簡介
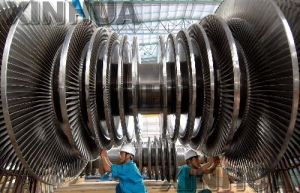
1629年,義大利的G.de布蘭卡提出由一股蒸汽衝擊葉片而鏇轉的轉輪。
1882年,瑞典的C.G.P.de拉瓦爾製成第一台5馬力(3.67千瓦)的單級衝動式汽輪機。
1884年,英國的C.A.帕森斯製成第一台10馬力(7.35千瓦)的多級反動式汽輪機。
1910年,瑞典的B.& F.容克斯川兄弟製成輻流的反動式汽輪機。20世紀初,法國的A.拉托和瑞士的H.佐萊分別製造了多級衝動式汽輪機,美國的C.G.柯蒂斯製成多個速度級的汽輪機。
歷史
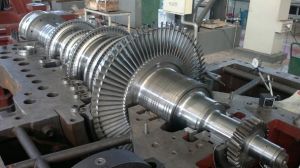
19世紀末,瑞典拉瓦爾和英國帕森斯分別創製了實用的汽輪機。拉瓦爾於1882年製成了第一台5馬力(3.67千瓦)的單級衝動式汽輪機,並解決了有關的噴嘴設計和強度設計問題。單級衝動式汽輪機功率很小,現在已很少採用。
20世紀初,法國拉托和瑞士佐萊分別製造了多級衝動式汽輪機。多級結構為增大汽輪機功率開拓了道路,已被廣泛採用,機組功率不斷增大。帕森斯在1884年取得英國專利,製成了第一台10馬力的多級反動式汽輪機,這台汽輪機的功率和效率在當時都占領先地位。
20世紀初,美國的柯蒂斯製成多個速度級的汽輪機,每個速度級一般有兩列動葉,在第一列動葉後在汽缸上裝有導向葉片,將汽流導向第二列動葉。現在速度級的汽輪機只用於小型的汽輪機上,主要驅動泵、鼓風機等,也常用作中小型多級汽輪機的第一級。
國際狀況

2.在60年代,世界工業發達的國家生產的汽輪機已經達到500—600MW等級水平。1972年瑞士ABB公司製造的1300MW雙軸全速汽輪機在美國投入運行,設計參數達到24Mpa,蒸汽溫度538°C,3600rpm;1974年西德KWU公司製造的1300MW單軸半速(1500rpm)飽和蒸汽參數汽輪機投入運行,;1982年世界上最大的1200MW單軸全速汽輪機在前蘇聯投入運行,壓力24Mpa,蒸汽溫度540°C。
3.世界各國都在研究大容量、高參數汽輪機的研究和開發,如俄羅斯正在研究2000MW汽輪機。主要是大容量汽輪機有如下特點:
1)降低單位功率投資成本。如800MW機組比500MW汽輪機的千瓦造價低17%;1200MW機組比800MW機組的千瓦造價低15%—20%。
2)提高運行經濟性。如法國的600MW機組比國產的125MW機組的熱耗率低276kj/kW.h,每年可節約燃煤4萬噸。
加快電網建設速度,滿足經濟發展需要。
提高電網的調峰能力。
4.汽輪機按照工作原理分為衝動式汽輪機和反動式汽輪機。
汽輪機是一種以蒸汽為動力,並將蒸氣的熱能轉化為機械功的鏇轉機械,是現代火力發電廠中套用最廣泛的原動機。汽輪機具有單機功率大、效率高、壽命長等優點。
——衝動式汽輪機蒸汽主要在靜葉中膨脹,在動葉中只有少量的膨脹。
——反動式汽輪機蒸汽在靜葉和動葉中膨脹,而且膨脹程度相同。
由於反動級不能作成部分進汽,因此第一級調節級通常採用單列衝動級或雙列速度級。如中國引進美國西屋(WH)技術生產的300MW、600MW機組。
