概念
防羽布亦稱防絨布、羽絨布是紗線密度較大的薄型織物,由於常用作羽絨服裝、羽絨被、羽絨褥墊等的面料,需要能防止羽絨向外鑽出,所以必須使織物達到高密度,才能有防止羽絨鑽出來的效果。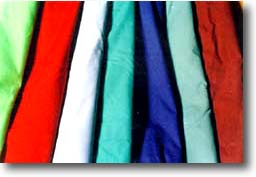
發展變遷
初期高密府綢在織造時遭遇很大的難度,幾經技改攻關終於取得成功,進而推而廣之。我國於20世紀70年代中期開始研製高密防羽布,當時在有梭織機上最早起步於CJ14.6/14.6523.5/283.5119.5府綢基礎上開發的窄幅防羽布,僅提高緯密,使織物總緊度達到88.45%,成品加工後縫製羽絨服,基本能滿足防漏絨的功能要求。接著於20世紀70年代後期,在有梭織機上又開發了170cm中幅防羽布,用來拼幅製作防羽布被出口,品種規格也有所擴展。鑒於當時我國紡織漿料的實際情況,採用的是PVA+玉米原澱粉+PAAm、CMC的“高濃高粘”混合漿料,加上在G142C型漿紗機較低壓漿力的條件下進行上漿,上漿率較高,漿膜脆硬,分絞困難,容易剝落,且並絞嚴重。當織造車間相對濕度超過75%以上,或黃梅季節漿軸經紗回潮超過9%時,經紗容易出現再粘,落漿短纖易積聚在停經片處,給防羽布織造帶來極大的困難。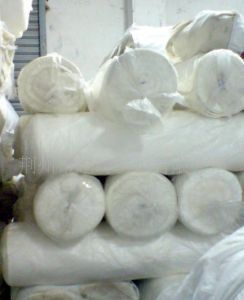
從20世紀80年代開始,在原紡織工業部的直接倡導和組織下,我國變性澱粉的開發套用有了較好的起步和進展。當時我們採用了第一代變性澱粉--酸解澱粉(18mPa•s~20mPa•s)替代原澱粉上漿,其他漿料成分不變,漿液粘度有所降低,且熱穩定性也有提高。有利於漿液滲透,增強粘結能力,漿膜性能也有改善,使中幅防羽布的可織性大大提高,也為開發更寬幅防羽布創造了一定的條件。
20世紀80年代中期,我們引進美國西點WP200型雙漿槽漿紗機、280cm雙織軸PU型和P7100型片梭織機,首先開發生產239cm及以上細號、特細號寬幅防羽布,為製作多種規格的獨幅羽絨被褥出口奠定了基礎。隨後,280cm雙織軸的噴氣織機也逐步推出,織制寬幅防羽布。儘管當時選用的酸解澱粉與PVA混合漿是“高濃中粘”漿料(30s左右),由於採用分層上漿之後,每個漿槽的實際漿紗覆蓋率僅25%~30%,漿液在擠壓區的流失也不多,基本上能適應片梭織機和噴氣織機雙織軸聯動織造寬幅防羽布的要求。
20世紀90年代開始,我國紡織漿料發展較快,國外新漿料也大量進入中國市場,漿料品種繁多,可選用的空間擴大。到目前為止,基本形成以PVA(1799+0588)+變性澱粉+聚丙烯酸類的“高濃低粘”混合漿料,而且逐步推廣套用“兩高一低”高壓上漿新工藝,使細號、特細號寬幅防羽布生產出現了新的發展階段。 經過30年來的生產實踐和探索,證明了細號、特細號高密防羽布的生產是隨著原紗質量的提高、漿料與漿紗技術的發展以及無梭織機先進織造技術的發展而逐步發展壯大。目前以片梭織機和噴氣織機織造寬幅防羽布最為適宜。由於兩種無梭織機的機械特性和引緯方式不同,生產工藝技術上出現的問題和要求也有所不同,對原紗質量、漿料選配和漿紗工藝。
噴氣機織造
經緯紗強力問題
眾所周知,無梭織機對原紗的質量要求應以強力和毛羽為兩大重點,而強力是主因。兩種織機對經緯紗的強力要求也有所不同。A經紗強力
片梭織機的寬幅入緯率一般為900m/min~1200m/min,而噴氣織機的寬幅入緯率為1100m/min~1500m/min。相同規格的寬幅防羽布,噴氣織機入緯率要高於片梭織機入緯率15%~25%。雖然兩者都採用“小開口、大張力”的上機工藝路線,但是,噴氣織機經紗承受的反覆拉伸負荷遠比片梭織機要高。在開口和打緯過程中,經紗的張力峰值如果與經紗的強力弱環負荷重疊時,容易產生斷經,而噴氣織機的斷經幾率也比片梭織機高。
