基本信息
[腐蝕物品]腐蝕品.一級無機酸性發煙硝酸(86%~97.5%)
[英]Nitric Acid Fuming
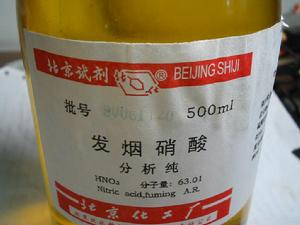
【化學結構】
HNO3
【化學特性】
含硝酸97.5%,水2%,氧化氮0.5%的發煙硝酸為淡黃色到紅褐色透明液體. 含硝酸86%,水5%,氧化氮6%~15%, 有強烈腐蝕性, 露置空氣冒煙, 能與水任意混溶, 有強氧化性. 相對密度: >1.480
【火災危險】
遇有機物如松節油,H發孔劑等能立即燃燒. 遇強還原劑能引起爆炸.
【處置方法】
霧狀水,砂土,二氧化碳.
生產方法
綜述
硝酸和硫酸一樣,也是無機化學工業中的重要產品,但它的產量比硫酸要小得多,1985年全世界的硝酸產量為3000萬t/a,中國1993年的產量(以100%硝酸計)已達56.3萬t/a.硝酸大部分用來製造肥料,如硝酸銨,氮磷鉀複合肥料等,亦大量用來製造炸藥,染料和醫藥中間體,硝酸鹽和王水等,還用作有機合成原料.硝酸是五價氮的含氧酸,純硝酸是無色液體,相對密度1.5027,熔點-42℃,沸點86℃.一般工業品帶微黃色.含硝酸86%~97.5%以上的濃硝酸又稱發煙硝酸,它是溶有二氧化氮的紅褐色液體,在空氣中猛烈發煙並吸收水分.硝酸是強氧化劑,有強腐蝕性,在生產,使用和運輸中要注意安全.與硫酸不同,硝酸與水會形成共沸混合物,共沸點與溫度和壓力的關係示於圖3-1-13,由圖3-1-13可見,共沸點隨壓力的增加而上升,但共沸點下的硝酸濃度卻基本一樣.在101.32 kPa下共沸點溫度為120.5℃,相應的硝酸濃度為68.4%.因此,不能直接由稀硝酸通過蒸餾方法製得濃硝酸,而應該首先將稀硝酸脫水,製成超共沸酸(即濃度超過共沸點時的硝酸濃度),經蒸餾最後才能製得濃硝酸.
在十七世紀,人們用硫酸分解智利硝石(NaNO3)來製取硝酸.硫酸消耗量大,智利硝石又要由智利產地運來,故本法目前已趨淘汰.1932年建立了氨氧化法生產硝酸的工業裝置,所用原料是氨和空氣.氨氧化催化劑是編織成網狀的鉑合金(常用鉑-銠網),產品為稀硝酸(硝酸濃度為45%~62%)和濃硝酸(硝酸濃度為98%).
稀硝酸生產過程
A 氨氧化主要反應有:
4NH3+5O2=4NO+6H2O
這是一個強放熱反應.反應溫度760~840℃,壓力0.1~1.0MPa,通過鉑網的線速度大於0.3 m/s,氧氨比(O2/NH3)為1.7~2.0,在以上工藝條件下,氨的氧化率可達95%~97%.
