真空電子器件製造
正文

清洗 金屬零件常用汽油、三氯乙烯、丙酮或合成洗滌劑溶液去除表面的油污,再經過酸、鹼等處理,去除表面的氧化層或銹垢等。有時還可在上述液體中進行超聲清洗,以獲得更佳的效果。玻璃外殼或零件可用混合酸處理。經化學清洗後的零件均需經充分的水洗。陶瓷件經去油、化學清洗和水沖洗後,還可再在馬弗爐中經1000

退火 將清洗過的零件加熱到其熔點以下的一定溫度並保持一定時間,然後緩慢冷卻,以消除零件在加工過程中引起的應力。大多數金屬要在保護性氣體或真空中退火,以免氧化,同時也可淨化表面和排除內部所含氣體。玻璃零件加工後在空氣爐中退火即可。
表面塗敷 為避免製造過程中氧化、便於焊接或減小使用時的高頻損耗,某些零件要在表面鍍鎳、銅、金或銀等。還有的零件須預先塗敷特殊塗層,如微波管內用的衰減器可用碳化、石墨噴塗或真空蒸發、濺射等方法塗敷一層高頻衰減材料。有的零件還須塗敷某種材料,如碳化鉭等,以提高表面逸出功,降低次級發射。
部件的製造與測試 為保證器件各電極能按設計要求,準確、可靠地裝配起來,預先製成幾個部件和組件。對部分組件須進行電氣參數的測試(亦稱冷測),構成管殼的組件則須經過氣密性檢驗,合格後才能總裝。主要製造工藝有裝架、封接、焊接和測試等。
裝架 把零件裝配成陰極、電子槍、柵極、慢波電路、陽極或收集極等組件,或進一步裝配成待封口的管子。裝架時採用的焊接方法有點焊、原子氫焊、雷射焊及超聲焊。有時也採用微束等離子焊、電子束焊和擴散焊。
玻璃封接工藝 玻璃之間和玻璃與金屬之間的熔封是常用的工藝之一,多已實現自動化操作。利用這種技術製成電極引線或芯柱,並將管殼與芯柱封接在一起。
銦封工藝 兩種膨脹係數相差很大的玻璃或玻璃與各種晶體、玻璃與金屬間的真空密封,可用高純銦作焊料冷壓而成。這種工藝常用於攝像管視窗和管殼間的封接。它適合於不能承受高溫的零部件的真空密封,且銦能作為電極引出線使用。
陶瓷-金屬封接工藝 為實現陶瓷絕緣件和金屬件的封接以構成部件,廣泛採用燒結金屬粉末法和活性金屬法兩種工藝。前者是將鉬、錳等金屬粉末(有時添加少量氧化物作為活化劑)塗敷在待封接的陶瓷表面,再在氫爐中在 900~1600

