概述
鐵水預處理是指鐵水進入煉鋼爐之前採取的冶煉工藝。鐵水預處理工藝始於鐵水爐外脫硫,1877年,伊頓(A.E.Eaton)等人用以處理不合格的生鐵。鐵水預脫矽、預脫磷始於1897年,英國人賽爾(Thiel)等人用一座平爐進行預處理鐵水,脫矽、脫磷後在另一座平爐中煉鋼,比兩座平爐同時煉鋼效率成倍提高。到20世紀初,由於人們致力於煉鋼工藝的改進,所以鐵水預處理技術發展曾一度遲緩。直至20世紀60年代,隨著煉鋼工藝的不斷完善和材料工業對鋼材產品質量的要求開趨嚴格,鐵水預處理得到了迅速的發展,並逐步成為鋼鐵冶金的必要環節。
傳統的煉鋼方法常將煉鋼的所有任務放在轉爐內的煉鋼工藝中去完成。但是隨著鋼鐵原料、燃料的日趨貧化,造成了這些原料、燃料中的磷、硫含量高,使得煉鋼用鐵水中初始磷、硫含量增加;另外,隨著科學技術進步的發展,用戶對煉鋼產品的質量、性能的要求越來越苛刻,這就要求鋼中的雜質含量如磷、硫含量很低才能滿足用戶的要求。而傳統的轉爐煉鋼方法,由於爐內的高溫和高氧化性,轉爐的脫磷、脫硫能力受到限制。因此為了解決這些矛盾,現代的高爐煉鐵和轉爐煉鋼之間採用了鐵水預處理工藝,對進入轉爐冶煉之前的鐵水做去除雜質元素的處理,以擴大鋼鐵冶金原料的來源,提高鋼的質量,增加轉爐煉鋼的品種和提高技術經濟指標。鐵水預處理工藝實質上是把原來在轉爐內完成的一些任務在空間和時間上分開,分別在不同的反應器中進行,這樣可以使冶金反應過程在更適合的環境氣氛條件下進行,以提高冶金反應效果。目前,鐵水預處理工藝已經發展到了很成熟的階段,先進國家的鐵水預處理比例高達90%—100%。
採用鐵水“三脫”處理能給轉爐煉鋼帶來一系列優點,如減少轉爐煉鋼吹煉過程中除去矽、磷所需的石灰造渣料,減少渣量,減少熔渣外溢及噴濺等,熔渣對爐襯的侵蝕也因之減輕,爐齡顯著提高。同時又縮短了轉爐的吹煉時間,提高了轉爐的生產率,降低了鐵損,鋼水質量也得到提高。這是轉爐採用少渣量操作帶來的優點。
分類
鐵水預脫矽
研究表明,鐵水中矽含量為0.3%即可保證化渣和足夠高的出鋼溫度,矽過多反而會惡化技術經濟指標。因此,有必要開展鐵水預脫矽處理。
脫矽劑以能夠提供氧源的氧化劑材料為主,以調整爐渣鹼度和改善流動性的熔劑為輔。如日本福山廠脫矽劑組成為鐵皮0~100%、石灰0~20%、螢石0~10%;日本川崎水島的脫矽劑為燒結礦粉75%、石灰25%。脫矽生成的渣必須扒除,否則影響下一步脫磷反應的進行。
目前鐵水預脫矽方法按處理場所不同,可分為高爐出鐵場鐵水溝內連續脫矽法和鐵水罐(或魚雷罐車)內脫矽兩種,其中高爐出鐵場是主要爐外脫矽場所。
鐵水預脫硫
除易切削鋼外,硫是影響鋼的質量和性能的主要有害元素,直接決定著鋼材的加工性能和適用性能。鐵水脫硫可在高爐內、轉爐內和高爐出鐵後脫硫站進行。高爐內脫硫技術可行,經濟性差;轉爐內缺少還原性氣氛,因此脫硫能力受限;而進入轉爐前的鐵水中脫硫的熱力學條件優越(鐵水中[C]、[P]和[Si]含量高使硫的活度係數增大,鐵水中比鋼液中高3—4倍),性價比高,成為脫硫的主要方式。