B緯紗強力
片梭織機屬積極引緯,可控制性較好,其引緯張力變化見圖1。當片梭在引緯箱被加速到最大速度時進行擊梭,緯紗出現第一個始投張力峰值a。當片梭自由飛行逐步降速至接梭箱被制動時,緯紗出現第二個制動張力峰值b。片梭的始投張力峰值較高,斷緯往往發生在始投張力峰值與緯紗強力弱環的負荷重疊處。由於片梭始投張力的加速僅作用在開始的一小段緯紗上,所以斷緯的幾率就較小。
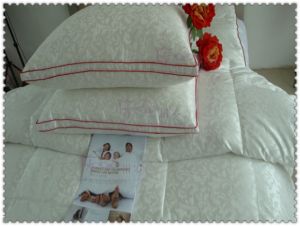
織物的透氣防絨問題
防羽布的基本功能性要求是:做成製品填充羽絨後必須具有防漏絨的性能及使用時透氣、柔軟、舒適的感覺。德國克爾勃?緒爾(K&S)公司有專用的檢測防羽絨儀器,我國現在普遍採用測定織物透氣量來控制防絨效果。防羽布的透氣量(L/m2?S)與防羽絨(漏絨)效果有著很強的相關性,一般都以染整加工後的最終成品測定的透氣量為準。測定坯布的透氣量僅作為設計坯布規格和控制織物緊度的參考指標,因為它與原紗的號數偏差、毛羽程度及上漿工藝有關,具有相當大的離散性。但是,在一定程度上還是可以反映織物的防絨效果。兩種織機防羽布的透氣量都是呈“中間大、兩邊小”的趨勢,而噴氣防羽布透氣量的極差為34.2L/m2S,明顯大於片梭防羽布的極差。與平均值相比,噴氣防羽布透氣量極差相差24.6%,片梭防羽布極差僅相差14.3%,噴氣防羽布的透氣量高。為了縮小兩者差異,根據客戶需求,適當增加噴氣防羽布的緯密(由614根/10cm改為622根/10cm),使織物透氣量均值降為136L/m2?S左右。由此可知,在設計寬幅防羽布時,噴氣防羽布的經緯紗總根數應略大於片梭防羽布。如果織造170cm中幅防羽布,影響較小,兩種織機的經緯紗總根數可以接近。
現在防羽布規格比較紊亂,即使經緯紗總根數小於上述測試品種規格,好像後道工序也沒有反映出漏絨問題。我們認為,這主要取決於後道染整工藝的加工情況。防羽布有一防(防絨)、二防(防絨、防水)之分,為此染整也有一軋(光)、二軋(光)之工藝,前者縮率小,後者縮率大;另外為防水也有表面浸漬溶液烘乾後再進行三軋(光)之工藝。這樣,織物的縮率和緊密程度不同,其防絨效果也就不一樣。
目前,我國防羽布的透氣量還沒有一個統一的標準範圍,各企業都是自訂內控標準進行控制。根據我們的實踐經驗,羽絨坯布透氣量一般控制在130L/m2?S~136L/m2S,織物總緊度平紋控制在87%以上,斜紋控制在90%~92%以上,緞紋及小提花控制在93%以上,基本可滿足後道染整各種加工工藝的需要。透氣量過於偏小,也不利於羽絨製品的透氣舒適性。考慮到測試數據離散性較大,宜增加測試子樣,取其集中範圍作參考。
梭織機織造
有梭織機織造純棉細號防羽布,難點在於織機覆蓋係數高,上漿難度大,織造打緯阻力大,織造難度大。通過最佳化漿料配方和漿紗工藝,各工序採用合理工藝及相應的技術措施,有效地提高了織機效率。隨著紡織機械的發展,有梭織機在品種適應性上明顯處於劣勢。自1993年以來陸續引進噴氣織機,獲得了較好的經濟效益。而有梭織機的品種問題一直困擾著公司,對此我們進行了分析和品種定位。為了降低生產成本,提高市場競爭力,我們用純棉普梳紗在有梭織機上開發生產純棉高密防羽布,其規格為C14.6/14.6524/394170。1 難點分析
有梭織機生產防羽布有兩個難點:一是經紗上漿難度大,要求高;二是織機覆蓋係數較高,經紗間摩擦大,緯密大,打緯阻力大。不僅對織機設備水平、工藝水平、操作水平是嚴峻的考驗,而且對經紗上漿質量也是嚴峻考驗。漿紗質量的好壞直接影響著織機的斷頭率、開台效率、產品質量等等。生產初期出現的主要問題有:①織軸倒斷頭較多;②織機斷經率較高(達1.5根/台•h),且斷頭多在綜絲織口處;③停經片處結花較多;④經紗斷頭斷一撮現象較多,操作難處理,影響開台效率;⑤布面回退,無故停台較高;⑥斷緯較多(達0.9根/台•h左右);⑦邊撐疵較多。針對以上問題,我們從原紗入手,對各道工序採取措施進行解決。2 原紗質量
