內螺紋管工作原理
工質在管內受熱蒸發過程中,隨著熱負荷的增大,原先為核態沸騰的工況因水不能及時補進壁面而轉變為膜態沸騰,此時壁面與蒸汽膜相接觸,放熱係數急劇下降,管子得不到良好冷卻而使管壁溫度急劇上升,造成受熱面過熱而燒損。防止膜態沸騰傳熱惡化的關鍵是要使管內壁上的環狀水膜的水能得到及時補充,而水源就是中心汽流中的水滴。要使中心汽流中的水滴沉積到水膜上一般有兩種方法,一是利用水滴本身的慣性力,這就需要提高汽流的紊流度,通常依靠增加流體流速來實現,這會使流道阻力增加。另一種方法是在流速不高的情況下利用離心力使水滴到達管壁。內螺紋管就是採用了後一種方法。
工質在內螺紋管內流動時在螺旋上升的內螺紋作用下產生旋轉,汽流中的水滴便在離心力的作用下不斷向管壁靠近,最後到達管壁而使水膜得到補充。另外,內螺紋矩形凹槽中的水膜因三向黏附力作用也不易被汽流帶走,使水膜得以持續保持,不被立即蒸乾。當然,內螺紋另一方面還增加了管內流體的紊流,提高了對流放熱係數,使傳熱得以強化,管壁得到更好的冷卻。
焊接法加工內螺紋管
焊接法是採用在銅帶上直接軋製成螺紋再焊接的方法。
生產工藝流程如下
高精度銅帶→螺紋軋制→成形焊接→定徑→精整卷取→退火→包裝。
焊接管的主要原料為TP2材質的紫銅帶。生產時,銅帶頭尾焊接保證生產線連續運轉。銅帶首先經過滾壓螺紋工序,根據螺紋形狀的不同,選擇不同數量的壓紋輥。
壓過螺紋的銅帶經數道成形輥成形後進行高頻焊接。為了保證管徑的均勻和尺寸,焊接後首先用刮刀去除外毛刺,然後經過定徑輥定徑,以保證管材的外徑和橢圓度符合技術要求。
生產的關鍵工序
焊接法內螺紋管成形工藝過程如下圖所示。
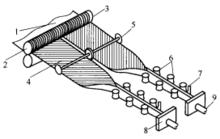
內螺紋焊接銅管生產流程中最關鍵的兩個工序為螺紋軋制和焊接。
1、螺紋軋制。壓紋輥的設計和製作是焊接成形的核心技術,設計不科學的壓紋輥會導致銅帶變形不均勻,造成周期性的焊接缺陷,同時縮短軋輥的使用壽命。
2、高頻焊接。高頻焊接的線速度非常快,一般平均速度在150m/min左右,如此快的加工速度,對擠壓和導向軋輥的精度提出了更高的要求。
在世界空調和製冷行業用銅管中,目前焊接管所占的比例還很小。除了對焊接管的傳統認識障礙外,制約推廣焊接管的重要原因之一是原材料(銅帶)的成本較高,同時由於這種工藝技術難度大,目前還處在發展階段。
拉伸法加工內螺紋管
拉伸法生產的內螺紋銅管為無縫內螺紋銅管,無縫內螺紋銅管是目前空調製冷行業普遍採用的傳熱管,其加工方法歸納起來主要有兩種:一種是擠壓拉伸法;一種是旋壓拉伸法。
擠壓拉伸法
擠壓拉伸法與光面管襯拉法相似,在拉伸過程中,由於受到力的作用,螺紋芯頭在變形區內產生旋轉運動,而管子不轉動,只做軸向直線運動,在拉伸外模及螺紋芯頭的作用下,管子內壁被迫擠壓出螺旋凸筋,從而成形內螺紋管,見下圖。
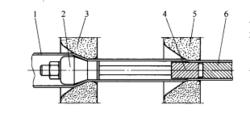
這種方法雖然裝置簡單,但不易使螺紋溝槽深度達到理想狀態,因在擠壓成形過程中,材料在被拉伸的軸向上容易流動,而在成齒的徑向上流動困難,且螺紋起槽處處於滑動摩擦,應力大,溫度高,更難以加工小直徑薄壁內螺紋管。
旋壓拉伸法
旋壓拉伸法有兩種方式:一種是行星滾輪旋壓,另一種是行星球 模旋壓。它的加工原理是用幾個行星式迴轉 的輥輪或滾球對管材外表面進行高速旋壓,使材料產生塑性變形,螺紋芯頭上的螺旋齒映像到管材的內表面上,從而形成內表面上的螺紋。這種方法與擠壓拉伸法相比,不但 能變滑動摩擦為滾動摩擦,降低起槽應力, 而且能加工較深的螺紋溝槽,管子經旋壓加工也大大改善了其力學性能。
產品套用
內螺紋管也叫乾蒸管、內肋管或內翅管。在中央空調機上它主要套用於乾式蒸發器上,熱交換時,管外的誰被管內蒸發膨脹的冷媒所冷卻;它也套用於家用和商用空調熱交換器上或用於高熱管。內螺紋管單位長度的內表面積為普通光面銅管的1.5~2倍,其傳熱係數為同規格光面銅管的1.5~2.4倍。而對載體流阻僅增加3-5%,可節能20~35%,適製冷空調器整機重量減少了10~25%。