B NO的氧化
出氨氧化反應器(亦稱氧化爐)的反應氣經廢熱鍋爐和氣體冷卻器分出冷凝稀酸後,在低溫下(小於200℃)利用反應氣中殘餘的氧繼續氧化生成NO2:
其中生成N2O3和N2O4的反應,速度極快(分別為0.1 s和10-4s),而生成NO2的反應則慢得多(約20 s左右),因此是整個氧化反應的控制步驟.上列三個反應是可逆放熱反應,反應後,摩爾數減少,因此降低反應溫度,增加壓力有利於NO氧化反應的進行.NO的氧化程度α-NO與溫度和壓力
C 吸收
吸收在加壓下進行.氮氧化合物中除NO外,其他的氮氧化合物在吸收塔內與水發生如下反應:
因在常溫下N2O3很容易分解成NO和NO2,因此由上列第三式生成HNO2的量不大,可以忽略不計.上列各式生成的HNO2隻有在溫度低於0℃,以及濃度極小時方才穩定,在工業生產條件下,它會迅速分解:
3HNO2=HNO3+2NO+H2O-75.9 kJ
因此,用水吸收氮氧化物的總反應式可寫作:
3NO2+H2O=2HNO3+NO+136.2 kJ
即NO2中2/3生成硝酸酸,1/3變成NO,它仍需返回到氧化系統參與氧化反應,而且由於受共沸酸濃度的限制,硝酸濃度不會很高,一般在60%左右.
現有的稀硝酸生產方法有5種,即常壓法,中壓法(0.25~0.50MPa),高壓法(0.7~1.2MPa),綜合法(氧化為常壓,吸收為加壓)和雙加壓法(氧化為中壓,吸收為高壓).
常壓法氧化和吸收都在常壓下進行,設備投資和動力消耗都較省,但製得的硝酸濃度不高,僅為45%~52%,排出的尾氣中,氮化物NOx(NO,NO2及其他氮化物的總稱)含量高,要增加處理裝置,經治理後才能排入大氣.
中壓法,高壓法和雙加壓法氧化和吸收都在加壓下進行,設備投資和動力消耗大,但製得的酸濃度高,可達65~72%,尾氣中氮化物NOx的含量比較低,容易處理或直接排放.其中雙加壓法加壓方式合理,吸收率達99.5%,尾氣中NOx只有180 ppm左右,可直接經煙囪排入大氣,因此是值得大力推廣的生產方法.綜合法氧化在常壓下進行,吸收在加壓下進行,設備投資和動力消耗介與常壓和加壓之間,硝酸濃度仍可達到65%~72%.
濃硝酸生產過程
生產濃硝酸有直接法,間接法和超共沸酸精餾法三種,直接法即由氨直接合成濃硝酸,基建投資較大,只在國內外大型工廠中採用.間接法是先生產稀硝酸再設法將稀硝酸中水分脫除,將濃度提高至共沸酸濃度以上,最後經蒸餾得到98%成品硝酸.這種生產方法適宜於中小型濃硝酸生產裝置,在國內外採用比較普遍.超共沸酸精餾法是使氧化氣中水分脫除較多,使NOx直接生成超共沸酸,再經蒸餾製得濃硝酸的方法,被認為是製造濃硝酸的一種好方法.A 直接法生產過程
直接法由氨和空氣經氧化直接合成濃硝酸,生產的關鍵是除去反應生成的水.反應經歷以下五個步驟:
①制一氧化氮 氨和空氣通過鉑網催化劑,在高溫下被氧化成一氧化氮,並急冷至40~50℃,使生成的水蒸氣經冷凝而除去.
②制二氧化氮 一氧化氮和空氣中的氧反應,生成NO2後,殘餘的未被氧化的NO和濃度大於98%的濃硝酸再反應,被完全氧化成二氧化氮:?
③分出二氧化氮 在低溫下用濃硝酸(>98%)吸收二氧化氮成為發煙硝酸,不能被吸收的惰性氣體(N2等)排出系統另行處理.
④制純NO2並冷凝聚合為液態四氧化二氮 加熱發煙硝酸,它熱分解放出二氧化氮,然後把這純的NO2冷凝成為液態四氧化二氮:
⑤高壓釜反應制濃硝酸 將液態四氧化氮與稀硝酸混合(要求稀硝酸中水分與液態N2O4成一定比例)送入高壓釜,在5.0MPa壓力下通入氧氣,四氧化二氮與水(來自稀硝酸)和氧反應直接生成98%濃硝酸.
