簡介
電弧爐煉鋼通過石墨電極向電弧煉鋼爐內輸入電能,以電極端部和爐料之間發生的電弧為熱源進行煉鋼的方法。電弧爐以電能為熱源,可調整爐內氣氛,對熔煉含有易氧化元素較多的鋼種極為有利,發明後不久,就用於冶煉合金鋼。並得到較大的發展。隨著電弧爐設備的改進以及冶煉技術的提高,電力工業的發展,電爐鋼的成本不斷降低,現在電爐不但用於生產合金鋼,而且大量用來生產普通碳素鋼,其產量在主要工業國家鋼總產量中的比重,不斷上升(見表)。
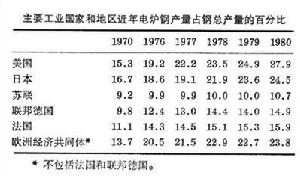
中國在20年代以後,一些主要工業城市陸續建了一些小電爐,直到1950年後才有較快的發展,主要用於生產優質鋼和合金鋼。1980年產量約占鋼總產量的20%,最大的電弧爐容量為50噸。
原料
電爐鋼以廢鋼為主要原料,有些電弧爐採用直接還原的海綿鐵來代替部分(30~70%)廢鋼。廢鋼經多次循環冶煉,會使某些對鋼質有害而又不能在冶煉過程中除去的元素(如銅、鉛等)富集。海綿鐵比廢鋼純淨得多,摻和使用就可起“淨化”的作用。冶煉合金鋼時,大多數採用成分相近或相應的合金廢鋼為爐料,以節約昂貴的鐵合金,不足之數在冶煉過程中再用鐵合金補充。
冶煉工序
補爐
上一爐的鋼水和渣出淨以後,立即把被侵蝕的爐襯補好。補爐動作要快,以便利用爐內的殘餘高溫,將補爐料和原爐襯燒結在一起,並可減少熱損失,節約電能。
裝料
補爐完畢後,移開爐蓋,用料筐從爐子頂部把爐料裝入爐內。不易氧化和難熔的合金料如鎳、鉬等可與廢鋼同時裝入。爐料的塊度應適當搭配,堆密度以1.6~2.0噸/米3為宜。
爐料的熔化和供電制度 裝好爐料,合上爐蓋後,即降下電極到爐料面近處,接通主電路開關,將電極調節系統的轉換開關放到自動控制位置,以次高級電壓通電起弧。約5~10分鐘,電弧伸入爐料熔成的“小井”後,改用最高電壓,達到輸入變壓器的最大有效功率,加速熔化爐料。電極隨“小井”底部的熔化而逐漸下降,直到電弧觸到鋼液,然後電極又隨鋼液面的升高而上提。當大部分爐料熔化,電弧就完全暴露在熔池面上,這時,為減少電弧對爐頂的強烈輻射,要改用較低電壓,直到爐料完全熔化。爐子輸入能量的制度,隨爐子的容量、冶煉鋼種和冶煉工藝而不同。附圖是一座電弧爐冶煉的能量供給和溫度制度示例。
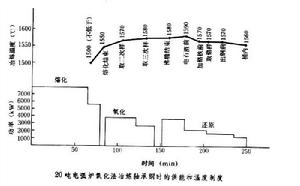
吹氧助熔
電弧暴露在熔池面上並降低輸入功率後,可即向熔池吹入氧氣,以加速廢鋼的熔化。氧氣壓力為6~10公斤力/厘米2。吹氧不宜過早,否則所生成的氧化鐵將積聚在溫度尚低的熔池中,待溫度上升時會發生急劇的氧化反應,引起爆炸式的大沸騰,導致惡性事故。
熔化期的氧化
在爐料將近全部熔化,而被爐渣覆蓋時,取樣分析並根據分析結果調整鋼和渣的成分。此時,爐內是氧化性氣氛,加上熔池中有來自鏽蝕廢鋼和在熔化過程中廢鋼氧化產生的氧化鐵,或者來自爐料鐵礦石的氧化鐵,鋼液中的矽、磷、錳等元素會大量氧化。如果熔池有足夠高的溫度尤其是在吹氧時,氧炬附近的鋼水就可引起碳的氧化。
在熔化期,合金廢鋼中除了矽、磷、錳、碳等元素氧化外,鉻、釩、鈦、鋁、硼等元素也會氧化,硫、鉛有少量氧化,只有鎳、鉬、銅、錫不氧化。
精煉
精煉過程通過對各階段鋼樣和渣樣的分析、溫度的測定來調整和控制。在精煉期,除碳的氧化物成為氣態逸出外,其他元素的化合物為固態或液態,分別浮入渣中,或留在鋼液內。精煉就是把對鋼質有害的一些元素和化合物,儘可能地從鋼液中排除掉。
煉法分類
