加熱原理
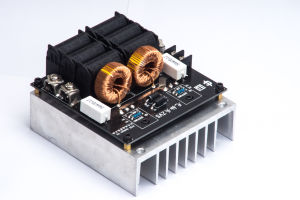
高頻加熱的深度為0.5-2.5mm,一般用於中小型零件的加熱,如小模數齒輪及中小軸類零件等。
中頻加熱深度為2-10mm,一般用於直徑大的軸類和大中模數的齒輪加熱。
工頻加熱淬硬層深度為10-20mm,一般用於較大尺寸零件的透熱,大直徑零件(直徑Ø300mm以上,如軋輥等)的表面淬火。
感應加熱表面淬火具有表面質量好,脆性小,淬火表面不易氧化脫碳,變形小等優點,所以感應加熱設備在金屬表面熱處理中得到了廣泛套用。
感應加熱設備是產生特定頻率感應電流,進行感應加熱及表面淬火處理的設備。
頻率選擇
感應加熱頻率的選擇:根據熱處理及加熱深度的要求選擇頻率,頻率越高加熱的深度越淺。高頻(10KHZ以上)加熱的深度為0.5-2.5mm,一般用於中小型零件的加熱,如小模數齒輪及中小軸類零件等。中頻(1~10KHZ)加熱深度為2-10mm,一般用於直徑大的軸類和大中模數的齒輪加熱。工頻(50HZ)加熱淬硬層深度為10-20mm,一般用於較大尺寸零件的透熱,大直徑零件(直徑Ø300mm以上,如軋輥等)的表面淬火。
經驗公式
感應加熱淬火表層淬硬層的深度,取決於交流電的頻率,一般是頻率高加熱深度淺,淬硬層深度也就淺。頻率f與加熱深度δ的關係,有如下經驗公式:δ=20/√f(20°C);δ=500/√f(800°C)。式中:f為頻率,單位為Hz;δ為加熱深度,單位為毫米(mm)。
具體套用
感應加熱表面淬火具有表面質量好,脆性小,淬火表面不易氧化脫碳,變形小等優點,所以感應加熱設備在金屬表面熱處理中得到了廣泛套用。感應加熱設備是產生特定頻率感應電流,進行感應加熱及表面淬火處理的設備。
金屬熱處理的工藝
熱處理工藝一般包括加熱、保溫、冷卻三個過程,有時只有加熱和冷卻兩個過程。這些過程互相銜接,不可間斷。加熱是熱處理的重要步驟之一。金屬熱處理的加熱方法很多,最早是採用木炭和煤作為熱源,進而套用液體和氣體燃料。電的套用使加熱易於控制,且無環境污染。利用這些熱源可以直接加熱,也可以通過熔融的鹽或金屬,以至浮動粒子進行間接加熱。金屬加熱時,工件暴露在空氣中,常常發生氧化、脫碳(即鋼鐵零件表面碳含量降低),這對於熱處理後零件的表面性能有很不利的影響。因而金屬通常應在可控氣氛或保護氣氛中、熔融鹽中和真空中加熱,也可用塗料或包裝方法進行保護加熱。加熱溫度是熱處理工藝的重要工藝參數之一,選擇和控制加熱溫度,是保證熱處理質量的主要問題。加熱溫度隨被處理的金屬材料和熱處理的目的不同而異,但一般都是加熱到相變溫度以上,以獲得需要的組織。另外轉變需要一定的時間,因此當金屬工件表面達到要求的加熱溫度時,還須在此溫度保持一定時間,使內外溫度一致,使顯微組織轉變完全,這段時間稱為保溫時間。採用高能密度加熱和表面熱處理時,加熱速度極快,一般就沒有保溫時間或保溫時間很短,而化學熱處理的保溫時間往往較長。
冷卻也是熱處理工藝過程中不可缺少的步驟,冷卻方法因工藝不同而不同,主要是控制冷卻速度。一般退火的冷卻速度最慢,正火的冷卻速度較快,淬火的冷卻速度更快。但還因鋼種不同而有不同的要求,例如空硬鋼就可以用正火一樣的冷卻速度進行淬硬。
金屬熱處理工藝大體可分為整體熱處理、表面熱處理、局部熱處理和化學熱處理等。根據加熱介質、加熱溫度和冷卻方法的不同,每一大類又可區分為若干不同的熱處理工藝。同一種金屬採用不同的熱處理工藝,可獲得不同的組織,從而具有不同的性能。鋼鐵是工業上套用最廣的金屬,而且鋼鐵顯微組織也最為複雜,因此鋼鐵熱處理工藝種類繁多。整體熱處理是對工件整體加熱,然後以適當的速度冷卻,以改變其整體力學性能的金屬熱處理工藝。鋼鐵整體熱處理大致有退火、正火、淬火和回火四種基本工藝。退火→將工件加熱到適當溫度,根據材料和工件尺寸採用不同的保溫時間,然後進行緩慢冷卻(冷卻速度最慢),目的是使金屬內部組織達到或接近平衡狀態,獲得良好的工藝性能和使用性能,或者為進一步淬火作組織準備。