產生原因
潤滑經濟崛起的必然原因

潤滑與機械設備運轉息息相關,是保證和改進機械設備高效、正常、長期運轉的基本手段,是機械運轉的命脈。失去了潤滑就沒有機械設備的存在。因此,各國都十分重視先進合理潤滑技術的開發和利用。據日本有關資料介紹1970年日本改善潤滑技術而增長經濟效益2萬億日元。名古屋鋼廠僅改善潤滑技術一項,就實現增長經濟效益20億日元,同時機械設備故障減少了百分之九十。
目前,全世界生產的能源,據德國沃格莆教授測算,約1/3到1/2消耗在摩擦、磨損上。當然摩擦、磨損一部分是不可避免的。但隨著摩擦潤滑科學技術進步和潤滑管理水平提高,其中一部分完全可以省下來。如美國機械工程學會在《依靠摩擦潤滑技術節能策略》中指出,美國每年從潤滑方面獲得經濟效益6000億美元。美國1992年“潤滑工程”介紹美國一年花在摩擦學的經濟費用高達2400萬美元,而收益則達1600億美元。加拿大的調查表明,摩擦、磨損引起的損失每年可達50億加元,而通過潤滑成果推廣套用可以挽回三分之一的損失。英國調查報告指出,每年從潤滑方面獲得經濟效益不少於五億英鎊。日本統計設備故障700例中,因潤滑不良造成故障有253例,占36%以上。中國統計潤滑發生故障在55%----65%。通過改善潤滑降低磨損的經濟效益占全國經濟總值2%以上。資料顯示,中國每年摩擦損耗造成損失在1000億人民幣以上。正因為摩擦學在經濟社會具有增效、節能、節材,使資源充分利用,最佳化環境和保障安全的作用,並能產生巨大的社會效益和經濟效益。因此潤滑經濟必將成為中國新型工業化道路和經濟可持續發展的重要方面。
在中國,潤滑經濟這個詞,是由漢非(北京)潤滑技術研究所王常青提出,“潤滑經濟”是指通過套用先進潤滑技術,顯著提高機械設備的極壓抗磨性能,減少摩擦磨損,減少動力損失,延長潤滑介質壽命,降低惡性機械事故發生機率,延長設備壽命,減少能耗,提高能效,減少排放,實現巨大經濟效益,其投入所產生的綜合效益遠高於1:100。套用先進潤滑技術帶來的不僅僅是直接節能,而且可以實現每道工序、工業環節及各產業鏈重複循環節能增效,改變機械設計、製造和套用及管理理念,改變石油煉製、冶金、機械製造、運輸等基礎產業結構,改變經濟成長方式,甚至改變人們的生產生活方式。
主要特徵
潤滑經濟的特徵是“低消耗、高產出”。具體為:
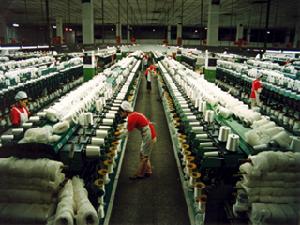
1、在生產過程中,儘量減少資源消耗和廢棄物,提高資源利用率。
中國設備固定資產原值達10萬億元,只要一運轉,就有摩擦,有摩擦就有磨損,有磨損就有潤滑,可謂面大,涉及到國民經濟各個部門、行業。但所用的油,有“貴賤”、“好壞”之分,二者之間性能相差百倍。用適應其工況的高性能油,可以降低能源,減少維修,延長工作時間,大幅增加設備壽命,減少油品消耗。否則得到相反效果。中國用油大都屬中、低檔油,約占市場份額70%。這不難想到為什麼中國等量GDP產值能耗高於西方主要國家5倍,1/3--2/3的鋼材備件消耗在無謂的摩擦,用著寶貴的能源,白白磨掉一些好的鋼材配件,可謂幹著“瞎磨”這種傻事。
2、在運行中,要對油品進行維護、監測。
油品屬精細化工產品,當今的高性能油品已是高科技寵兒。油品中加入各種不同功能添加劑,極大提高油品性能。如運行中高溫、氧化、污染、進水能會大大降低其壽命,進而造成備件早期損壞,因此運行中的維護至關重要。遺憾的是中國相當企業對此未以足夠重視和理解。對肉眼已分不出“好”和“壞”的油,缺乏配備基本監測手段。這些都造成油品能源大量消耗。油品運行中變質,又是備件早期夭折的主要原因。
