個人履歷
清華大學工商管理碩士,現場精益管理與班組建設實戰專家。精益管理方面,精益生產、TPM設備維護保養、IE工業工程、成本管控、KYT與現場安全零事故活動、6S、可視化管理、QC小組等現場精益改善活動諮詢顧問、資深培訓師。
班組建設方面,進行五型四化班組建設、TWI、班組長勝任力提升培訓。
畢業於清華大學經濟管理學院與麻省理工斯隆管理學院聯合培養國際工商管理碩士。具有國際化視野和雄厚的理論功底。
在韓資電子企業任職近十年,歷任車間主任、生產經理、生產總監,有豐富的企業現場管理實戰經驗。
作為諮詢顧問,輔導企業推進TPM全員參與設備維護活動、現場作業標準化與訓練體系建設、QC小組活動、改善提案活動、KYT與現場安全零事故活動、6S與可視化管理等,並採用六西格瑪實施關鍵流程DMAIC工具進行現場改善活動。通過豐富而專業的輔導經驗幫助客戶取得了良好效益。
擁有清華大學碩士研究生教育經歷、韓資企業管理實戰經驗、諮詢顧問現場輔導經驗,使得宋文強成為同時具有雄厚理論功底和豐富實戰經驗的現場改善專家。

個人著作
宋文強著有《現場精細化管理(圖解版)》、《圖解TPM管理實務(案例實踐版)》、《圖解6S管理實務》等現場管理實戰書籍。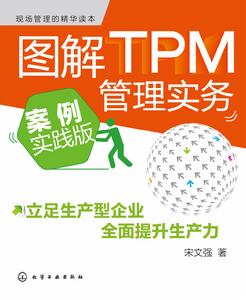
個人文章
宋文強的專欄文章請參見:“中國現場改善網”中的“宋文強專欄”。專長方向
1、班組建設與現場綜合管理類課程:如何建設五型四化班組
班組長如何提升管理勝任能力
TWI--基層主管現場管理技能訓練
現場(班組)精細化管理八大利器
2、精益生產類課程:
精益生產實戰技法訓練
單元生產與現場作業精益改善
JIT準時化生產與準時化精益物流
現場浪費改善與成本管控實務
IE工業工程—現場效率提升七大手法
自働化-防錯法與精益安燈系統套用實務
3、現場精益管理基礎類課程:
(1)質量管理類
挑戰零缺陷--TQM與現場質量管理實務
QC小組實戰演練十二周
(2)設備管理類
實現零故障--設備點檢與預防性維修保養管理實務
TPM--全員參與設備維護實戰訓練
(3)安全管理類
現場安全管理實務--本質安全與行為安全
KYT與現場(班組)安全零事故活動實戰
(4)現場基礎管理類
6S--現場精益管理的基礎
可視化管理—打造一目了然的現場
工作方式
1、培訓時,課程內容以現場管理實戰技能為主,學員分組以進行討論、練習。內容中包括大量案例、練習、討論、問答互動等。將案例講解、課堂討論、課堂練習結合。每門課程都備有課後試題和課後套用作業。課後考試用以了解學員對課程了解程度。還可以起到督促學員學習的作用。如果要更好地了解學員的學習效果,那就要進行課後實踐套用。課後套用作業主要是課程內容關鍵點的實戰套用。這些課題要求學員在工作崗位進行運用,以便於鞏固所學課程內容。
課程內容採用“模組化設計”,客戶可以根據具體需求進行“選單式選擇”,將各種模組組合在一起進行訓練。
2、諮詢時,利用在現場管理和諮詢方面的多年經驗,採用診斷、分析、培訓、輔導諮詢、確認效果這種閉環管理的諮詢方式,不僅幫助企業進行現場改善,更幫助企業提升觀察現場問題、分析現場問題、解決現場問題的意識與能力。授人以魚,更授人以漁。