世界上生產衝動式汽輪機的企業有:美國通用公司(GE)、英國通用公司(GEC)、日本的東芝(TOSHIBA)和日立、俄羅斯的列寧格勒金屬工廠等。製造反動式汽輪機的有美國西屋公司(WH)、日本三菱、英國帕森斯公司、法國電器機械公司(CMR)等,德國(SIEMENS)。
衝動式汽輪機為隔板型,如國產的300MW高中壓合缸汽輪機;反動式汽輪機為轉鼓型(或筒型),如上海汽輪機廠引進的300MW、600MW汽輪機。
5.汽輪機按照蒸汽參數(壓力和溫度)分為:
——低壓汽輪機:主蒸汽壓力小於1.47Mpa;
——中壓汽輪機:主蒸汽壓力在1.96—3.92Mpa;
——高壓汽輪機:主蒸汽壓力在5.88—9.8Mpa;
——超高壓汽輪機:主蒸汽壓力在11.77—13.93Mpa;
——亞臨界壓力汽輪機:主蒸汽壓力在15.69—17.65Mpa;
——超臨界壓力汽輪機:主蒸汽壓力大於22.15Mpa;
——超超臨界壓力汽輪機:主蒸汽壓力大於32Mpa;
由於冶金技術的不斷發展,使得汽輪機結構也有了很大改進。大機組普遍採用了高中壓合缸的雙層結構,高中壓轉子採用一根轉子結構,高、中、低壓轉子全部採用整鍛結構,軸承較多地採用了可傾瓦結構。各國都在進行大容量、高參數機組的開發和設計,如俄羅斯正在開發的2000MW汽輪機。日本正在開發一種新的合金材料,將使高中、低壓轉子一體化成為可能。
中國狀況
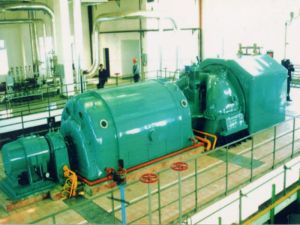
郵票上的125MW汽輪機組
郵票上的125MW汽輪機組
2.1987年採用引進技術生產的300MW機組在石橫電廠投入運行;1989年採用引進技術生產的600MW機組在平圩電廠投入運行;2000年從俄羅斯引進兩台超臨界800MW機組在綏中電廠投入運行。
3.上海汽輪機廠是中國第一家汽輪機廠,在1995年開始與美國西屋電氣公司合作成立了STC,1999年德國西門子公司收購了西屋電氣公司發電部,STC相應股份轉移給西門子。哈爾濱汽輪機廠1956年建廠,先後設計製造了中國第一台25MW、50MW、100MW和200MW汽輪機,80年代從美國西屋公司引進了300MW和600MW亞臨界汽輪機的全套設計和製造技術,於1986年製造成功了中國第一台600MW汽輪機,自主研製的三缸超臨界600MW汽輪機已經投入生產。東方汽輪機廠1965年開始興建,1971年製造出第一台汽輪機,主力機型為600MW汽輪機。北京北重汽輪電機有限責任公司做為後起之秀,以300MW機組為主導產品,它是由始建於1958年的北京重型電機廠通過資產轉型在2000年10月份成立的又一大動力廠,2台600MW汽輪機也已經投入生產。
4.中國四大動力廠以600MW和1000MW機組為主導產品。
工作原理
汽輪機是能將蒸汽熱能轉化為機械功的外燃迴轉式機械,來自鍋爐的蒸汽進入汽輪機後,依次經過一系列環形配置的噴嘴和動葉,將蒸汽的熱能轉化為汽輪機轉子鏇轉的機械能。蒸汽在汽輪機中,以不同方式進行能量轉換,便構成了不同工作原理的汽輪機。汽輪機進汽量的調節為適應外界負荷變化,需要改變汽輪機的進氣量,調節進汽量的主要方法有節流調節、噴嘴調節、旁通調節和滑壓調節。
節流調節
