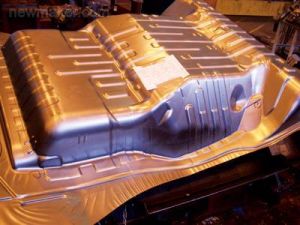
計算機輔助過程分析仿真(cae)是20世紀後期對於金屬成形最具重大意義的技術進步之一,其核心是有限元分析技術。
以有限元法為基礎的衝壓成形過程中計算機仿真技術或數值模擬技術,以衝壓模具設計、衝壓過程設計與工藝參數最佳化提供了科學的新途徑,將是解決複雜衝壓過程設計和模具設計的最有效手段。國外大型企業的套用步伐非常迅速,而汽車工業走在前列,現已逐漸成熟,用於模具設計和試模的時間減少50%以上。美國gm居世界領先地位。
數值模擬技術的發展趨勢可概括如下:
進一步提高模擬計算的精度和速度。重點突破回彈精確預測;發展快速有限元模擬技術,實現“當天工程”、甚至“2小時工程”;同時加強基礎研究,解決複雜變形路徑等基礎性問題。
(2)降低軟體對人員專業素質的要求。目前市場軟體功能強大,主要面向分析師,買了先進軟體系統,不一定能獲得好的模擬結果。面向中小企業,推廣更加困難。
(3)降低軟體對硬體平台的要求。目前,幾乎著名的衝壓模擬軟體都已完成向微機版的轉化。
(4)加強初始化設計環節的研究。初始化設計環節(初始方案),作為計算分析的起點和修改的基礎,至今仍需要靠有經驗的人員完成。迫切需要發展知識庫工程(kbe),將專家系統(es)、人工智慧技術(ai)與有限元模擬軟體相結合,實現智慧型化初始工作,減少對工藝專家的依賴。
(5)加強基礎試驗。材料性能本構關係、摩擦狀態、缺陷判據等數據來自試驗,其真實性、準確性是限制模擬分析達到可靠精度的重要因素。
(6)進一步向產品衝壓製造系統擴展,實現製造全過程、全生命期的綜合最佳化。目前,成形過程分析,仍重在解決成“形”問題。未來,將同時向改“性”發展,實現變形方式、成形過程及成形後性能的綜合最佳化。
(7)普及cae技術勢在必行。cad技術經過5-10年的大力普及,基本解決了手工繪圖問題。未來5-10年,cae技術的普及將勢在必行。
中小機械製造企業70多萬家,衝壓、模具企業為數甚大,以高新技術改造傳統技術的任務十分艱巨,結合產業調整,統籌規劃,需要提上日程。
套用廣泛
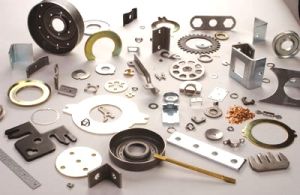
衝壓件與鑄件、鍛件相比,具有薄、勻、輕、強的特點。衝壓可制出其他方法難於製造的帶有加強筋、肋、起伏或翻邊的工件,以提高其剛性。由於採用精密模具,工件精度可達微米級,且重複精度高、規格一致,可以衝壓出孔窩、凸台等。
冷衝壓件一般不再經切削加工,或僅需要少量的切削加工。熱衝壓件精度和表面狀態低於冷衝壓件,但仍優於鑄件、鍛件,切削加工量少。
衝壓是高效的生產方法,採用複合模,尤其是多工位級進模,可在一台壓力機上完成多道衝壓工序,實現由帶料開卷、矯平、沖裁到成形、精整的全自動生產。生產效率高,勞動條件好,生產成本低,一般每分鐘可生產數百件。
工藝種類
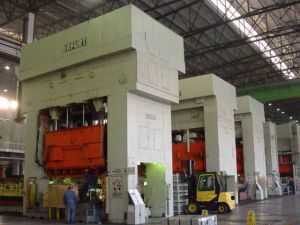
衝壓用板料的表面和內在性能對衝壓成品的質量影響很大,要求衝壓材料厚度精確、均勻;表面光潔,無斑、無疤、無擦傷、無表面裂紋等;屈服強度均勻,無明顯方向性;均勻延伸率高;屈強比低;加工硬化性低。
在實際生產中,常用與衝壓過程近似的工藝性試驗,如拉深性能試驗、脹形性能試驗等檢驗材料的衝壓性能,以保證成品質量和高的合格率。
模具的精度和結構直接影響衝壓件的成形和精度。模具製造成本和壽命則是影響衝壓件成本和質量的重要因素。模具設計和製造需要較多的時間,這就延長了新衝壓件的生產準備時間。
模座、模架、導向件的標準化和發展簡易模具(供小批量生產)、複合模、多工位級進模(供大量生產),以及研製快速換模裝置,可減少衝壓生產準備工作量和縮短準備時間,能使適用於減少衝壓生產準備工作量和縮短準備時間,能使適用於大批量生產的先進衝壓技術合理地套用於小批量多品種生產。
