分級淬火
減少變形的理想理念,為了將變形控制在最小範圍內,ECM公司開發了一種創新的分級淬火工藝,這種工藝利用了設備的靈活性的優勢。通過確保淬火工藝和鋼材的連續冷卻曲線儘可能地接近就可以得到更好的質量。這已經通過試驗在零件上進行了確認。在氣淬過程中,氣體的壓力和攪拌速率這兩個可變參數用來控制淬火強度。這種靈活可變性昭示著在控制變形方面一些有意義的前景:“採用可變強度的分級淬火可以讓易變形零件的變形控制到最小”ECM研發中心的經理Rossignol先生解釋說。這已經過自從2006年春季以來和GM公司一系列的試驗的論證。
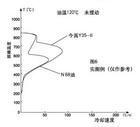
結論
ECM比較了分級淬火和強度不變的直接淬火之間的區別。對於傳動齒輪,測到的齒向變形的平均值從13微米減
少到4微米,控制在了變形要求的範圍之內。對於傳動齒環,外徑的變形減小為原來的四分之一。而且,在上兩種試驗中,在裝爐料的各個部位檢測到的結果均是高度一致的。正如Rossignol先生所說的“同時解決了變形問題和一致性問題。”
我們是如何解釋這種改進的呢?分級淬火使得工藝強度在變形及容易產生的臨界階段得到調整以及控制。就整體來看,分級淬火工藝類似於一個三階段的冷卻淬火過程。“遵循著鋼的連續冷卻轉變曲線(CCT),這一點對冶金學家來說是眾所周知的。”Rossignol先生解釋說。消除殘餘應力為了保證最大限度的均勻一致性,爐料的溫度在熱處理結束之後開始降低,也即第一個冷卻階段,在最初的時候冷卻過程相對比較緩和,採用適中的氣體壓力和攪拌風速。然後冷卻強度逐步增加,以便儘可能地避免珠光體以及貝氏體相的形成。
然後,第二階段,非常關鍵的一步,在馬氏體轉變階段之前,淬火冷卻有一個幾秒鐘的停頓。氣體的攪拌延緩,從而增加了零部件之間的熱傳導,這將會防止零件表面和心部之間存在一個大的溫差。而這種溫差實際上是殘餘應力的誘因,會在隨後的馬氏體轉變過程中產生變形。
最後,也即第三步,採用最大的淬火速度。馬氏體轉變階段的冷卻速率越快,得到的鋼的機械性能也就越好。分級淬火工藝通過預見性的控制及減少變形最佳化了整個熱處理工藝過程,從而減少了生產總成本:更少的拒收,更少的矯直操作,更少的變形返修。“開發分級淬火工藝是一種質量確保程式”Rossignol先生解釋說。能不能將分級淬火作為標準操作程式呢?專家回答:“這取決於零件的形狀”。一些不容易變形以及對變形要求不高的零件不需要採用分級淬火。而對另外一些零件,分級淬火工藝打開了一個新的研究前景。ECM有一些專用的方法和工具,例如由ECM公司和法國液化空氣公司聯合開發的QuenchAL冷卻模擬軟體,用來幫助客戶建立理想的工藝數據模型。