依靠改變調節閥的開度來調節進汽量。當調節閥部分開啟時,汽輪機進汽過程的節流損失增加,這在圖6上表現為B點沿水平線向右移動,使汽輪機效率下降。節流調節的優點是汽輪機的構造簡單、製造成本低,缺點是低負荷時熱效率很差。
噴嘴調節
將調節級的噴嘴分為幾組,每組各由一隻調節閥控制,通過依次啟閉這些調節閥來調節進汽量。圖7a為1台有4隻調節閥的汽輪機進汽室的橫剖面。當打開1隻或2隻閥時,汽輪機發出低於額定的功率。當3隻閥全開足時,所通過總汽量G0可以使汽輪機發出額定功率。當新汽參數降低或背壓升高時,4隻閥全開,以保證汽輪機仍能發出額定功率。圖7b為噴嘴調節的工作曲線。壓力線p1表示調節級後蒸汽壓力隨汽輪機流量(即功率)而變化的情況。pΙ、pⅡ、pⅢ和p各曲線表示各調節閥由關閉到開足時各組噴嘴前的壓力隨進汽量而變化的情況。採用這種調節方式時,通常至多只有最後開啟的一隻閥的節流較大。因此,這種方式在部分負荷時的節流損失比採用節流調節小得多。這種調節方式的缺點是當第一隻調節閥全開時,調節級前後的壓差很大,而且是部分進汽,這對調節級葉片的強度振動特性極為不利。 旁通調節 汽輪機在高負荷時,蒸汽繞過高壓級組,直接進入低壓級組,以通過較多的蒸汽。這種調節方式只在船用汽輪機上仍有採用。
滑壓調節
保持汽輪機調節閥開度不變,依靠滑壓(改變鍋爐供汽壓力)來調節汽輪機的進汽量。這種調節方式的主要特點是調節級後的溫度變化極小,因而避免了在汽缸內產生較大熱應力的危險。另有採用滑壓與噴嘴混合調節的方式,即在滿負荷到半負荷之間採用噴嘴調節,而在半負荷以下依靠鍋爐滑壓來調節
配套設施
汽輪機通常在高溫高壓及高轉速的條件下工作,是一種較為精密的重型機械,一般須與鍋爐(或其他蒸汽發生器)、發電機(或其他被驅動機械)以及凝汽器、加熱器、泵等組成成套設備,一起協調配合工作。結構部件
由轉動部分和靜止部分兩個方面組成。轉子包括主軸、葉輪、動葉片和聯軸器等。靜子包括進汽部分、汽缸、隔板和靜葉柵、汽封及軸承等。
汽缸
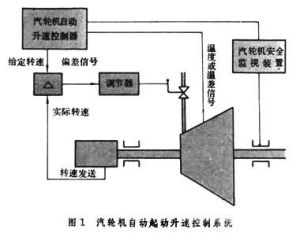
汽缸的高、中壓段一般採用合金鋼或碳鋼鑄造結構,低壓段可根據容量和結構要求,採用鑄造結構或由簡單鑄件、型鋼及鋼板焊接的焊接結構。
高壓缸有單層缸和雙層缸兩種形式。單層缸多用於中低參數的汽輪機。雙層缸適用於參數相對較高的汽輪機。分為高壓內缸和高壓外缸。高壓內缸由水平中分面分開,形成上、下缸,內缸支承在外缸的水平中分面上。高壓外缸由前後共四個貓爪支撐在前軸承箱上。貓爪由下缸一起鑄出,位於下缸的上部,這樣使支承點保持在水平中心線上。
中壓缸由中壓內缸和中壓外缸組成。中壓內缸在水平中分面上分開,形成上下汽缸,內缸支承在外缸的水平中分面上,採用在外缸上加工出來的一外凸台和在內缸上的一個環形槽相互配合,保持內缸在軸向的位置。中壓外缸由水平中分面分開,形成上下汽缸。中壓外缸也以前後兩對貓爪分別支撐在中軸承箱和1號低壓缸的前軸承箱上。
低壓缸為反向分流式,每個低壓缸一個外缸和兩個內缸組成,全部由板件焊接而成。汽缸的上半和下半均在垂直方向被分為三個部分,但在安裝時,上缸垂直結合面已用螺栓連成一體,因此汽缸上半可作為一個零件起吊。低壓外缸由裙式台板支承,此台板與汽缸下半製成一體,並沿汽缸下半向兩端延伸。低壓內缸支承在外缸上。每塊裙式台板分別安裝在被灌漿固定在基礎上的基礎台板上。低壓缸的位置由裙式台板和基礎台板之間的滑銷固定。
