氧氣頂吹轉爐煉鋼
自50年代初投入工業生產以來,在世界範圍內得到迅速推廣,逐步取代空氣轉爐法和平爐煉鋼法,成為現代煉鋼的主要方法。最早建於奧地利的林茨(Linz)和多納維茨(Donawiz),因而亦稱LD法。在美國通常稱為BOF法。頂吹氧氣轉爐的金屬爐料主要是鐵水,約占金屬總裝料量的70~85%,其餘部分是廢鋼(個別廠採用富鐵礦或球團礦)。通過氧槍從熔池上面垂直向下吹入高壓(6~10大氣壓)的純氧(含O299.5%以上),氧化去除鐵水中的矽、錳、碳和磷等元素,並通過造渣進行脫磷和脫硫。各種元素氧化所產生的熱量,加熱了熔池中的液態金屬(從鐵到鋼),使鋼水達到規定的化學成分和溫度(圖1)。
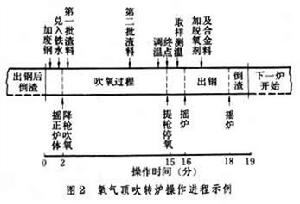
槍位 操作槍位是指噴頭端面到靜止熔池金屬液面的距離。由於氧氣射流隨射程增長而速度逐漸衰減,所以調整槍位可以控制射流對熔池的衝擊力和衝擊面積。在吹煉中熔池運動狀況對雜質的氧化成渣、金屬成分、溫度、噴濺和爐齡等都有很大影響。由冷態模型實驗可看出,氧氣流股對熔池的作用有兩種狀況:
① 淺吹或軟吹 當槍位高或氧壓低時,氧氣射流的動能較小,只能在熔池表面衝擊出一個“淺坑”,由於凹坑表面反射氣流的作用, 帶動附近的金屬液向上運動,導致離凹坑較遠處的金屬液向下運動。這種狀況稱為”淺吹”或“軟吹”(圖3)。
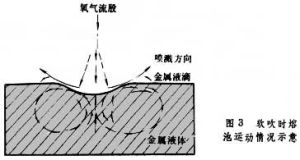
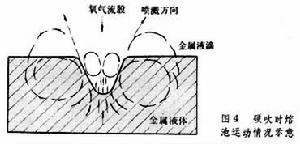
調節氧氣射流對熔池的作用狀態,如調整氧槍噴口和液面的相對位置,是控制氧氣頂吹轉爐吹煉過程的重要手段。
吹煉中金屬和爐渣成分的變化 氧氣頂吹轉爐吹煉時,由於一次反應區的溫度很高,吹煉初期鐵水中的碳就會被氧化。又由於氧氣頂吹轉爐能調整氧槍槍位,有效地控制成渣狀況和渣中氧化鐵含量,從而能在脫碳的同時進行脫磷,這是氧氣頂吹轉爐區別於底吹轉爐的重要特點。吹煉過程中金屬熔池和爐渣的成分變化例示於圖5。
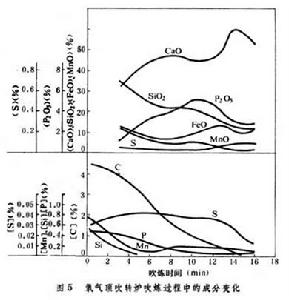
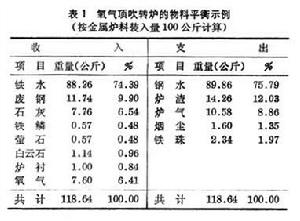
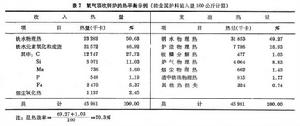
過程控制 氧氣頂吹轉爐煉鋼的冶煉周期短,需要控制和調節的參數相當多。加上冶煉的鋼種日益增多,對質量的要求越來越高;爐子的容量也不斷增大,單憑操作人員的經驗來控制,已不能適應需要。套用電子計算機於氧氣頂吹轉爐的過程控制,能對冶煉的各種參數,進行快速、準確的計算和處理,給出所需的綜合結果,指出合理的操作方式和內容,可以進行自動控制。
計算機靜態控制 採用計算機控制轉爐吹煉,早期都為靜態控制;就是通過模擬煉鋼工的操作經驗,或者根據物料平衡和熱平衡建立起的數學模型,按照吹煉時間或者按分配的氧量(中途不調整參數)完成預定的操作程式。其控制的基本原則如圖6。
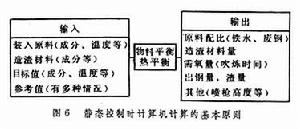