服務過的企事業單位
汽車、機械:天津一汽豐田、北京賓士、北汽福田、北京現代摩比斯、中國第二重型機械集團、北京星航機電設備、上海星客特、重慶水泵廠。電子、醫療器械:無錫希捷、天加中央空調、富電電子公司、深圳瑪斯蘭電路科技公司、瑞奇外科。
鋼鐵:承德鋼鐵、無錫興澄特鋼、唐山九江線材、山西中陽鋼鐵。
電廠、電力:華能四川水電、國華電力滄東公司、內蒙古電力、青海電力、中核集團太原新能、九江電廠、山東膠州電力、河北滄州電力、浙江縉雲電力。
食品、化工、材料加工:五糧液酒業集團、中海油採油工程研究院、山東海科院、中航三鑫、濟南力諾集團、天津日石潤滑、山東天一化學、北京冶金正源公司、九江焦化。
服裝、紡織、皮革:廣州歌莉婭、河北聖侖集團、山東同大海島新材料。
菸草:貴州中煙、湖北菸草公司、武漢捲菸集團、河南菸草公司等。
建築:青海天和路橋建設公司。
航空、物流:首都機場、五礦集團國際貨運公司。
著作內容介紹
《圖解TPM管理實務(案例實踐版)》
簡介圖書作者:宋文強。
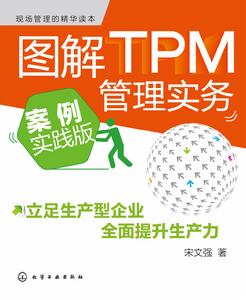
本書重點介紹TPM三大支柱:自主維護、專業維護、設備效率改善。其中:第二章、第三張、第四章介紹如何自主維護活動;第五章、第六章介紹如何開展專業維護活動;第七種介紹如何開展設備效率改善活動。
為了讓讀者能夠很好地了解TPM活動的各種工具、手法,並能迅速在企業管理當中套用TPM這一管理利器,本書共配有八十多張圖、近九十張表格供學習參考。同時,為了便於讀者了解TPM活動推進全貌,本書在第九章利用整個章節比較全面地介紹了一個企業推進TPM活動的各個方面;在每章的最後一節提供一個案例,這可以加深對本章內容的理解;有幾十個小案例點綴全書。
宋文強
圖解TPM管理實務(案例實踐版)目錄
第一章 TPM:全面生產性維護
1.1 TPM:全員、全效率的生產性維護
1.2 加強設備維護,提升生產進度、質量、成本和安全
1.3 控制小缺陷,預防大故障
第二章 自主維護:全員參與,及時維護
2.1 TPM的核心:操作員工自主進行設備維護
2.2 開展自主維護,及時發現和消除小缺陷
2.3 案例:海爾如何推進全員參與TPM活動
第三章 分步實施,自主維護七步驟
3.1 第一步:設備清掃訓練,啟動初期清掃
3.2 第二步:制訂清掃規範,落實設備規範化清掃
3.3 第三步:改善污染髮生源和清掃困難部位
3.4 第四步:開展OPL活動,進行總點檢培訓與演練
3.5 第五步:制訂設備維護規範,開展設備自主維護
3.6 第六步:點檢與維護可視化、效率化
3.7 第七步:全員參與現場改善,自主維護常態化
3.8 案例:南山鋼鐵設備TPM自主維護實施辦法
第四章 穩紮穩打,紮實推進全員自主維護活動
4.1 TPM周例會,每周一次PDCA循環
4.2 階段性診斷,步步為營推進自主維護
4.3 案例:東華機械TPM活動診斷驗收過程簡介
第五章 推進設備專業維護,提升設備可靠性
5.1 第一步:開展設備專項培訓,提升專業維護能力
5.2 第二步:完善專業維護標準體系,規範專業維護
5.3 第三步:實施設備專業點檢,及時發現故障缺陷