正火→將工件加熱到適宜的溫度後在空氣中冷卻,正火的效果同退火相似,只是得到的組織更細,常用於改善材料的切削性能,也有時用於對一些要求不高的零件作為最終熱處理。淬火→將工件加熱保溫後,在水、油或其它無機鹽、有機水溶液等淬冷介質中快速冷卻。淬火後鋼件變硬,但同時變脆。為了降低鋼件的脆性,將淬火後的鋼件在高於室溫而低於710℃的某一適當溫度進行長時間的保溫,再進行冷卻,這種工藝稱為回火。退火、正火、淬火、回火是整體熱處理中的“四把火”,其中的淬火與回火關係密切,常常配合使用,缺一不可。“四把火”隨著加熱溫度和冷卻方式的不同,又演變出不同的熱處理工藝。為了獲得一定的強度和韌性,把淬火和高溫回火結合起來的工藝,稱為調質。某些合金淬火形成過飽和固溶體後,將其置於室溫或稍高的適當溫度下保持較長時間,以提高合金的硬度、強度或電性磁性等。這樣的熱處理工藝稱為時效處理。把壓力加工形變與熱處理有效而緊密地結合起來進行,使工件獲得很好的強度、韌性配合的方法稱為形變熱處理;在負壓氣氛或真空中進行的熱處理稱為真空熱處理,它不僅能使工件不氧化,不脫碳,保持處理後工件表面光潔,提高工件的性能,還可以通入滲劑進行化學熱處理。
表面熱處理是只加熱工件表層,以改變其表層力學性能的金屬熱處理工藝。為了只加熱工件表層而不使過多的熱量傳入工件內部,使用的熱源須具有高的能量密度,即在單位面積的工件上給予較大的熱能,使工件表層或局部能短時或瞬時達到高溫。表面熱處理的主要方法,有雷射熱處理、火焰淬火和感應加熱熱處理,常用的熱源有氧乙炔或氧丙烷等火焰、感應電流、雷射和電子束等。化學熱處理是通過改變工件表層化學成分、組織和性能的金屬熱處理工藝。化學熱處理與表面熱處理不同之處是後者改變了工件表層的化學成分。化學熱處理是將工件放在含碳、氮或其它合金元素的介質(氣體、液體、固體)中加熱,保溫較長時間,從而使工件表層滲入碳、氮、硼和鉻等元素。滲入元素後,有時還要進行其它熱處理工藝如淬火及回火。化學熱處理的主要方法有滲碳、滲氮、滲金屬、複合滲等。
熱處理是機械零件和工模具製造過程中的重要工序之一。大體來說,它可以保證和提高工件的各種性能,如耐磨、耐腐蝕等。還可以改善毛坯的組織和應力狀態,以利於進行各種冷、熱加工。
例如白口鑄鐵經過長時間退火處理可以獲得可鍛鑄鐵,提高塑性;齒輪採用正確的熱處理工藝,使用壽命可以比不經熱處理的齒輪成倍或幾十倍地提高;另外,價廉的碳鋼通過滲入某些合金元素就具有某些價昂的合金鋼性能,可以代替某些耐熱鋼、不鏽鋼;工模具則幾乎全部需要經過熱處理方可使用。
淬火套用
感應加熱表面淬火的套用一、套用:承受扭轉、彎曲等交變負荷作用的工件,要求表面層承受比心部更高的應力或耐磨性,需對工件表面提出強化要求,適於含碳量We=0.40~0.50%鋼材。二、工藝方法快速加熱與立即淬火冷卻相結合。通過快速加熱使待加工鋼件表面達到淬火溫度,不等熱量傳到中心即迅速冷卻,僅使表層淬硬為馬氏體,中心仍為未淬火的原來塑性、韌性較好的退火(或正火及調質)組織。三、主要方法:感應加熱表面淬火(高頻、中頻、工頻),火焰加熱表面淬火,電接觸加熱表面淬火,電解液加熱表面淬火,雷射加熱表面淬火,電子束加熱表面淬火。四、感應加熱表面淬火(一)基本原理:將工件放在用空心銅管繞成的感應器內,通入中頻或高頻交流電後,在工件表面形成同頻率的的感應電流,將零件表面迅速加熱(幾秒鐘內即可升溫800~1000度,心部仍接近室溫)後立即噴水冷卻(或浸油淬火),使工件表面層淬硬。(如下面動畫所示)(二)加熱頻率的選用室溫時感應電流流入工件表層的深度δ(mm)與電流頻率f(HZ)的關係為頻率升高,電流透入深度降低,淬透層降低。常用的電流頻率有:1、高頻加熱:100~500KHZ,常用200~300KHZ,為電子管式高頻加熱,淬硬層深為0.5~2.5mm,適於中小型零件。2、中頻加熱:電流頻率為500~10000HZ,常用2500~8000HZ,電源設備為機械式中頻加熱裝置或可控矽中頻發生器。淬硬層深度~10mm。適於較大直徑的軸類、中大齒輪等。