簡介
隨著我國經濟的持續發展,用戶對板帶鋼材的品種、材質、精度提出了更高要求,要求軋機的壓下機構精度高、速度快、穩定、同步、可靠,只有滿足這些要求,才能適應不斷提高的用戶要求。顯然傳統的機械電動壓下由於壓下絲槓和螺母存在磨擦,只有克服了摩擦力之後才會使壓下絲槓轉動,其結果往往是滯後(20~30)ms,不能滿足現代用戶的產品要求。而液壓自動厚度控制HAGC能很好滿足以上用戶的要求,尤其是能有效減少甚至消除鋼帶頭尾縱向厚差,以提高產品質量 。
液壓 AGC 系統用測厚儀、位移感測器、壓力感測器和其他儀器連續測量相應的參數,完成液壓缸位移和軋制壓力的連續調整,從而實現控制鋼板的厚度差的目的。
一個完整的液壓厚度自動控制系統主要由計算機、檢測元件為主的控制設備和以一套液壓缸為主的執行機構構成。操作側和傳動側每一側都有一個液壓缸,在每個液壓缸的中心部位有一個 SONY 磁尺,作為相對位置感測器來檢測壓上缸活塞的位移量,在壓上缸的外部邊緣安裝一隻 Tempsonics 磁尺,作為絕對值感測器,用來檢測油缸的傾斜位移,使其不超差。在軋鋼的時候都是使用位於中間部位的感測器,操作側和傳動側位移的平均值作為位置閉環反饋的位移量,測量範圍是 0~150mm,解析度為 0.0025mm。每個液壓缸都有一個壓力感測器,用來檢測液壓缸兩側工作時的軋制壓力,並根據彈跳方程間接來調節輥縫。精軋軋機出口距離軋機中心線 12.26m 處側安裝有 X 射線測厚儀,作為外閉環,監控出口厚度的變化,用以及時調整輥縫 。
HAGC的運行方式
根據精軋機各機架鎖定板厚目標值的不同,HAGC可分為絕對方式和相對方式。操作工可根據工作狀態和條件進行選擇,同時如果設定偏差大於某一個值時,HAGC系統會自動由絕對方式切換到相對方式。
(1)絕對方式。當選擇絕對方式時,各機架鎖定板厚設定值Hs為各機架受到負載100ms以後的板厚實際值,這種控制方式稱為絕對AGC方式。這時AGC功能在機架受載100ms後參與調節,其軋制力由FSU(LZ的設定模型)設定,套用在自動方式操作上。

(2)相對方式。當選擇相對方式時,各機架鎖定板厚設定值Hs為各機架受載2s後4次板厚實際值的平板厚實際值,,式中,Hi為實際測量板厚,這時AGC功能在機架經受2s後參與調節,這種控制方式套用在手動方法,其軋制力由手動輸人給定。AGC系統工作時絕對方法和相對方式是自動切換的,切換的依據是設定軋制力和實際軋制力差值或由操作人員干預 。
液壓AGC系統的組成
電液和測控系統
液壓壓下裝置一般由位移感測器,液壓缸和電液伺服閥等所組成。系統通過電液伺服閥對液壓缸的流量和壓力的調節來控制液壓缸上、下移動的行程來調節軋輥輥縫值。
液壓AGC系統通過測厚儀、位移感測器和壓力感測器等對相應參數的連續測量,連續調整壓下缸位移、軋制壓力等,從而控制板材的厚度差。一個完整的厚度液壓伺服自動控制系統以SIMADYN-D控制系統為核心、現場位移、壓力等檢測元器件、厚度檢測系統為信號反饋裝置,以伺服閥為驅動控制裝置,以上位機、過程計算機為監測的一套綜合系統。具體檢測元件主要有:壓力感測器(每側1個)以及安裝在液壓缸上的4個位移感測器(每個液壓缸2個)和2個電動輥縫旋轉編碼器(每個絲槓1個)。要構成1個完整的液壓AGC系統,主要有6種動態裝置:伺服閥、供油管道、液壓缸、軋機、感測器、控制調節器。
AGC內環經過控制器數學模型的綜合計算及伺服放大器驅動後,改變壓下液壓缸行程,從而調節軋機輥縫的大小,達到消除鋼板厚差的目的。它是位置閉環控制系統,主要由伺服控制器、伺服放大器、電液伺服閥、壓下液壓缸及位移感測器等組成。
自動化控制系統
從系統上劃分,液壓AGC控制系統分為兩級,即基礎自動化級和過程級。
(1)基礎自動化級的組成:
1) 控制系統,目前濟鋼中板廠SIMADYN-D系統採用12槽機架,3個CPU處理器框架插卡式系統。各處理器分別執行APC , AGC及相關功能,也稱為板軋機控制器;
2) 監控系統,由WINCC5.1運行監控軟體開發的上位機作為監控操作站,放置在軋鋼操作台;
3) 存放各班操作工自己的軋制規程即人工規程,以備調用;
4) 數據顯示,包括規程數據、設備數據、報警數據等;
5) 採用鍵盤或螢幕上的軟功能鍵進行操作,實時監控各個道次的道次溫度、壓力、輥縫、主機轉速、電機電流等曲線監控電動輥縫、4個位移感測器、系統壓力柱狀顯示圖;
6) 檢測系統,檢測壓下螺絲位置的編碼器,檢測液壓缸行程的位移感測器,檢測油壓的壓力感測器,檢測軋件溫度的測溫儀,檢測成品厚度的測厚儀。
(2)過程級的構成:過程級主要由過程計算機系統構成。目前過程計算機的功能除上述過程參數計算功能以外,根據要求還可以涵蓋整個軋區的過程控制:
1) 加熱爐裝爐、出爐信息;
2) 粗軋機的軋制完成信號,開軋溫度信號,粗軋厚度信息;
3) 精軋機輥縫數據的設定,精軋主機參數;
4) 精整區鋼板軋制跟蹤信息 。
液壓AGC控制系統的原理
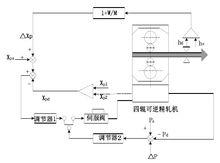
液壓AGC控制系統原理圖如1所示。一個完整的液壓AGC系統的是由多個閉環迴路組成,其中,最主要的是以下三個迴路:




(1)壓下缸的位置閉環:隨著軋制力條件的變化能夠對壓下位移量進行及時準確的控制。表示操作側活塞相對於壓上缸的位移量,表示傳動側活塞相對於壓上缸的位移量。把它倆的平均值作為實際輸出的位移量反饋到輸入端,與給定的位移量比較,差值△Xp作為軋機出口側測厚儀的反饋量。
(2)軋制壓力閉環:通過控制軋制力來控制板材的厚度。Ps表示軋制力的開始設定值,Pd表示軋制壓力實際的測量值,∆p 表示軋制壓力的修正值。把用壓力感測器檢測到的軋制壓力信號反饋給系統,用來補償因軋制壓力產生變化後軋機機座彈跳所造成的輥縫變化,保持板材出口厚度不變,形成軋制壓力閉環反饋系統。


(3)測厚儀監控閉環:在精軋機出口處安裝有測厚儀,作為 AGC 系統的外反饋閉環,監控出口厚度的變化,從而使系統能夠配合位置閉環和軋制力閉環這兩個內反饋環及時的調節輥縫。測厚儀監控閉環可以消除由於軋輥磨損、熱膨脹等因素對出口厚度造成的影響。M 表示剛度係數,W 表示塑性係數,表示軋件實際出口厚度,表示設定的軋件厚度。
為了軋制出高精度、厚度均勻的產品,不僅需要設定適當的初始空載輥縫,而且在軋制過程中,還要使得隨軋制條件的變化及時準確地調節輥縫,以軋出厚度均勻的鋼板。輥縫的調節需要通過設定和調整壓下位置來實現。液壓壓下位置控制系統也叫做液壓位置閉環控制系統,可以準確地控制壓下位移量來調節輥縫,它是軋機液壓 AGC 系統的執行終端,因此液壓位置控制系統的好壞直接決定液壓 AGC 系統的好壞 。
液壓 AGC 位置控制系統的控制原理
液壓 AGC 位置控制系統它主要由供油管道、伺服閥、回油管道、液壓缸、感測器、控制放大器組成,如圖 2 所示。
液壓位置控制系統主要任務是接收來自二級 AGC 模型設定的當前道次的輥縫的調整量,然後和位移感測器測量出的實際液壓缸活塞的位移量相比較,得出的偏差 e 作為 PID 調節器的輸入,經過 PID 調節器後得到一個輸出電壓信號△U作為伺服放大器的輸入。伺服放大器,作為驅動伺服閥的功率放大器,可以把PID 輸出的電壓信號△U 轉換並放大成電流信號△I,對電液伺服閥的開口進行控制。電流信號△I 傳遞給電液伺服閥,電液伺服閥閥口打開,隨即會有一個相應的流量△Qv輸出,推動液壓缸移動,軋輥也隨之移動。位移感測器將液壓缸活塞的位移量△Xp反饋到輸入端,形成反饋控制迴路。測量值與設定值進行作差比較,然後進行輥縫自動調節,直到達到符合工藝要求的輥縫間隙 。