概念
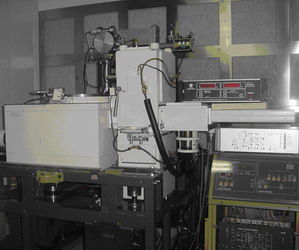
電子束加工是由德國的科學家K.H.施泰格瓦爾特於1948年發明的。作為加熱工具,電子束的特點是功率高和功率密度大,能在瞬間把能量傳給工件,電子束的參數和位置可以精確和迅速地調節,能用計算機控制並在無污染的真空中進行加工。根據電子束功率密度和電子束與材料作用時間的不同,可以完成各種不同的加工。
加工原理
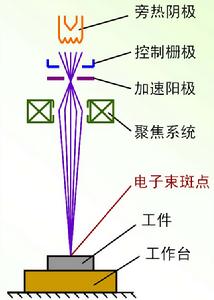
特點
1.是一種精密微細的加工方法。2.非接觸式加工,不會產生應力和變形。
3.加工速度很快,能量使用率可高達90%。
4.加工過程可自動化。
5.在真空腔中進行,污染少,材料加工表面不氧化。
6.電子束加工需要一整套專用設備和真空系統,價格較貴。
分類
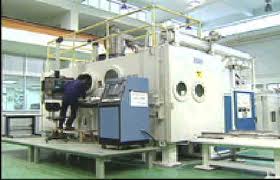
電子束功率密度達105~106瓦/厘米2時,電子束轟擊處的材料即局部熔化;當電子束相對工件移動,熔化的金屬即不斷固化,利用這個現象可以進行材料的焊接。電子束焊具有深熔的特點,焊縫的深寬比可達20:1甚至50:1。這是因為當電子束功率密度較大時,電子束給予焊接區的功率遠大於從焊接區導走的功率。利用電子束焊的這一特點可實現多種特殊焊接方式。利用電子束幾乎可以焊接任何材料,包括難熔金屬(W、Mo、Ta、Nb)、活潑金屬(Be、Ti、Zr、U)、超合金和陶瓷等。此外,電子束焊接的焊縫位置精確可控、焊接質量高、速度快,在核、航空、火箭、電子、汽車等工業中可用作精密焊接。在重工業中,電子束焊機的功率已達100千瓦,可平焊厚度為200毫米的不鏽鋼板。對大工件焊接時須採用大體積真空室,或在焊接處形成可移動的局部真空。
2、電子束刻蝕和電子束鑽孔
用聚焦方法得到很細的、功率密度為 106~108瓦/厘米2的電子束周期地轟擊材料表面的固定點,適當控制電子束轟擊時間和休止時間的比例,可使被轟擊處的材料迅速蒸發而避免周圍材料的熔化,這樣就可以實現電子束刻蝕、鑽孔或切割。同電子束焊接相比,電了束刻蝕、鑽孔、切割所用的電子束功率密度更大而作用時間較短。電子束可在厚度為0.1~6毫米的任何材料的薄片上鑽直徑為1至幾百微米的孔,能獲得很大的深度-孔徑比,例如在厚度為 0.3毫米的寶石軸承上鑽直徑為25微米的孔。電子束還適合在薄片(例如燃氣輪機葉片)上高速大量地鑽孔。
3、電子束熔煉
電子束熔煉法發明於1907年,但直到50年代才用於熔煉難熔金屬,後來又用於熔煉活潑金屬(如Ti錠)和高級合金鋼。電子束加熱可使材料在真空中維持熔化狀態並保持很長時間,實現材料的去氣和雜質的選擇性蒸發,可用來製備高純材料。電子束加熱是電能轉為熱能的有效方式之一,大約有50%功率用於熔化和維持液化。功率在60千瓦以下的電子束熔煉機可用直熱式鎢絲作為電子槍的陰極。60千瓦以上熔煉機的電子槍則用間熱式塊狀鉭陰極,它由背後的鎢絲所發射的電子轟擊加熱到 2700K,可有每平方厘米為幾安的發射電流密度。電子槍加速電壓約30千伏,這樣容易防止電擊穿和減弱 X射線輻射,電子束用磁聚焦和磁偏轉。電子槍和熔煉室用不同的真空泵抽氣,真空度分別維持在10-3和10-1帕左右。80年代已生產出600千瓦級的電子槍。如需更大功率,可用幾支電子槍同時工作。利用電子束加熱可鑄造100噸的坯料。
加工裝置
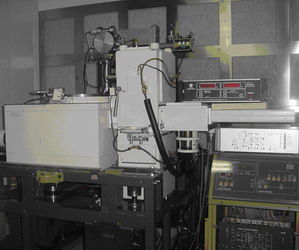
1、電子槍是獲得電子束的裝置,它包括電子發射陰極、控制柵極和加速陽極等。其中陰極經電流加熱發射電子,帶負電荷的電子高速飛向帶高電位的正極,在飛向正極的過程中,經過加速,又通過電磁鏡把電子束聚焦成很小的束流。(1)發射陰極一般用純鎢或鉭做成陰極。大大功率時用鉭做成塊狀陰極。在電子束打孔裝置中,電子槍陰極在工作過各中受到損耗,因此每過10~30 h就得進行定期更換。
(2)控制柵極為中間有孔的圓筒形,其上加以較陰極為負的偏壓,既能控制電子束的的強弱,以有初步的聚集作用。(3)加速陽極通常接地,而在陰極加以很高的負電壓以驅使電子加速。
2、真空系統是為了保證在電子束加工時達到1.33x10-2~1.33x10-4Pa的真空度。因為只有在高真空時,電子才能高速運動。為了消除加工時的金屬蒸氣影響電子發射,使其不穩定現象,需要不斷地把加工中產生的金屬蒸氣抽去。它一般由機械鏇轉泵和油擴散泵或渦輪分子泵兩部分組成,先用機械鏇轉泵把真空室抽至1.4~0.14Pa的初步真空度,然後由油擴散泵或渦輪分子泵抽至0.014~0.00014的高真空度。
3、控制系統是由束流聚焦控制、束流位置控制、束流強度控制以及工作檯位移的控制等組成。
(1)束流聚焦控制是為了提高電子束的的能量密度,使電子束聚焦成很小的束流,它基本上決定著加工點的孔徑或縫寬。聚焦一種是利用高壓靜電場使電子流聚焦成細束;另一種比較可靠是利用“電磁透鏡(實際上是為一電磁線圈,通電後它產生的軸向磁場與電子束中心線相平行,徑向磁場則與中心線垂直。)”靠磁場聚焦。
(2)束流強度控制是為了使電流得到更大的運動速度,常在陰極上加上50~150KV以上的負高壓。加工時,為了避免熱量擴散到不用加工的部位,常使用電子束間歇脈沖性地運動。
(3)工作檯的移控制是為了在加式過程中控制工作檯的位置。如果在大面積加工時有伺服電機控制工作檯移動並與電子束的偏轉相配合將減少像差和影響線性。
套用
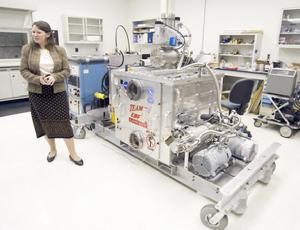
1、高速打孔 ;
2、加工型孔及特殊表面;
3、刻蝕;
4、焊接;
5、熱處理;
6、電子束光刻