5.4 第四步:推進設備維護保養:潤滑,緊固調整更換
5.5 案例:北海鋼鐵公司專職點檢員小張的一天
第六章 加強設備故障分析與改善,實現設備零故障
6.1 設備故障管理:故障搶修、分析與改善
6.2 MTBF分析:確定設備可靠性與檢修維護重點
6.3 PM分析:改善重複性故障與慢性故障
6.4 Why-Why分析:簡單實用的故障分析方法
6.5 案例:南方電氣公司設備故障分析流程
第七章 減少設備效率損失,提升設備綜合效率
7.1 減少設備效率六大損失,提升設備利用率
7.2 設備綜合效率OEE:TPM活動的核心指標
7.3 開展焦點改善活動,解決設備問題
7.4 焦點改善六步驟,實現PDCA循環
7.5 改善提案:參與現場改善,提升自主管理
7.6 案例:福電電子電路板清洗設備焦點改善
第八章 TPM推進要點:統籌規劃,穩步推進
8.1 強力組織,全程統一推進TPM活動
8.2 系統規劃,用計畫指引行動
8.3 領導重視,TPM是一把手工程
8.4 創造氛圍,激發員工參與TPM積極性
8.5 樣板先行,示範引導率先突破
8.6 由點到面,全面導入整體推進
8.7 檢查考核,維持鞏固TPM改善成果
8.8 全面改善,從設備系統擴展到整個生產系統
8.9 案例:福電電子經營革新的助力器—TPM活動
第九章 綜合案例:TPM,華豐汽車公司的助推器
9.1 建立組織,從上到下、層層負責
9.2 現場6S與設備清掃,奠定TPM基礎
9.3 自主保全,“我們的設備我們管”
9.4 專業保全,精確點檢、及時修復
9.5 保全可視化,提升保全效率與效果
9.6 OPL自主培訓,提升能力、素質與氛圍
9.7 創意功夫提案,以員工為中心的自主改善
9.8 焦點改善,以效益為中心的小集團活動
9.9 紅牌作戰,挖掘問題督促整改
9.10管理看板,企業管理的重要載體
《現場精細化管理(圖解版)》
圖書簡介圖書作者:宋文強。

現場情況千變萬化,但基本管理對象只有五個,就是現場管理五要素:人、機、料、法、環。
現場管理千頭萬緒,但基本管理目標只有六個:Q(質量)、C(成本)、D(交貨期)、P(生產效率)、S(安全)、M(士氣)。
如何通過有效管理人機料法環五種要素來實現QCDPSM六方面的目標呢?通過現場精細化管理。
5S、可視化兩個利器重點在於改善現場的基本環境,為現場精細化管理奠定基礎;
TPM、防錯法、KYT訓練三個利器都是從預防的角度實現機器設備“零故障”、產品質量“零缺陷”、人員安全“零事故”等三個零;
動作經濟原則是從改善動作細節的角度提升作業效率和改善交貨期;
OEC管理來源於海爾,是加強現場管控、實現PDCA循環的成功方法;
精益生產則通過消除現場七大浪費,在生產製造方面進行精細化管理。
這八大利器基本涵蓋了現場精細化管理所有方面。為了讓讀者能夠更好地理解和套用這些工具,本書舉出了幾十個大大小小的實戰性案例,並用一百多張圖片與表單清晰易懂地來介紹如何套用精細化管理八大利器。
---宋文強
現場精細化管理(圖解版)目錄
第一章 現場管理精細化:向細節要效益
1.1 四個故事引發的思考:細節決定成敗
1.2 現場管理:五大要素與六大目標
1.3 對現場進行精細化管理:精益求精
