產業格局
1.SMT/MES產業三足鼎立中國SMT/MES產業主要集中在東部沿海地區,其中廣東、福建、浙江、上海、江蘇、山東、天津、北京以及遼寧等省市SMT/MES的總量占全國80%以上。按地區分,以珠三角及周邊地區最強,長三角地區次之,環渤海地區第三。環渤海地區SMT/MES總量雖與珠三角和長三角相比有較大差距,但增長潛力巨大,發展勢頭更強。國家有關部門公布,位於天津的濱海新區繼深圳、上海浦東之後將成為我國經濟成長的第三極。不久的將來,我國SMT/MES產業必然形成珠三角、長三角、環渤海地區三足鼎立之勢。 中國SMT/MES產業之所以出現如此大好形勢,主要是中國政府有關部門高度重視電子信息產品製造業的發展,制定了良好的發展政策、引進政策。世界電子信息產品製造業發達的國家和地區如美、日、韓、歐洲和我國台灣地區,把電子製造業往中國內地轉移是其重要因素。
2.中國SMT產業仍主要集中在珠江三角洲地區和長江三角洲地區,這兩個地區產業銷售收入占到了整體產業規模的90%以上,其中僅珠江三角洲地區就占到了整體比重的67.5%。另外環渤海地區SMT產業的銷售額也達到了3.1億元,占整體產業比重的7.6%。
3.同時我們預計,未來5年內中國SMT產業還仍將主要集中在長江三角洲地區、珠江三角洲地區和環渤海地區。不過,長江三角洲地區在中國SMT產業中所占比重將從2007年起開始快速攀升,2009年達到43.9%。而珠江三角洲地區比重雖然下降到47.O%,但仍占據首要位置。另外,環渤海地區的SMT產業也有較快的發展。長江三角洲地區SMT產業的快速增長主要來自於全球SMT產業的轉移,尤其是貼片機生產的轉移。從歷史原因來看,長江三角洲地區發展設備製造業的基礎相對雄厚。同時長江三角洲地區筆記本、手機等中高端電子整機產品製造業比較發達,另外再加上長江三角洲地區獨特的地理位置優勢,因此在2007年的全球SMT產業的大轉移過程中,長江三角洲地區將承接相當大部分的比例。不過,對珠江三角洲地區而言,由於在過去幾年的發展中,其SMT產業已經形成了較為完整的產業鏈和產業配套環境,因此珠江三角洲地區在承接產業轉移方面也具有比較明顯的優勢。
4.從產業自身的發展周期來看,雖然中國的SMT產業尚處於發展初期,但是已經呈現出了蓬勃生機。同時,SMT產業又是一個重要的基礎性產業,對於推動中國的電子信息產業製造業結構調整和產業升級有著重要意義。推動中國SMT產業快速健康發展需要產業上下游各個環節的共同協作。
5.對政府而言,我們建議做好兩件事情。一是加大對SMT產業的扶持力度,尤其是加強對基礎材料和精密儀器等領域基礎研究的投入。二是政府作為重要的市場監管部門,要加強智慧財產權保護力度,積極引導制定中國的SMT產業標準,並加以積極推廣和執行。
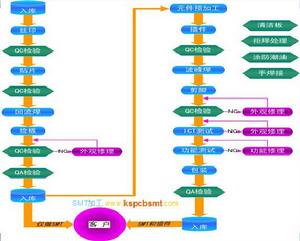
6.對企業而言,我們也建議做好五件事情。一是轉變觀念,充分認識生產工藝對SMT設備研製的重要性。只有完全熟悉實際生產的工藝流程,了解實際生產中的工藝技術參數調整變化,才能真正設計出符合實際生產要求的SMT設備。二是順應無鉛化趨勢,突破重點技術並實現關鍵設備產品系列化。三是加強銷售服務,研製適合中國企業需要的新機型。四是藉助培訓認證,形成設備市場推廣新模式。根據國家勞動社會保障部和信息產業部的要求,從事表面貼裝行業的從業人員在2006年前必須持證上崗,這也給國內企業藉助專業培訓和認證方式來推廣其SMT設備產品留下的發展空間。五是充分重視自我人才的培養,實現技術創新和健康發展。
物料損耗
1,吸嘴變形,堵塞,破損、真空氣壓不足,漏氣,造成吸料不起 ,取料不正,識別通不過而拋料。解決方法:要求技術員必須每天點檢設備,測試 NOZZLE中心,清洗吸嘴,按計畫定期保養設備。
2,彈簧張力不夠、吸嘴與HOLD不協調、上下不順造成取料不良;解決方法:按計畫定期保養設備,檢查和更換易損配件。
3,HOLD/SHAFT或PISTON變形、吸嘴彎曲、吸嘴磨損變短造成取料不良;解決方法:按計畫定期保養設備,檢查和更換易損配件。
4,取料不在料的中心位置,取料高度不正確(一般以碰到零件後下壓0.05MM為準)而造成偏位,取料不正,有偏移,識別時跟對應的數據參數不符而被識別系統當做無效料拋棄;解決方法:按計畫定期保養設備,檢查和更換易損配件,校正機器原點。
5,真空閥、真空過濾芯髒、有異物堵塞真空氣管通道不順暢,吸著時瞬間真空不夠設備的運行速度造成取料不良;解決方法:要求技術員必須每天清洗吸嘴,按計畫定期保養設備。
6,機器定位不水平,震動大、機器與FEEDER共振造成取料不良;解決方法:按計畫定期保養設備,檢查設備水平固定支撐螺母。
7,絲桿、軸承磨損鬆動造成運行時震動、行程改變而取料不良;解決方法:嚴禁用風槍吹機器內部,防止灰塵、雜物、元件粘 附在絲桿上。按計畫定期保養設備,檢查和更換易損配件。
8,馬達軸承磨損、讀碼器和放大器老化造成機器原點改變、運行數據不精確而取料不良;解決方法:按計畫定期保養設備,檢查和更換易損配件,校正機器原點。
9,視覺、雷射鏡頭、吸嘴反光紙不清潔,有雜物干擾相機識別造成處理不良;解決方法:要求技術員必須每天點檢設備,測試NOZZLE中心,清洗吸嘴,按計畫定期保養設備。
10,識別光源選擇不當、燈管老化發光強度、灰度不夠造成處理不良;解決方法:按計畫定期保養設備,測試相機的輝度和燈管的亮度,檢查和更換易損配件。
11,反光稜鏡老化積炭、磨損刮花造成處理不良;解決方法:按計畫定期保養設備,檢查和更換易損配件。
