內容提要

如果你剛剛開始學習精益化的基本知識,本書將教給你一種提高未來工作成效的方法;如果你已經參加過一些研討班或做過一些模擬訓練,閱讀過一些相關文獻,或參加過精益化革新團隊的一些活動,那么本書將會改變你實現精益化的方式。
作者簡介
唐・泰平在電信、醫療、汽車、工業以及航空業領域已經為消除浪費現象和改進經營成果工作了20多年。泰平先生在伊頓航空分部指導精益化實施的時間長達5年,此前他還曾在斯倫貝謝技術有限公司、尤尼斯特拉特公司、數據瀏覽服務公司做過類似的工作。
目錄
概覽
價值流管理 1
本書的目的 2
價值流管理的起源 3
誰應該閱讀本書 3
學習特色 4
導論 價值流管理的過程 6
第一步 承擔精益化的任務 14
第二步 選擇價值流 29
第三步 學習精益化的有關知識 38
第四步 描繪目前的狀態 82
第五步 確定精益化的計量標準 100
第六步 描繪未來的狀態 111
第七步 設計持續改善計畫 140
第八步 實施持續改善計畫 148
附錄 151
專用術語表 204
參考文獻 210
價值流管理
在企業實踐中,一個典型的現象是誰也說不準增值活動占企業生產活動的比例。導致這種現象的基本原因有兩種:其一,在大量生產模式下,部門按功能設定,彼此畫地為牢,管理人員缺乏對企業運作的巨觀了解。其
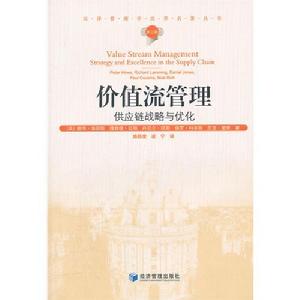
二,管理人員缺乏對增值和非增值活動的認識和判別,難以運用系統的觀點對企業的浪費現象進行分析和改善。 圖一價值流管理流程鑒此,在精益生產中提出了“價值流管理”的概念。這種管理模式徹底打破了大量生產模式下的功能割據,由“價值流團隊”對產品從供應商到顧客整個過程進行管理,實現對運作過程的系統而有效的控制,從而提高滿足顧客需求的能力及反應速度。價值流經理由直接向最高管理者匯報的管理人員擔任,享有改革的充分授權和自主權。價值流經理組建由跨部門成員組成的價值流團隊,以顧客為導向選定產品族,並跟隨其生產路徑,從頭到尾分析和描繪每一個工序的狀態、工序間的物流、信息流和價值流,此為“當前狀態圖”。找出需要改善的地方,再描繪一個“未來狀態圖”,顯示價值流改善的方向和結果。在此基礎上,團隊決定改善的計畫和行動。整個價值流管理實行全成本核算,價值流經理對整個產品族的流程、資源配置及成本運作擔負著主要領導、協調和控制的責任。
價值流管理的特點
價值流管理的特點主要表現在以下三個方面:連續流動性、價值流圖分析、標準化作業。 一、連續流動性
連續流動性是指價值流在供應鏈上連續不斷的進行,企業只在合適的時間,按合適的數量生產所需要的產品。價值流管理把企業生產與超市管理相結合,建立產成品超市,即產品實物流動的終點就是超市的貨架.一旦客戶從貨架上將產品挑出來拿走,企業就會生產同樣數量的商品來補充存貨。產品在被拿走之前是不會被替換的,當客戶訂購了一些產品之後,這產品才會被拿走,這就是拉動價值流系統的起點。企業確定生產需求後,就要從原材料供應到生產出產成品等環節進行一系列連續精確的價值流動,按照事先確定的生產節拍,各環節都應實現最理想的連續流動,確保上游的作業決不會生產出比下游作業所需要的更多的產品,並且使這種流動長期地保持下去,在企業內部形成永不間斷的價值流動系統。企業要實現理想的價值流動,就要將各項作業從外部結構上改造成若干個包含幾項增值作業的自我管理生產單元,在一個生產單元內,設備和人力按照加工的順序來進行安排。