1.4 現場精細化管理的基本流程:PDCA循環
1.5 八大利器提升現場精細化管理水平
第二章 利器一:5S,夯實現場精細化管理的基礎
2.1 5S活動:讓生產現場更精細
2.2 整理:物品數量最最佳化,簡化現場管理對象
2.3 整頓:物品放置合理化,創造整潔有序的現場
2.4 清掃:現場清掃標準化,改善環境與設備
2.5 清潔:5S活動制度化,維持、鞏固5S成果
2.6 素養:5S管理習慣化,形成良好企業文化
2.7 案例:來鑫公司5S樣板區推進計畫
第三章 利器二:可視化,打造一目了然的精細化現場
3.1 地面劃線:規範化的放置與通行
3.2 標識牌:一目了然的小看板
3.3 安全可視化:醒目刺激的警示與提醒
3.4 顏色:直觀高效的辨識方法
3.5 形跡管理:精確定位的物品放置技巧
3.6 辦公可視化:提升辦公效率
3.7 案例:南海公司可視化規範與推進計畫
第四章 利器三:TPM全員設備維護,實現設備“零故障”
4.1 TPM:全員參與設備維護
4.2 TPM的核心:操作員工自主進行設備維護
4.3 第一步:設備清掃訓練,初步了解設備
4.4 第二步:制訂清掃規範,推進設備清掃活動
4.5 第三步:改善污染髮生源和清掃困難部位
4.6 第四步:開展OPL活動,進行總點檢訓練
4.7 第五步:制訂設備維護規範,開展設備自主維護
4.8 第六步:點檢與維護可視化、效率化
4.9 第七步:全員參與現場改善,自主維護常態化
4.10 案例:海爾如何推進全員參與TPM活動
第五章 利器四:防錯法,實現產品質量“零缺陷”
5.1 質量管理的核心是質量問題預防
5.2 防錯法:質量問題預防的手段
5.3 自動檢測
5.4 自動報警
5.5 自動選擇
5.6 自動定位、自動對齊
5.7 自動停止
5.8 案例:豐田汽車公司防錯法套用
第六章 利器五:KYT危險預知訓練,實現人員“零事故”
6.1 安全:消除隱患、實現零事故
6.2 KYT危險預知訓練:危險分析的班組活動
6.3 KYT課題來源:“嚇一跳、冒冷汗”事件記錄法
6.4 KYT小組討論分析四步法
6.5 KYT活動企業推進五階段
6.6 KYT行動落實:“手指口述”安全確認法
6.7 案例:寶泉電路板廠KYT活動紀實
第七章 利器六:動作經濟原則,提升現場作業效率
7.1 動作改善的故事:吉爾布雷斯與砌磚
7.2 動作經濟原則:改善動作,提升效率
7.3 人體動作改善五原則,動作改善的基礎
7.4 工裝夾具改善二原則,減少疲勞、提升效率
7.5 作業環境改善二原則,科學布局、身心舒適
7.6 案例:UPS 公司如何辦理辦理最快捷的運送?
第八章 利器七:OEC管理,實現日常管控的精細化
8.1 海爾OEC管理法:日事日畢,日清日高
8.2 OEC管理法三大體系之一:目標體系
8.3 目標體系的工具:總帳、分類帳、明細賬
8.4 OEC管理法三大體系之二:日清控制體系
8.5 日清控制體系的工具:日清欄、3E卡、日清表
8.6 OEC管理法三大體系之三:激勵體系
8.7 激勵體系的工具:SST(索酬、索賠、跳閘)機制
8.8 OEC管理的每日運行:一帳、三表、七步驟