12,氣壓不足,真空有泄漏造成氣壓不足而取料不起或取起之後在去貼片的途中掉落;解決方法:按計畫定期保養設備,檢查和更換易損配件。
13,供料器變形互相擠壓造成送料位置改變而取料不良;解決方法:按規定要求操作。
14,供料器壓蓋變形、彈簧張力不夠造成料帶沒有卡在供料器的棘齒輪上、不捲帶拋料,檢查和更換易損配件。
15,相機鬆動、老化造成識別不良拋料;解決方法:按計畫定期保養設備,檢查和更換易損配件。
16,供料器棘齒輪、驅動爪、定位爪磨損、電氣不良、送料馬達不良 造成供料器進料不暢取料不到或不良而拋料;檢查和更換易損配
17,機器供料平台磨損造成FEEDER安裝後鬆動而取料不良;解決方法:按計畫定期保養設備,檢查和更換易損配件。
18,其它某些特殊的需要減速貼裝的零件沒有減速而進行貼裝,也會造成吸著率的地下。對策:feeder供料減速,X/Y/H軸減速或調整各個動作配合時序控制。
簡介
複雜技術
只需重視一下如今在各地舉行的五花八門的專業會議的主題,咱們就不難知道電子產物中選用了哪些最新技能。CSP、0201無源元件、無鉛焊接和光電子,可以說是近來許多公司在PCB製造及SMT加工上值得炫耀的先進技能。比如說,怎么處置在CSP和0201拼裝中常見的超小開孔(250um)難題,就是焊膏印刷曾經從未有過的根本物理難題。板級光電子拼裝,作為通訊和網路技能中發展起來的一大範疇,其工藝非常精密。典型封裝貴重而易損壞,特別是在器材引線成形之後。這些雜亂技能的描繪輔導準則也與通常SMT工藝有很大區別,因為在保證拼裝生產率和產物牢靠性方面,板描繪扮演著更為重要的角色;例如,對CSP焊接互連來說,只是經過改動板鍵合盤尺度,就能有明顯進步的可靠性。
CSP使用
如今大家常見的一種關鍵技能是CSP。CSP技能的魅力在於它具有許多長處,如減小封裝尺度、添加針數、功用∕功能增強以及封裝的可返工性等。CSP的高效長處體如今:用於板級拼裝時,可以跨出細距離(細至0.075mm)周邊封裝的邊界,進入較大距離(1,0.8,0.75,0.5,0.4mm)區域陣列布局。
已有許多CSP器材在消費類電信範疇使用多年了,大家遍及認為它們是SRAM與DRAM、中等針數ASIC、快閃記憶體和微處置器範疇的低本錢解決方案。CSP可以有四種根本特徵方式:即剛性基、柔性基、引線結構基和晶片級規劃。CSP技能可以替代SOIC和QFP器材而成為主流組件技能。
CSP拼裝工藝有一個難題,就是焊接互連的鍵合盤很小。通常0.5mm距離CSP的鍵合盤尺度為0.250~0.275mm。如此小的尺度,經過面積比為0.6乃至更低的開口印刷焊膏是很艱難的。不過,選用精心描繪的工藝,可成功地進行印刷。而毛病的發作通常是因為模板開口阻塞致使的焊料缺乏。板級牢靠性首要取決於封裝類型,而CSP器材平均能飽嘗-40~125℃的熱周期800~1200次,可以無需下填充。但是,若是選用下填充資料,大多數CSP的熱牢靠功能添加300%。CSP器材毛病通常與焊料疲憊開裂有關。
無源元件的前進
另一大新式範疇是0201無源元件技能,因為減小板尺度的市場需要,大家對0201元件非常重視。自從1999年中期0201元件推出,蜂窩電話製作商就把它們與CSP一同拼裝到電話中,印板尺度由此至少減小一半。處置這類封裝適當費事,要削減工藝後缺點(如橋接和直立)的呈現,焊盤尺度最最佳化和元件距離是要害。只需描繪合理,這些封裝可以緊貼著放置,距離可小至150mm。
另外,0201器材能貼放到BGA和較大的CSP下方。有0.8mm距離的14mm CSP組件下面的0201的橫截面圖。因為這些小型分立元件的尺度很小,拼裝設備廠家已方案開發更新的體系與0201相兼容。
到2009年,實際量產的手機已經採用01005(公制,英制為0402)的製程。到2013年,03015(公制)及以下的零件已經進入貼裝實驗階段。
通孔拼裝仍有生命力
光電子封裝正廣泛使用於高速數據傳送盛行的電信和網路範疇。通常板級光電子器材是“蝴蝶形”模組。這些器材的典型引線從封裝四邊伸出並水平擴大。其拼裝辦法與通孔元器材一樣,通常選用手藝工藝—-引線經引線成型壓力東西處置並刺進印板通路孔貫穿基板。
處置這類器材的首要難題是,在引線成型工藝時刻可以發作的引線損壞。因為這類封裝都很貴重,有必要當心處置,防止引線被成型操作損壞或引線-器材體銜接口處模組封裝開裂。歸根到底,把光電子元器材結合到規範SMT產物中的最佳解決方案是選用主動設備,這樣從盤中取出元器材,放在引線成型東西上,之後再把帶引線的器材從成型機上取出,最終把模組放在PCB上。鑒於這種挑選需求適當大本錢的設備出資,大多數公司還會持續挑選手藝拼裝工藝。
大尺度印板(20×24″)在許多製作範疇也很遍及。比如機頂盒和路由/開關印板一類的產物都相當雜亂,包含了本文評論的各種技能的混合,舉例來說,在這一類PCB上,常常可以見到大至40mm2的大型陶瓷柵陣列(CCGA)和BGA器材。
這類器材的兩個首要難題是大型散熱和熱致使的翹曲效應。這些元器材能起大散熱片的效果,致使封裝外表下非均勻的加熱,因為爐子的熱操控和加熱曲線操控,可以致使器材中間鄰近不潮濕的焊接銜接。在處置時刻由熱致使的器材和印板的翹曲,會致使如部件與施加到PCB上的焊膏別離這樣的“不潮濕表象”。因而,當測繪這些印板的加熱曲線時有必要當心,以保證BGA/CCGA的外表和整個印板的外表得到均勻的加熱。
PCB板翹曲要素
為防止印PCB過度下彎,在再流爐里適當地支撐PCB是很重要的。PCB翹曲是電路拼裝中有必要注重調查的要素,並應嚴厲進行特微描繪。再流周期中由熱致使的BGA或PCB的翹曲會致使焊料空穴,並把很多殘留應力留在焊料銜接上,形成早期毛病。選用莫爾條紋投影印象體系很簡單描繪這類翹曲,該體系可以線上或脫機操作,用於描繪預處置封裝和PCB翹曲的特微。脫機體系經過爐內設定的為器材和PCB製作的根據時刻/溫度座標的翹曲圖形,也能模仿再流環境。
