熱裝分類
根據鑄坯入爐溫度分為連鑄坯直接熱裝和連鑄坯熱裝兩種形式。
(1)連鑄坯直接熱裝軋制,簡稱CC-DHCR。連鑄坯溫度在A3以下,A1以上,鑄坯直接送加熱爐加熱後軋制。加熱爐在連鑄機和軋機間起緩衝作用。鑄坯處於γ+α兩相區,鑄坯組織部分經過γ→α→γ相變,既有原始粗大的奧氏體晶粒,又有經相變的奧氏體細晶粒,經加熱後的鑄坯為混晶組織,微量元素的析出和溶解程度不同,需採取相應的軋制工藝,以獲得質量優良的最終產品。此外,對一些低合金鋼和中、高碳鋼等,特別是電爐鋼,由於氮含量較高,還需注意因AlN析出而形成表面裂紋,導致表面質量變壞而不能實行直接熱裝。
(2)連鑄坯熱裝軋制,簡稱CC-HCR。連鑄坯溫度在A1以下,400℃以上,鑄坯不放冷即送保溫設備(保溫坑、保溫車和保溫箱等)中保溫,然後再送加熱爐加熱後軋制。保溫設備在連鑄機和加熱爐之間起緩衝和協調作用,使生產工序匹配和物流管理具有更大的靈活性。其鑄坯組織狀態與常規冷裝爐鑄坯狀態基本相同。但對於某些低合金鋼、中高碳鋼,在冷卻過程中易產生裂紋,熱裝導致表面變壞。一般將鑄坯溫度達400℃作為熱裝的低溫界限;400℃以下熱裝的節能效果較小,且此時表面已不再氧化,故一般不再稱做熱裝。
作用
連鑄坯熱送的主要作用是:
(1)利用連鑄坯物理顯熱能,節約能源消耗。連鑄坯熱送的節能效果與生產條件、板坯熱裝率和熱裝溫度有關。據資料報導,在500℃熱裝,可減少燃耗30%左右,在800℃熱裝,至少可降低燃耗50%。通常板坯裝爐溫度每升高100℃,可使燃耗減少(63~72)×10kJ/t,即熱裝溫度愈高,節能效果愈顯著。
(2)提高金屬收得率。在連鑄坯熱送工藝中,由於實現了無缺陷鑄坯的生產,取消了傳統工藝中的表面缺陷火焰清理,可使金屬收得率提高2%。其次,傳統工藝冷裝爐加熱產生的氧化鐵皮損失為1%,熱裝爐時降為0.5%~0.7%,加熱時間縮短也減少了氧化鐵皮的生成。
(3)縮短生產周期和生產工藝流程,縮減廠房面積。節約基建投資和生產費用,降低生產成本等。連鑄坯熱送將連鑄與軋鋼兩大工序相連線,實現了連續化生產,向短流程,高效率、節能、節省投資、減少環境污染方面跨進了一大步。實現連鑄坯熱送,要求連鑄與軋鋼工序同步作業,以保證整個系統均衡、不間斷的連續化生產。因此,必須確保熱送過程中物流、能流與信息流的暢通。實現連鑄坯熱送的關鍵技術為無缺陷鑄坯生產技術、高溫鑄坯生產技術、連鑄與連軋的合理銜接與柔性化生產技術和一體化生產管理系統;同時,以改進工藝和設備可靠性的技術相配合。
無缺陷鑄坯生產技術
連鑄坯的缺陷主要有:(1)表面缺陷,如振動痕跡、表面裂紋、表面夾渣、氣孔和氣泡、表面增碳和偏析、凹坑和重皮、切割端面缺陷等;(2)內部缺陷,如內部裂紋、偏析條紋、斷面裂紋和中心星狀裂紋、中心疏鬆、中心偏析、非金屬夾雜物等;(3)形狀缺陷,如鼓肚與菱變等。其中對連鑄坯熱裝影響最大的是表面裂紋缺陷。在傳統工藝中,為清除鑄坯表面缺陷,可在鑄坯精整區進行熱清理。而在連鑄坯熱裝軋制工藝中,為保證鑄坯入爐溫度,無法對鑄坯表面進行熱清理。