8.9 案例:OEC管理法在海爾冰櫃質量管理中的套用
第九章 利器八:精益生產,精細化的生產製造
9.1 從“豐田生產方式”到“精益生產”
9.2 消除七大浪費,實現精益生產理念
9.3 拉動式生產:適時適量適物
9.4 看板:拉動式生產的典型工具
9.5 流線化生產:實現精益生產的布局方式
9.6 單元式生產布局:流線化生產的最佳套用
9.7 案例:佳能公司的單元式生產方式
第十章 綜合案例:華豐汽車公司精細化管理紀實
10.1 5S管理為現場自主管理奠定基礎
10.2 可視化助力現場全方位精細化管理
10.3 拉動式生產與看板(Kanban)系統實現零庫存
10.4 U型單元式生產布局提升生產柔性
10.5 安燈(ANDON)等自働化防錯法降低產品不良
10.6 全員參與TPM,“我們的設備我們管 ”
10.7 作業動作最佳化提升作業效率
10.8 “創意提案活動”帶動全員參與現場改善
10.9 KYT危險預知安全活動促進安全生產零事故
《圖解6S管理實務(中國實戰版)》簡介
圖書簡介圖書作者:宋文強。
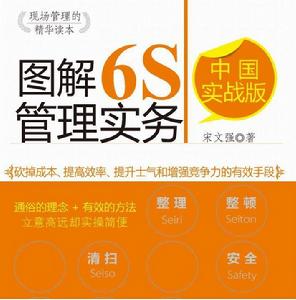
中國是一個製造業大國,改革開放以來,尤其是進入二十一世紀以後,中國製造的風潮席捲世界。“Made in China”的標籤布滿全球。而對於製造型企業來講,6S管理已經成為現場管理模式的代名詞。
在日本,5S管理作為經濟騰飛的兩大工業法寶之一被格外推崇;在我國,5S作為企業現場管理的傑出手段,被越來越多的企業認知、認可,並逐步形成具有中國本土特色的6S管理體系。6S逐漸成為中國企業基礎工作中不可或缺的組成部分,無論是在生產現場還是在辦公室,6S都是提升工作效率、降低成本、減少浪費、提高士氣和增加競爭力的有效手段。
6S管理沒有什麼太深奧的理論,所用工具、方法也都簡單易行,但是,要求在推進過程中細緻入微和持之以恆。
筆者曾經在韓資企業從事生產管理工作近十年,受6S精神的薰陶與影響非常深。後來又從事生產現場管理的改善輔導與培訓工作。在這過程中,一方面為能為幫助企業推行6S感到高興,同時,也為許多國內企業在系統推進6S管理方面不得要領而感到遺憾。
因此,筆者萌發了與更多企業同仁分享6S知識與經驗的想法。現在,將多年的實戰經驗以及這過程中使用的各種工具、方法、表單等進行系統匯總,編寫成本書。
筆者希望通過易懂實用的本書能為企業在構築6S的大廈時既能打下堅實基礎又能添磚加瓦、更上一層樓。
本書主要以層層遞進的6個S(整理、整頓、清掃、安全、清潔、素養)為軸線,對每個階段的活動內容進行詳細介紹,具體包括:每階段的活動推進步驟、所用工具與方法;每階段會遇到問題與解決對策。對於每個階段,都配有許多實戰性案例,並且用大量的圖片和表單清晰易懂地來介紹如何推行6S活動。書的最後還分析了企業全面推進6S的實施要點以及誤區分析。
本書可供企業的管理人員、現場人員、諮詢顧問、培訓師作為實戰參考或培訓教材。
書中若有一些錯誤或不妥之處,希望廣大讀者諒解並懇請給予指正。
---- 宋文強
圖解6S管理實務(中國實戰版)目錄
第一章 6S概論
1.1 6S活動:現場管理的基礎
1.2 推行6S,讓生產現場更卓越!