鐵水預脫磷
除易切削鋼和炮彈鋼外,磷是絕大多數鋼種的有害元素,顯著降低鋼的低溫衝擊韌性,增加鋼的強度和硬度,這種現象稱為冷脆性。
鐵水預脫磷採用的脫磷劑主要由氧化劑、造渣劑和助熔劑組成,其作用在於供氧將鐵水中磷氧化成,使之與造渣劑結合成磷酸鹽留在脫磷渣中。目前工業上使用較廣的石灰系脫磷劑以為主,配加氧化劑和助熔劑。
鐵水預脫磷按處理設備可分為爐外法和爐內法。爐外法設備為鐵水包和魚雷罐,爐內法設備為專用爐和底吹轉爐。按加料方式和攪拌方式可分為噴吹法、頂加熔劑機械攪拌法(KB)和頂加熔劑吹氮攪拌法等,目前多採用噴吹法。爐外法預處理後鐵水磷含量不應高於0.030%,轉爐內預處理後的鐵水磷含量不應高於0.01%。,若生產超低磷鋼種時,處理後鐵水磷含量不應高於0.005%。採用爐外法預脫磷,必須先進行預脫矽處理,鐵水中矽含量不應高於0.2%。
鐵水預處理提釩
釩是重要的TAk原料,我國西南、華北、華東等地區的礦石中含有釩,冶煉出的鐵水含釩較高,可達0.4%~0.6%。因此,可通過特殊的預處理方法提取鐵水中的釩。
目前,我國主要採用氧化提釩工藝進行含釩鐵水提釩,即先對含釩鐵水吹氧氣,使鐵水中的釩氧化進入爐渣,然後對富含的爐渣進行富集分離來提釩。
鐵水提釩方法有搖包法、轉爐法、霧化法和槽式爐法,德國、南非主要採用轉爐法和搖包法,我國主要採用轉爐法和霧化法。
目的
鐵水預處理是指鐵水在進入轉爐煉鋼之前,為了去除某些有害成分或回收有益成分的處理過程。針對煉鋼而言,主要是使鐵水中的矽、硫、磷含量降低到所要求的範圍,以簡化煉鋼過程,提高鋼材的質量。
在鐵和鋼的生產過程中,硫之所以成為主要脫除或控制的元素之一,是因為它對鋼的性能有著多方面的影響。
(1)熱脆:硫在鐵液中以FeS形式存在,1600℃硫在鐵液巾能無限溶解,但其溶解度隨溫度的降低而減小,在固態鐵中的溶解度很小。在鋼液凝固過程中,低熔點(1193℃)的FeS將濃聚於液相中,並將與Fe形成低熔點共晶(988℃),最後凝固時形成網狀組夠分布於鐵晶粒周界上。當鋼在熱加工的加熱過程中,溫度超過1100℃左右時,富集於晶界的低熔點硫化物將使晶界成脆性或熔融狀態,在軋制或鍛造時,即出現裂紋,這種現象稱為“熱脆”。
(2)疲勞斷裂:鋼材的疲勞斷裂是由於使用過程中鋼材內部顯微裂紋不斷擴展的結果。當硫含量偏高時產生晶界裂紋,這就是由於硫高而導致疲勞斷裂的原因。
(3)力學性能:硫化物夾雜對鋼材力學性能的影響,主要是由於硫化物夾雜在鋼材加工中易變成長條狀和片狀,因此使鋼材橫向抗拉強度及塑性大大下降,同時衝擊韌性也下降。
(4)抗蝕、焊接和切削性能:鋼中硫化物夾雜還會引起坑蝕現象。在鋼的焊接過程中,鋼中的硫化錳夾雜能引起熱撕裂。硫對鋼還有一種很好的影響,即它能改善鋼的切削性能。
