背景
隨著現代工業生產和科學技術的迅速發展,對鋼材質量的要求日益提高。例如,為了避免鋼坯(特別是連鑄|軋鋼板坯)產生內部裂紋和得到良好的表面質量,要求普通鋼的含硫量小於0.020%;為了使結構鋼具有均勻的機械性能(即減少各向異性),要求鋼中含硫量小於0.010%;為了使石油和天然氣輸送管、石油精煉設備用鋼、海上採油平台用鋼、低溫用鋼、厚船板鋼和航空用鋼等具有抗氫致裂紋性能、更均勻的機械性能和更高的衝擊韌性,矽鋼具有良好的電磁性能,薄板鋼具有優良的深沖性能等等,要求鋼中含硫量小於0.005%(甚至小於0.002%~0.001%)。要求如此低硫的鋼材,用傳統的高爐連續鑄鋼|煉鐵一轉爐煉鋼工藝是很難生產的,只有在煉鋼之前加上鐵水預脫硫工序、煉鋼之後加上爐外精煉工藝才能生產。
當高爐用的焦炭硫含量較高,出爐鐵水的硫含量不符合煉鋼要求;或高爐採用了酸性渣的操作,減少渣量,以降低焦比及增加產量;或需要排放鹼金屬時,則爐內不能充分脫硫,出爐鐵水的硫含量高,這就需要採用鐵水的爐外單一脫硫法,以進一步降低鐵水的硫含量。另外,隨著連續鑄鋼技術的發展和低硫鋼、超低硫鋼需要量的增加,要求進一步降低轉爐入爐鐵水的硫含量,以減少石灰造渣料的用量,實現少渣操作,並使鐵的收得率提高。因此,也需要進行鐵水常規的爐外脫硫處理。


除易切削鋼外,硫是影響鋼的質量和性能的主要有害元素,直接決定著鋼材的加工性能和適用性能。鐵水脫硫可在高爐內、轉爐內和高爐出鐵後脫硫站進行。高爐內脫硫技術可行,經濟性差;轉爐內缺少還原性氣氛,因此脫硫能力受限;而進入轉爐前的鐵水中脫硫的熱力學條件優越(鐵水中[C]、[P]和[si]含量高使硫的活度係數 增大,鐵水中 比鋼液中高3~4倍),性價比高,稱為脫硫的主要方式。
脫硫劑

工業上採用的鐵水脫硫劑主要有兩類:一類是以石灰基為主,如石灰(CaO),電石( )等;另一類是純鎂或鎂基脫硫劑(配加石灰、電石、焦炭等)。雖然鎂的價格較高,但脫硫效果好、用量少、綜合成本低。脫硫劑的形狀隨加入方式的不同而變化,可製成粉末、細粒、團塊、錠條、鎂焦等各種形狀。
方法及設備
鐵水預脫硫的處理方法,按照脫硫劑加入方式和鐵水攪拌方法的不同,有鋪散法、搖包法、機械攪拌法、噴吹法、餵線法等。其中,噴吹法具有操作靈活、處理鐵水量大、費用低、效果好等一系列優點,得到了廣泛的採用。
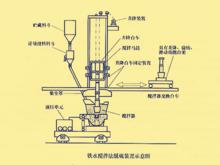
經脫硫預處理後鐵水的硫含量不應高於0.015%,生產超低硫鋼種用的鐵水不應高於0.005%。
(1)KR攪拌法
在鐵水罐內通過攪拌器旋轉攪動鐵水,使鐵水產生旋渦,將加入的脫硫劑捲入鐵水內部進行充分反應,從而實現鐵水脫硫,具有脫硫效率高、脫硫劑耗量少、金屬損耗低等特點。設備配置示意圖如右圖所示。
(2)噴吹法
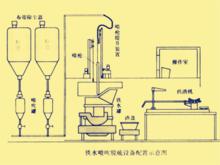
噴吹法是將脫硫劑用載氣經噴槍吹入運送鐵水的魚雷罐車或是煉鋼廠的鐵水包里,使粉劑與鐵水充分接觸,在上浮過程中將硫去除。如右圖所示為鐵水噴吹脫硫設備配置示意圖。
意義
硫除了在易切削鋼中能起到積極作用外,作為有害元素必須在冶煉過程中去除。為得到表面質量高的連鑄坯,避免鑄坯產生內部裂紋,要求普通鋼中的含硫量小於0.02%;為了使結構鋼具有均勻的力學性能,減少各向異性,要求鋼中的硫含量小於0.01%;為了使石油和天然氣輸送管道、石油精煉設備用鋼、海上採油平台用鋼、低溫用鋼、厚船板鋼和航空用鋼等具有抗氫致裂紋性能、更均勻的力學性能和更高的衝擊韌性,矽鋼具有良好的導磁性,薄板鋼具有優良的深衝擊性能等,要求鋼中的硫含量小於0.005%(甚至小於0.002%~0.001%)。靠傳統的高爐、轉爐脫硫已難以滿足用戶對鋼的含硫量日趨嚴格的要求。
要求以低硫含量鋼水為條件的連鑄技術的迅速發展,使得目前大多數鋼種都要求平均含硫量在0.015%以下,對某些超純淨鋼硫的含量要求降到0.001%。傳統的高爐一轉爐工藝難以滿足連鑄工藝發展的需要。
