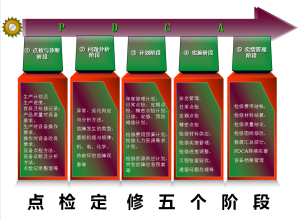
定義:
點檢定修是以點檢管理為核心,在推行設備點檢管理的基礎上,依據設備技術狀態,確定設備的檢修周期和檢修項目,在確保檢修間隔內的設備穩定、可靠運行的基礎上,做到使連續生產系統的設備停修時間最短。將檢修負荷壓到最低限、強化減少維修停機(停產)時間、實現可預測的均衡修理負荷的一種維修方式。
點檢定修制,點檢人員既負責設備點檢,又負責設備管理、運行、檢修等,是設備維修的擔當者、組織者和管理者。
點檢定修制提出了對設備進行動態管理的要求,要求運行方、檢修方和管理方都要參與圍繞設備的PDCA管理,使設備的各項技術指標符合四保持要求,延長設備服役期,達到故障為零、狀態受控。
核心:
在點檢定修制中,點檢人員是設備管理的責任主體,既負責設備點檢,又負責設備全過程管理,點檢、運行、檢修三方面之間,點檢員處於核心地位
特點:
⑴傾向性管理:它是從嚴格周期修理制度發展為以狀態為主的項目修理制度。每個制度雖然也有周期,但僅作參考,主要依據設備狀態來確定修理時間和內容。防止過維修和欠維修現象的發生。
⑵堅持預防為主:其指導思想是以“防”為主,改變以往以修為主的傳統思想,因此可以最大限度地減少事故和故障發生。
⑶建立四大標準:點檢定修制建有一套較為完整的點檢管理標準體系(即四大標準),點檢就是把設備可能發生劣化和故障的部位,設定若干個點,明確規定出標準管理值(檢修標準值),點檢周期和點檢方法,並指定人員,即實行“八定”管理的點檢管理體系,這是貫徹執行點檢定修制的技術基礎和依據。
⑷建立以點檢為核心的管理體制:整個維修管理重心下移,讓最了解最熟悉現場設備技術狀況的點檢人員來掌握編制計畫大權。因為他們最有發言權,能夠達到預防為主的目的,甚至日修、定修的現場指揮也讓點檢方擔當,這樣減少了傳統管理的多餘層次和環節,信息反饋暢通,使用與管理不脫節,利於實現高效管理。
⑸管理目標集中:減少設備故障,降低維修費用,有利於提高檢修效率
⑹突出為產品服務的觀念:由於每個檢修工程項目在實施中都有標準可依,並且主控項目都有工時工序表,因而計畫的命中率很高,這樣既保證了生產計畫的正常執行,又滿足了檢修工程的要求,體現了生產與檢修的統一協調性。
⑺實行全員管理:凡參加生產過程的人員都要關心和參加設備維護工作,特別是操作人員負有用好、緊固、清掃、補油、調整、小修理和日常點檢業務,使生產人員與點檢方融為一體,成為全員管理的基礎
⑻採用PDCA工作法:點檢定修制在管理上採用PDCA工作方法,各級管理層每月召開一次實績分析會(班組→作業區→車間(分廠)→設備部,自下而上召開),逐級提供資料,用數據和圖表來分析當月設備狀態、檢修工程實施及維修費用使用等情況,並提出改進對策和實施措施
⑼堅持安全第一:點檢定修制堅持安全第一的方針,實行開展安全確認制度,危險預知活動,安全會診活動三項有效措施,尤其是堅持貫徹執行點檢方、檢修方、生產方(運行方)的三方掛(摘)牌制度或【鎖定標定】制度,這對防止人身傷害事故的發生起到了應有的作用。
⑽員工技能的多樣化:由於點檢定修制自身的要求和設備現自動化水平的逐步提高,維修技術的日益發展,對操作、點檢、修理人員的素質要求也愈來愈高,團隊成員間活用一言教室進行技能傳承。
實質:
設備點檢制與設備定修制的有機結合。
基本特徵:
生產操作人員具有的設備管理與維修責任,以崗位點檢(操作點檢)的形式進行確認和體現。
有一支專職點檢員隊伍從事定期點檢,並行使設備現場管理基本職能,同時,對設備現場管理實行作業區制(區域責任制)。
有一套完善的點檢基準和相關的技術或作業標準,包括點檢標準、潤滑標準、維修技術標準和作業標準及其相應的業務作業流程,合理的責權關係和推進工作的技術組織保障。
有完備的用於點檢、檢測和分析的檢測儀器、檢測手段和完善的檢維修管理體
五個階段:
①點檢與診斷階段
生產計畫及
生產進度,
夜班及搶修記錄;
產品質量對設備要求,
生產對設備操作要求,
操作對設備改良要求,
設備點檢方法,
設備診斷及分析方法,
點檢記錄整理等
②問題分析階段
異常、劣化判定與分析方法,
故障發生的類型,
磨損機理與規律,
機、電、化學、熱破壞的故障現象等
③計畫階段
年度修理計畫,
日常點檢、定期點檢、精密點檢計畫,
日修、定修、預防維修計畫,
檢修費用預算計畫,
檢修人力資源需求計畫,
檢修資源供應計畫,
突發故障應急預案等
④實施階段
安全管理,
日常點檢
定期點檢
精密點檢
檢修材料供應,
檢修實施管理,
檢修進度調整,
工程檢查驗收,
遺留問題處理等
⑤實績管理階段
檢修費用結帳,
檢修材料結算,
檢修質量結論,
檢修圖紙修改,
數據匯總統計,
PDCA持續完善
設備檔案管理等