將粗銅(含銅99%)預先製成厚板作為陽極,純銅製成薄片作陰極,以硫酸(H2SO4)和硫酸銅
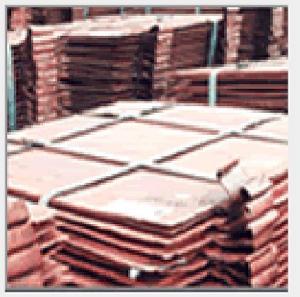
標準
中華人民共和國國家標準GB/T 467—1997 陰極銅前 言
本標準是參照ASTMB115-93《陰極銅》對GB467-82《電解銅》進行修訂的。
本標準將原GB 467-82 中的電解銅(Cu-1)改名為標準陰極銅(Cu-CATH-2),相當於ASTMB115中的2號陰極銅。根據國內的實際情況,本標準對標準陰極銅中雜質極限含量的規定,與ASTMB115中的2號陰極銅有以下差別:標準陰極銅的鉍含量較高,而鉛含量較低;對鋅和硫作了規定,而對硒和碲未作規定,ASTMB115與此相反,對硒和碲作了規定,而對鋅和硫未作規定。
此外,還將GB/T 13585-92《高純陰極銅》規定的高純陰極銅(Cu-CATH-1)納入了本標準。GB/T 13585-92是等效採用BS 6017-1989《精煉銅》中的高純陰極銅製定的,有關技術內容納入本標準時未作任何修改。
本標準的範圍與原標準不同,並將標準名稱改為《陰極銅》。
本標準自實施之日起,代替原GB 467-82和GB/T 13585-92,同時GB 466-82標準作廢。
本標準由中國有色金屬工業總公司提出。
本標準由中國有色金屬工業總公司標準計量研究所歸口。
本標準由上海冶煉廠和中國有色金屬工業總公司標準計量研究所負責起草。
本標準由上海冶煉廠和中國有色金屬工業總公司標準計畫研究所起草。
本標準主要起草人:曾雲華、范順科、蘆如瓊、堯川。
1 範圍
本標準規定了陰極銅的要求、試驗方法、檢驗規則標誌、包裝和質量證明書。
本標準適用於電解精煉法或電解銅,產生陰極銅,通常供重熔用。
2 引用標準
下列標準所包含的條文,通過 標準中作用可構成為本標準的條文,本標準出版時,所示版本均為有效。所有標準都會被修訂,使用本標準的 應探討使用下列標準最新版本的可能性。
GB/T 5121.1-5121.23-1997 銅及銅 化學分析
GB 8170-3 數值修約規定
GB/T 132.23-91 高純陰極銅化學分析方法
3 訂貨單(或合)內容
本標準所列材料的訂貨單(或契約)內應包括下列內容
3.1 產品名稱
3.2 牌號
3.3 數量
3.4 標準編號、年代號
3.5 雜質含量特殊要求
3.6 尺寸要求
3.7 包裝要求
3.8 其他
4 要求
4.1 產品分類
陰極銅按化學成分分為高純陰極銅(Cu-CATH-1)和標準陰極銅(Cu-CATH-2)兩個牌號。
4.2 化學成分
4.2.1 高純陰極銅化學成分應符合表1的規定。標準陰極銅化學成分應符合表2的規定。
表1 高純陰極銅(Cu-CATH-1)化學成分 %
元素組 | 雜質元素 | 含量,不大於 | 元素組總含量,不大於 | |
1 | Se | 0.00020 | 0.00300 | 0.0005 |
Fe | 0.00020 | |||
Bi | 0.00020 | |||
2 | CR | - | 0.0015 | |
Mn | - | |||
Sb | 0.0004 | |||
Cd | - | |||
As | 0.0005 | |||
P | - | |||
3 | Pb | 0.0005 | 0.0005 | |
4 | S | 0.00150 | 0.0015 | |
5 | Sn | - | 0.0020 | |
Ni | - | |||
Fe | 0.0010 | |||
Si | - | |||
Zn | - | |||
Co | - | |||
6 | Ag | 0.0025 | 0.0025 | |
雜質元素總含量 | 0.0065 | |||
1)需在鑄樣上測定 |
4.3 表面質量
4.3.1 陰極銅表面應潔淨,無污泥、油污等各種外來物。
4.3.2 高純陰極銅表面表面應無硫酸銅;標準陰極銅表面(包括吊耳部分)的綠色附著物總面積應不大於單面面積的3%.但由於潮濕空氣的作用,使陰極銅表面氧化而生成一層暗綠色者不作廢品。
4.3.3 陰極銅表面及邊緣不得有呈現花瓣狀或樹枝狀的結粒(允許修整)。