無鉛焊接
無鉛焊接是另一項新技能,許多公司現已開端選用。這項技能始於歐盟和日本工業界,起先是為了在進行PCB拼裝時從焊材中撤銷鉛成份。完成這一技能的日期一直在改變,起先提出在2004年完成,後來提出的日期是在2006年完成。不過,許多公司現正爭取在2004年具有這項技能,有些公司如今現已供給了無鉛產物。
如今市場上已有許多無鉛焊料合金,而美國和歐洲最通用的一種合金成份是95.6Sn∕3.7Ag∕0.7Cu。處置這些焊料合金與處置規範Sn/Pb焊料相比較並無多大不同。其間的列印和貼裝工藝是一樣的,首要不同在於再流工藝,也就是說,關於大多數無鉛焊料有必要選用較高的液相溫度。Sn∕Ag∕Cu合金通常需求峰值溫度比Sn/Pb焊料高大概30℃。別的,開始研討現已標明,其再流工藝視窗比規範Sn/Pb合金要嚴厲得多。
關於小型無源元件來說,削減外表能相同也可以削減直立和橋接缺點的數量,特別是關於0402和0201尺度的封裝。總歸,無鉛拼裝的牢靠性闡明,它徹底比得上Sn/Pb焊料,不過高溫環境在外,例如在汽車使用中操作溫度可以會超越150℃。
倒裝片
當把當時先進技能集成到規範SMT組件中時,技能遇到的艱難最大。在一級封裝組件使用中,倒裝片廣泛用於BGA和CSP,雖然BGA和CSP現已選用了引線-結構技能。在板級拼裝中,選用倒裝片可以帶來許多長處,包含組件尺度減小、功能進步和本錢降低。
令人遺憾的是,選用倒裝片技能需求製作商添加出資,以使機器晉級,添加專用設備用於倒裝片工藝。這些設備包含可以滿意倒裝片的較高精度需求的貼裝體系和下填充滴塗體系。此外還包含X射線和聲像體系,用於進行再流焊後焊接檢測和下填充後空穴剖析。
焊盤描繪,包含形狀、巨細和掩膜限制,關於可製作性和可測驗性(DFM/T)以及滿意本錢方面的需求都是至關重要的。
PCB板上倒裝片(FCOB)首要用於以小型化為要害的產物中,如藍牙模組組件或醫療器械使用。一個藍牙模組印板,其間以與0201無源元件相同的封裝集成了倒裝片技能。拼裝了倒裝片和0201器材的相同的高速貼裝和處置也可環繞封裝的附近放置焊料球。這可以說是在規範SMT拼裝線上與施行先進技能的一個上佳比如。
特點
組裝密度高、電子產品體積小、重量輕,貼片元件的體積和重量只有傳統插裝元件的1/10左右,一般採用SMT之後,電子產品體積縮小40%~60%,重量減輕60%~80%。
可靠性高、抗震能力強。焊點缺陷率低。
高頻特性好。減少了電磁和射頻干擾。
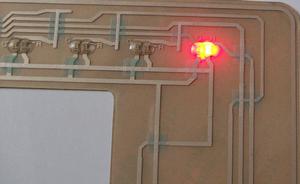
易於實現自動化,提高生產效率。降低成本達 30%~50%。節省材料、能源、設備、人力、時間等。
組成
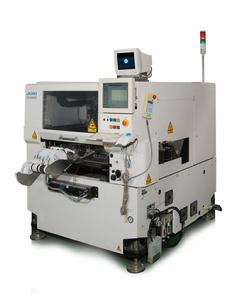
總的來說,SMT包括表面貼裝技術、表面貼裝設備、表面貼裝元器件、SMT管理。
前景
進入21世紀以來,中國電子信息產品製造業每年都以20%以上的速度高速增長,規模從2004年起已連續三年居世界第二位。在中國電子信息產業快速發展的推動下,中國表面貼裝技術(SMT)和生產線也得到了迅猛的發展,表面貼裝生產線的關鍵設備——自動貼片機在中國的保有量已位居世界前列。
中國是最重要的市場
到2006年底中國約有近2萬條SMT生產線,擁有SMT貼片機約近5萬台,其中90%是2001年以後購買的。至今,中國自主開發的SMT貼片機還處於試用期,市場上用的SMT貼片機幾乎全部是從國外進口的。從2001年至2006年的六年中,中國自動貼片機市場以年平均27.2%的速度增長。到2006年共進口自動貼片機10351台,進口金額達到17億美元,中國的SMT貼片機市場已占全球市場份額的40%左右。單台自動貼片機的平均價格已達到16.4萬美元。2006年中國進口的10351台自動貼片機主要來自日本,占77.9%,但德國的自動貼片機單台平均價格最高,單台均價達31.1萬美元。2006年中國進口的自動貼片機在廣東省占54.4%,列各地區自動貼片機進口的首位,其次是江蘇、上海和北京。
需求將保持平穩增長
根據信息產業部的最新統計,2006年中國電子信息產業實現銷售收入4.75萬億元,增長23.7%。2007年中國電子信息產業發展的巨觀目標是實現銷售收入5.8萬億元,同比增長23%。SMT貼片機在中國的主要市場——手機、筆記本電腦和數位相機等IT產品發展迅猛。在中國,手機用戶2006年達到4.61億戶,每百人擁有35.3台手機。按照電子信息產業“十一五”發展規劃制定的目標,到2010年手機用戶將達到6億戶,每百人將擁有45台手機。中國手機的產量一直保持著迅速增長,2006年手機產量達到4.8億台,比2005年增長58.2%。筆記本電腦在微型計算機中的比重已超過50%,並且比重逐年在增長。中國筆記本電腦的產量年均增長率在60%以上,2006年產量為5912萬台,同比增長29.5%。2006年中國數位相機產量為6695.1萬台,比2005年增長21.2%。綜上分析,2007年中國自動貼片機的市場在中國電子信息產業快速發展和手機、筆記本電腦和數位相機迅猛發展的推動下,市場需求將繼續保持平穩增長的勢態。同時由於國產的自動貼片機今年還不會進入產業化,所以2007年中國的自動貼片機市場仍將依靠進口。
工藝構成