在不改變配棉和不增加成本的情況下,改善紗線強力不勻率,降低強力CV值,提高紗線最低強力,減少片紗中的弱環,消除斷頭隱患。要求電子清紗能有效清除紗疵。經實踐,成紗質量達如下水平,對織造比較有利;C14.6tex單紗斷裂強度達12.1cN/tex以上,單強CV值控制在10%以內,條幹CV值控制在17%以下,細節控制在烏斯特89公報25%水平,粗節、棉結控制在烏斯特89公報50%水平,十萬米紗疵控制在烏斯特公報50%水平,3mm及以上毛羽控制在30個/m以下。3 漿紗工藝及技術措施
3.1漿紗工藝純棉細號高密織物的紗號細,強力低,漿料配方採用了傳統的高比例PVA-1799加變性澱粉及丙烯類漿料,且最初我們採用中壓上漿,經上機效果不太理想,織機出現經紗斷頭高、斷一撮、停經片結花等現象,分析原因如下:(1)漿液粘度偏高,滲透增強不夠,表面上漿;(2)漿膜強度大,乾分絞困難,再生毛羽多。針對以上原因,我們調整了漿紗工藝,因PVA-1799聚合度高,漿膜強度大,造成分紗困難,因此減少PVA-1799用量,多用變性澱粉,同時加入了PVA-205MB,並降低了漿液粘度,加大壓漿輥壓力,採用“兩高一低”的上漿工藝,織機效率大幅度提高。
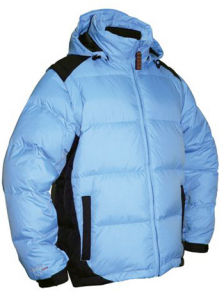
(1)經軸退繞張力要小而均勻,退繞加壓裝置要勤檢修,經軸架氣缸壓力隨經軸直徑減小逐漸減小。
(2)調整好“五段張力”,張力宜小不宜大,減小紗線的彈性損失。
(3)漿紗回潮率控制在6%左右。
(4)兩漿槽餵入張力要一致,濕態保持鬆弛狀態。
(5)織軸纏筘齒要均勻,每兩隻軸放一次絞紗,減少並絞。
4 織造工序
4.1原因分析GA615-190型有梭織機織造純棉細號防羽布覆蓋係數高,難度大,問題多。上機初期我們遇到了布面回退、斷緯多、無故停台高、邊撐疵等難題。分析原因如下:(1)緯密太高,打緯阻力大,緯紗弱環在打緯時發生斷頭;(2)卷取裝置不太適合,造成布面回退,使斷緯自停裝置作用造成無故停台。
4.2技術措施
針對以上織造問題,我們採取了以下措施。
(1)改變提綜方法,由13,24提綜改為14,23提綜,有效減小了綜框摩擦及紗線之間的摩擦;
(2)改變停經片穿法,由1234順穿改為11223344重疊穿法,實踐證明此種穿法在斷經時停經片易於落下,有效地增強了斷頭自停裝置的靈敏度;
(3)杜絕停經刻齒棒等停經裝置的不平直現象,使落下的停經片及時被夾住,保證斷頭自停的靈敏度;
(4)梭內採取措施,不增加緯紗退繞張力;
(5)梭庫尺寸與梭子配合合理,避免梭子出入梭庫時軋斷緯紗;
(6)增加筘座重量,增強打緯力度,保證慣性打緯力大於打緯阻力;
(7)改變卷取彈簧力矩,增加卷取力量,縮短卷取刺毛皮整修更換周期,加大布面張力,杜絕了布面回退,減少了無故停台;
(8)上機張力稍大,可以減少邊撐疵;
(9)織造車間相對濕度控制在75%~83%,保證正常開車;
(10)停經架位置後移,減小開口經紗張力,提高開台效率;
(11)採用綜框導軌裝置,避免綜框抖動、碰撞,減少“三跳”織疵,提高布面質量。
通過改變漿紗工藝及對上機工藝進行調整,織造經向斷頭由1.8根/台•h減少為0.75根/台•h,緯向斷頭由0.89根/台•h減少為0.38根/台•h,無故停台由0.95次/台•h減少為0.3次/台•h以下,效率由75%提高到88%。