實現無缺陷連鑄坯生產的關鍵是冶煉和連鑄工藝的改進。為防止連鑄坯裂紋的產生,從根本上說就是要儘可能增加鋼的抗裂性,避免或減緩各種內應力和外應力,消除可能造成應力集中的薄弱部位。為此,應採取的主要技術措施有:(1)適當調整鋼種成分,嚴格控制S、P、O、N等雜質含量;(2)採用爐外精煉及真空處理技術,進行脫氣除硫,提高鋼水純淨度;(3)採用全程保護澆注,以保證鋼的純淨度,並穩定控制結晶器內液面波動,以利於增加坯殼的厚度和均勻性,減少表面裂紋和夾渣的形成;(4)增大中間罐容量和鋼液深度,設定擋渣牆,促進夾雜上浮排除。調整鋼液溫度,實現低過熱度澆注,並採用連鑄電磁攪拌技術以擴大等軸晶帶,減小中心疏鬆和偏析;(5)改善連鑄二冷制度,採用氣—水噴霧冷卻,實行弱冷、均冷的二冷工藝,並提高矯直溫度以抑制氮化物析出,以防止裂紋缺陷的產生等;(6)提高連鑄設備的對弧精度、加強坯殼支托(如二冷輥分段配置、細輥密排等),採用壓縮鑄造、輕壓下和多點矯直等技術,以減小和分散各種變形應力,防止裂紋產生。
隨著煉鋼和連鑄技術的不斷進步,大部分的普通碳素鋼連鑄坯已基本達到無缺陷的要求。但對某些要求較高的特殊鋼連鑄坯,還應在切斷之後進行熱檢測和熱清理。例如,可用各種探測儀檢測出鑄坯缺陷性質,以聯動火焰清理對缺陷進行熱清理,同時反饋了解產生缺陷的工藝因素,並及時修正。各國鋼廠使用的熱檢測方法中,表面質量檢測主要採用光學法、感應加熱法和渦流法,而內部缺陷的檢測則主要採用超音波和電磁超音波方法。
高溫鑄坯生產技術
為保證鑄坯熱裝,尤其是直接熱裝,必須設法使鑄坯保持較高的溫度。即以充分利用鑄坯內部的冶金潛熱為主,其次才是靠外部加熱。對於鑄坯熱裝工藝主要是使鑄坯保持較高的連鑄機出坯溫度和輸送途中絕熱保溫兩個方面。在連鑄機上儘量利用來自鑄坯內部潛熱主要靠改變澆注速度和冷卻制度來加以控制。由於改變澆注速度要受到煉鋼能力配合和順利拉坯的限制,故變化冷卻制度便成為控制鋼坯溫度的主要手段。一些工廠採取在二冷段上部強冷以防鼓肚和拉漏,在中部緩冷或噴霧冷卻以調整凝固長度,在下部絕熱保溫利用液芯潛熱對凝固外殼進行復熱的冷卻制度,可使連鑄出坯溫度比一般連鑄的大約高出120~180℃。
為了使鑄坯在凝固終點處具有較高的表面溫度,必須將鑄坯凝固終點控制在連鑄機冶金長度的末端處,為此採用電磁超音波檢測的方法(E-MUST)對凝固終端進行檢測與控制,精度可達到±0.5m。對於要嚴格控制氮化物和碳化物析出的鋼種,還必須注意保持容易冷卻的鑄坯邊角部也有較高的溫度,這可在二冷段減少邊角冷卻,甚至在鑄機下部或切割機前後設定邊角部溫度補償加熱器和絕熱罩,來保持所要求的邊角部溫度。為了防止連鑄坯在出連鑄機以後的轉運過程中散熱降溫,近距離輸送通常使用帶保溫罩的絕熱輥道。這種輥道用絕熱材料包覆了鑄坯50%的表面,具有較好的保溫性能。而遠距離輸送則採用高速鑄坯保溫車,這種保溫車除具有保溫功能外,還有使鑄坯均熱的能力。在輸送距離超過1000m時,高速鑄坯保溫車與保溫輥道相比,輸送速度快3倍,輸送時間縮短了2/3,保溫效果提高8倍。兩者具體性能比較見表。