3、工頻加熱:電流頻率為50HZ。採用機械式工頻加熱電源設備,淬硬層深可達10~20mm,適於大直徑工件的表面淬火。(三)、感應加熱表面淬火的套用:與普通加熱淬火比較具有:1、加熱速度極快,可擴大A體轉變溫度範圍,縮短轉變時間。2、淬火後工件表層可得到極細的隱晶馬氏體,硬度稍高(2~3HRC)。脆性較低及較高疲勞強度。3、經該工藝處理的工件不易氧化脫碳,甚至有些工件處理後可直接裝配使用。4、淬硬層深,易於控制操作,易於實現機械化,自動化。五、火焰表面加熱淬火適於中碳鋼35、45鋼和中碳合金結構鋼40Cr及65Mn、灰口鑄鐵、合金鑄鐵的火焰表面淬火。是用乙炔-氧或煤氣-氧混合氣燃燒的火焰噴射快速加熱工件。工件表面達到淬火溫度後,立即噴水冷卻。淬硬層深度為2~6mm,否則會引起工件表面嚴重過熱及變形開裂。
特點
1.加熱溫度高,而且是非接觸式加熱;
2.加熱速度快——被加熱工件的表面氧化層少,工件變形小;
3.加熱效率高——節能;
4.溫度容易控制——產品質量穩定;
5.操作簡單容易實現自動控制——省力,節省人工;
6.環保作用環境好——幾乎沒有熱、噪音、粉塵等;
7.工作占地少——生產效率高;
8.可以局部加熱——產品質量好,節能;
9.能加熱各式各樣的工件,適用面廣;
10.感應加熱可以隨時快速加熱二次變形工件,滿足工藝需求。
技術研究
現代感應加熱電源正朝著大功率,高頻化方向發展。這對現代電力電子器件來說是一個相當大的挑戰。傳統的方法是採用器件串並聯的方式,但這存在器件之間均流均壓閒難的問題,特別是當器件串並聯很多時,則需要保證精確的同步信號,以避免器件之間的環流損壞電力電子器件。但在很多情況下這很難精確保證。特別是當串並聯器件較多功率等級很大時,它的優良特性可有效地減少逆變橋並聯之間的環流,通過參數設計可以均衡各橋的功率分配,降低器件的損耗,從而有效地解決了逆變橋並聯中出現的一些問題,有利於感應加熱電源多橋並聯,提高輸出功率和可靠性。
電壓型LLC負載拓撲如圖1所示。由圖1可知,不同之處是在以往LC並聯負載基礎上再串聯一個電感L1,L2和R為感應圈的等效電路,通常L1比L2大很多,L1參與諧振並起到隔離負載和電源,調節功率分配的作用。可見它與傳統感應加熱電源中的負載匹配變壓器作用很相似,因而可以消除造價昂貴,效率不高的高頻變壓器,使得整個裝置的體積縮小、重量減輕。LLC諧振電路阻抗表達式為由基本的電路分析可得它有兩個諧振頻率,一個是並聯諧振頻率f0和一個串聯諧振頻率f1式中:Leq=L1//L2。
定義k=L1/L2,一般來說k值較大以滿足負載匹配的要求,因此f0與f1很接近。為了獲得較大功率以及控制系統設計方便,系統的理想工作點在f1。Q=L2ωo/R≈L2ω1/R為了負載的品質因數{Q》1),將k》1,Q代入式(1),則在諧振點有由式(3)可知在ω1、點電源工仵在感性狀態以保證開關管可靠換流,且電容上電壓滯後逆變器輸出電壓90°。可以證明在ω1點為輸出功率最大值。由式(4)可看出電感L1起到阻抗變換,功率調節作用。系統功率曲線以及阻抗特性曲線如圖2所示。
從圖2中可以看出φ(ω)在整個頻域內是非單調函式,這種特性不利於用鎖相環控制.相反θ(ω)=arg(vc/v1)卻呈單調變化特性,且在ω1點有θ(ω1)≈-90°,所以.θ(ω)可作為控制變數引入到PLL中,從而鎖定在諧振點。電容上電壓最大值出現在諧振點ω1。vc≈v1Q/k(5)
2感應加熱並聯模組環流分析
LLC諧振負載最大的優點是有利於感應加熱中的多機並聯,它不需要在逆變器之間附加任何元件,即使各橋的信號延時角度很大也能保證系統止常工作,抑制各橋之間的環流,調節各逆變器的輸出功率,多機並聯圖所示。
未來特性
隨著感應熱處理生產線自動化控制程度及電源高可靠性要求的提高,必須加強加熱工藝成套裝置的開發。同時感應加熱系統正向智慧型化控制方向發展,具有計算機智慧型接口、遠程控制和故障自動診斷,小型化,適合野外作業,高效節能等控制性能的感應加熱電源系統正成為未來的發展目標。