計算機動態控制 動態控制的終點目標命中率要比靜態控制高得多,通常為85~95%。實現計算機動態控制的關鍵在於能有一個取得吹煉中間信息的良好測試手段。目前已有多種能夠檢測中間信息的方法,諸如爐氣定碳等。但是,真正廣泛用來配合動態控制的測試手段為轉爐副槍。即在氧氣頂吹轉爐氧槍旁邊,另安裝一根可隨時升降的水冷槍。副槍本身包括:槍身(由三層不同半徑的鋼管組成)、傳動設備、探頭、自動更換探頭的裝置和副槍動作的程式控制系統等。測溫由位於探頭下部的熱電偶進行,定碳由探頭內的一個樣杯,用結晶定碳法實現。副槍上安裝的探頭每次使用後,即行更換。副槍可在吹煉過程中進行測定工作。副槍測出的數據直接送入電子計算機,進行計算,由計算機自動調整和控制各種操作參數。
目前在實際生產中套用的計算機控制吹煉的方法,多為副槍點測和靜態、動態相結合的控制方法。靜態控制主要用於吹煉的前半期,此時由於熔池中碳、矽、磷濃度比較高,吹入爐內氧氣幾乎全部用於氧化這三個元素,氧的分配率可以掌握。因此,靜態控制在此階段中,能有較高的精確度。但是,到了吹煉的後半期,碳、矽、磷三元素濃度減小,有一定數量氧氣,被消耗於鐵的氧化,氧的分配率不能掌握,以致溫度和碳偏離控制軌道。因此,在後期需要採用動態控制。大約在距終點前 3分鐘左右,下降副槍取得溫度和碳的信息,通過計算機運算,適當添加冷卻劑並調整吹入氧量,糾正偏離的軌道,從而命中終點目標。從某種意義上說後期階段的動態控制,實際上也是變相的短時間靜態控制(圖7)。
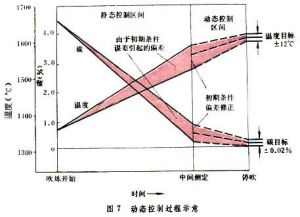
轉爐的冶煉時間短,出鋼次數頻繁,必須在布置上儘可能減少各操作工序相互干擾,因此組成跨間數目較多(一般為3~4個)。近年採用連續鑄鋼,使組成跨間有進一步增多的趨勢。轉爐兌鐵水和加廢鋼操作,均在裝料跨內進行。為了避免干擾,有關設備分別布置在裝料跨的兩端。鐵水經混鐵爐或混鐵車傾入開口鐵水包,並用吊車從一端運向轉爐;廢鋼則從另一端裝槽並吊運至轉爐。根據轉爐容量大小,設定一個或兩個澆鑄跨。在澆鑄跨內布置鑄錠列車線或連鑄設備。脫模、整模操作或鑄坯冷卻、堆存,在相鄰跨間內進行。氧氣頂吹轉爐車間的典型布置見圖8。
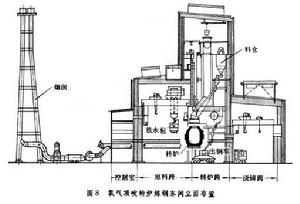
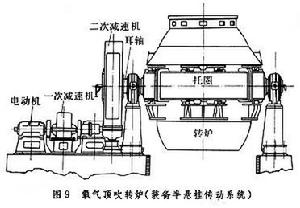
冶煉時間30分鐘
其中:吹氧時間 18~20分鐘
氧氣消耗48~58標米3/噸
鋼鐵料消耗 1096~1150公斤/噸
廢鋼比 20~30%
石灰消耗(包括白雲石) 60~70公斤/噸
螢石消耗1.5~3.0公斤/噸
鐵礦石消耗 30~50公斤/噸(高鐵水比時)
爐襯消耗3~7公斤/噸
電耗9~12千瓦·時/噸
轉爐單位公稱噸年產鋼 10000~15000噸
參考書目
R.D.佩爾克等著,邵象華、樓盛赫等譯校:《氧氣頂吹轉爐煉鋼》,冶金工業出版社,北京,(上冊)1980,(下冊)1982。(R.D.Pehlke,ed., BOF Steelmaking,AIME,1974~1977.)