衝壓設備除了厚板用水壓機成形外,一般都採用機械壓力機。以現代高速多工位機械壓力機為中心,配置開卷、矯平、成品收集、輸送等機械以及模具庫和快速換模裝置,並利用電腦程式控制,可組成高生產率的自動衝壓生產線。
在每分鐘生產數十、數百件衝壓件的情況下,在短暫時間內完成送料、衝壓、出件、排廢料等工序,常常發生人身、設備和質量事故。因此,衝壓中的安全生產是一個非常重要的問題。
特點
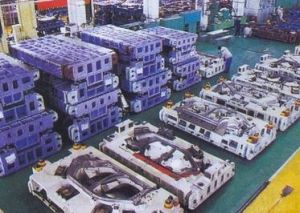
(2)操作工藝方便,不需要操作者有較高水平的技藝。
(3)衝壓出的零件一般不需要再進行機械加工,具有較高的尺寸精度。
(4)衝壓件有較好的互換性。衝壓加工穩定性較好,同一批衝壓件.可相互交換使用,不影響裝配和產品性能。
(5)由於衝壓件用板材作材料,它的表面質量較好,為後續表面處理工序(如電鍍、噴漆)提供了方便條件。
(6)衝壓加工能獲得強度高、剛度大而重量輕的零件。
(7)用模具批量生產的衝壓件成本低廉。
(8)衝壓能製造出其它金屬加工方法難加工出的形狀複雜的零件。
衝壓工序
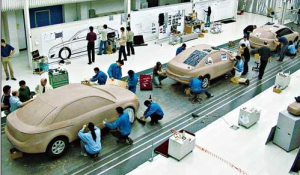
沖裁:使板料實現分離的衝壓工序(包括沖孔、落料、修邊、剖切等)。
彎曲:將板料沿彎曲線彎成一定的角度和形狀的衝壓工序。
拉深:將平面板料變成各種開口空心零件,或把空心件的形狀、尺寸作進一步改變的衝壓工序。
局部成形:用各種不同性質的局部變形來改變毛坯或衝壓件形狀的衝壓工序(包括翻邊、脹形、校平和整形工序等)。
尋求突破
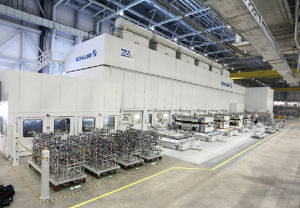
機械化、自動化程度低
美國680條衝壓線中有70%為多工位壓力機,日本國內250條生產線有32%為多工位壓力機,而這種代表當今國際水平的大型多工位壓力機在我國的套用卻為數不多;中小企業設備普遍較落後,耗能耗材高,環境污染嚴重;封頭成形設備簡陋,手工操作比重大;精沖機價格昂貴,是普通壓力機的5~10倍,多數企業無力投資阻礙了精沖技術在中國的推廣套用;液壓成形,尤其是內高壓成形,設備投資大,中國難以起步。
加速技術改造
要改變當前大部分還是手工上下料的落後局面,結合具體情況,採取新工藝,提高機械化、自動化程度。汽車車身覆蓋件衝壓應向單機連線自動化、機器人衝壓生產線,特別是大型多工位壓力機方向發展。爭取加大投資力度,加速衝壓生產線的技術改造,使儘早達到當今國際水平。而隨著微電子技術和通訊技術的發展使板材成形裝備自動化、柔性化有了技術基礎。應加速發展數位化柔性成形技術、液壓成形技術、高精度複合化成形技術以及適應新一代輕量化車身結構的型材彎曲成形技術及相關設備。同時改造國內舊設備,使其發揮新的生產能力。
生產集中度低
許多汽車集團大而全,形成封閉內部配套,導致各企業的衝壓件種類多,生產集中度低,規模小,易造成低水平的重複建設,難以滿足專業化分工生產,市場競爭力弱;機車衝壓行業面臨激烈的市場競爭,處於“優而不勝,劣而不汰”的狀態;封頭製造企業小而散,集中度僅39.2%。
走專業化道路
迅速改變“大而全”、“散亂差”的格局,儘快從汽車集團中把衝壓零部件分離出來,按衝壓件的大、中、小分門別類,成立幾個大型的衝壓零部件製造供應中心及幾十個小而專的零部件工廠。通過專業化道路,才能把衝壓零部件做大做強,成為國際上有競爭實力的衝壓零部件供應商。
衝壓板材自給率不足,品種規格不配套
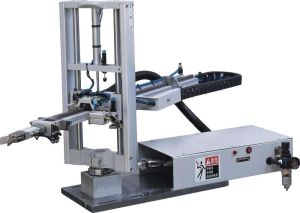
用材應與行業協調發展
汽車用鋼板的品種應更趨向合理,朝著高強、高耐蝕和各種規格的薄鋼板方向發展,並改善衝壓性能。鋁、鎂合金已成為汽車輕量化的理性材料,擴大套用已勢在心行。
科技成果轉化慢先進工藝推廣慢