3、對換下來的油品應進行回收,變廢為寶。
中國這么多設備,每年有大量油品被換下,所謂“廢油”,是否就“廢”呢?應當說90%以上可以用。真正“廢油”不超過10%。如果通過符合環保的方法進行處理,完全可以回收,變廢為寶。現下不少企業油品一是倒掉,污染江河湖海,二是賣掉給二道販子。很少自己回收處理。致使一大批能源白白浪費掉。現下有的單位對大量“廢油”已成負擔,有的燒鍋爐。結果造成積炭,影響散熱效率。
主要作用
1、在生產過程中,儘量減少了能源效耗,提高了資源利用率
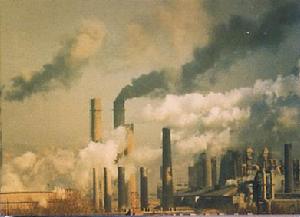
就國內資源而言,中國石油、天然氣、煤炭,可采儲量為例,僅為世界4%、5%和57%。能源短缺是中國經濟社會軟肋。更為嚴重的是資源利用率僅為30%。有人形容這好比是:“吃一碗、倒二碗”。日本通過節能潤滑設計和操作,以及採用節能型潤滑油脂措施,使機械磨損大大降低,節能動力10%--20%。再比如交通運輸用油占石油總耗45%,汽車機械耗能68%消耗在摩擦付上,如合理潤滑正確開展摩擦學設計、節約效果,將十分明顯。據報導,汽車發動機磨損60%發生在起動初期,如使用多級油後,即可減少油料消耗5---10%,就是冷凍起動,也能得到良好潤滑。美國90%以上汽油機,60%柴油機。日本100%汽油機,52%柴油機,均使用多級油。中國前幾年報導,汽油機13%,柴油機16%。可見潛在節能效益。節能也表現在間接上,一出設備從原料生產、冶煉、軋制、鑄造、機加、裝配整個過程都要效耗大量能源,如果通過摩擦學設計以及運行中對油品維護,就可以大幅延長設備壽命,使得一台設備等幾十台用。
2、高清潔度的油品帶來了摩擦付長壽命
近年來陸續有報導,由於油品污染造成的損失數目驚人。如某礦山新油運到礦井地面,其污染度已達到nasio級。某礦務局從國外引進綜采機組由於油液污染嚴重,短短的幾個月時間內,就有數十台液壓泵和液壓馬達損壞,造成直接經濟損失幾十美元。某築路單位從國外購買卡特公司各種工程機械達幾百萬元,由於使用時不懂維護,短短的幾年造成液壓閥組卡咬,動作失效,換成國產閥組至今處於出工不出力狀態。國內外資料表明,液壓元件失效70---85%,歸因於油品污染,變質。這其中除了管理上問題外,還由於近年來液壓潤滑元件精密程度越來越高,運動間隙變小,對超細微粒越來越敏感所致,加之一些用油單位不認識,又沒有檢測手段造成事故頻繁。通過國內外大量實際研究證實了油品本身質量外,常與管理維護不當使油污染有關,要在油品高清潔度上下功夫,必須有一個與使用設備相適應的高效潤滑過濾系統,把污染物及時分離出來。
skf軸承製造商是世界最負有盛名的公司,它們通過大量試驗,深入研究了負荷、油液粘度、顆粒污染物等各種因素對軸承壽命的影響並得出結論:即清除潤滑油中2---5微米固體顆粒,滾動軸承疲勞壽命可延長到原來的10---50倍。根據發動機綜合研究理論,使用改良後的清潔型機器潤滑油將發動機壽命延長8倍。1997年bhp(澳大利亞墨爾本大學維護技術研究院)鋼鐵維修委員會在日本bhp鋼鐵公司兩大軋鋼廠中,通過運行中潤滑問題的研究,在1975年----1985年間nsc鋼廠設備故障率由每年342起減少至85起。設備故障率減少87%。又在此期間通過在全廠範圍內實行潤滑污染預防控制工藝,取得了顯著效益。全廠範圍內軸承購買率減少5%,液壓泵更新率減少80%,潤滑油消耗減少83%,潤滑故障頻率減少90%。