低碳電工鋼和阿姆科鐵
正文
1886年美國西屋(Westinghouse)電器公司用雜質含量約為0.4%的鋼板,製成變壓器疊片鐵芯。1890年已廣泛使用0.35mm厚的熱軋低碳鋼薄板,製造電機和變壓器鐵芯。低碳鋼板由於電阻率 (ρ)低,鐵芯損耗(鐵損)大,碳、氮含量還不夠低,磁時效嚴重,到1906年已陸續被矽鋼片所代替。1910年美國 Armco鋼公司首先用鹼性平爐冶煉成碳及其他雜質含量都比低碳電工鋼為低的阿姆科鐵(Armco iron),因為阿姆科鐵的產量在工業純鐵中占的份額最大,一般說“工業純鐵”即指阿姆科鐵。50年代末由於氧氣頂吹轉爐和真空冶金等冶煉新技術以及連續爐濕氫脫碳退火技術的出現,低碳鋼中的氧、氮含量降低到50ppm以下,磁時效明顯減輕。此時美國又開始大量生產低碳電工鋼(AISI1008和1010,含碳0.08~0.10%),用經一次冷軋和連續爐脫碳退火製成厚0.50或0.65mm的“低碳電工鋼板”製造家用電器中的微電機等。現在美國和日本的低碳電工鋼板產量已接近矽鋼片的產量。中國於1955年開始生產阿姆科鐵,1964年製成無時效的鋁鎮靜阿姆科鐵,1975~1980年試製成含碳0.010~0.025% 的高氣密性阿姆科鐵。1981年開始生產低碳電工鋼板。
成分和性能 低碳電工鋼和阿姆科鐵的飽和磁感應強度(Bs)和居里溫度(770℃)都高,矯頑力(Hc)則較低,磁導率也較高(表1和表2),機械加工性和焊接性良好,製造工藝簡單。它們的主要缺點是電阻率低、並且容易產生磁時效。
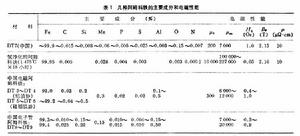
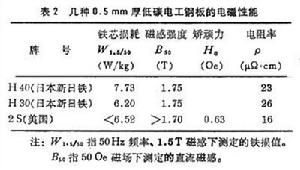
碳、氮、氧和硫對鐵的磁性產生很壞的影響。它們使鐵的晶格嚴重畸變,引起很大的應力,使矯頑力和磁滯損耗明顯升高(圖1和圖2)。碳和氮還會引起磁時效(圖3)。
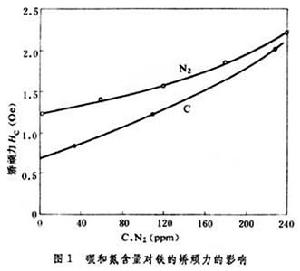
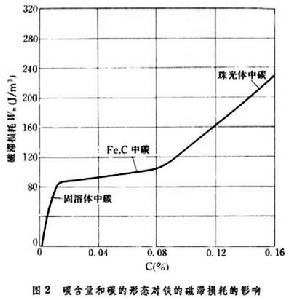
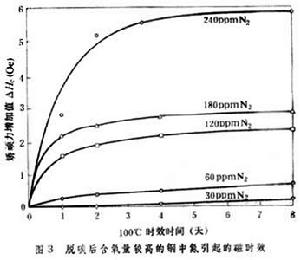
低碳電工鋼板 主要用於製作微電機、小電機、鎮流器和繼電器中的鐵芯。在微電機和小電機中因銅線引起的損耗(銅損)通常比鐵芯引起的損耗(鐵損)大 2~4倍。與普通矽鋼片相比,低碳電工鋼板有較高的磁感。用低碳電工鋼板做電機的鐵芯,電機的勵磁電流較低,銅線匝數可以減少,銅損可以顯著下降。雖然電機的鐵損較高,但電機的銅損和鐵損總損耗卻降低了。用低碳電工鋼板製成的鐵芯,體積和重量可減小15~20%,勵磁電流可降低5%,電機的功率因數提高,材料費用可降低20%。
生產工藝 70年代阿姆科鐵和低碳電工鋼主要用氧氣頂吹轉爐冶煉,並進行真空處理脫碳和加鋁脫氧。在這兩種材料的生產中,為了改善熱加工性,防止硫引起的熱脆性(900~1050℃範圍內),常加入0.3~0.5%的錳;為了防止氮引起的時效現象,加入少量的鋁或鈦;為了改善沖片性,可加入0.08~0.15%的磷。日本生產H30和H40低碳電工鋼有時還加入少量矽(Si≤0.5%)來提高電阻率(降低鐵損)和硬度,減輕磁時效。中國主要採用電爐冶煉阿姆科鐵,用電渣重熔或真空熔煉技術生產各種氣密性好的阿姆科鐵。
阿姆科鐵有熱加工產品和冷加工產品,低碳電工鋼主要為冷軋板材。阿姆科鐵和低碳電工鋼都有成品和半成品兩種產品。成品製造的工藝要點是,厚約 2.3mm的熱軋帶卷經酸洗,一次冷軋至成品厚度(主要為 0.50和0.65mm),在保護氣氛中退火(阿姆科鐵退火溫度為860~930℃,低碳電工鋼為760~820℃),使晶粒長大,矯頑力和鐵損降低,然後根據用戶要求塗絕緣層。半成品製造工藝要點是,鋼帶冷軋後經軟化退火(600~700℃),然後在鋼帶表面塗防鏽油交用戶。用戶沖剪後在保護氣氛中再進行較高溫度的成品退火。這種半成品的優點是成本低和沖片性好。這種工藝可消除沖剪應力,從而改善磁性。如果需要表面絕緣,用戶可在退火後冷到約450℃時通入水蒸汽進行發藍處理。
為了控制阿姆科鐵和低碳電工鋼的含碳量,鋼錠和連鑄坯中的含碳量一般在0.03~0.10%範圍內,冷軋後須在濕的氫氮混合氣氛中退火脫碳,將含碳量降到0.005%以下。如果鋼水經過真空處理脫碳,則應在乾的保護氣氛中退火。這能夠提高產量,避免形成內氧化層,從而獲得鐵損更低的優質材料。70年代採用某些工藝方法以改善低碳電工鋼板織構(見擇優取向)。如提高熱軋終軋溫度和卷取溫度,冷軋前將熱軋帶卷進行預退火,或在鋼中加入少量銻、錫等元素,以增加有利織構的組分,從而提高磁感應強度和降低鐵損。