4.3.4 標準陰極銅表面高5mm以上圓頭密集結粒的總面積不得大於單面面積的10%(允許修整)。
4.4 其他要求
4.4.1 陰極銅以整塊供應。經供需雙方協商,也可供應切塊。
4.4.2 陰極銅塊應經受普通裝卸而不脆斷。
4.4.3 單塊陰極銅的重量應不小於15kg或中心部位厚度不小於5mm。
5 試驗方法
5.1 高純陰極銅化學成分的仲裁分析方法按GB/T 13293的規定進行。
5.2 標準陰極銅化學成分的仲裁分析方法按GB/T 5121的規定進行。
5.3 表面質量用目視檢測。
6 檢驗規則
6.1 檢查和驗收
6.1.1 產品應由供方技術監督部門進行檢驗,保證產品質量符合本標準的規定,並填寫出質量證明書。
6.1.2 需方可對收到的產品質量檢驗,如檢驗結果與本標準規定不符,可在收到產品之日起一個月內向供方提出,由供需雙方協商解決。如需仲裁,仲裁取樣在需方由供需雙方共同進行。仲裁分析結果為最終結果。
6.2 組批
產品應成批提交檢驗,每批應由同一天、同一循環系統、同一電流密度產出的陰極銅組成。批重不大於200t。
6.3 仲裁取樣方法
6.3.1 高純陰極銅的仲裁取樣方法
6.3.1.1 每批高純陰極銅中任取24塊,按自然數編號。
6.3.1.2 將編號的每塊高純陰極銅垂直等分成24個長方條,從左到右也按自然編號,然後按每塊的號數選取對應號數的長方條。即第一塊切取第一個長方條,第二塊切取第二個長方條,第三塊切取第三個長方條,依此類推。
6.3.1.3 室溫下,將採取的24個長主條切成適當的小塊,於10%的鹽酸溶液中浸泡15min,然後用去離子水充分洗滌,清除全部外來污物,並乾燥(避免氧化)。
6.3.1.4 從該批中取出一些高純陰極銅置於有蓋的石墨坩堝內進行熔化,再把熔體倒掉。
6.3.1.5 依據石墨坩堝(6.3.1.4)容量的大小,將清洗過的小塊試樣(6.3.1.3)按下面的兩種方法之一進行熔化。
a)將清洗過的試樣置於石墨坩堝內,在惰性氣體保護下於感應爐或電阻爐內加熱熔化,用石墨棒充分攪拌熔體,然後按前、後、中順序過程倒入石墨模中,鑄成三個適當尺寸的樣錠。
b)當石墨坩堝容量不夠大時,可以將清洗過的試樣分成兩組或兩組以上,然後依照方法a)進行。
6.3.1.6 在熔澆過程中,應避免氧的侵入。
6.3.1.7 除去樣錠的表層後,用硬質合金刀具鑽、銑或鋸切(應防止過熱,以免氧化)取樣。獲得大於600g的細屑,將細屑仔細混勻,用磁鐵除淨加工時可能帶入的鐵,將除鐵後的試樣縮分成四份(每份量不小於150g),一份供供方分析用,一份供需分析用,一份挖仲裁分析用,一份留作備用。
6.3.2 標準陰極銅的仲裁取樣方法
6.3.2.1 從該陰極銅中隨機取出6-10個樣塊。
6.3.2.2 用直徑10mm-20mm的鑽頭,在距陰極銅四周100mm的矩形中,以棋盤行列布置鑽孔若干處,鑽取時,不許用任何潤滑劑,鑽速以試樣不氧化為宜。
6.3.2.3 表面鑽屑應去掉,鑽孔深度應大於樣塊厚度的二分這一。將所得的鑽屑仔細混勻,用磁鐵除淨加工時帶入的鐵,並縮分至不少於600g,均勻分成四份,一份供供方分析用,一份供需分析用,一份供仲裁分析用,一份備用。
6.4 檢驗結果判定
6.4.1 化學成分仲裁分析結果與本標準的規定不符時,該批為不合格品。
6.4.2 表面檢驗結果不符合標準4.4條規定時,按塊判為不合格品。
6.4.3 物理要求不符合標準4.5.2條和4.5.3條時,按塊判為不合格品。
7 標誌、包裝和質量證明書
7.1 陰極銅應包裝成適合裝卸重量的捆。經供需雙方協定,也可不包裝。
7.2 每捆陰極銅必須有明顯的標誌,註明:
a) 生產廠標誌;
b) 產品牌號;
c) 批號。
7.3 每批陰極銅應附有質量證明書,註明:
a) 生產廠名稱;
b) 產品名稱和牌號;
c) 批號;
d) 批重;
e) 分析檢驗結果和技術監督部門印記;
f) 本標準編號;
g) 出廠日期。
化學反應