中國天津港務局是外貿主要港口之一,現有66個泊位,各類機械2272台(套),船舶44艘,設備固定資產總值達17億元,該局從20世紀90年代開始抓油液淨化工作,使得各種發動機,鏟車、吊車、裝載車故障明顯下降。停機維修損失大為減少,每年節約油料和維修成本高達500萬元。當前,已有單位,甚至將新進油品(當然不是高清潔度油)先過濾達到污染度等級再用,針對這一全球技術課題,美國一公司提出了“全面清潔度控制”(tcc)的理念,旨在從單個零件的生產系統開始運行及今後的工作壽命的整個生產過程中,降低污染物發生率及其影響與全面質量管理(tqc)相似,tcc也需要“全過程、全系統、全體人員”參加,特別是液壓系統,其失效除了系統本身質量不合格外,往往與系統管理工作不落實有效規章制度,規範,未能實施有關。因此,要想真正落實tcc,必須做到“三全”管理才行。目前中國高清潔度油生產不多,就是生產多,在運行過程中,也必須線上過濾才算最好。因為將油中顆粒物分離出去,會使軸承疲勞壽命提高10----50倍。這種易於得到巨大效益,何人不要呢!一台濾油機過濾裝置有幾萬元就可買到,顯然投資是很少的。關鍵是認識問題。
3、對換下來的油品進行回收,變廢為寶
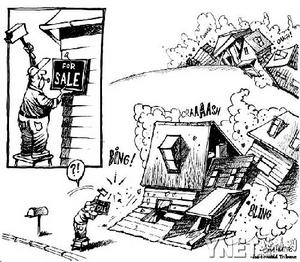
所謂廢油是指各種潤滑油在不同機械設備使用過程中,因受到污染,氧化等因素,改變了原來的各項性能指標,不能繼續用而換下來的油,這些廢油如內燃機油,在工作時,活塞頂部溫度可達300℃以上,部分烴類反應成了3.4—苯並芘等多環芳烴化合物,它們一部分隨廢油排入大氣,一部分留在油中,隨廢油排出。因此礦油不降解,倒入土壤中,導致植物死亡,進入水源,則污染飲用水。而且3.4—苯並芘在水中溶解度很小,但可溶解許多有機溶劑中,它通過人體和動物的表皮滲透到血液中,並在體內積累,導致各種細胞喪失功能,是當今由各種渠道排放到環境中多環芳烴成為對人類威脅的最大致癌物。全世界每年排放的3.4—苯並芘高達5000多噸,給環境造成極大影響。為了減少廢油在土壤和水中積累,1991年歐盟要求用於公共土木工程機械和液壓設備一率用可降解液壓油。瑞士立法禁止在森林、水源、耕地使用非生物降解潤滑油。如果將這些廢油通過符合環保的辦法,如無酸化廢油再生技術,就可使一些廢油變廢為寶。但必須禁止那些仍沿用對環境造成危害的硫酸/白土老工藝處理廢油。現在一些單為處理廢油一是倒掉,二是賣給二道販子。很少自己回收。中國是潤滑油生產和消費大國,每年生產和消費得400萬噸,只廢油回收每年就達100萬噸。如果處理好,是一筆很大財富。60年代美國廢油再生處理產量相當新油18%。潤滑油在原油提煉過程中,僅很小比例。而且非任何原油均可提煉。廢油回收工藝簡單,投資少,收效快。
4、設備潤滑機理革命代來了用油高性能化
當今機械設備發展的趨勢,正向著重量輕、體積小、負荷大、效益高、長壽命發展。潤滑油必須更新換代,來適應設備向高參數發展,首先油中加了高效添加劑,形成了吸附膜層,稱吸附膜邊界潤滑,對負荷低轉數,低滑動速度,摩擦部件上比流體潤滑膜更為穩定和可靠的潤滑作用。一般情況下,邊界吸附膜厚度約0.1----1nm。吸附膜油膜強度優於流體潤滑,但在更高溫度和負荷下也會失效。油中加有硫、磷、氯等極性物質,通過與金屬表面反應形成的化學反應膜進行潤滑,極壓反應膜適用於高溫和重載時等苛刻條件下潤滑。由於潤滑機理髮生變化,傳統靠油的粘度選油,已不在是唯一條件了,油品的高性能化帶了可觀的效益,如將鈣基脂改用相同稠度的鋰基脂,換油期可提高6倍,1ig可當6ig用,將普通hl液壓油改用相同粘度抗磨液壓油hm。泵的壽命可提高10倍,1台泵等10台泵用。對於這種變化意味著這裡蘊藏巨大經濟效益。實際上也就是換一換油,沒有更大投資,懸殊的投入與產出的比例,是任何從機械和備件上下功夫的人想向不到的。