電弧爐冶煉分為單渣法和雙渣法。一般如廢鋼含磷高,則採用雙渣法,先加入氧化劑或向鋼液中吹氧氣,進行氧化,除去一部分碳、磷和其他雜質,扒去氧化渣再進行還原精煉。對含磷要求不高的鋼種可採用不扒去氧化渣、直接用脫氧劑進行還原精煉的單渣法。冶煉高合金鋼時,為避免爐料中合金元素的氧化損失,多採用以純淨廢鋼裝料的單渣法。普碳鋼和一般低合金鋼可採用只造氧化渣的單渣法冶煉,許多生產普碳鋼的大型電弧爐即採用此法;在氧化精煉末期,鋼液成分和溫度達到規定要求時出鋼,同時加入鐵合金到盛鋼桶脫氧。為了充分利用變壓器的容量,提高鋼的質量和產量,降低電耗,近年採用爐外精煉,把電弧爐的雙渣法中的還原期工作移到鋼包或精煉爐中進行。
氧化精煉
氧化精煉的主要目的是去磷、去氣、去非金屬夾雜物,並將溫度均勻地提高到高於出鋼溫度。碳的氧化,使熔池沸騰,起強烈攪拌作用,增加鋼液和渣液的接觸面,促進渣中的氧向鋼液傳輸,以氧化雜質,提高熔池溫度並使非金屬夾雜上浮,進入爐渣。鋼液中的氫、氮等氣體擴散到一氧化碳氣泡中,一起逸入爐氣。鋼液經過氧化精煉,如果仍含較高的磷,則需除去部分爐渣,再造新渣去磷。
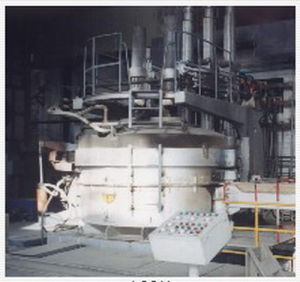
還原精煉
操作過程是在氧化期結束除淨氧化渣後,加入鋁等進行預脫氧。隨後立即加石灰、火磚塊(或砂子)、螢石等先造稀薄渣,然後按照冶煉鋼種的要求再加還原渣料進行還原精煉。常用的還原渣有電石渣和白渣等幾種,它們都是還原性強的強鹼性渣(鹼度CaO:SiO2=3~4)。與其他煉鋼渣相比,它們可以更多更快地脫去鋼液中的氧和硫。由於爐氣也是還原性的,鋼液不易氧化,所加入的易氧化元素損失也很少。
產物成分
電石渣的大致成分為:CaO55~65%,SiO210~15%,MgO8~10%,Al2O32~3%,MnO<1%,CaC21~4%,FeO<0.5%。電石渣分強電石渣和弱電石渣兩種。強電石渣含碳化鈣(CaC2)2~4%,冷後呈黑色並夾有白色條紋,無光澤。弱電石渣含CaC21~2%,冷後呈灰色。製造電石渣的方法是向爐內的稀薄渣上加較多的炭粉、矽鐵粉,密封爐子不使空氣進入,使碳與鈣在高溫下生成碳化鈣。這種爐渣脫氧能力強,碳化鈣與渣中氧化物反應生成CO逸出,而氧化物被還原成金屬進入鋼液:
(CaO)+3C─→(CaC2)+CO↑(CaC2)+3(FeO)─→3【Fe】+(CaO)+2CO↑
為保持渣中有一定量的CaC2,需周期性地加入炭粉和石灰。由於形成CaC2所需的溫度較高,所以造渣時間較長。這種渣易使鋼液增碳,宜用於冶煉高碳鋼種。還因它不易與鋼液分離,會形成鋼中的夾雜物,所以在出鋼前要破壞電石渣,使它變成白渣。因為白渣與鋼液之間界面張力大,不致污染鋼液。
白渣的大致成分為:CaO60%, SiO220%,MgO8%,Al2O35%,MnO1%,FeO<0.5%。造渣方法是向稀薄渣上加矽鐵粉和適量的炭粉,使渣中 FeO還原成鐵進入鋼液,並形成SiO2,因此需追加石灰以保持渣液的鹼度。
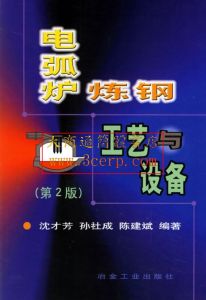
(FeO)+C─→【Fe】+CO↑
這種爐渣的形成時間較短,脫硫能力強。爐渣呈白色,冷卻後自行碎裂成白色粉末,以此得名。有時為了提高脫氧能力,在還原開始時,先造一個短時間的弱電石渣,隨即使之轉變為白渣。
另有火磚渣,用石灰、螢石和廢耐火磚塊造成,是中性渣,主要用於冶煉不鏽鋼;特點是加熱快,不易增碳,渣、鋼容易分離,但脫硫能力低。
參考書目
C.E.Sims, Electric Furnace Steelmaking,AIME,1962.
Electric Furnace Proceedings,AIME.1943~1981.