意義
在鍛造生產中,為進一步提高模鍛件的精度和降低表面粗糙度,通常是採用精壓的方法。精壓就是通過對鍛件金屬的少量擠壓,獲得良好的尺寸精度和表面質量。精壓可以部分或全部代替切削加工。一般精壓鍛件的尺寸精度,其公差可達到±0.25mm,經過多次精壓可達到±0.10mm,表面粗糙度一般可降低到0.8~1.6μm。由於通過對鍛件的精壓,使得鍛件表面層硬化,從而提高了零件的耐磨性。顯而易見,精壓提高了勞動生產率,降低了生產成本,具有良好的經濟效益。
鍛件及可行性工藝分析
圖2所示鍛件是為國外公司新開發的鍛件毛坯件,材料為DIN41Cr4(GB40Cr),硬度為HB255~296。日產量為2000件左右,兩端的尺寸精度、形位公差和表面粗糙度要求高於GB12362-90(Steeldieforgings–Tolerancesondimensions)鋼製模鍛件尺寸公差標準。鍛件圖如圖1所示。
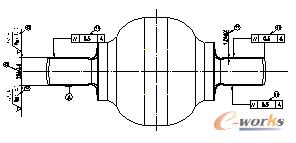
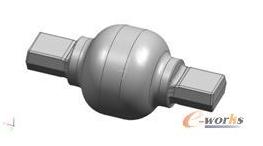
針對此鍛件兩端局部表面粗糙度要求Ra≤12.5,四個面相對的平行度小於0.3mm,鍛件的厚度要求控制在在±0.5mm以內。分析此鍛件的特殊技術要求,初步有兩種可行性工藝方案:①、四端平面機加工,但鍛件設計時,增加兩端四平面機加工餘量。②、採用兩端平面的冷精壓工藝。從降低鍛件批量生產和工裝模具製作成本為基本出發點,首選冷精壓工藝,不但提高了勞動生產率,降低了生產成本,可為公司帶來可觀的經濟效益。
設備選型及其精壓模具的設計:
精壓可以在精壓機、曲柄壓力機、摩擦壓力機或模鍛錘等鍛壓設備上進行(精壓應在精壓機或強有力的機械壓力機上進行)。首先要計算鍛件精壓時所需壓力的確定:精壓時,一般變形速度較低,變形量也較小,其所需的壓力主要與變形材料的力學性能、變形溫度、變形物體與工具接觸面之間摩擦及受力狀態等有關。其所需壓力可按下列公式作近似估算:
P=ρ.F①
①式中P―所需的精壓力(N);
F-鍛件的精壓投影面積(cm2);
ρ-平均單位壓力(MPa)
對於矩形零件:

②式中:σs―精壓材料的屈服點;(請查閱有關手冊)
μ―摩擦係數,對於無潤滑劑與拋光的精壓壓板可取0.1~0.15;(請查閱有關手冊)
a和b―矩形零件底面的短邊和長邊。
也可以根據經驗,各種材料在冷精壓時的平均單位壓力可查表①。對於熱精壓時,根據精壓的溫度,其所需要的平均單位壓力可取為冷精壓的30%~50%。通過對此鍛件所需的精壓力計算,並結合公司現有生產設備。冷精壓設備選定為300T摩擦壓力機。
表①各種材料精壓時的平均單位壓力(MPa)(摘自《最新鍛造工藝技術、質量檢測與標準規範實務全書》)
在考慮精壓模設計時必須考慮到影響精壓精度的因素:①、精壓變形的特點:冷精壓時由於精壓面中心部分的金屬流動困難,壓應力的分布極不均勻,中心高,邊緣低,使得精壓模模板與精壓件都產生不均勻的彈性變形,其拱起值f可達到0.3~0.5mm。②、影響拱起值f的因素:⑴、精壓件材料的力學性能強度越高,拱起值f也就越大;⑵、與精壓件受壓面的尺寸D與高度H之比,隨著D/H之比增加,拱起值f也增大。⑶、精壓變形量越大,拱起現象越嚴重;⑷、精壓模材料的硬度高,則彈性變形量小,拱起現象不嚴重。所以採用淬硬性高的材料做精壓模,淬火後模板硬度在HRC58~62或更高一些。故採用Cr12MoV製作精壓模。
精壓件精壓餘量必須在鍛件設計中必須考慮:精壓餘量按零件的表面粗糙度、尺寸精度、幾何形狀、尺寸和材料等綜合因素來確定。精壓餘量請參見表②,精壓公差件參見表③。
表②精壓餘量(mm)(摘自《鍛壓手冊》)
高度方向尺寸(即施壓方向) | 單面餘量值 |
<10 | 0.3 |
10~20 | 0.5 |
>20 | 0.7 |
表③精壓件公差(mm)(摘自《鍛壓手冊》)
精壓表面的水平投影面積(mm2) | 一般精度精壓 | 超精度精壓 |
<1000 | ±0.15 | ±0.08 |
1000~2000 | ±0.20 | ±0.10 |
>2000 | ±0.25 | ±0.15 |
精壓模的尺寸精度與加工表面粗糙度是根據鍛件精度要求來定。一般模具製造尺寸精度取鍛件尺寸公差的一半,局部地方為其公差的四分之三,表面粗糙度為0.2µm以下。
實際生產中使用效果
鍛件精壓工藝安排在表面清理(拋丸處理)工序之後,但精壓前需進行磷化處理或潤滑處理(因考慮到生產成本,實際生產中沒有對被精壓件進行行磷化處理或潤滑處理,而是通過提高精壓模具型腔的表面粗糙度Ra≤12.5)。精壓後鍛件檢測結果參見表④:
表④精壓後鍛件檢測結果
檢測結果 | 檢測設備 |
1、精壓表面粗糙度Ra≤6.3 | 粗糙度檢測儀 |
2、四個面相對的平行度小於0.3mm; | 三坐標測量儀 |
3、鍛件的厚度公差在±0.3mm以內; | 遊標卡尺 |
精壓後鍛件請參見圖7、圖8
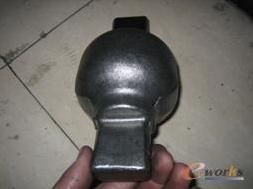
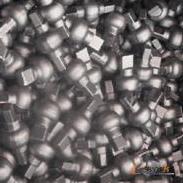
成果
該精壓工藝實踐驗證成功,精壓模設計合理,現已批量生產。精壓模使用壽命能達到30000件左右,每班次可生產2000件左右。精壓後尺寸精度、平行度及表面粗糙度均符合技術要求,滿足工藝要求,模具結構簡單,更換方便。不但降低了生產成本,而且大大提高了生產效率。
參考文獻:
【1】《鍛壓手冊》機械工業出版社出版中國機械工程學會鍛壓學會編
【2】《最新鍛造工藝技術、質量檢測與標準規範實務全書》李金苑王汝寧編當代中國音像出版社
【3】《GB12362-90鋼質模鍛件公差及機械加工餘量》出自《中國機械工業標準彙編》中國標準出版社、全國鍛壓標準化技術委員會編中國標準出版社