5、為工礦企業提供了安全保障
生產必須安全,安全為了生產。潤滑油的改革升級解決不少企業安全隱患。如汽車制動液是制動系統中傳遞壓力制止車輪轉動的液體,其質量好壞,直接關係到行車安全。目前市場上制動液比較混亂。1998年國家技術監督局公布顯示,中國汽車制動液合格率當時僅為41.7%。江西質量監督局又公布了檢查結果,近六成剎車液安全不達標。如運動粘度不達標,流動潤滑性能差,冬季出現制動滯後現象,制動液易汽化產生氣阻,導致制動疲軟。就制動液而言分醇型,礦油型和合成型三類。醇型制動液價格低,高低溫性能差。中國90年5月已淘汰。但至今市場應有生產和出售。礦油型加了增粘劑,抗氧劑,防鏽劑調和而成,適應性比醇型好,但對天然橡膠有溶脹作用,使用時,應將皮碗軟管換成耐油橡膠製品。合成型通常以乙二醇醚,二乙二醇醚、矽油等加入添加劑組成,適應工作溫度寬,粘溫性好,對橡膠相溶性好,適合高速、大功率、重負荷頻繁制動,是目前使用最多的一種。
再比如,工礦使用鋼絲繩,下現場看到有些用量較大的單位,更換下來鋼絲繩堆積如山,鋼絲繩作為提升、拉拔、牽引的載體,由於在使用時受到拉拔,扭轉、負載突變,時斷時續,風吹日曬,雨淋,工況十分惡劣,特別是室外,出廠時,鋼繩中間有油芯,可儲油進行鋼絲之間潤滑,但實際效果並不理想,出現斷絲、銹絲、乃至突斷,造成惡性安全事故。現在由於研究出可滲透性鋼索油,不但解決了鋼絲之間潤滑,同時使鋼絲表面與導輪間潤滑也得到解決。大連北良港用進口可滲透鋼索油,取得滿意效果。
再比如,用量較大往復空壓機油,過去用13#、19#,由於積炭重,常出安全事故。現在生產的daa、dab、dac空壓機油比13#、19#積炭減少4/5。大大減少因積炭過多,造成爆炸事故。
6、變被動維修為主動維護
維修第一。在中國多年每個企業都有一批維修人員和庫有備件。一但出現故障就搶修,似乎成為中國部分企業的維修模式。但先進的主動維護方式的出現,將對傳統模式一大衝擊。主動維護是對導致設備損壞根源性參數進行監測並控制,延遲失效發生,把故障的苗頭消滅在萌芽之中。最大限度減少停機,達到相對成本低的一種維護方式。一些已開發國家,就已開始使設備周期費用達到最經濟。就設備來講,從事後維修、定期維修,到預防維修,發展到維護型,適應性維護,其核心是把設備周期費用降到最低。潤滑技術的發展適應了這一形勢。潤滑劑使用不當,造成摩擦付過度磨損,裝配精度破壞、升溫、振動、噪音接鍾而來。最後導致無形磨損和突發事故。當今機械化自動化程度越來越高,許多設備維修工所能做的就是“換一換油”,像過去那樣大拆大卸已不可能。
國外已有lcc周期達到不解體大修。這裡關鍵在維護。正確選油變成十分重要。運行中的油品監測、淨化、過濾變成日常工作。實為液體維護技術,這些都是提前進行的。如中國青島港務局前港公司cat裝載機不解體維修超過15000運行台時,佳友dc---25輪胎起重機不解體維修達35000台時。就是在潤滑劑上先下了功夫。當然主動維護雖然成本低,也需要時間和資金的投入,但忽視所帶來的將是更大的資金和時間的投入。有人估計主動維護所產生的綜合經濟效益所謂投入與產出之比大於10,但從國外一些資料看,遠遠超出比數。未雨綢繆,事半功倍。
注意事項
1、必須突破部分企業領導、管理人員對潤滑偏見
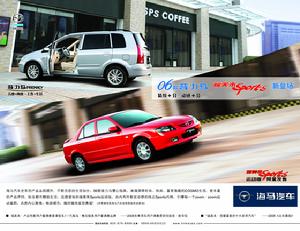
