簡介
減徑機可分為:
1、一般微張力減徑機,作用就是減縮管徑,生產機組不能軋制或加工起來很不經濟的規格;
2、張力減徑機,作用是減徑又減壁,使機組產品規格進一步擴大;並可適當加大來料的重量,提高減徑率軋制更長的成品。單此一項,據統計即可提高機組產量約15%~20%,所以近20~30年來張力減徑機得到迅速發展。
減徑機按主機架軋輥數分有三輥式和二輥式兩種,三輥式套用較廣,因三輥軋制變形分布較均勻,管材橫剖面壁厚均勻性好,同樣的名義輥徑,三輥機架間距小可縮短12%~14%;二輥主要用於壁厚大於10~12mm的厚壁管。從傳動形式看有集體傳動、單獨傳動和差動傳動等,後兩種的傳動形式見下圖。
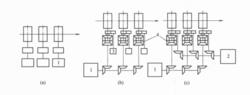
以差動傳動採用最廣,因其便於調整速度能滿足現代軋機對產品規格範圍和精度的要求,單獨傳動也能滿這一點,只是投資昂貴,但在高速運轉條件下(>10~12m/s)比較安全可靠。集體傳動已不使用。
減徑機的一般工藝特點
普通微張力減徑機因減徑過程中管壁增厚和橫截面上的壁厚不均嚴重,主要生產中等壁厚的管材,或以5~11架軋機作定徑使用。現代張力減徑機因為張力大所以不僅可以減徑,同時可以減壁,而且橫截面上壁厚分布比較均勻,延伸係數達到6~8。但它有個突出的缺點,就是首尾管壁相對中部偏厚,增加了切頭損失。所以如何降低減徑管首尾壁厚偏高的程度和長度,成為研究的主要課題之一。
研究證明,張減管端偏厚的主要原因是軋件首尾軋制時都是處於過程的不穩定階段,首先,軋件兩端總有相當於機架間距的一段長度,一直都是在無張力狀態下減徑;其次,前端在進入機組的前3~5機架之後,軋機間的張力才逐漸由零增加到穩定軋制的最大值,而尾部在離開最後3~5機架時,軋機間的張力又從穩定軋制的最大值降到零。這樣軋件相應的前端壁厚就由最厚逐漸降到穩定軋制時的最薄值,尾端又由穩定軋制的最薄值逐漸增厚到無張力減徑時的最大厚度。因此首尾厚壁段的切損率,主要取決於以下因素:
1、機架間距,機架間距愈小,厚壁端愈短;
2、軋機的傳動特性,傳動速度的剛性愈好,恢復轉速的時間愈短,首尾管壁的偏厚值愈小,長度愈短;
3、延伸係數和減徑率愈大首尾管壁的偏厚值愈大長度愈長;
4、機架間的張力愈大,首尾相對中間的壁厚差亦愈大,切損愈高。但從另一方面看,加大張力可以使用較厚的毛管提高機組產率。所以實際生產中應當摸索合理的張力制度,以求得最佳的經濟效果。實踐證明,進入減徑機的來料長度應在18~20m以上,在經濟上才是合理的。因此張力減徑機多用於連續軋管機、皮爾格軋機和連續焊管機組之後。
減少切頭損失措施
為了減少張力減徑機的切頭損失主要可以從以下幾方面著手:
1、改進設備設計,儘量縮小機架間距;
2、改進工藝設計,儘量加長減徑機軋出長度;
3、通過電器控制改善軋機傳動特性,下圖所示為張力減徑機的一種調速方案,穩定軋制時各機架轉速根據張力要求按a線分布;前端軋制時使軋輥轉速按b線分布,令各機架轉速的增值總是依次略高於上一機架;尾端軋制時使軋輥轉速按e線分布,令各機架轉速的降低值總是依次小於上一機架,目的使軋件首尾通過減徑機組所受的張力變形效應,基本上與穩定軋制時相近,減少管端增厚的程度和長度,減少切損;
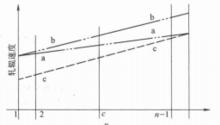
4、提供兩端壁厚較薄的軋管料;
5、“無頭軋制”,這種軋制方法如能實現,將使偏厚端頭的切損降到最低限度。但在實際生產中套用還存在一定問題,目前發展勢頭不大。現代張力減徑機軋後成品長度一般在120~180m,進入冷床前由飛鋸或飛剪下成定尺。
減徑機的變形制度和孔型設計
減徑機組的總減徑率和單機徑縮率是減徑變形過程的重要參數。不適當地加大單機徑縮率,或單機徑縮率不變增加機架數提高總減徑率都會惡化成品管橫剖面的壁厚均勻性,和加大首尾壁厚段的增厚程度。嚴重時在二輥軋機上出現“外圓內方”,在三輥軋機上出現“外圓內六角”。因此減徑管的形狀和尺寸精度限制了減徑機的減徑率和延伸值。目前微張力減徑機的最大總減徑率限制在40%~45%;厚壁管限制在25%~30%。張力減徑機總減徑率限制在75%~80%,減壁率在35%~40%,延伸係數達到6~8。
現代張力減徑機機架數雖由24增加到30,但主要是用於增加張力提升階段和張力降低階段的機架數,以保證軋制過程的穩定性和改善產品壁厚的均勻性。總的來說無論是提高單機徑縮率還是總的機組徑縮率都將使減徑管的壁厚均勻性惡化,因此確定這些變形參數時,應認真考慮到產品的尺寸精度要求。目前微張力減徑機的單機徑縮率取值在3%~5%,考慮到成品管尺寸精度常限制在3.0%~3.5%。張力減徑機單機徑縮率可高達10%~12%,為控制管壁均勻性一般多限制在6%~9%,管徑大取下限。對薄壁管單機的最大徑縮率還應考慮到變形過程中軋件橫截面在孔型中的穩定性,不然就會在孔型開口處出現凹陷和軋折。管件橫截面在孔型內的穩定性主要隨相對壁厚h/d、機架內輥數、平均張力係數Z(軋機前後張力平均值)而正變。此可根據有關的實測曲線確定不同變形條件下的最大允許單機縮徑率。
減徑機的孔型設計按以下步驟進行:首先向各機架分配徑縮率;然後計算各架孔型的平均直徑;再按各道平均直徑具體設計各道孔型的形狀和尺寸。微張力減徑機的管件徑縮率一般第一架皆取機組平均徑縮率的一半,保證順利咬入,和防止來料沿縱向直徑波動,局部徑縮量過大造成軋折。成品前架也取平均徑縮率的一半,成品機架不給壓下,這主要為獲得要求的尺寸精度。張力減徑機除上述問題外,還應考慮提升和降低張力軋制過程的穩定性,以及控制管材首尾壁厚的增值。所以張力減徑機開始第一架徑縮率也取得很小,通過1~2架軋機後,再逐步增加徑縮率,直到正常值,機架間的張力也相應提升到正常的張力係數。保證順利地咬入和穩定地建立起張力軋制過程。最後3~4架的徑縮率也是逐漸減小,直至成品機架取零,相應機架間的張力也由正常值逐漸降到零。其目的也是保證張力降低過程中變形區不打滑,過程穩定;保證良好的管材尺寸精度;減少孔型磨損延長使用壽命。中間各機架的徑縮率原則上均勻分配。但實踐表明,由於軋件溫度愈來愈低,這樣做軋機的負荷愈向出口愈高,軋輥也愈向出口磨損愈嚴重。所以合理的減徑率分配應向出口逐漸下降,達到機架負荷與孔型磨損均勻化。一般皆使相鄰機架間單機徑縮率逐次降低1.5%~2.0%。