高爐脫硫比轉爐脫硫容易,但高爐脫硫必須提高渣鹼度,從而增加焦比,同時因低硫原料的日益匱乏及價格的不利變化,使得高爐脫硫在經濟上的優勢蕩然無存。轉爐煉鋼過程是個氧化過程,轉爐由於爐內冶煉過程熱力學條件的制約,脫硫率低,一般僅為30%左右。為適當放寬高爐生產的鐵水硫含量和轉爐的少渣吹煉,給高爐減輕負擔,降低焦比,減少渣量,提高生產能力、降低鋼鐵生產的綜合成本,需要採用鐵水預處理工序。
由於已有的低硫原料和燃料的來源會逐漸減少,鐵水中的硫含量可能要相應提高,為此,鐵水預脫硫處理就顯得格外重要,這也使爐外脫硫工藝得到迅速發展。
技術優勢
為保證鋼的質量,必須在爐外對鐵水進行脫硫預處理。鐵水爐外脫硫工藝在經濟上和技術上是合理的和可行的,主要原因在於以下幾方面。
(1)鐵水中含有大量的矽、碳和錳等還原性好的元素,因此在使用不同類型的脫硫劑,特別是強脫硫劑,如鈣、鎂、稀土等金屬及其合金時,不會發生大量的燒損,以致影響脫硫反應進行。 ’
(2)鐵水中的碳、矽等元素能大大提高硫在鐵水中的活度係數,致使硫較容易脫到低水平。鐵水中的氧含量較低,硫的分配係數相應有所提高,有利於脫硫。鐵水處理溫度較低,對處理裝置的壽命有益。
(3)鐵水爐外脫硫可以在魚雷罐、鐵水罐中進行,也可以在鐵水溝中進行,這樣可減少投資。
(4)在鐵水預脫硫的過程中鐵水成分的變化,比煉鋼和鋼水處理中鋼水成分的變化對最終鋼種影響小。
(5)鐵水硫含量可以降低到超低含量,有利於轉爐冶煉優質鋼和合金鋼,擴大冶煉品種,生產出具有高附加值的優質鋼材。
(6)能保證煉鋼吃精料,降低轉爐煉鋼生產成本,提高生產率;蒂森公司研究表明,在鐵水含硫量為0.06%和鋼中含硫量為0.018%的條件下,如果將鐵水中的含硫量從0.025%降低到0.017%,可以使轉爐爐渣鹼度從4降到3,石灰的消耗量減少20kg/t鐵,渣量減少25kg/t鐵,鐵的收得率提高0.6%。
(7)解放高爐生產能力,高爐脫硫負擔減輕,可降低爐渣鹼度,減少渣量,減輕鹼金屬的危害,有利於冶煉低矽鐵,使高爐穩定順行,降低焦比,提高作業率,高爐每降低鐵水中0.001%的含硫量,需增加焦比2~3kg/t鐵;而進行爐外脫硫,可以降低焦比30~40kg/t鐵,產量提高5%~8%。
(8)可以有效地提高鐵、鋼、材系統的綜合效益。硫、磷是決定連鑄坯質量的關鍵因素,鐵水預處理是目前實現全連鑄、近終形連鑄連軋和熱裝熱送新工藝的最經濟、最可靠的技術保障。
發展歷史
早在1877年伊頓(A.E.Eaton)和貝克(L.Beck)就提出可用蘇打作為鐵水的脫硫劑。早期的鐵水爐外脫硫採用簡易的鋪撤法,即在高爐出鐵時發現鐵水含硫過高,立即往鐵水溝中撤放蘇打進行脫硫,從而得到合格的鐵水。後來,美國的拜爾斯公司(A.M.ByersCo)於1927年開發了在鐵水罐中加蘇打粉對化鐵爐鐵水進行脫硫的方法,脫硫後的鐵水用於酸性轉爐煉鋼。由於此法蘇打較貴,鈉的氣化損失較多和易侵蝕罐襯等原因,未能推廣使用。而後,英國的紐厄爾(Newell)等人於1948年向鐵水罐中加入石灰和螢石等混合粉劑進行鐵水脫硫,但由於效果不佳,也未能推廣。
自20世紀60年代以來,對低硫鋼([S]≤0.01%)和超低硫鋼([S]≤0.005%)的需求量激劇增加,促使鐵水預脫硫技術得到迅速的發展。最先研製成功的鐵水預脫硫技術有迴轉爐法和搖包法。迴轉爐法是由瑞典的卡林(B.Kalling)等人在1947年試驗成功的,用石灰粉進行鐵水脫硫。並於1950年在瑞典的蘇拉哈默(Surahammar)工廠建成15t迴轉爐投產。但由於此法處理時間長達30min、鐵水溫度下降過多、爐襯壽命低和處理量受限制等問題,故未能推廣。