現在的潤滑已跳出原來的純技術,進入到設備管理、生產管理,直接進入到企業管理行列中。它已涉及到增效、節能、環保和安全諸項企業管理大項。因此企業中高層決策者必須首先接受培訓,轉變觀念,提高認識,特別國家調整產業結構上,節約能源是一種無可選擇的選擇,科學用能,才能完成“十一五”,比“十五”能耗下降20%的硬指標。在當前情況下,國人必須重新認識“潤滑”,並給以恰當的定位。當今設備正趨向體積小、功率大、壽命長、自動化程度高,各項指標向高參數發展,潤滑肩負的使命更為突出。如高性能添加劑,納米添加劑,金屬自修復材料以及氟特加塗層,這些加在油里後,使摩擦付形成各種“膜”、“層”、幾倍、十幾倍提高了摩擦付的承載耐磨能力及其他功效。這顯然是原設備設計者,維修工作者及設備管理人員無法想像的。也是從事機械工作的同仁們單純從材料、熱處理、加工上仍沿傳統從機械上再想辦法也難以達到的。這就是當今不斷發展的潤滑。它正在以更小的投資走一條捷徑來滿足設備不斷更新發展的需要。
2、必須突破目前企業管理者只認購廉價油
一些單位購油只看單價成本,不看企業總成本降低觀念,而不注重購買適合本工況高性能油。
△突破目前企業一出現故障只從備件上找原因
不少領導一出故障只從材質、材料、加工精度、和熱處理上找原因,而不從占事故60%以上是由選油和維護油不當造成的觀念。隨這企業的發展,操作技術含量逐漸下降,維護的技術含量不斷上升。最終作到設備維護在一個相當長階段保持正常運轉,儘可能避免檢修和維修,追求周期費用最經濟。顯而易見,未來的維修所從事的工作,面對機電液一體化現代化設備只能是換一換油,只要把潤滑劑維護好,就會使摩擦付磨損降到最低。國外已有整個lcc不解體大修範例,關鍵在維護。最近茂名石化乙烯報導已安全運行79個月的佳績。目前乙烯國際平均運行水平為54個月,改變可以往一年一小修,兩年一大修思維管理模式。據統計少一次大修,其效益接近2億元,就是強化了對關鍵機組維護保養和狀態監測,從定期檢修變為預知檢修。
3、必須突破當下企業無崗、人事無編、學校無專業的“三無”現象
油品套用,同油品煉製一樣,是一個學科。因為它有廣大的工礦企業市場,必須培養一些即懂油,又懂設備的專業技術人員上崗,把應當建立和配套設施健全起來。
潤滑在中國已明顯落後,在油品套用方面,不但落後台灣、東南亞,甚至落後印度和巴基斯坦。不難看出為什麼同樣的設備,國外運行6000小時,而1500小時就要進修配廠。關鍵在選油及油品的維護保養上。有資料顯示,如果能達到日本的節能水平,那么中國能源需求量今後60年不必增加,日本70%能源依靠進口,尤其99%以上石油依靠進口。他們重點抓了節能技術和節能潤滑油脂開發,1980年增加了低粘度油和稠化多級油,如省能內燃機油省燃料5—10%。省能液壓油省電3—7%。日本1973年----1982年間,取得了每年國民經濟總值增張了3.8%。而能源消耗確每年下降2。0----2.9%。產值能耗單耗每年下降3.6%,1982比1979年總能耗取得下降10%的巨大節能效果,資源貧乏的日本,其能源儲備遠遠不及中國,為什麼經濟總量始終坐穩第二把交椅,gdp四倍於中國,它們早在70年代就開展了潤滑現代化工作,設立了專門機構,積極推行潤滑現代化,普及到各個行業,甚至家喻戶曉。在科學界形成了一門新興學科“摩潤學”。中國為加強合理潤滑技術,國家技術監督局93年公布了“合理潤滑技術通則”,內容十分豐富,至今翻看仍然新穎。遺憾的是,未能引起人們更多重視。人們的觀念必須更新,潤滑是一座“金山”,它以巨大的效益展現在面前。在當前能源十分緊張、材料上漲、成本上升情況下,各個企業都把潤滑經濟開展起來,是一條康莊大道。