包括為完成一件產品或一道主要生產工序所必需的全部作業。然後,在一個價值流動內平均地分配工作要素,以滿足生產節拍的要求,實現均衡生產。如果不能實現這種連續的均衡生產,那么某些生產單元的生產進度就可能會落在後面,導致下游工序出現閒置時間,而另外一些時候。這些生產單元又可能停工待料。企業生產實現連續流動之後,便可縮短訂貨提前期,大幅度降低在產品存貨,能儘早的發現並解決問題,使企業生產計畫有條不紊,持續不斷地進行。因此,在價值流管理中,首先應保證生產作業的連續流動性。
二、價值流圈分析
實現精益生產管理,最基本的一條就是消滅浪費,而在企業的生產經營活動中,要消滅浪費,就必須判別企業生產中的兩個基本構成:增值和非增值活動。統計研究發現,企業生產活動中,增值活動約占企業生產和經營活動的5% 。必要但非增值活動約占60% ,其35% 為浪費。價值流管理就是通過繪製價值流圖,進行價值流圖分析來發現並消滅浪費、降低成本,贏取最高的邊際利潤。價值流就是將一種產品從原材料狀態)~n-r成客戶可以接受的產成品的一整套操作過程,包括增值和非增值活動。價值流圖是一種使用鉛筆和紙的工具,用一些簡單的符號和流線從頭到尾描繪每一個工序狀態、工序間的物流、信息流和價值流的當前狀態圖,找出需要改善的地方後,再描繪一個未來狀態圖,以顯示價值流改善的方向和結果。價值流圖分析就是先對運作過程中的現狀進行分析,即對“當前狀態圖”進行分析,從顧客一端開始,首先了解顧客的需求情況和節拍,然後研究運作流程中的每一道工序,從下游追溯到上游,直至供應商。分析每個工序的增值和非增值活動,包括準備、加工、庫存、物料的轉移方法等,記錄對應的時間,了解分析物流信息傳遞的路徑和方法,然後根據分析情況來判別和確定出浪費所在及其原因,為消滅浪費和持續改善提供目標。最後根據企業的實際情況,設計出新的價值流程,為未來的運作指明方向。
三、標準化作業
為了能夠在生產過程中的價值流內部實現連續流動,工人按生產節拍生產出產品,並且利用所分配的工作要素取得一致性的周期時間,就必須把每一項工作按生產節拍以~定的標準確定下來,使每個人都能以同樣的方式去做同樣的工作,這樣就產生了標準化作業。標準化作業是指已取得了一致意見的一套工作規程,它確定了每一項生產或裝配過程中的最佳方法和操作順序,是企業最佳的工作流程,最佳的人員培訓,最佳的工作方法 標準化工作滲透在企業生產和管理過程中的每一個環節,需要所有的人都來參加,以實現最大化的消滅浪費。在實施標準化過程中,要遵循三個指導原則:一是與操作人員一起努力,共同確定效率最高的工作方法,並確保對此達成一致意見。二是利用標準化工作組合表來理解過程周期時間與生產節拍之間的關係。它顯示了一個過程中物資和人員的工作流程,說明了每一項作業中每個工序的準確時間。三是遵守生產節拍,這是標準化工作的一個關鍵計量指標,不要試圖通過對每個人的工作負荷做一些實質性的改變來適應生產節拍的變化 當生產節拍縮短時,應對各項工作進行合理化改進.必要時可增加庭員,當生產節拍加長時,可給生產過程分配較少的雇員。實施標準化工作能夠最大限度的發揮人力和機器的效用,與此同時還能確保全全的工作條件。只要從價值流的這三個方而去理解和實施價值流活動,就能達到消滅浪費,降低成本,最佳化資源配置。提高運營管理水平的目的。