轉子
轉子是由合金鋼鍛件整體加工出來的。在高壓轉子調速器端用剛性聯軸器與一根長軸連線,此節上軸上裝有主油泵和超速跳閘機構。
所有轉子都被精加工,並且在裝配上所有的葉片後,進行全速轉動試驗和精確動平衡。
套裝轉子:葉輪、軸封套、聯軸節等部件都是分別加工後,熱套在階梯型主軸上的。各部件與主軸之間採用過盈配合,以防止葉輪等因離心力及溫差作用引起鬆動,並用鍵傳遞力矩。中低壓汽輪機的轉子和高壓汽輪機的低壓轉子常採用套裝結構。套裝轉子在高溫下,葉輪與主軸易發生鬆動。所以不宜作為高溫汽輪機的高壓轉子。
整鍛轉子:葉輪、軸封套、聯軸節等部件與主軸是由一整鍛件削而成,無熱套部分,這解決了高溫下葉輪與軸連線容易鬆動的問題。這種轉子常用於大型汽輪機的高、中壓轉子。結構緊湊,對啟動和變工況適應性強,宜於高溫下運行,轉子剛性好,但是鍛件大,加工工藝要求高,加工周期長,大鍛件質量難以保證。
焊接轉子:汽輪機低壓轉子質量大,承受的離心力大,採用套裝轉子時葉輪內孔在運行時將發生較大的彈性形變,因而需要設計較大的裝配過盈量,但這會引起很大的裝配應力,若採用整鍛轉子,質量難以保證,所以採用分段鍛造,焊接組合的焊接轉子。它主要由若干個葉輪與端軸拼合焊接而成。焊接轉子質量輕,鍛件小,結構緊湊,承載能力高,與尺寸相同、有中心孔的整鍛轉子相比,焊接轉子強度高、剛性好,質量輕,但對焊接性能要求高,這種轉子的套用受焊接工藝及檢驗方法和材料種類的限制。
組合轉子:由整鍛結構套裝結構組合而成,兼有兩種轉子的優點。
聯軸器
聯軸器用來連線汽輪機各個轉子以及發電機轉子,並將汽輪機的扭矩傳給發電機。現代汽輪機常用的聯軸器常用三種形式:剛性聯軸器,半撓性聯軸器和撓性聯軸器。
剛性聯軸器:
這種聯軸器結構結構簡單,尺寸小;工作不需要潤滑,沒有噪聲;但是傳遞振動和軸向位移,對中性要求高。
半撓性聯軸器
右側聯軸器與主軸鍛成一體,而左側聯軸器用熱套加雙鍵套裝在相對的軸端上。兩對輪之間用波形半撓性套筒連線起來,並以配合兩螺栓堅固。波形套筒在扭轉方向是剛性的,在變曲方向剛是撓性的。這種聯軸器主要用於汽輪機-發電機之間,補償軸承之間抽真空、溫差、充氫引起的標高差,可減少振動的相互干擾,對中要求低,常用於中等容量機組
撓性聯軸器 通常有兩種形式,齒輪式和蛇形彈簧式。
這種聯軸器,可以減弱或消除振動的傳遞。對中性要求不高,但是運行過程中需要潤滑,並且製作複雜,成本較高。
靜葉片
隔板用於固定靜葉片,並將汽缸分成若干個汽室。
動葉片
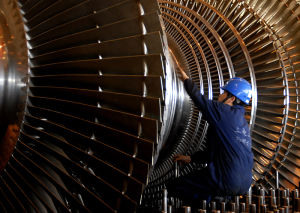
葉片一般由葉型、葉根和葉頂三個部分組成。
葉型是葉片的工作部分,相鄰葉片的葉型部分之間構成汽流通道,蒸汽流過時將動能轉換成機械能。按葉型部分橫截面的變化規律,葉片可以分為等截面直葉片、變截面直葉片、扭葉片、彎扭葉片。
等截面直葉片:斷面型線和面積沿葉高是相同的,加工方便,製造成本較低,有利於在部分級實現葉型通用等優點。但是氣動性能差,主要用於短葉片。