在中國,許多衝壓新技術起步並不晚,有些還達到了國際先進水平,但常常很難形成生產力。先進衝壓工藝套用不多,有的僅處於試用階段,吸收、轉化、推廣速度慢。技術開發費用投入少,導致企業對先進技術的掌握套用慢,開發創新能力不足,中小企業在這方面的差距更甚。國內企業大部分仍採用傳統衝壓技術,對下一代輕量化汽車結構和用材所需的成形技術缺少研究與技術儲備。
走產、學、研聯合之路
中國與歐、美、日等相比,存在的最大的差距就是還沒有一個產、學研聯合體,科研難以做大,成果不能儘快轉化為生產力。所以應圍繞大型開發和產業化項目,以高校和科研單位為技術支持,企業為套用基地,形成產品、設備、材料、技術的企業聯合實體,形成既能開發創新,又能迅速產業化的良性循環。
大、精模具依賴進口
當前,衝壓模具的材料、設計、製作均滿足不了國內汽車發展的需要,而且標準化程度尚低,大約為40%~45%,而國際上一般在70%左右。
提升信息化、標準化水平
必須用信息化技術改造模具企業,發展重點在於大力推廣CAD/CAM/CAE一體化技術,特別是成形過程的計算機模擬分析和最佳化技術(CAE)。加速中國模具標準化進程,提高精度和互換率。力爭2005年模具標準件使用覆蓋率達到60%,2010年達到70%以上基本滿足市場需求。
專業人才缺乏
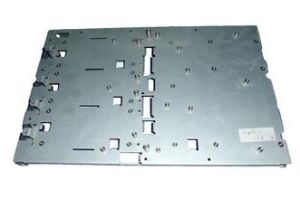
提高行業人員素質
這是一項迫在眉睫的任務,又是一項長期而系統的任務。振興中國衝壓行業需要大批高水平的科技人才,大批熟悉國外市場、具有現代管理知識和能力的企業家,大批掌握先進技術、工藝的高級技能人才。要捨得花大力氣,有計畫、分層次地培養。
衝壓加工也存在著一些問題和缺點。主要表現在衝壓加工時產生的噪音和振動兩種公害,而且操作者的安全事故時有發生。不過,這些問題並不完全是由於衝壓加工工藝及模具本身帶來的,而主要是由於傳統的衝壓設備及落後的手工操作造成的。隨著科學技術的進步,特別是計算機技術的發展,隨著機電一體化技術的進步,這些問題一定會儘快二完善的得到解決。衝壓成形用戶市場的迅猛發展為衝壓行業帶來了全新的發展機遇,雖然在衝壓業發展的道路上還存在著各種各樣的阻力與障礙,但我們始終相信,這些都阻擋不了衝壓行業前進的步伐。
發展趨勢
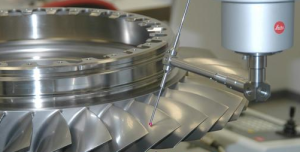
(2)衝壓成形技術將更加科學化、數位化、可控化。科學化主要體現在對成形過程、產品質量、成本、效益的預測和可控程度。成形過程的數值模擬技術將在實用化方面取得很大發展,並與數位化製造系統很好地集成。人工智慧技術、智慧型化控制將從簡單形狀零件成形發展到覆蓋件等複雜形狀零件成形,從而真正進入實用階段。
(3)注重產品製造全過程,最大程度地實現多目標全局綜合最佳化。最佳化將從傳統的單一成形環節向產品製造全過程及全生命期的系統整體發展。
(4)對產品可製造性和成形工藝的快速分析與評估能力將有大的發展。以便從產品初步設計甚至構思時起,就能針對零件的可成形性及所需性能的保證度,作出快速分析評估。
(5)衝壓技術將具有更大的靈活性或柔性,以適應未來小指量多品種混流生產模式及市場多樣化、個性化需求的發展趨勢,加強企業對市場變化的快速回響能力。
(6)重視複合化成形技術的發展。以複合工藝為基礎的先進成形技術不僅正在從製造毛坯向直接製造零件方向發展,也正在從製造單個零件向直接製造結構整體的方向發展。
加入wto以後,中國的汽車工業、航空航天工業等支柱產業必將有大的發展。我國的衝壓行業既充滿發展的機遇,又面臨進一步以高新技術改造傳統技術的嚴峻挑戰。國民經濟和國防建設事業將向衝壓成形技術的發展提出更多更新更高的要求。我國的板料加工領域必須加強力量的聯合,加強技術的綜合與集成,加快傳統技術從經驗向科學化轉化的進程。加速人才培養,提升技術創新能力,提高衝壓技術隊伍的整體素質和生產企業的競爭力。