工藝方法
鐵水預處理是對煉鋼用鐵水進行脫矽、脫磷和脫硫處理(簡稱為“三脫”),主要在出鐵溝、魚雷式混鐵車、鐵水包和混鐵爐中進行。
鐵水預處理工藝方法有:鐵水溝連續處理法(鋪撒法)、鐵水罐噴吹法、機械攪拌法、專用爐法、搖包法、轉鼓法、鐘罩法以及噴霧法等。
鐵水溝連續處理法:此法是一種最簡易的鐵水預處理方法,可分為上置法和噴吹法兩種。前者只需將預處理劑鋪撒在鐵水溝適當的位置,預處理劑即隨鐵水流下,靠鐵流的攪動和衝擊使預處理劑和鐵水發生反應而脫出有關雜質元素;而後者則需在鐵水溝上設定噴吹攪拌槍或噴粉槍,使預處理劑經噴吹攪拌強化與鐵水的接觸。
鐵水罐噴吹法:將預處理劑用噴槍噴人鐵水罐內的鐵水中,使其與鐵水充分反應,以達到淨化鐵水、脫除或提取有關元素的目的。鐵水罐有魚雷罐和敞口罐之分。
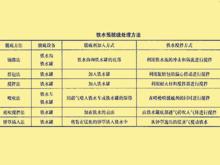
機械攪拌法:將置於鐵水表面的預處理劑通過攪拌與鐵水有效接觸的一種高效方法,這種方法多用於深度脫硫。
專用爐法:此法是用一種容量寬鬆易於控制的鐵水預處理專用設備處理鐵水,也有用轉爐作為專用爐的。
鐵水預脫硫的各種處理方法如右圖所示。
鐵水預處理劑
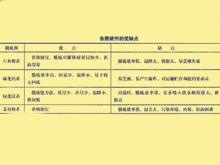

脫硫劑常用的有活潑金屬脫硫劑(金屬鎂)、碳化物脫硫劑(如電行 )、碳酸鹽脫硫劑(如蘇打)、氧化物脫硫劑(如石灰)。脫矽嗣l脫磷劑皆以氧化物為主,輔以熔劑和活化劑。氧化劑有固體氧化劑(鐵磷等)和氣體氧化劑(氧氣);熔劑主要是石灰和蘇打,起固化矽、磷等氧化物的作用,形成穩定的矽酸鹽和磷酸鹽,同時降低熔渣的熔點。活化劑是用來激化脫矽、脫磷反應的物質(如螢石和氯化鈣等),也起助熔的作用。鐵水預脫硫常用的脫硫劑有四種:石灰粉系、碳化鈣系、鈍化鎂系、蘇打粉系。各脫硫劑的優缺點如右圖所示。
目前發展了一種單吹顆粒金屬鎂的鐵水預處理脫硫方法。鐵水包單吹顆粒金屬鎂脫硫技術是為了進一步提高脫硫效率和金屬鎂的利用率,降低生產運行成本而在共吹法基礎上發展起來的新型脫硫方法,它取消碳化鈣,而單吹顆粒鎂,比混吹(鎂+石灰)節省成本,脫硫效率高,可將鐵液中S含量降至0.001%以下,脫硫劑利用率可高達95%以上。
脫硫機理:吹入鐵水的顆粒鎂經噴槍上的氣化室預熱,在噴槍出口處迅速得到氣化,並溶人鐵水。氣化上升或溶人鐵水中的鎂在載流氣體攪拌下與鐵水中的硫進行充分的接觸,發生高效的脫硫反應,從而達到最經濟的脫硫日的。


鎂在鐵液中的行為: ,經歷熔化、氣化、溶解過程。鐵水中溶解鎂與硫反應: 。
單吹顆粒鎂鐵水脫硫工藝相對於KR攪拌法脫硫工藝而言,設備用量少,基建投人低,脫硫效率更高,脫硫效果更好,鐵水溫降低,鐵損低。但是噴吹法最大的缺點是動力學條件差。有研究表明:在都使用氧化鈣脫硫劑的前提下,KR攪拌法的脫硫率是噴吹法的四倍。另外,顆粒鎂的高昂價格也限制了噴吹法的發展。