印刷(紅膠/錫膏)--> 檢測(可選AOI全自動或者目視檢測)-->貼裝(先貼小器件後貼大器件:分高速貼片及積體電路貼裝)-->檢測(可選AOI 光學/目視檢測)-->焊接(採用熱風回流焊進行焊接)--> 檢測(可分AOI 光學檢測外觀及功能性測試檢測)--> 維修(使用工具:焊台及熱風拆焊台等)--> 分板(手工或者分板機進行切板)
工藝流程簡化為:印刷-------貼片-------焊接-------檢修(每道工藝中均可加入檢測環節以控制質量)
錫膏印刷
其作用是將錫膏呈45度角用刮刀漏印到PCB的焊盤上,為元器件的焊接做準備。所用設備為印刷機(錫膏印刷機),位於SMT生產線的最前端。
零件貼裝
其作用是將表面組裝元器件準確安裝到PCB的固定位置上。所用設備為貼片機,位於SMT生產線中印刷機的後面,一般為高速機和泛用機按照生產需求搭配使用。
回流焊接
其作用是將焊膏融化,使表面組裝元器件與PCB牢固焊接在一起。所用設備為回流焊爐,位於SMT生產線中貼片機的後面,對於溫度要求相當嚴格,需要實時進行溫度量測,所量測的溫度以profile的形式體現。
AOI光學檢測
其作用是對焊接好的PCB進行焊接質量的檢測。所使用到的設備為自動光學檢測機(AOI),位置根據檢測的需要,可以配置在生產線合適的地方。有些在回流焊接前,有的在回流焊接後。
維修
其作用是對檢測出現故障的PCB進行返修。所用工具為烙鐵、返修工作站等。配置在AOI光學檢測後。
分板
其作用對多連板PCBA進行切分,使之分開成單獨個體,一般採用V-cut與 機器切割方式。
基礎知識
焊錫膏是將焊料粉末與具有助焊功能的糊狀焊劑混合而成的一種漿料,通常焊料粉末占90%左右,其餘是化學成分。
我們把能隨意改變形態或任意分割的物體稱為流體,研究流體受外力而引起形變與流動行為規律和特徵的科學稱為流變學。但在工程中則用黏度這一概念來表征流體黏度的大小。
焊錫膏的流變行為
焊錫膏中混有一定量的觸變劑,具有假塑性流體性質。焊錫膏在印刷時,受到刮刀的推力作用,其黏度下降,當達到模板視窗時,黏度達到最低,故能順利通過視窗沉降到PCB的焊盤上,隨著外力的停止,焊錫膏黏度又迅速回升,這樣就不會出現印刷圖形的塌落和漫流,得到良好的印刷效果。
影響焊錫膏黏度的因素:焊料粉末含量;焊料粉末粒度;溫度;剪下速率。
1、焊料粉末含量
焊錫膏中焊料粉末的增加引起黏度的增加。
2、焊料粉末粒度
焊料粉末粒度增大,黏度降低。
3、溫度
溫度升高,黏度下降。印刷的最佳環境溫度為23±3度。
回流焊
回流焊或浸焊等方法加以焊接組裝的電路裝連技術。
概述
回流焊又稱“再流焊”或“再流焊機”或“回流爐”(Reflow Oven),它是通過提供一種加熱環境,使焊錫膏受熱融化從而讓表面貼裝元器件和PCB焊盤通過焊錫膏合金可靠地結合在一起的設備。根據技術的發展分為:氣相回流焊、紅外回流焊、遠紅外回流焊、紅外加熱風回流焊和全熱風回流焊。另外根據焊接特殊的需要,含有充氮的回流焊爐。比較流行和實用的大多是遠紅外回流焊、紅外加熱風回流焊和全熱風回流焊。
紅外再流焊
(1)第一代-熱板式再流焊爐
(2)第二代-紅外再流焊爐
熱能中有 80%的能量是以電磁波的形式――紅外線向外發射的。其波長在可見光之上限0.7~0.8um 到1mm 之間,0.72~1.5um 為近紅外;1.5~5.6um 為中紅外;5.6~1000um 為遠紅外,微波則在遠紅外之上。
升溫的機理:當紅外波長的振動頻率與被輻射物體分子間的振動頻率一致時,就會產生共振,分子的激烈振動意味著物體的升溫。波長為1~8um。
![SMT[表面組裝技術]](/img/5/8b8/nBnauM3X4gjM2gTN4czN2cjM2UTM1QDN5MjM5ADMwAjMwUzL3czL4gzLt92YucmbvRWdo5Cd0FmLyE2LvoDc0RHa.jpg)
第四區溫度設定最高,它可以導致焊區溫度快速上升,提高泣濕力。優點:使助焊劑以及有機酸和鹵化物迅速水利化從而提高潤濕能力;紅外加熱的輻射波長與吸收波長相近似,因此基板升溫快、溫差小;溫度曲線控制方便,彈性好;紅外加熱器效率高,成本低。
缺點:穿透性差,有陰影效應――熱不均勻。
對策:在再流焊中增加了熱風循環。
(3)第三代-紅外熱風式再流焊。
對流傳熱的快慢取決於風速,但過大的風速會造成元件移位並助長焊點的氧化,風速控制在1.0~1.8m/s。熱風的產生有兩種形式:軸向風扇產生(易形成層流,其運動造成各溫區分界不清)和切向風扇(風扇安裝在加熱器外側,產生面板渦流而使得各溫區可精確控制)。
基本結構與溫度曲線的調整:
1. 加熱器:管式加熱器、板式加熱器鋁板或不鏽鋼板;
2. 傳送系統:耐熱四氟乙烯玻璃纖維布;
3. 運行平穩、導熱性好,但不能連線,適用於小型熱板型不鏽鋼網,適用於雙面PCB,也不能連線;鏈條導軌,可實現連線生產。
4. 強制對流系統:溫控系統。
工藝流程
1. 單面板:
(1) 在貼裝與外掛程式焊盤同時印錫膏;
(2) 貼放 SMC/SMD;
(3) 插裝 TMC/TMD;
(4) 再流焊。
2. 雙面板:
(1) 錫膏-再流焊工藝,完成雙面片式元件的焊接;
(2) 然後在 B 面的通孔元件焊盤上塗覆錫膏;
(3) 反轉 PCB 並插入通孔元件;
(4) 第三次再流焊。
注意事項
1、與SMB 的相容性,包括焊盤的潤濕性和SMB 的耐熱性;
2、焊點的質量和焊點的抗張強度;
3、焊接工作曲線:
預熱區:升溫率為1.3~1.5 度/s,溫度在90~100s 內升至150 度。
保溫區:溫度為 150~180 度,時間40~60s。
再流區:從180到最高溫度250 度需要10~15s,回到保溫區約30s快速冷卻