銅的電解提純:將粗銅(含銅99%)預先製成厚板作為陽極,純銅製成薄片作陰極,以硫酸(H2SO4)和硫酸銅(CuSO4)的混和液作為電解液。通電後,銅從陽極溶解成銅離子(Cu)向陰極移動,到達陰極後獲得電子而在陰極析出純銅(亦稱電解銅)。粗銅中雜質如比銅活潑的鐵和鋅等會隨銅一起溶解為離子(Zn和Fe)。由於這些離子與銅離子相比不易析出,所以電解時只要適當調節電位差即可避免這些離子在陽極上析出。比銅不活潑的雜質如金和銀等沉積在電解槽的底部。這樣生產出來的銅板,稱為“電解銅”,質量極高,可以用來製作電氣產品。
沉澱在電解槽底部的稱為“陽極泥”,裡面富含金銀,是十分貴重的,取出再加工有極高的經濟價值。
把電解銅再進一步加工,可製作成為極細的電解銅粉。
銅電解精煉的原理如下:
陽極反應:Cu—2e=Cu2+
Me—2e=Me2+
H2O—2e=2H++1/2O2
SO42-—2e=SO3+1/2O2
式中Me代表Fe、Ni、Pb、As、Sb等比Cu更負電性的金屬,它們從陽極上溶解進入溶液。H2O和SO42-失去電子的反應由於其電位比銅正,故在正常情況下不會發生。貴金屬的電位更正,不溶解,而進入陽極泥。
陰極反應:Cu2++2e=Cu
2H++2e=H2
Me2++2e=Me
在這些反應中,具有標準電位比銅正、濃度高的金屬離子才可能在陰極上被還原,但它們在陽極不溶解,因此只有銅離子還原是陰極反應的主要反應。
原材料
電解銅⑴銅精礦
在自然界中自然銅存量極少,一般多以金屬共生礦的形態存在。銅礦石中常伴生有多種重金屬和稀有金屬,如金、銀、砷、銻、鉍、硒、鉛、碲、鈷、鎳、鉬等。根據銅化合物的性質,銅礦物可分為自然銅、硫化礦和氧化礦三種類型,主要以硫化礦和氧化礦,特別是硫化礦分布最廣,目前世界銅產量的90%左右來自硫化礦。銅礦石經選礦富集獲得精礦,常見為褐色、灰色、黑褐色、黃綠色,成粉狀,粒度一般小於0.074mm。含銅量13-30%,按行業標準YS/T318-1997《銅精礦》的規定,其化學成分和產品分類如表1。
⑵未精煉銅
按國家標準GB/T11086-1989《銅及銅合金術語》規定,未精煉銅包括冰銅、黑銅、沉澱銅和粗銅。冰銅主要由硫化亞銅和硫化亞鐵組成的中間產品,黑銅通常用彭風爐熔煉廢雜銅或氧化銅礦石而產生的含雜質較多的銅,銅含量一般為60%-85%。沉澱銅通常用鐵從含銅的溶液中置換,沉澱而獲得的銅和氧化銅的不純混合物,乾量計算銅含量一般約50%-85%。粗銅是用轉爐吹煉冰銅而產生的純度不高的銅,粗銅中銅的含量一般約為98%,本標準中規定的未精煉銅,主要指的是粗銅。粗銅按行業標準YS/T70-1993《粗銅》的規定,按化學成分分為三個品級。
(3)銅廢碎料
銅廢碎料涉及的範圍較廣,包括紫銅、黃銅、青銅、白銅的廢雜料,本標準規定的銅廢碎料僅指紫雜銅。紫雜銅為銅製品所產生的各類廢料、廢件。如廢舊電纜、紫銅管、棒、板、塊、帶及帶薄鍍層的上述材料和其它非合金類銅廢料等。有以下5種分類及規格:
第1類:
(a)紫銅管、棒、板、塊、帶,表面乾淨,無油泥和其它沾附、夾雜。
(b)各種裸銅線、短線和其它純銅廢料。
第2類:
(a)1類銅廢料中混有紙屑、各種絕緣材料、少量油泥、銹垢、雜物,但重量必須小於1%。
(b)直徑0.3mm以上的漆包線,無污物和雜物。
第3類:各種報廢的純銅或有薄鍍鋅層的純銅電器開關,零部件。
第4類:
(a)直徑0.1-0.3mm的漆包線。
(b)有油泥或少量其它夾雜的漆包線。
(c)乾淨、發脆的火燒線。
第5類:各種純銅水箱、蒸發器、熱交換器具、但其內部不得有充填物,只允許有少量自然形成的水垢。
加工方法
銅的冶煉方法可分為兩類:火法冶金和濕法冶金。世界上精銅產量的85%以上是用火法冶金從硫化銅精礦和再生銅中回收的,濕法冶金生產的精銅只占15%左右。⑴火法冶金
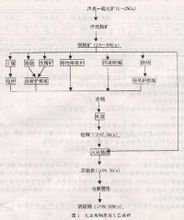
在中國,從銅精礦中提取金屬銅,主要採用火法冶金的方法,目前,比較先進的是閃速熔煉,其產量占全國產銅量的30%以上。由於能耗低,規模大,能有效控制環境污染等優點。這一冶煉技術正在煉銅工業上得到日益發展。閃速熔煉根據不同爐型的工作原理可分為兩種類型:Outokumpu閃速熔煉、InCo閃速熔煉。以下介紹Outokumpu熔煉的工藝流程。
⑵濕法冶金
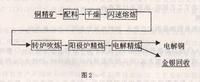