第二章 第一個S:整理
2.1 整理:區分必要物與不要物
2.2 現場檢查:老鼠蟑螂檢查法、下班後檢查法
2.3 確定不要物標準:使用頻率、抽屜法則
2.4 處理不要物:設立暫存區和再利用區
2.5 整理階段的核心工具:紅牌作戰
2.6 整理階段的存在的問題及其解決對策
2.7 案例:東方汽車製造公司“6S整理”活動
第三章 第二個S:整頓
3.1 整頓:整齊放置、清晰標識
3.2 定置管理:定數量、定位置
3.3 立體放置:節省空間,方便取用
3.4 定容放置:整齊、高效
3.5 形跡管理:一目了然、容易歸位
3.6 先進先出:最佳化存貨,快速存取
3.7 整頓階段存在的問題及其解決對策
3.8 案例:南海公司工具箱整理整頓的行動方案
第四章 第三個S:清掃
4.1 清掃:讓工作現場與作業設備乾淨明亮
4.2 清掃責任制:公開宣示
4.3 清掃標準:清掃作業指導書
4.4 清掃環境:不留死角,隨時打掃
4.5 擦拭機器設備:邊清掃邊檢查設備狀況
4.6 清掃用具:整齊放置、觸手可及
4.7 檢查清掃結果:關注細節與角落
4.8 改善污染髮生源:從源頭治理
4.9 清掃階段存在的問題及其解決對策
4.10案例:海爾的白襪子、白手套
第五章 第四個S:安全
5.1 安全:消除隱患、預防事故
5.2 海因里希法則:小錯不斷、大錯必犯
5.3 安全檢查:找到問題,進行整改
5.4 安全可視化:醒目刺激,危險警示
5.5 安全事故分析:前車之鑑,後車之師
5.6 KYT危險預知訓練:發現危險,尋找對策
5.7 安全階段存在的問題及其解決對策
5.8 案例:檯燈、火災與輪船沉沒
第六章 第五個S:清潔
6.1 清潔:用制度化帶動常態化
6.2 制訂標準:推進標準、檢查標準
6.3 自我檢查:自查自糾,主動改進
6.4 巡視檢查:隨時巡視,及時整改
6.5 評比檢查:為了評比考核進行定期檢查
6.6 檢查評比的評分方法:追求公平合理
6.7 定點攝影:用圖片說話,視覺衝擊效果好
6.8 6S管理看板:6S管理的可視化
6.9 清潔階段存在的問題及其解決對策
6.10案例:麥當勞的標準化與檢查督導
第七章 第六個S:素養
7.1 素養:形成習慣並持續改善
7.2 素養形成的三階段:形式化、行事化和習慣化
7.3 員工行為準則:提升員工素養的基礎
7.4 班前會與大腳印:現場自主管理的日常化
7.5 改善提案:參與現場改善,提升自主管理
7.6 3U-Memo:改善提案的基礎性工具
7.7 素養階段遇到的問題及其解決對策
7.8 案例:從清掃到素養,環境影響心態
第八章 可視化管理:打造一目了然的現場
8.1 通過可視化實現公開化、便捷化、傻瓜化
8.2 顏色:直觀認知,高效辨識
8.3 劃線:沒有規矩,不成方圓
8.4 標識牌:小型看板,一目了然
8.5 形跡管理:精確定位,整齊明晰
8.6 燈號:異常警示,衝擊力強
8.7 對齊管理:迅速發現異常
8.8 可視化管理逐步提升的四個層次
8.9 可視化管理遇到的問題及解決對策
8.10案例:南海公司可視化規範與推進計畫(部分)
第九章 6S實施要點:全員參與,穩步推進
9.1 成立組織,統一推進和輔導
9.2 領導重視,要體現在行動上
9.3 鼓勵員工參與,讓員工感受到好處
9.4 制訂計畫與方案,不盲目突進
9.5 宣傳推廣和教育培訓,充分了解6S
9.6 選擇樣板區率先突破
9.7 全面導入時既要統一又要變通
9.8 通過檢查評比實現6S活動常態化
9.9 從整齊亮麗型6S到改善型6S
9.10持續改善、不斷深化
第十章 6S十大誤區及其分析
10.1誤區一:領導與員工都很忙,沒時間做6S
10.2誤區二:公司員工素質低,不願意主動參與6S
10.3誤區三:通過罰款才能迫使員工全力工作
10.4誤區四:6S就是大掃除,沒必要興師動眾
10.5誤區五:公司早就做過6S了,沒有什麼好的效果
10.6誤區六:6S活動只花錢不賺錢
10.7誤區七:6S只是搞形式,沒有實質性作用
10.8誤區九:我們搞得挺好,沒必要搞6S
10.9誤區八:6S能“包治百病”
10.10誤區十:6S能立竿見影、速戰速決