無鉛焊接溫度(錫銀銅)217度。
4、Flip Chip 再流焊技術F.C。
汽相再流焊
又稱汽相焊(Vapor Phase Soldering,VPS),美國最初用於厚膜積體電路的焊接,具有升溫速度快和溫度均勻恆定的優點,但傳熱介質FC-70 價格昂貴,且需FC-113,又是臭氧層損耗物質。優點:
1、汽相潛熱釋放對SMA 的物理結構和幾何形狀不敏感,使組件均勻加熱到焊接溫度;
2、焊接溫度保持一定,無需採用溫控手段,滿足不同溫度焊接的需要;
3、VPS 的汽相場中是飽和蒸氣,含氧量低;
4、熱轉化率高。
雷射再流焊
1、原理和特點:利用雷射束直接照射焊接部位。
2、焊點吸收光能轉變成熱能,加熱焊接部位,使焊料熔化。
3、種類:固體YAG(乙鋁石榴石)雷射器。
常用知識
1.一般來說,SMT車間規定的溫度為23±7℃;
2.錫膏印刷時,所需準備的材料及工具 :錫膏、鋼板、刮刀、擦拭紙、無塵紙、清洗劑、攪拌刀;
3. 一般常用的錫膏成份為Sn96.5%/Ag3%/Cu0.5%;
4. 錫膏中主要成份分為兩大部分錫粉和助焊劑;
5. 助焊劑在焊接中的主要作用是去除氧化物、破壞融錫表面張力、防止再度氧化;
6. 錫膏中錫粉顆粒與Flux(助焊劑)的體積之比約為1:1,重量之比約為9:1;
7. 錫膏的取用原則是先進先出;
8. 錫膏在開封使用時,須經過兩個重要的過程回溫、攪拌;
9.鋼板常見的製作方法為:蝕刻、雷射、電鑄;
10. SMT的全稱是Surface mount(或mounting)technology,中文意思為表面粘著(或貼裝)技術;
11.ESD的全稱是Electro-static discharge,中文意思為靜電放電;
12. 製作SMT設備程式時,程式中包括五大部分,此五部分為PCB data; Mark data;Feeder data; Nozzle data; Part data;
13. 無鉛焊錫Sn/Ag/Cu 96.5/3.0/0.5的熔點為217C;
14. 零件乾燥箱的管制相對溫濕度為<10%;
15. 常用的被動元器件(PassiveDevices)有:電阻、電容、電感(或二極體)等;主動元器件(ActiveDevices)有:電晶體、IC等;
16. 常用的SMT鋼板的材質為不鏽鋼;
17. 常用的SMT鋼板的厚度為0.15mm(或0.12mm);
18.靜電電荷產生的種類有摩擦、分離、感應、靜電傳導等;靜電電荷對電子工業的影響為:ESD失效、靜電污染;靜電消除的三種原理為靜電中和、接地、禁止;
19. 英制尺寸長x寬0603=0.06inch*0.03inch,公制尺寸長x寬3216=3.2mm*1.6mm;
20. 排阻ERB-05604-J81第8碼“4”表示為4個迴路,阻值為56歐姆。電容ECA-0105Y-M31容值為C=106PF=1NF =1X10-6F;
21. ECN中文全稱為:工程變更通知單;SWR中文全稱為:特殊需求工作單,必須由各相關部門會簽,檔案中心分發,方為有效;
22.5S的具體內容為整理、整頓、清掃、清潔、素養;
23. PCB真空包裝的目的是防塵及防潮;
24. 品質政策為:全面品管、貫徹制度、提供客戶需求的品質;全員參與、及時處理、以達成零缺點的目標;
25. 品質三不政策為:不接受不良品、不製造不良品、不流出不良品;
26.QC七大手法是指檢查表、層別法、柏拉圖、因果圖、散布圖、直方圖、控制圖;
27.錫膏的成份包含:金屬粉末、溶劑、助焊劑、抗垂流劑、活性劑;按重量分,金屬粉末占85-92%,按體積分金屬粉末占50%;
28. 錫膏使用時必須從冰櫃中取出回溫,目的是:讓冷藏的錫膏溫度恢復到常溫,以利印刷。如果不回溫則在PCBA進Reflow後易產生的不良為錫珠;
29. 機器之檔案供給模式有:準備模式、優先交換模式、交換模式和速接模式;
30. SMT的PCB定位方式有:真空定位、機械孔定位、雙邊夾定位及板邊定位;
![SMT[表面組裝技術]](/img/c/e18/nBnauM3XyQzM3EDMwgzN2cjM2UTM1QDN5MjM5ADMwAjMwUzL4czL0czLt92YucmbvRWdo5Cd0FmLxE2LvoDc0RHa.jpg)
31. 絲印(符號)為272的電阻,阻值為2700Ω,阻值為4.8MΩ的電阻的符號(絲印)為485;
32.BGA本體上的絲印包含廠商、廠商料號、規格和Datecode/(Lot No)等信息;
33. 208pinQFP的pitch為0.5mm;
34. QC七大手法中,魚骨圖強調尋找因果關係;
35. CPK指:實際狀況下的製程能力;
36. 助焊劑在恆溫區開始揮發進行化學清洗動作;
37. 理想的冷卻區曲線和回流區曲線鏡像關係;
38. Sn62Pb36Ag2之焊錫膏主要試用於陶瓷板;
39. 以松香為主的助焊劑可分四種:R、RA、RSA、RMA;
40.RSS曲線為升溫→恆溫→回流→冷卻曲線;
41. 我們現使用的PCB材質為FR-4;
42. PCB翹曲規格不超過其對角線的0.7%;
43. STENCIL製作雷射切割是可以再重工的方法;
44. 計算機主機板上常用的BGA球徑為0.76mm;
45.ABS系統為絕對坐標;
46. 陶瓷晶片電容ECA-0105Y-K31誤差為±10%;
47. 使用的計算機的PCB,其材質為: 玻纖板;
48. SMT零件包裝其卷帶式盤直徑為13寸、7寸;
49. SMT一般鋼板開孔要比PCB PAD小4um可以防止錫球不良之現象;