彎扭葉片:截面型心的連線連續發生扭轉,具有良好的撥動特性及強度,但製造工藝複雜,主要用於長葉片。
葉根是將葉片固定在葉輪或轉鼓上的連線部分。它應保證在任何運行條件下的連線牢固,同時力求製造簡單、裝配方便。
T形葉根:加工裝配方便,多用於中長葉片。
菌形葉根:強度高,在大型機上得到廣泛套用。
叉形葉根:加工簡單,裝配方便,強度高,適應性好。
樅樹型葉根:葉根承載能力大,強度適應性好,拆裝方便,但加工複雜,精度要求高,主要用於載荷較大的葉片。
汽輪機的短葉片和中長葉片通常在葉頂用圍帶連在一起,構成葉片組。長葉片剛在葉身中部用拉筋連線成組,或者成自由葉片。
圍帶的作用:增加葉片剛性,改變葉片的自振頻率,以避開共振,從而提高了葉片的振動安全性;減小汽流產生的彎應力;可使葉片構成封閉通道,並可裝置圍帶汽封,減小葉片頂部的漏氣損失。
拉筋:拉筋的作用是增加葉片的剛性,以改善其振動特性。但是拉筋增加了蒸汽流動損失,同時拉筋還會削弱葉片的強度,因此在滿足了葉片振動要求的情況下,應儘量避免採用拉筋,有的長葉片就設計成自由葉片。
汽封
轉子和靜體的間的間隙會導致漏汽,這不僅會降低機組效率,還會影響機組安全運行。為了防止蒸汽泄漏和空氣漏入,需要有密封裝置,通常稱為汽封。
汽封按安裝位置的不同,分為通流部分汽封、隔板汽封、軸端汽封。
軸承
軸承是汽輪機一個重要的組成部分,分為徑向支持軸承和推力軸承兩種類型,它們用來承受轉子的全部重力並且確定轉子在汽缸中的正確位置。
1、多有楔軸承(三油楔、四油楔):輕載、耗功大,高速小機
2、圓軸承:可承重載,瓦溫高
3、橢圓軸承:可承重載
4、可傾瓦軸承:2、4、5、6瓦塊軸承,穩定性好,承載範圍大,耗油量較大
5、推力軸承:1)固定瓦塊式:承載能力小,用於小機組
2)可傾瓦塊式:
①密切爾式: 瓦塊背面線接觸
②金斯伯里式:瓦塊背麵點接觸
種類
結構分類
有單級汽輪機和多級汽輪機;各級裝在一個汽缸內的單缸汽輪機,和各級分裝在幾個汽缸內的多缸汽輪機;各級裝在一根軸上的單軸汽輪機,和各級裝在兩根平行軸上的雙軸汽輪機等。原理分類
有蒸汽主要在各級噴嘴(或靜葉)中膨脹的衝動式汽輪機;蒸汽在靜葉和動葉中都膨脹的反動式汽輪機;以及蒸汽在噴嘴中膨脹後的動能在幾列動葉上加以利用的速度級汽輪機。特性分類
有為凝汽式、供熱式、背壓式、抽汽式和飽和蒸汽汽輪機等類型。凝汽式汽輪機排出的蒸汽流入凝汽器,排汽壓力低於大氣壓力,因此具有良好的熱力性能,是最為常用的一種汽輪機;供熱式汽輪機既提供動力驅動發電機或其他機械,又提供生產或生活用熱,具有較高的熱能利用率;背壓式汽輪機的排汽壓力大於大氣壓力的汽輪機;抽汽式汽輪機是能從中間級抽出蒸汽供熱的汽輪機;飽和蒸汽輪機是以飽和狀態的蒸汽作為新蒸汽的汽輪機。用途分類
可分為電站汽輪機、工業汽輪機、船用汽輪機等。按汽缸數目可分為單缸汽輪機、雙缸汽輪機和多缸汽輪機。
另外還可按照蒸汽初壓(低壓、中壓、高壓、超高壓、亞臨界、超臨界)、排列方式(單軸、雙軸)等進行分類。
優點