為了加快反應的進行,加入的液態N2O4應比理論量多些,這樣製得的是含大量游離二氧化氮(即發煙硝酸)的白色濃硝酸,將它放到漂白塔內,通入空氣,把游離的NO2吹出,制到98%成品濃硝酸.二氧化氮經回收冷凝後再送到高壓釜使用.如果氨的氧化不用空氣,而採用純氧(需加水蒸氣稀釋以防爆炸),製得的一氧化氮濃度可高些,這對以後的制酸操作是有利的.但需建造制氧裝置和增加動力消耗.
B 間接法
間接法所用脫水劑有硫酸,硝酸鎂,硝酸鈣和硝酸鋅等.經過多年生產實踐的篩選,現在幾乎全部採用硝酸鎂.
圖3-1-15 Mg(NO3)2-H2O系統的結晶曲線
硝酸鎂是三斜晶系的無色晶體,變成水溶液後,隨濃度的不同,可以形成多種結晶水合物,圖3-1-15示出了Mg(NO3)2-H2O系統的結晶曲線.圖中D點是臨界溶解溫度,即當硝酸鎂溶液濃度為57.8%時,其結晶溫度為90℃,此時析出Mg(NO3)2·6H2O結晶.F點為轉熔點,即當硝酸鎂溶液濃度為81.1%時,其結晶溫度為130.9℃,此時Mg(NO3)2和Mg(NO3)2·2H2O結晶共同析出.因此在選擇硝酸鎂操作溫度時,應該避開這些最高點,以免溶液結晶.當硝酸鎂溶液濃度大於67.6%時,其結晶溫度隨溶液濃度增加而迅速上升,溶液濃度超過81%時,則結晶溫度直線上升,在此濃度下操作極易造成管道堵塞.因此,硝酸鎂濃度太稀脫水效果固然不好,太高則也難以操作,在實際生產中一般控制在64%~80%之間,即濃硝酸鎂濃度不超過80%(一般為72%),加熱器出口(即吸水後稀硝酸濃度)不低於64%.硝酸鎂法濃縮原理如下:濃度為72%~74%的硝酸鎂溶液加入稀硝酸中,便立即吸收稀硝酸中的水分,使硝酸濃度提高到68.4%以上,而硝酸鎂由於吸收水分,濃度下降至65%左右,此時在硝酸和硝酸鎂混合溶液的氣相中HNO3濃度在80%以上,再將後者精餾即可得到成品濃硝酸.Mg(NO3)2-HNO3-H2O三元混合物沸騰時所產生的HNO3蒸氣成分可由圖3-1-16求得.從而確定濃縮硝酸所需的最低硝酸鎂的用量.
C 超共沸酸精餾法
該法由西班牙Espimdesa公司開發成功,技術關鍵是要求氨氧化反應後氣體中水分要儘量除盡(冷凝酸濃度低於2%HNO3),使脫水後系統總物料中生成硝酸的濃度超過稀硝酸共沸點的濃度.脫水反應氣在氧化塔中用共沸酸氧化,使NO轉化成NO2,在超共沸酸吸收塔中吸收生成濃度80%~90%的HNO3,再進入超共沸酸精餾塔,熱酸漂白塔製得98%成品酸.本法具有可大型化,投資省,運行費用低的優點,是目前最經濟的方法,排出的尾氣中NOx含量在200 ppm以下,故可直接排放,不會造成環境污染.現將三種濃硝酸生產方法可變成本的比較示於表3-1-10.表中(1)為超共沸酸精餾法;(2)為全壓法(壓力0.45MPa)製取稀硝酸,再用硝酸鎂法制濃硝酸;(3)為雙加壓法(氧化0.45MPa,吸收1.15MPa)制稀硝酸,再用硝酸鎂法制濃硝酸.由表3-1-10可見,超共沸酸精餾法可變成本最低,比全壓法低118.24元/t,比雙加壓法低87.83元/t,對一個全年生產5萬噸濃硝酸的工廠而言,超共沸酸精餾法可節約生產成本42~600萬元。