搖包脫硫法由瑞典的伊克托普(S.Eketorp)和卡林研製成功的,於1959年在瑞典多姆納維特(Dom narfvet)工廠建成3.0t偏心單向迴轉搖包,用CaCz進行鐵水脫硫。隨後新日鐵的八幡鋼鐵廠引進了30t搖包。1962年神戶鋼鐵公司尼崎鋼鐵廠對此法進行了改進,研製成功40t的正逆雙向迴轉搖包法,又稱DM法(Duo VorticalMixingCoverter)。搖包法在一定程度上克服了迴轉爐法的缺點,於70年代曾在工業生產中套用較多。但搖包法要求較大的驅動功率,故只適用於較小容量的鐵水包,因此發展不快。
為了解決大批量鐵水的脫硫問題和克服容器運動法的缺點,相繼開發了多種機械攪拌法脫硫和吹氣攪拌脫硫等方法。這些方法的特點是無需容器運動,由插入鐵水內的攪拌器或通過鐵水內部的氣泡,使鐵水與脫硫劑很好地接觸而加速脫硫。這是鐵水脫硫技術的很大進步。
機械攪拌法脫硫中主要有KR法、RS法和DO法。KR法(KambaraReactor)是新日鐵廣煙制鐵所於1963年開始研製,並於1965年投入工業生產。以後被日本鋼管和住友金屬公司等採用,鐵水罐容量可達200t以上。RS法(Rheinstahl)是德國萊茵鋼鐵廠的克雷默(F.Kraemei’)等人於1969年研製成功的,後來曼內斯曼(Mannesmann)公司引進了200t:的RS裝置。歐洲各國也採用此法。DO法(Demag一Ostbelg)是德國德馬克公司的奧斯特伯格(J.E.Ostherg)於1966年研製成功的,並於1968年在德國的奧古斯特蒂森冶金公司(AugustThyssen—HiltteAG)建成95t的D0裝置。這些方法利用機械攪拌f乍用使鐵水與脫硫劑很好地接觸,脫硫效率高而穩定,能得到低硫或超低硫鐵水。但它們的主要缺點是設備比較複雜,需要二次扒渣、鐵水溫度降低較多和罐襯壽命較低等,因此僅在60~70年代有一定的發展,但在鐵水噴粉脫硫法研製成功後,就不再新建這類裝置了。
吹氣攪拌脫硫法中主要有PDS法和GMR法。PDS法(Porous plug methord)又稱透氣塞脫硫法,它是將脫硫劑加在鐵水面上,通過裝在鐵水包底部的透氣塞頭吹入氣體,攪動鐵水進行脫硫。新日鐵的八幡鋼鐵廠在1968年投產70t的PDS法裝置。後來新日鐵的廣煙鋼鐵廠對此法作了改進,使用專用鐵水包,能連續處理4包鐵水,稱為CLDS法(鐵水包連續脫硫法)。GMR法(Gas LiftMixingReactoI)也稱氣泡泵環流攪拌法,它是神戶鋼鐵公司利用“氣泡泵”原理而研製成的。於1973年研製成功,並於1974年在加古川廠投產一台200t的GMR裝置。吹氣攪拌法的操作簡便,設備費用較低,但由於脫硫效率稍差,因此也沒能推廣。70年代以後噴射冶金技術發展非常迅速,噴粉法已成為當今鐵水預脫硫的主流方法。鐵水噴粉脫硫法最初由德國博克默維賴因(Boehumer Verein)工廠的波爾(H.Pohl)等人於1963年研製成功,鐵水罐容量為40t。由於當時噴射冶金技術處於開發初期,如粉劑輸送、控制和鐵水噴濺等問題未很好解決,因此發展較緩慢。直到1969年,德國奧古斯蒂森冶金公司(AugustThyssen—HiietteAG)的米切斯納(w。Meichsner)等人研製成功魚雷罐車鐵水噴粉脫硫法,稱為ATH法。稍後,新日本鋼鐵公司也試驗成功魚雷罐車頂噴粉脫硫法(Desulpho rization by Top Injection Process)簡稱TDS法,並於1971年在名古屋鋼鐵廠正式投產。魚雷罐車的容量為250t或300t,這樣就解決了大批量鐵水的脫硫問題。由於此法具有處理能力大、反應速度快(即處理時間短)、自動化程度高、脫硫效率高、操作費用和設備費用低等優點,因此它正在代替其他的脫硫方法,已成為當今鐵水預處理的主流方法。
此外,自1972年以來,美國、加拿大、前蘇聯和德國等相繼開發用鎂一焦、鎂一鋼屑團塊和鎂一白雲石團塊等的脫硫劑。它們是將焦炭塊或鋼屑團塊浸入鎂水中而製成,並將它們放入石墨鐘罩內,再插入鐵水中,放出鎂蒸氣與鐵水接觸而進行脫硫,故此法稱為鐘罩法脫硫(plunging bell method)。由於此法鎂的氣化速率控制較難等問題,後來被噴吹鎂一石灰粉或包鹽鎂粒等所取代。