50. 按照《PCBA檢驗規範》當二面角>90度時表示錫膏與波焊體無附著性;
51. IC拆包後濕度顯示卡上濕度在大於30%的情況下表示IC受潮且吸濕;
52. 錫膏成份中錫粉與助焊劑的重量比和體積比正確的是90%:10%,50%:50%;
53. 早期之表面粘裝技術源自於20世紀60年代中期之軍用及航空電子領域;
54. 目前SMT最常使用的焊錫膏Sn和Pb的含量各為:63Sn 37Pb;共晶點為183℃
55. 常見的頻寬為8mm的紙帶料盤送料間距為4mm;
56. 在20世紀70年代早期,業界中新出現一種SMD,為“密封式無腳晶片載體”,常以LCC簡代之;
57. 符號為272之組件的阻值應為2.7K歐姆;
58. 100NF組件的容值與0.10uf相同;
60. SMT使用量最大的電子零件材質是陶瓷;
61. 回焊爐溫度曲線其曲線最高溫度215C最適宜;
62. 錫爐檢驗時,錫爐的溫度245℃較合適;
63. 鋼板的開孔型式方形、三角形、圓形,星形,本磊形;
64. SMT段排阻有無方向性無;
65. 市面上售之錫膏,實際只有4小時的粘性時間;
66. SMT設備一般使用之額定氣壓為5KG/cm2;
67. SMT零件維修的工具有:烙鐵、熱風拔取器、吸錫槍、鑷子;
68. QC分為:IQC、IPQC、FQC、OQC;
69. 高速貼片機可貼裝電阻、電容、IC、電晶體;包裝方式為 Reel、Tray兩種,Tube不適合高速貼片機;
70. 靜電的特點:小電流、受濕度影響較大;
71. 正面PTH,反面SMT過錫爐時使用何種焊接方式擾流雙波焊;
72. SMT常見之檢驗方法: 目視檢驗、X光檢驗、機器視覺檢驗、AOI光學儀器檢測;
73.鉻鐵修理零件熱傳導方式為傳導對流;
74. BGA材料其錫球的主要成份Sn90 Pb10,SAC305,SAC405;
75. 鋼板的製作方法雷射切割、電鑄法、化學蝕刻;
76. 迥焊爐的溫度按:利用測溫器量出適用之溫度;
77. 迥焊爐之SMT半成品於出口時其焊接狀況是零件固定於PCB上;
78. 現代質量管理髮展的歷程TQC-TQA-TQM;
79.ICT測試是針床測試;
80. ICT之測試能測電子零件採用靜態測試;
81. 焊錫特性是融點比其它金屬低、物理性能滿足焊接條件、低溫時流動性比其它金屬好;
82. 迥焊爐零件更換製程條件變更要重新測量測度曲線;
83. 西門子80F/S屬於較電子式控制傳動;
84. 錫膏測厚儀是利用Laser光測: 錫膏度、錫膏厚度、錫膏印出之寬度;
85. SMT零件供料方式有振動式供料器、盤狀供料器、卷帶式供料器;
![SMT[表面組裝技術]](/img/0/a25/nBnauM3XycTO2ATOxgzN2cjM2UTM1QDN5MjM5ADMwAjMwUzL4czL2MzLt92YucmbvRWdo5Cd0FmLxE2LvoDc0RHa.jpg)
86. SMT設備運用哪些機構:凸輪機構、邊桿機構、螺桿機構、滑動機構;
87. 目檢段若無法確認則需依照何項作業BOM、廠商確認、樣品板;
88. 若零件包裝方式為12w8P,則計數器Pinth尺寸須調整每次進8mm;
89. 迥焊機的種類: 熱風式迥焊爐、氮氣迥焊爐、laser迥焊爐、紅外線迥焊爐;
90. SMT零件樣品試作可採用的方法:流線式生產、手印機器貼裝、手印手貼裝;
91. 常用的MARK形狀有:圓形,“十”字形、正方形,菱形,三角形,萬字形;
92. SMT段因Reflow Profile設定不當,可能造成零件微裂的是預熱區、冷卻區;
93. SMT段零件兩端受熱不均勻易造成:空焊、偏位、墓碑;
94. 高速機與泛用機的Cycle time應儘量均衡;
95. 品質的真意就是第一次就做好;
96. 貼片機應先貼小零件,後貼大零件;
97. BIOS是一種基本輸入輸出系統,全英文為:Base Input/Output System;
98. SMT零件依據零件腳有無可分為LEAD與LEADLESS兩種;
![SMT[表面組裝技術]](/img/f/0b0/nBnauM3X2YTM4ADM4czN2cjM2UTM1QDN5MjM5ADMwAjMwUzL3czL3EzLt92YucmbvRWdo5Cd0FmLwE2LvoDc0RHa.jpg)
99. 常見的自動放置機有三種基本型態,接續式放置型,連續式放置型和大量移送式放置機;
100. SMT製程中沒有LOADER也可以生產;
101. SMT流程是送板系統-錫膏印刷機-高速機-泛用機-迥流焊-收板機;
102. 溫濕度敏感零件開封時,濕度卡圓圈內顯示顏色為藍色,零件方可使用;
103. 尺寸規格20mm不是料帶的寬度;
104. 製程中因印刷不良造成短路的原因:a. 錫膏金屬含量不夠,造成塌陷b.鋼板開孔過大,造成錫量過多c. 鋼板品質不佳,下錫不良,換雷射切割模板d.Stencil背面殘有錫膏,降低刮刀壓力,採用適當的VACUUM和SOLVENT;
105.一般回焊爐Profile各區的主要工程目的:a.預熱區;工程目的:錫膏中容劑揮發。b.均溫區;工程目的:助焊劑活化,去除氧化物;蒸發多餘水份。c.回焊區;工程目的:焊錫熔融。d.冷卻區;工程目的:合金焊點形成,零件腳與焊盤接為一體;
106. SMT製程中,錫珠產生的主要原因:PCB PAD設計不良、鋼板開孔設計不良、置件深度或置件壓力過大、Profile曲線上升斜率過大,錫膏坍塌、錫膏粘度過低。
貼片紅膠
基本知識
SMT貼片紅膠是一種聚稀化合物,與錫膏不同的是其受熱後便固化,其凝固點溫度為150℃,這時,紅膠開始由膏狀體直接變成固體。
