製造方法
環氧樹脂模塑粉的製造方法是通過工藝措施把各組分混合均
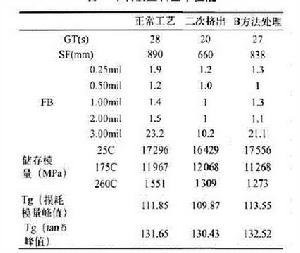
原料準備
填料應選用符合細度要求的品種。樹脂和其他固體物料進行粉碎和過篩。應有30%以上通過60目篩。樹脂磨得過細,則能耗增加,生產效率降低,還給輥壓操作帶來困難。過粗,則使模塑粉質量不均勻,影響產品性能。易吸濕組分應烘乾,使含水量達到規定要求。太乾或太濕都會增加輥壓工序的困難,影響產品質量。
乾混合
粉料在球磨機、Z型捏合機、高速攪拌機等混合設備中進行混合。加料順序對物料混合的均勻性影響很大。應首先將樹脂和除填料以外的其他小組分混勻後,再加入填料進行混合。因為填料用量很大,若一同混合,則會影響混合效率和均勻性。混合好的物料不宜直接使用。因為各組分的密度不同,在運送和裝料過程中受振動時會破壞其均勻性。其次,樹脂尚未充分浸漬填料等添加物,也沒有預聚到需要的程度,模壓時流動性大,工藝性差,產品質量低。所以必須經熱輥壓後,才能用來壓制製品。
熱輥壓
熱輥壓是模塑粉生產的關鍵工序。配方確定後,模塑粉的質量取決於熱輥壓的溫度和時間。輥壓操作在雙輥輥壓機(又稱塑煉機)上進行。輥壓機由兩個空心鋼輥筒構成。可通蒸汽加熱和用水冷卻。也可用電加熱。兩個輥筒以不同的轉速相對旋轉,轉速比為1.3左右。兩個輥筒的溫度也不同。低溫輥筒的溫度應高於樹脂的軟化點,高溫輥筒則比低溫輥筒的溫度高20~30℃。兩輥筒的間隙可調節,其大小決定了料片的厚度。通常料片厚度控制為1.5~3mm。
輥壓時,物料在輥筒上受熱熔融。通過輥筒間隙時受到擠壓、剪下、捏合等作用,使各組分浸漬得更好、分散得更均勻。樹脂熔化形成的黏性物料均勻地附在一個輥筒(低溫快速輥筒)的表面,此輥簡稱為工作輥筒,另一個稱為空轉輥筒。這種輥壓法稱為逆式輥壓法。為了混合得更均勻,可用人工或多片刮刀把工作輥筒上的料片割下來,翻轉後再輥壓,並重複多次。若將快速輥筒變為高溫,慢速輥筒變為低溫,則稱為順式輥壓法。這時物料不包輥,隨輥隨落,需要不斷地把物料重新放到輥筒上繼續輥壓。據中國環氧樹脂行業協會專家介紹,這種方法費工但物料輥壓程度可隨時掌握,避免把料輥老。逆式輥壓法的物料經常包住輥筒,熱量損失少,輥筒利用率高。
熱輥壓的目的是使樹脂更好地浸漬填料等添加物;使各組分充分混合均勻;進行一定程度的預聚,提高交聯度使接近B階段,以改善模塑時的流動性、縮短成型周期,提高生產效率;除去部分揮發物,改善工藝性及製品質量;使模塑粉密實,減小比容,以減輕模具並有利於成型操作。
控制輥壓質量的主要指標是流動性、揮發物含量和外觀質量。由於輥壓時間不長,在實際生產中來不及實測這些指標來控制質量,通常是由操作者憑經驗來控制。
後期
輥壓好的料片從輥壓機上卸下後應迅速冷卻,終止預聚反映。冷卻後即可粉碎、過篩。粉碎的細度以能保證模塑粉有良好的鬆散性和一定的比容(通常<2)為宜。顆粒度愈均勻愈好。這樣它在模具中就具有均勻一致的溫升和塑化速度,成型工藝性和製品質量好。通常模塑粉的粒徑<2mm,但應儘量減少過細顆粒。粉碎了的模塑粉還要進行磁選,除去金屬雜質。並批後即可包裝。