發動機冷測試試驗原理
發動機冷測試試驗是用來檢測內燃機裝配質量的一種方法。當採用冷測試技術檢測發動機時,發動機不需要燃料來運行,也不需要冷卻液進行冷卻。被測試的發動機進入測試台,通過氣缸或液壓缸夾緊發動機的進氣、排氣口,同時通過專用機油壓力適配器連線到設備上,用抱爪或其他夾緊機構自動夾緊發動機的飛輪或適配器,測試台的伺服電機驅動發動機以不同的速度旋轉,與此同時,測試系統通過數據採集卡同時從發動機進氣口、出氣口、夾緊機構的扭矩感測器以及主油道出口的壓力感測器上採集數據,採集到的測試數據通過測試台專用軟體進行分析,然後將分析結果與測試台已設定好的極限值進行比較,從而確定發動機是否被正確裝配。
另外,設備通過測試程式對發動機上相關感測器傳送執行操作的指令,同時發動機各種感測器及執行器也通過CAN-Line或K-Line將反饋信號反饋給測試台,測試台軟體對發動機反饋的各種信息進行一系列的分析比較,最終確定發動機各感測器及執行器是否正常工作。
發動機冷測試試驗中的機械性能測試
發動機冷測試試驗中的機械性能測試,主要有扭矩測試(包括脫離扭矩、運轉扭矩、監控扭矩等)、進氣真空度測試、排氣壓力測試、機油壓力測試、正時機構測試等。
脫離扭矩測試
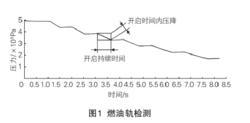
發動機從靜止狀態到開始運動的瞬間所產生的扭矩,稱為脫離扭矩。脫離扭矩的檢測主要是為了確認發動機內部各運動部件之間的配合是否有缺陷,例如軸瓦漏裝、活塞錯裝等。如果脫離扭矩過高,設備會自動停止運行並報警,要求操作人員檢測故障所在並解決,以避免高速運轉造成發動機不可逆轉的損壞,降低生產報廢成本。
燃油軌檢測
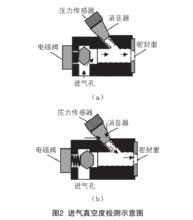
發動機的燃油噴射系統在出廠前都會進行一系列嚴格的測試以確保其質量,但在運輸及裝配過程中,不可避免的會有一定比率的磕碰及其他損傷情況,故有必要在冷測試中對其進行檢測。
一般對燃油軌的檢測方式是,向燃油軌內通入相當於發動機工作狀態時汽油壓力的壓縮空氣,然後由測試程式控制燃油噴嘴逐個開啟、關閉,通過檢測燃油噴嘴的開啟時間及壓縮空氣的壓降情況,來確定燃油軌的零件及裝配質量。見圖1。
進氣真空度測試
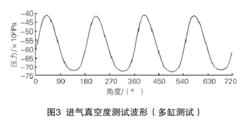
通過安裝在進氣側的壓力感測器測量進氣真空度的變化情況,可以檢測出氣門泄漏,進氣歧管墊片的折損或漏、錯裝,真空管路的連線情況等。
圖2所示為進氣真空度檢測裝置的示意圖。密封面一側連線的是發動機進氣歧管,另一側的電磁閥控制氣路走向,有壓力感測器與氣路相通。當不進行進氣真空度的檢測時,電磁閥控制閥門打開,氣道走向通往大氣,發動機正常進氣(圖2a);當進行進氣真空度的檢測時,電磁閥控制閥門關閉,氣體通過消聲器以一定的流量進入發動機,通過連通在消聲器一側的壓力感測器檢測到產生的進氣真空度(圖2b)。
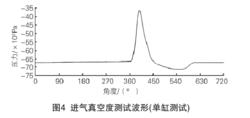