SMT貼片紅膠具有粘度流動性,溫度特性,潤濕特性等。根據紅膠的這個特性,故在生產中,利用紅膠的目的就是使零件牢固地貼上於PCB表面,防止其掉落。
印刷機或點膠機上使用:
1、為保持貼片膠的品質,請置於冰櫃內冷藏(5±3℃)儲存;
2、從冰櫃中取出使用前,應放在室溫下回溫2~3小時;
3、可以使用甲苯或醋酸乙酯來清洗膠管 點膠:
![SMT[表面組裝技術]](/img/f/394/nBnauM3X4YDM0QTM3czN2cjM2UTM1QDN5MjM5ADMwAjMwUzL3czL1gzLt92YucmbvRWdo5Cd0FmLyE2LvoDc0RHa.jpg)
①在點膠管中加入後塞,可以獲得更穩定的點膠量;
②推薦的點膠溫度為30-35℃;
③分裝點膠管時,請使用專用膠水分裝機進行分裝,以防止在膠
水中混入氣泡 刮膠:推薦的刮膠溫度為30-35℃注意事項:紅
膠從冷藏環境中移出後,到達室溫前不可打開使用。為避免污
染原裝產品,不得將任何使用過的貼片膠倒回原包裝內。
印刷方式
1) 印刷方式:鋼網刻孔要根據零件的類型,基材的性能來決定,其厚度和孔的大小及形狀。其優點是速度快、效率高。

2) 點膠方式:點膠是利用壓縮空氣,將紅膠透過專用點膠頭點到基板上,膠點的大小、多少、由時間、壓力管直徑等參數來控制,點膠機具有靈活的功能。對於不同的零件,我們可以使用不同的點膠頭,設定參 數來改變,也可以改變膠點的形狀和數量,以求達到效果,優點是方便、靈活、穩定。缺點是易有拉絲和氣泡等。我們可以對作業參數、速度、時間、氣壓、溫度調整,來儘量減少這些缺點。
3) 針轉方式,是將一個特製的針膜,浸入淺膠盤中每個針頭有一個膠點,當膠點接觸基板時,就會脫離針頭,膠量可以借著針的形狀和直徑大小來變化。固化溫度100℃ 120℃150℃ 固化時間5分鐘 150秒60秒 典型固化條件:注意點:
1、固化溫度越高以及固化時間越長,粘接強度也越強。
2、由於貼片膠的溫度會隨著基板零件的大小和貼裝位置的不同而變化,因此我們建議找出最合適的硬化條件。紅膠的儲存:在室溫下可儲存7天,在小於5℃時儲存大於個6月,在5~25℃可儲存大於30天。
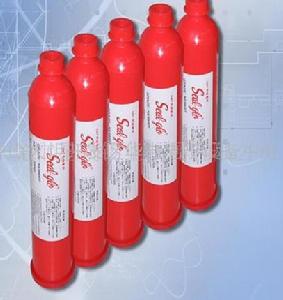
由於SMT貼片紅膠受溫度影響用本身粘度,流動性,潤濕等特性,所以SMT貼片紅膠要有一定的使用條件和 規範的管理。
1) 紅膠要有特定流水編號,根據進料數量、日期、種類來編號。
2) 紅膠要放在2~8℃的冰櫃中保存,防止由於溫度變化,影響特性。
3) 紅膠回溫要求在室溫下回溫4小時,按先進先出的順序使用。
4) 對於點膠作業,膠管紅膠要脫泡,對於一次性未用完的紅膠應放回冰櫃保存,舊膠與新膠不能混用。
5) 要準確地填寫回溫記錄表,回溫人及回溫時間,使用者需確認回溫完成後方可使用。通常,紅膠不可使用過期的。
組裝工藝
SMT組裝工藝與焊接前的每一工藝步驟密切相關,其中包括資金投入、PCB設計、元件可焊性、組裝操作、焊劑選擇、溫度/時間的控制、焊料及晶體結構等。
焊料
波峰焊接最常用的焊料是共晶錫鉛合金:錫63%;鉛37%,應時刻掌握焊錫鍋中的焊料溫度,其溫度應高於合金液體溫度183℃,並使溫度均勻。過去,250℃的焊錫鍋溫度被視為“標準”。
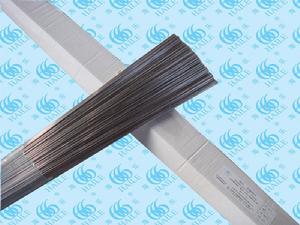
隨著焊劑技術的革新,整個焊錫鍋中的焊料溫度的均勻性得到了控制,並增設了預熱器,發展趨勢是使用溫 度較低的焊錫鍋。在230-240℃的範圍內設定焊錫鍋溫度是很普遍的。通常,組件沒有均勻的熱質量,要保證所有的焊點達到足夠的溫度,以便形成合格的焊點是必要的。重要的問題是要提供足夠的熱量,提高所有引線和焊盤的溫度,從而確保焊料的流動性,濕潤焊點的兩面。焊料的溫度較低就會降低對元件和基板的熱衝擊,有助於減少浮渣的形成,在較低的強度下,進行焊劑塗覆操作和焊劑化合物的共同作用下,可使波峰出口具有足夠的焊劑,這樣就可減少毛刺和焊球的產生。
焊錫鍋中的焊料成份與時間有密切關係,即隨著時間而變化,這樣就導致了浮渣的形成,這就是要從焊接的組件上去除殘餘物和其它金屬雜質的原因及在焊接工藝中錫損耗的原因。以上這些因素可降低焊料的流動性。在採購中,要規定的金屬微量浮渣和焊料的錫含量的最高極限,在各個標準中,(如象IPC/J-STD-006都有明確的規定)。在焊接過程中,對焊料純度的要求在ANSI/J-STD-001B標準中也有規定。除了對浮渣的限制外,對63%錫;37%鉛合金中規定錫含量最低不得低於61.5%。波峰焊接組件上的金和有機泳層銅濃度聚集比過去更快。這種聚集,加上明顯的錫損耗,可使焊料喪失流動性,並產生焊接問題。外表粗糙、呈顆粒狀的焊點常常是由於焊料中的浮渣所致。由於焊錫鍋中的集聚的浮渣或組件自身固有的殘餘物暗淡、粗糙的粒狀焊點也可能是錫含量低的徵兆,不是局部的特種焊點,就是錫鍋中錫損耗的結果。這種外觀也可能是在凝固過程中,由於振動或衝擊所造成的。
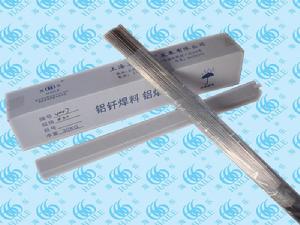
焊點的外觀就能直接體現出工藝問題或材料問題。為保持焊料“滿鍋”狀態和按照工藝控制方案對檢查焊錫 鍋分析是很重要的。由於焊錫鍋中有浮渣而“倒掉”焊錫鍋中的焊劑,通常來說是不必要的,由於在常規的套用中要求往錫鍋中添加焊料,使錫鍋中的焊料始終是滿的。在損耗錫的情況下,添加純錫有助於保持所需的濃度。為了監控錫鍋中的化合物,應進行常規分析。如果添加了錫,就應採樣分析,以確保焊料成份比例正確。浮渣過多又是一個令人棘手的問題。毫無疑問,焊錫鍋中始終有浮渣存在,在大氣中進行焊接時尤其是這樣。使用“晶片波峰”這對焊接高密度組件很有幫助,由於暴露於大氣的焊料表面太大,而使焊料氧化,所以會產生更多的浮渣。焊錫鍋中焊料表面有了浮渣層的覆蓋,氧化速度就放慢了。