與往復式蒸汽機相比,汽輪機中的蒸汽流動是連續的、高速的,單位面積中能通過的流量大,因而能發出較大的功率。大功率汽輪機可以採用較高的蒸汽壓力和溫度,故熱效率較高。19世紀以來,汽輪機的發展就是在不斷提高安全可靠性、耐用性和保證運行方便的基礎上,增大單機功率和提高裝置的熱經濟性。發展前景
汽輪機的出現推動了電力工業的發展,到20世紀初,電站汽輪機單機功率已達10兆瓦。隨著電力套用的日益廣泛,美國紐約等大城市的電站尖峰負荷在20年代已接近1000兆瓦,如果單機功率只有10兆瓦,則需要裝機近百台,因此20年代時單機功率就已增大到60兆瓦,30年代初又出現了165兆瓦和208兆瓦的汽輪機。此後的經濟衰退和第二次世界大戰期間爆發,使汽輪機單機功率的增大處於停頓狀態。50年代,隨著戰後經濟發展,電力需求突飛猛進,單機功率又開始不斷增大,陸續出現了325~600兆瓦的大型汽輪機;60年代製成了1000兆瓦汽輪機;70年代,製成了1300兆瓦汽輪機。現在許多國家常用的單機功率為300~600兆瓦。
汽輪機在社會經濟的各部門中都有廣泛的套用。汽輪機種類很多,並有不同的分類方法。 汽輪機的蒸汽從進口膨脹到出口,單位質量蒸汽的容積增大幾百倍,甚至上千倍,因此各級葉片高度必須逐級加長。大功率凝汽式汽輪機所需的排汽面積很大,末級葉片須做得很長。
汽輪機裝置的熱經濟性用汽輪機熱耗率或熱效率表示。汽輪機熱耗率是每輸出單位機械功所消耗的蒸汽熱量,熱效率是輸出機械功與所耗蒸汽熱量之比。對於整個電站,還需考慮鍋爐效率和廠內用電。因此,電站熱耗率比單獨汽輪機的熱耗率高,電站熱效率比單獨汽輪機的熱效率低。
一座汽輪發電機總功率為1000兆瓦的電站,每年約需耗用標準煤230萬噸。如果熱效率絕對值能提高1%,每年可節約標準煤 6萬噸。因此,汽輪機裝置的熱效率一直受到重視。為了提高汽輪機熱效率,除了不斷改進汽輪機本身的效率,包括改進各級葉片的葉型設計(以減少流動損失)和降低閥門及進排汽管損失以外,還可從熱力學觀點出發採取措施。
根據熱力學原理,新蒸汽參數越高,熱力循環的熱效率也越高。早期汽輪機所用新蒸汽壓力和溫度都較低,熱效率低於20%。隨著單機功率的提高,30年代初新蒸汽壓力已提高到3~4兆帕,溫度為400~450℃。隨著高溫材料的不斷改進,蒸汽溫度逐步提高到535℃,壓力也提高到6~12.5兆帕,個別的已達16兆帕,熱效率達30%以上。50年代初,已有採用新蒸汽溫度為600℃的汽輪機。以後又有新蒸汽溫度為650℃的汽輪機。
現代大型汽輪機按照其輸出功率的不同,採用的新蒸汽壓力又可以分為各個壓力等級,通常採用新蒸汽壓力24.5~26兆帕,新蒸汽溫度和再熱溫度為535~578℃的超臨界參數,或新汽壓力為16.5兆帕、新汽溫度和再熱溫度為535℃的亞臨界參數。使用這些汽輪機的熱效率約為40%。
另外,汽輪機的排汽壓力越低,蒸汽循環的熱效率就越高。不過排汽壓力主要取決凝汽器的真空度,真空度又取決於冷卻水的溫度和抽真空的設備(通常稱為真空泵),如果採用過低的排汽壓力,就需要增大冷卻水流量、增大凝汽器冷卻水和冷卻介質的換熱面、降低被使用的冷卻水的溫度和抽真空的設備,較長的末級葉片,但同時真空太低又會導致汽輪機汽缸(低壓缸)的蒸汽流速加快,使汽輪機汽缸(低壓缸)差脹加劇,危及汽輪機安全運轉。凝汽式汽輪機常用的排汽壓力為5~10千帕(一個標準大氣壓是101325帕斯卡)。船用汽輪機組為了減輕重量,減小尺寸,常用0.006~0.01兆帕的排汽壓力。