根據發動機整機測試的規劃,可以將進氣真空度測試分為單缸測試與整機測試。所謂整機測試,即將進氣歧管裝配好,在節氣門處連線管路到感測器,對發動機整體進氣真空度進行測量,見圖3。
所謂單缸測試即不裝進氣歧管,每個密封裝置對應於密封各個氣缸的進氣口分別進行檢測。這種測試方式的優點是精確度高,能夠迅速確定進氣故障的根源所在;缺點是由於沒有裝進氣歧管,無法檢測進氣歧管的整體性能及其裝配情況。見圖4。
排氣壓力測試
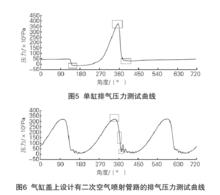
發動機冷測試中的排氣壓力測試,即移去排氣管,在每個氣缸對應的排氣口安裝獨立的壓力感測器進行排氣連線埠的壓力測量。其檢測裝置和進氣真空度的檢測裝置原理是相同的,可參考圖2。
根據不同的發動機構造,排氣壓力測試的曲線又有多種形式。圖5所示是一種比較常見的單缸排氣壓力測試曲線。圖6所示是在氣缸蓋上設計有二次空氣噴射管路的排氣壓力測試曲線。
排氣壓力測試與進氣真空度測試相結合,可以用來檢測進、排氣系統的缺陷,如檢測氣門安裝是否到位、氣缸是否存在漏點、活塞環是否完全張開、正時系統及可變正時系統是否正確裝配,以及凸輪軸和液壓挺柱的裝配缺陷等。
扭矩測試
在伺服電機與發動機夾緊裝置之間,有一扭矩感測器,在伺服電機驅動發動機運轉的時候,通過該感測器便可以實時檢測到作用在驅動軸上的力矩。在扭矩感測器之後,有一個超速離合器,在運轉扭矩嚴重超載時可起到保護扭矩感測器的作用,見圖7。扭矩測試波形見圖8。
機油壓力測試
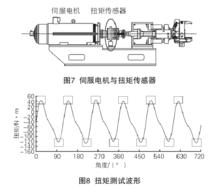
機油潤滑是發動機運轉過程中不可缺少的潤滑劑,如果缺少足夠的潤滑,那么發動機會產生劃傷、抱軸、軸瓦磨損等情況。因此,在測試過程中,必須要保證發動機有足夠的機油壓力。另外,在特定轉速時機油壓力的波動值也能體現發動機的某些零件的裝配情況,如主軸軸瓦、主油道等。
對機油壓力的測試,主要設定有監控油壓、低速油壓、高速油壓測試。
監控油壓主要是為了確保在發動機整個測試循環過程中,各個相對運動件有足夠的潤滑。低速油壓是為了檢測發動機主要零部件的裝配情況,如曲軸、主軸軸瓦等。高速油壓主要檢測機油泵的卸荷閥(限壓閥)是否能正確開啟,防止發動機在高速運轉時因機油壓力過高而產生損壞。
發動機正時系統測試
發動機正時系統的檢測是一項綜合的工作,對於有精確角度控制的發動機來講,在冷測試中可以精確地檢測到脈衝輪的安裝角度,因此也就非常容易地確定正時系統安裝是否正確。對於這種類型的發動機,我們在設定參數時,一般會將參數範圍設定為一個飛輪齒的寬度。
目前,大部分2.0 L排量以下的發動機,對曲軸位置及凸輪軸位置的檢測,並沒有精確到檢測出每一時刻凸輪軸所處的角度,因此需要通過排氣壓力、運轉扭矩等機械性能測試項來間接地檢測發動機正時系統裝配是否正確。例如,可以通過檢測所有氣缸扭矩的零點位置所處的角度值來判斷正時系統安裝是否正確;另外,也可以通過排氣壓力發生轉折時的角度來確定正時系統的安裝情況。
其他機械性能參數的測試
對某些套用了可變正時技術的發動機,在冷測試試驗時還需要進一步檢測可變正時調節系統的工作狀況。