在焊接中,由於錫鍋中波峰的湍流和流動而會產生更多的浮渣。推薦使用的常規方法是將浮渣撇去,要是經常進行撇削的話,就會產生更多的浮渣,而且耗用的焊料更多。浮渣還可能夾雜于波峰中,導致波峰的不穩定或湍流,因此要求對焊錫鍋中的液體成份給予更多的維護。如果允許減少錫鍋中焊料量的話,焊料表面的浮渣會進入泵中,這種現象很可能發生。有時,顆粒狀焊點會夾雜浮渣。最初發現的浮渣,可能是由粗糙波峰所致,而且有可能堵塞泵。錫鍋上應配備可調節的低容量焊料感測器和報警裝置。
波峰
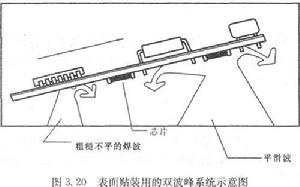
在波峰焊接工藝中,波峰是核心。可將預熱的、塗有焊劑、無污物的金屬通過傳送帶送到焊接工作站,接觸 具有一定溫度的焊料,而後加熱,這樣焊劑就會產生化學反應,焊料合金通過波峰動力形成互連,這是最關鍵的一步。常用的對稱波峰被稱為主波峰,設定泵速度、波峰高度、浸潤深度、傳送角度及傳送速度,為達到良好的焊接特性提供全方位的條件。應該對數據進行適當的調整,在離開波峰的後面(出口端)就應使焊料運行降速,並慢慢地停止運行。PCB隨著波峰運行最終要將焊料推至出口。在最佳的情況下,焊料的表面張力和最佳化的板的波峰運行,在組件和出口端的波峰之間可實現零相對運動。這一脫殼區域就是實現了去除板上的焊料。應提供充分的傾角,不產生橋接、毛刺、拉絲和焊球等缺陷。有時,波峰出口需具有熱風流,以確保排除可能形成的橋接。在板的底部裝上表面貼裝元件後,有時,補償焊劑或在後面形成的“苛刻的波峰”區域的氣泡,而進行的波峰整平之前,使用湍流晶片波峰。湍流波峰的高豎直速度有助於保證焊料與引線或焊盤的接觸。在整平的層流波峰後面的振動部分也可用來消除氣泡,保證焊料實現滿意的接觸組件。焊接工作站基本上應做到:高純度焊料(按標準)、波峰溫度(230~250℃)、接觸波峰的總時間(3~5秒鐘)、印製板浸入波峰中的深度(50~80%),實現平行的傳送軌道和在波峰與軌道平行狀態下錫鍋中焊劑含量。
焊接後的冷卻
![SMT[表面組裝技術]](/img/3/016/nBnauM3X2UDM4IDOygzN2cjM2UTM1QDN5MjM5ADMwAjMwUzL4czL2EzLt92YucmbvRWdo5Cd0FmLzE2LvoDc0RHa.jpg)
通常在波峰焊機的尾部增設冷卻工作站。為的是限制銅錫金屬間化合物形成焊點的趨勢,另一個原因是加速 組件的冷卻,在焊料沒有完全固化時,避免板子移位。快速冷卻組件,以限制敏感元件暴露於高溫下。然而,應考慮到侵蝕性冷卻系統對元件和焊點的熱衝擊的危害性。一個控制良好的“柔和穩定的”、強制氣體冷卻系統應不會損壞多數組件。使用這個系統的原因有兩個:能夠快速處理板,而不用手夾持,並且可保證組件溫度比清洗溶液的溫度低。人們所關心的是後一個原因,其可能是造成某些焊劑殘渣起泡的原因。另一種現象是有時會出現與某些焊劑浮渣產生反應的現象,這樣,使得殘餘物“清洗不掉”。在保證焊接工作站設定的數據滿足所有的機器、所有的設計、採用的所有材料及工藝材料條件和要求方面沒有哪個定式能夠達到這些要求。必須了解整個工藝過程中的每一步操作。4 結論總之,要獲得最佳的焊接質量,滿足用戶的需求,必須控制焊接前、焊接中的每一工藝步驟,因為SMT的整個組裝工藝的每一步驟都互相關聯、互相作用,任一步有問題都會影內到整體的可靠性和質量。焊接操作也是如此,所以應嚴格控制所有的參數、時間/溫度、焊料量、焊劑成分及傳送速度等等。對焊接中產生的缺陷,應及早查明起因,進行分析,採取相應的措施,將影響質量的各種缺陷消滅在萌芽狀態之中。這樣,才能保證生產出的產品。
減少故障方法
製造過程、搬運及印刷電路組裝 (PCA) 測試等都會讓封裝承受很多機械應力,從而引發故障。隨著格柵陣列封裝變得越來越大,針對這些步驟應該如何設定安全水平也變得愈加困難。
多年來,採用單調彎曲點測試方法是封裝的典型特徵,該測試在 IPC/JEDEC-9702 《板面水平互聯的單調彎曲特性》中有敘述。該測試方法闡述了印刷電路板水平互聯在彎曲載荷下的斷裂強度。但是該測試方法無法確定最大允許張力是多少。
對於製造過程和組裝過程,特別是對於無鉛PCA而言,其面臨的挑戰之一就是無法直接測量焊點上的應力。最為廣泛採用的用來描述互聯部件風險的度量標準是毗鄰該部件的印刷電路板張力,這在 IPC/JEDEC-9704 《印製線路板應變測試指南》中有敘述。
隨著無鉛設備的用途擴大,用戶的興趣也越來越大;因為有很多用戶面臨著質量問題。
隨著各方興趣的增加,IPC 覺得有必要幫助其他公司開發各種能夠確保BGA在製造和測試期間不受損傷的測試方法。這項工作由 IPC 6-10d SMT 附屬檔案可靠性測試方法工作小組和 JEDEC JC-14.1 封裝設備可靠性測試方法子委員會攜手開展,目前該工作已經完成。
該測試方法規定了以圓形陣列排布的八個接觸點。在印刷電路板中心位置裝有一 BGA 的 PCA 是這樣安放的:部件面朝下裝到支撐引腳上,且負載施加於 BGA 的背面。根據 IPC/JEDEC-9704 的建議計量器布局將應變計安放在與該部件相鄰的位置。
PCA 會被彎曲到有關的張力水平,且通過故障分析可以確定,撓曲到這些張力水平所引致的損傷程度。通過疊代方法可以確定沒有產生損傷的張力水平,這就是張力限值。