此外,提高汽輪機熱效率的措施還有,採用回熱循環、採用再熱循環、採用供熱式汽輪機等。提高汽輪機的熱效率,對節約能源有著重大的意義。
大型汽輪機組的研製是汽輪機未來發展的一個重要方向,這其中研製更長的末級葉片,是進一步發展大型汽輪機的一個關鍵;研究提高熱效率是汽輪機發展的另一方向,採用更高蒸汽參數和二次再熱,研製調峰機組,推廣供熱汽輪機的套用則是這方面發展的重要趨勢。
現代核電站汽輪機的數量正在快速增加,因此研究適用於不同反應堆型的、性能良好的汽輪機具有特別重要的意義。
全世界利用地熱的汽輪機的裝機容量,1983年已有3190兆瓦,不過對熔岩等深層更高溫度地熱資源的利用尚待探索;利用太陽能的汽輪機電站已在建造,海洋溫差發電也在研究之中。所有這些新能源方面的汽輪機尚待繼續進行試驗研究。
另外,在汽輪機設計、製造和運行過程中,採用新的理論和技術,以改善汽輪機的性能,也是未來汽輪機研究的一個重要內容。例如:氣體動力學方面的三維流動理論,濕蒸汽雙相流動理論;強度方面的有限元法和斷裂力學分析;振動方面的快速傅立葉轉換、模態分析和雷射技術;設計、製造工藝、試驗測量和運行監測等方面的電子計算機技術;壽命監控方面的超聲檢查和耗損計算。此外,還將研製氟利昂等新工質的套用,以及新結構、新工藝和新材料等。
目前發展瓶頸主要在材料上,材料問題解決了,單片的功率就可以更大。
常見問題
在汽輪機運行過程中,汽輪機滲漏和汽缸變形是最為常見的設備問題,汽缸結合面的嚴密性直接影響機組的安全經濟運行,檢修研刮汽缸的結合面,使其達到嚴密,是汽缸檢修的重要工作,在處理結合面漏汽的過程中,要仔細分析形成的原因,根據變形的程度和間隙的大小,可以綜合的運用各種方法,以達到結合面嚴密的要求。
漏氣
1.汽缸是鑄造而成的,汽缸出廠後都要經過時效處理,就是要存放一些時間,使汽缸在住鑄造過程中所產生的內應力完全消除。如果時效時間短,那么加工好的汽缸在以後的運行中還會變形,這就是為什麼有的汽缸在第一次泄漏處理後還會在以後的運行中還有漏汽發生。因為汽缸還在不斷的變形。
2.汽缸在運行時受力的情況很複雜,除了受汽缸內外氣體的壓力差和裝在其中的各零部件的重量等靜載荷外,還要承受蒸汽流出靜葉時對靜止部分的反作用力,以及各種連線管道冷熱狀態下對汽缸的作用力,在這些力的相互作用下,汽缸發生塑性變形造成泄漏。
3.汽缸的負荷增減過快,特別是快速的啟動、停機和工況變化時溫度變化大、暖缸的方式不正確、停機檢修時打開保溫層過早等,在汽缸中和發蘭上產生很大的熱應力和熱變形。
4.汽缸在機械加工的過程中或經過補焊後產生了應力,但沒有對汽缸進行回火處理加以消除,致使汽缸存在較大的殘餘應力,在運行中產生永久的變形。
5.在安裝或檢修的過程中,由於檢修工藝和檢修技術的原因,使內缸、汽缸隔板、隔板套及汽封套的膨脹間隙不合適,或是掛耳壓板的膨脹間隙不合適,運行後產生巨大的膨脹力使汽缸變形。
