導軸承的結構分類
根據水輪發電機的總體結構布置,導軸承的結構型式分為:
1、具有單獨油槽的導軸承。它一般都有滑轉子(熱套於軸上並與軸一起加工),導軸承瓦直徑較小,瓦塊數也較少,在滑轉子下緣開徑向供油孔,在離心力作用下向軸瓦供油,並使油路經油冷卻器形成循環。這種結構適用於大、中容量懸式水輪發電機或半傘式水輪發電機的上導軸承。
2、與推力軸承合用一個油槽的導軸承。它常將推力頭兼作滑轉子,具有結構緊湊的特點,但導軸承直徑較大,瓦塊數也較多。為了加強導軸承瓦的潤滑冷卻,通常在鏡板或推力頭上開若干個徑向孔。此種結構適用全傘式水輪發電機的下導軸承和中小容量懸式水輪發電機的上導軸承。
通常導軸承用支柱螺釘進行調整軸瓦間隙。目前採用楔子板代替支柱螺釘,簡化了結構和製造工藝,凋節螺帽和鎖定零件裝設在軸承油麵上部靠近軸承蓋處、便於調節軸承瓦面與滑轉子的間隙。
當水輪發電機磁路不對稱,勵磁繞組發生兩點接地,軸附近存在漏磁等情況時,軸兩端間將出現感應交變電動勢。如果軸堆油膜被擊穿,並形成電流通路時,鏡板和軸瓦將因流過軸電流而受損。為此需採取軸絕緣措施,通常是對上導軸承和推力軸承均用絕緣墊與軸承座相絕緣。在不充油的情況下,導軸承對地絕緣電阻值應不低於1MΩ。
水輪發電機導軸承的工作原理
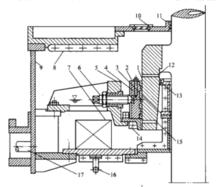
水輪發電機導軸承的作用是:承受機組轉動部分的徑向機械不平衡力和電磁不平衡力,維持機組主軸在軸承間隙範圍內穩定運行。現在大多數水電廠的水輪發電機均採用分塊瓦式導軸承,只不過有的導軸承具有單獨的油槽,有的則與推力軸承共用一個推力油槽。位於發電機轉子上方的導軸承稱為上部導軸承,反之稱為下部導軸承,其結構大同小異。1台水輪發電機裝置有哪幾個導軸承,要根據機組的形式來確定。
圖1所示的分塊瓦式導軸承主要由固定在主軸上的軸領1、抱在軸領上的數塊扇形導軸瓦2、頂在導軸瓦後面的調整螺釘6、托著導軸瓦及固定調整螺釘的軸承體5(瓦背與調整螺釘之間及瓦的下部與軸承體之
間均裝置有絕緣墊,以防止軸電流的形成)以及裝置上述部件及冷卻器7的油槽9組成。
一般情況下,軸瓦浸在油中1/3。當機組運行時,軸領帶動油旋轉,在離心力的作用下形成一定的動壓力,使油進入軸領下部油孔,該油一部分進入瓦問,一部分進入軸瓦與軸領的間隙,從瓦側及瓦上部出來的熱油向外流,經頂瓦螺栓孔轉向軸承體空洞向下,通過冷卻器降溫後向里流,再經軸領進油孔向上,如此循環往復,達到潤滑冷卻的目的。
性能特點分析
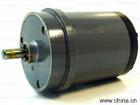
水輪發電機導軸承氣體絕緣金屬封閉變電站即GIS變電站與戶外空氣絕緣變電站相比,可靠性高、使用壽命長,但其一次投資成本高。正在研究和開發的一種新型的變電站——現代緊湊型變電站,綜合了這2種變電站的優點。以下將從技術經濟最佳化出發,討論現代緊湊型變電站及其基於現代微機、光電、通信技術的一次和二次設備集成技術,並分析這種變電站所產生的技術經濟效益。
電樞繞組由一定數目的電樞線圈按一定的規律連線組成,他是直流電機的電路部分,也是感生電動勢,產生電磁轉矩進行機電能量轉換的部分。線圈用絕緣的圓形或矩形截面的導線繞成,分上下兩層嵌放在電樞鐵心槽內,上下層以及線圈與電樞鐵心之間都要妥善地絕緣,並用槽楔壓緊。大型電機電樞繞組的端部通常緊扎在繞組支架上。電樞繞組分直流電樞繞組和交流電樞繞組兩大類。它們分別用於直流電機和交流電機。
水輪發電機導軸承的檢修
一般發電機導軸承都採用分塊瓦稀油潤滑結構,與水輪機水導軸承中分塊瓦稀油潤滑結構相同。
發電機導軸承主要檢修工作是導軸瓦的修理和刮削.導軸承間隙的調整,三個導軸承同心度的調整等。
1.導軸瓦的修理
在拆導軸瓦前,應測量導軸承的間隙,並作記錄,測量方法與水導軸承相同。
將軸瓦鬆開,放在墊有木塊的地面上,檢查軸瓦表面的磨損情況。通常軸瓦磨損並不嚴重,局部被磨損,可用平刮刀颳去高點,再重新挑花。若局部區域磨損嚴重,如出現條狀溝或由於軸電流使鎢金被損壞時,須採用熔焊的辦法進行處理,處理後的軸瓦要進行研磨和刮削,並修刮進油邊,達到有關技術要求。
2.導軸承裝復
(1)導軸瓦裝復應符合下列要求:
1)軸瓦裝復應在機組軸線及推力瓦受力調整合格後,水輪機止漏環間隙及發電機氣隙均符合要求.即機組軸線處於實際迴轉中心位置的條件下進行。一般應在軸承固定部分適當位置建立測點,並記錄有關數據.以方便複查軸承中心位置。
2)導軸瓦裝配後,間隙調整應根據主軸中心位置。並考慮盤車的擺度方位、大小,進行間隙調整。安裝總間隙應符合設計要求。
3)導軸瓦間隙調整前,必須檢查所有軸瓦是否已頂緊靠在軸領上。
4)分塊式導軸瓦間隙允許偏差不應超過±0.02mm。
(2)導軸領表面應光亮,對局部軸電流燒損或劃痕.可先用天然油石磨去毛刺,再用細毛氈、研磨膏研磨拋光。軸領清掃時,必須清掃外表面及油孔。
(3)導軸承裝復後應符合的要求。
1)導軸承油槽清掃後進行煤油滲漏試驗,至少保持4h,應無滲漏現象。
2)油質應合格,油位高度應符合設計要求,偏差不超過±10mm。
3)導軸承冷卻器應按設計要求的試驗壓力進行耐壓試驗。設計無規定時,試驗壓力一般為工作壓力的兩倍,但不得低於0.4MPa,保持60min,無滲漏現象。