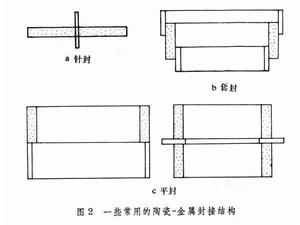
測試 有些高頻系統的部件,如諧振腔、慢波電路等,製成後應先進行“冷測”,以檢驗其電氣性能。必要時可對部件作些調整。對於光電器件,靶面製成後需經動態測試,以檢驗其性能。封接、釺焊或氬弧焊的部件,如作為管殼的一部分,則必須用檢漏儀(如氦質譜儀等)檢驗其焊縫的密封性能,合格後才能用於總裝。
總裝 經檢驗合格的部件用高頻集中焊、釺焊或氬弧焊等方法裝配成整管後即可進行排氣。如果是玻璃管殼,則要把管芯與外殼裝配起來,在連線處用火焰熔封,即封口。有時,在總裝後再進行一次總體檢漏再行排氣。
排氣 將總裝好的器件內部氣體抽出,使壓強達到10-5帕以下的過程稱排氣。在排氣過程中還必須進行管殼去氣、電極去氣、陰極分解和激活等,以保證管子正常工作。排氣系統常用機械泵與油擴散泵串聯的系統,近年來又逐漸採用無油排氣系統,這有助於改善器件的性能(見真空獲得技術)。
烘烤 在排氣過程中常用外部加熱的方法對管殼和零件進行烘烤除氣,再由排氣系統排出管外。為防止管殼金屬部分氧化,還常在真空器件外部再設定一真空烘罩,以便在真空環境下進行烘烤,又稱“雙真空排氣”。
電極去氣 管內的電極系統除用外烘烤去氣外,還可用高頻加熱、電子轟擊以及直接通電加熱等方法進行除氣。加熱的溫度應高於使用溫度。
陰極分解和激活 對於氧化物陰極,在排氣過程中須加熱陰極使碳酸鹽分解成氧化物。為提高陰極的發射能力,還應進一步提高陰極溫度或用支取較大電流的方法加以激活。陰極的分解激活也有在管子封離後進行的,如顯像管的“台下分解”。
封離 在器件排氣過程終了,管內氣體壓強達10-5帕以下時,將器件與排氣系統分開並保持密封的過程叫封離。對採用玻璃排氣管的器件,用火焰噴燒排氣管使玻璃融合而與排氣系統分開。採用金屬排氣管的器件,則用特殊夾鉗直接夾斷金屬管,夾口起密封作用以保持管內的真空狀態。含有吸氣材料的器件常用高頻感應加熱使蒸散型吸氣劑蒸散或使非蒸散型吸氣劑激活以吸收器件內殘餘氣體,進一步提高真空度。
老煉 對排氣後的器件進行電氣處理以獲得穩定的電氣性能的工藝稱為老煉。
首先在陰極加熱條件下,各電極上加正常的或略高的電壓,並持續一定時間,使電極進一步去氣,並使陰極發射電流和其他參數達到穩定。對於高電壓器件,老煉前應在陰極不加熱的條件下,各電極間加以比工作電壓更高的電壓,利用放電現象,去除器件內各電極上殘留的毛刺、灰塵以及絕緣件表面的污點等,以免器件在使用時發生跳火現象。為保持器件內足夠的真空度,有的器件本身還裝有鈦泵。
測試 器件經老煉後需要測試性能,主要參數應達到預定的指標。這種測試亦稱“熱測“。為使用可靠,還須抽樣進行動態特性試驗、壽命試驗、耐衝擊試驗、耐震試驗及冷熱循環等例行試驗。
充氣工藝 有些器件,如穩壓管、閘流管和離子顯示器件等,內部須充有一定的特種氣體如氫、氦、氖、氬等。氣體在排氣過程結束時充入。充入的氣體要非常純淨,因此充氣過程要採取一定措施,仔細控制。
鍍膜工藝 在現代真空電子器件製造過程中,鍍膜工藝套用很廣。鍍膜工藝包括真空蒸發、濺射、離子塗敷及化學氣相沉積等。在製作攝像管、光電倍增管時,各類透明導電膜、光電陰極和光導靶面材料採用真空蒸塗的方法製成。顯像管螢光膜內表面常蒸鋁膜以防止螢光膜灼傷,也可提高管子的亮度和對比度。現代鍍膜工藝也被用來改變某些材料的表面狀態,製作陰極以及使陶瓷或其他介質表面低溫金屬化和實現高頻低損耗的封接等。
離子刻蝕 這是用離子能量將固體原子或分子從表面層上逐漸剝離的一種新型微細加工方法。使用掩膜可以制出精密圖形。這種工藝可用於器件零部件的表面薄層剝離、有機膜的去除以及對攝像管晶體靶面進行清潔處理或製作靶面的精細格線等(見電子束與離子束微細加工)。
螢光屏塗敷工藝 顯像管和示波管屏面內表面須塗敷一層均勻的螢光物質。塗屏的方法應儘量保持材料的螢光性質。對塗層的要求是均勻、顆粒大小分布要滿足一定要求、真空性能好、放氣量小、有足夠的粘附強度。塗屏方法主要有沉澱法、粉漿法和乾法幾種。
沉澱法 黑白顯像管、示波管常用沉澱法塗屏。先將玻屏清洗乾淨,注入含矽酸鉀的工作液,再注入含螢光質的懸浮液。經過一定時間的靜置沉澱後倒出殘液,通入60


粉漿法 彩色顯像管螢光屏多採用粉漿法塗敷螢光粉,即採用含有水溶性感光膠的螢光粉漿注入屏面內進行旋塗,使螢光粉漿均勻分布,再經光學曝光、顯影(溫純水沖洗)等步驟製造而成。
三種螢光物質需分三次相繼塗敷以使其分別固定在相應的位置上。有的管型需預先在三種色粉之間的位置塗以石墨黑底。螢光膜上要先用溶液法塗一層有機膜,再蒸塗鋁膜以保證鋁膜表面光亮,而有機膜在以後的焙燒中燒掉。由於屏面塗有螢光粉而不能經受玻璃熔封的高溫,須採用低熔點玻璃焊料在 440

乾法 這是新發展的一種光粘工藝,屬於乾法塗屏工藝。
先在屏面上塗以疏水性預塗膜,再塗以光粘膠。由於光粘膠曝光即有粘性,所以在撒上乾螢光粉後,可用空氣噴吹螢幕,將未曝光部分的粉吹掉而達到塗屏的目的。彩色管的三種顏色的螢光粉分三次進行塗敷。這種工藝簡單、成本低、螢光膜亮度高、解析度高,可以滿足超高精細管對塗屏的要求。
參考書目
莫純昌、陳國平等編:《電真空工藝》,國防工業出版社,北京,1980。
劉聯寶主編:《電真空器件的釺焊與陶瓷-金屬封接》,國防工業出版社,北京,1980。
H.Kohl Walter,The Handbook of Materials and Techniques for Vacuum Devices, Reinhold Pub.Corp., New York,1967.