6.使用的汽缸密封劑質量不好、雜質過多或是型號不對;汽缸密封劑內若有堅硬的雜質顆粒就會使密封面難以緊密的結合。VIF900高溫汽缸密封劑是最新汽輪機汽缸密封材料,高、中、低壓缸可通用,避免了型號選擇不當而造成的汽缸泄漏。
7.汽缸螺栓的緊力不足或是螺栓的材質不合格。汽缸結合面的嚴密性主要靠螺栓的緊力來實現的。機組的起停或是增減負荷時產生的熱應力和高溫會造成螺栓的應力鬆弛,如果應力不足,螺栓的預緊力就會逐漸減小。如果汽缸的螺栓材質不好,螺栓在長時間的運行當中,在熱應力和汽缸膨脹力的作用下被拉長,發生塑性變形或斷裂,緊力就會不足,使汽缸發生泄漏的現象。
8.汽缸螺栓緊固的順序不正確。一般的汽缸螺栓在緊固時是從中間向兩邊同時緊固,也就是從垂弧最大處或是受力變形最大的地方緊固,這樣就會把變形最大的處的間隙向汽缸前後的自由端轉移,最後間隙漸漸消失。如果是從兩邊向中間緊,間隙就會集中於中部,汽缸結合面形成弓型間隙,引起蒸汽泄漏。
9.高壓缸上下缸溫差過大 汽輪機首次沖轉時,轉速在2130r/min時開始進行中速暖機,在暖機過程中,高壓外缸缸中部檢水溫差達到汽輪機廠汽輪機運行說明書中所規 定的上限值55.6℃,此時上、下外缸的溫度分別達 到207℃和151℃,但此時機組各運行參數穩定, 各軸承振動沒有明顯變化。考慮到機組首次沖轉, 並且是高壓外缸下缸溫度明顯高於上缸,存在積水 的可能,因而手動打閘停機。
漏油
在現代工業的連續生產中,由於介質腐蝕、沖刷、溫度、壓力、震動等因素的影響,設備、管道、閥門及容器等都不可避免的出現泄露問題。帶壓堵漏技術是在不影響正常生產的前提下,帶溫、帶壓修復滲漏部位,達到重新密封的一種特殊技術手段。由於這種技術有事是在工藝介質、壓力、流量均不降低,且有介質外泄的情況下實施的,因此它與傳統的停車堵漏具有本質的區別,其經濟價值更加顯著。
常見故障
裂紋滲漏
汽輪機的油動機等液壓設備,在工作過程中承受較大的壓力及振動力。由於設備材質為鑄鐵,鑄造過程中難免存在不易發現的鑄造缺陷,加上長時間滿負荷運行,在殼體的薄弱部位極容易出現砂眼滲漏或裂紋滲漏,使設備無法正常工作,液壓油的泄漏同時給現場工作環境造成極大的安全隱患,嚴重威脅企業的安全連續化生產。
在出現此類問題後,企業往往沒有及時有效的解決手段,由於鑄鐵的焊接性能非常差,加上液壓設備的密封性要求較高,傳統的焊補工藝根本無法實現修復。而現場一般沒有此類設備的備品備件,購買更換需要大量的停機時間。上述問題已可以使用高分子複合材料進行現場修復,套用較多的有福世藍2211F高分子金屬修復材料系列。其優良的機械性能及良好的粘接力、耐壓性,使得該問題得以有效解決。施工過程簡單快速可滿足現場施工之要求,並可延長設備使用壽命、提高生產率。
氣缸變形
氣缸變形的原因與汽缸壁及法蘭金屬的厚度和結構尺寸有關,與啟停工況時投入法蘭、螺栓加熱的操作有關,與汽缸保溫情況也有一定的關係,還與製造過程有關。由於汽缸鑄造時的時效問題,以及複雜的受力情況,汽缸變形是不可避免的問題,通常會表現為汽缸出現內張口或外張口的情況,而且低壓缸更容易出現這個問題。出現此問題後,應避免採用開槽等破壞性的修復手法,目前西方國家套用比較成熟的技術是採用德國西門子能源事業部採用的高溫平面密封劑修復技術對變形的結合面間隙進行直接修復。