簡介

蓄熱式均熱爐採用高溫空氣燃燒技術,具有極限利用煙氣餘熱和極大降低排放的優點,煙氣中的熱回收率可達70%~80%,充分提高了能源的利用率。因此,蓄熱式均熱爐在節能降耗方面潛力巨大,是均熱爐發展的趨勢。
均熱爐屬室狀爐類型,即爐溫是隨時間而變的。均熱爐要根據鋼錠的材質、尺寸規格、裝爐溫度、出爐溫度等,確定爐子的加熱制度,即確定加熱升溫曲線,包括各階段的加熱溫度、加熱時間、加熱速度、保溫時間口。
均熱爐在保證安全運行及完成加熱鋼坯任務的同時,還要考慮高效及經濟地燃燒。當均熱爐控制系統的負荷及煤氣的質量等因素髮生波動時,採用何種合理有效的控制手段,仍然能使加熱爐內的爐膛溫度、爐膛壓力、排煙溫度等參數穩定在控制範圍之內,並且能夠使加熱爐工作在最佳燃燒區。
工作原理
蓄熱式均熱爐工作原理:蓄熱式燃燒技術,確切地應稱為蓄熱式換熱燃燒技術。這是一項古老的換熱方式,十九世紀中期就在平爐和高爐上採用延續至今。軋鋼系統的初軋鋼錠加熱爐以蓄熱式均熱爐最為節能,並且採用的就是低熱值的高爐煤氣為燃料。終因其蓄熱室占用車間面積大,換向時間長,操作複雜,逐漸被中心換熱均熱爐和上部單側燒嘴均熱爐所取代。此後,蓄熱式換熱技術遠離了軋鋼系統的加熱爐。蓄熱式換熱技術,屬不穩態傳熱,利用耐火材料作載體,交替地被廢氣熱量加熱。再將蓄熱體蓄存的熱量加熱空氣或煤氣,使空氣和煤氣獲得高溫預熱,達到廢熱回收的效能。由於蓄熱體是周期性地加熱、放熱,為了保證爐膛加熱的連續性,蓄熱體必須成對設定。同時,要有換向裝置完成蓄熱體交替加熱、放熱。到了二十世紀八十年代,解決了蓄熱體的小型化和換向時間縮短到以分秒計,才使這項古老的換熱技術得以在軋鋼系統的連續式加熱爐(含步進式加熱爐)上重現廢熱回收的優勢,即將空、煤氣雙預熱到1000℃左右,排出廢氣溫度在150℃以下,使廢熱回收率達到極限值。並且,出現研究高溫空氣燃燒理論與實踐的新領域。
存在問題
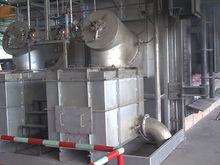
1、換向設備頻繁報警
換向設備設有閥位報警、超溫報警。由於設備長期工作在高溫下,膨脹、變形、升降桿失去潤滑、閥芯密封膠圈硬化失效、壓縮空氣壓力不足、閥位感測器檢測失真等許多原因都會引起閥位報警,換向閥未到位的直接後果是引起部分空、煤氣被吸人煙道,達到一定條件便會發生爆炸。由於設備頻繁報警,故障不斷,均熱爐的作業效率會降低。
2、漏煤氣現象
蓄熱室中漏出的煤氣首先在蓄熱室下部的鋼結構外形成明火,有時爐底大梁以及蓄熱室上部也會出現明火。分析泄漏煤氣的原因,有耐火材料因素,也有人為因素的影響。眾所周知,均熱爐為周期性工作的工業爐,而蓄熱室尤其是蓄熱室下部的溫度更是周期性變化,這就要求築爐的耐火材料具有非常好的抗熱震穩定性,否則,爐體就易出現破裂,剝落甚至坍塌。人為因素的影響是指在均熱爐乾打渣過程中,施工單位為了在廠方規定的短時間內完成任務,便向溫度未完全降下來的爐內通人冷水來降溫。這樣更加速了爐牆裂縫的出現。生產過程中,煤氣便會從蓄熱室牆體上出現的裂縫溢出,j沿著爐牆與爐牆鋼板之間的間隙泄漏到爐外。以上漏煤氣現象多發生在爐子投產中後期階段。
3、爐膛正壓力大
由於爐膛正壓力大,爐口砂封中的砂粒經常被吹離砂封槽,加之砂封刀壽命短,造成爐口冒火嚴重。爐膛正壓大的原因,一是集中排煙時,由空氣蓄熱室和煤氣蓄熱室排出的煙氣並人同一煙管中(煙管中設隔板),由同一台排煙機和一座鐵皮煙囪提供抽力。這就造成空、煤氣側蓄熱室排煙相互干擾,某一側易出現超溫甚至燒壞網箱的現象。另一個原因是燃料中還原性氣體CO與氧化鐵粉塵發生物理和化學反應,形成熔點更低的氧化亞鐵,在較低的溫度下發生軟熔現象⋯,從而導致陶瓷小球的嚴重粘結,使排煙阻力增大;另外砌築蓄熱室的耐火材料的抗熱震穩定性差,破碎、坍塌以及檢修的舊爐料覆蓋在蓄熱體的上層,造成蓄熱體氣體通道堵塞,爐膛壓力增大。
控制關鍵問題
蓄熱式均熱爐控制中有幾個關鍵問題:
1、對均熱爐的爐膛溫度控制,這是最重要的。對於不同材質的鋼坯必須按照不同的升溫曲線進行鋼坯的烘烤。因為如果溫度過低,達不到軋制工藝的質量要求:溫度過高則也會帶來一些不良的後果,如鋼過熱時鋼的品粒增大,使鋼的機械性能下降,加工時容易產生裂紋等。
2、對爐壓的控制,必須保證爐膛壓力為微正壓。如果壓力過高,則會在爐蓋縫隙處向外竄火,不僅浪費能源,而且易燒壞爐蓋和沙封刀。如果壓力過低,則會在爐子縫隙處吸入大量的冷空氣,這必然降低爐溫,又使加熱時間延長,浪費了大量的能源。
3、換向控制策略的選擇。蓄熱式燃燒技術得以實現,關鍵在換向控制。換向控制策略則關係到均熱爐整體運行效果,也關係到燃料的能耗,還有換向閥和蓄熱體的使用壽命。