蓄熱爐裂解
正文
用填有固體載熱體的爐子裂解烴類以製取乙烯(或乙炔)的一種烴類裂解方法。載熱體為熱容量較高的耐火材料,裂解原料通過載熱體獲取所需熱量而進行裂解反應。在反應過程中載熱體溫度逐漸降低到一定程度後,即停止裂解,通入空氣及燃料油進行燒焦(燒除積炭)和升溫,使載熱體重新蓄夠熱量備用,因此,它是加熱燒焦和裂解交替進行的一種間歇式操作工藝;可套用殘炭值很高的重質烴(如原油),甚至渣油作為裂解原料。蓄熱爐裂解法自問世至今,已出現多種工藝,主要有下列三種:伍爾夫法 20世紀30年代初,美國伍爾夫公司首先開發並用於生產乙炔。60年代中期,美國聯合碳化物公司成功地改進了伍爾夫爐,以輕質餾分油為原料在1100~1300°C下進行裂解,同時生產乙烯和乙炔。伍爾夫法採用雙爐操作,每一個循環分四個階段總計4min,其中反應占2min。聯邦德國曾用此法建立過大型工業生產裝置,規模(kt)為年產乙烯140,乙炔70,苯120。
派塞法 為澳大利亞石油與化學公司所開發。它是利用兩個蓄熱爐交替操作,每個周期4min,其中裂解為1¼min。以印尼渣油為原料在 1200°C的載熱體上進行裂解,所得主要產品的產率(%)為乙烯20、丙烯7、丁二烯2、苯7、甲苯3、二甲苯1。該公司建有年產30kt乙烯和17kt芳烴的生產裝置。
筒形蓄熱爐裂解法 為60年代國中國所開發,適合於小型石油化工企業。根據爐筒的數量可分為單筒、雙筒和三筒等三種。按照燃燒氣和裂解氣的流向可分為順流和逆流兩類。其中套用最多的是雙筒雙向逆流式。這種爐子由兩個煙囪和兩個裂解爐組成(圖1),
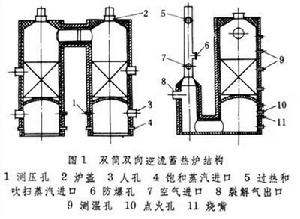
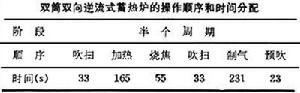
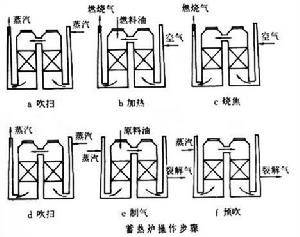