保溫輥道與保溫車使用性能比較
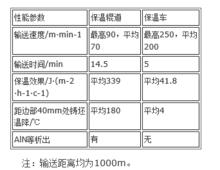
對於連鑄坯低溫熱裝軋制工藝,鑄坯在裝入加熱爐之前往往還採用保溫坑進行鑄坯保溫,允許鑄坯在裝爐之前有更長的等待時間,給生產計畫管理以更大的靈活性。
連鑄與連軋的合理銜接與柔性化生產
連鑄坯熱送將煉鋼、連鑄與軋鋼連線為一個統一的生產體系,必須保證實現煉鋼→連鑄→軋鋼的同期連續生產,也即要求連鑄與連軋之間的合理銜接和柔性化生產,需儘可能減少因更換鑄坯和產品規格品種、軋輥、導衛裝置,改變軋制工藝及事故處理的時間,以保證生產過程的節奏和連續性。這在扁平材連鑄坯熱裝軋制工藝中包括有靈活變更寬度技術、自由規程軋制技術等;在長型材連鑄坯熱裝軋制工藝中則包括有柔性開坯、中軋、精軋技術等。結晶器線上調寬技術已在許多鋼廠得到廣泛套用。一般採用微機控制結晶器的調寬過程,結晶器可按照事先設定的程式自動進行調寬,達到設定的寬度以後即自動停止。調寬速度一般不小於30mm/min,可達64mm/min以上,且在調寬過程中連鑄機的拉速能穩定在1.6m/min。連鑄機雖可進行鑄坯調寬,但一則其能力有限;二則為了穩定澆注作業,穩定煉鋼與連鑄的節奏均衡匹配及減少錐形板坯長度,還應儘量減少結晶器寬度的調節變化,而將調節板坯寬度規格的主要任務交給軋鋼完成。為此,在軋鋼廠要設立調寬軋機、調寬壓力機或立輥軋邊機,以實現寬度大壓下軋制。有的工廠還利用粗軋機組的立輥和使用中間機架(精軋前的M機架)的立輥進行軋邊,提供一種寬度自動控制(AWC)的功能,使軋制因結晶器寬度改變而形成的錐形板坯時,板帶鋼的寬度得到較精確的控制。
自由規程軋制技術
在傳統連鑄與軋鋼生產中,連鑄與軋鋼是兩個獨自進行生產計畫管理的車間。在連鑄車間澆鑄相同寬度、相同鋼種的板坯時必須嚴格按序號澆鑄。在軋鋼車間,由於受到軋輥磨損的限制,必須按每套軋輥先軋寬板後軋窄板的程式進行生產,即所謂的“塔形計畫”。但在實行連鑄坯熱裝軋制時,煉鋼→連鑄→軋鋼三者連成一體,服從於統一的生產計畫,軋鋼不能按傳統的先寬後窄的生產程式獨自安排計畫,而必須服從煉鋼與連鑄的計畫安排。產品必須是寬窄相混,進行所謂“鋸齒形”生產,即進行板寬無規則變化的或程式自由的生產。為了實現自由程式軋制,必須大力減少軋輥的磨損,延長軋輥的使用壽命,保證板帶的板形和厚度精度質量。板寬邊部的溫度比中部要低,而寬度方向的金屬流動在邊部又較大,因此與板帶邊部接觸的軋輥表面局部磨損也要大。為了解決軋輥不均勻磨損問題,用耐磨材料製造工作輥,並在軋制中採用竄輥技術(即移動工作輥的技術,簡稱HCW或WRS),以使磨損得以分散,其影響得以縮小。HCW技術由日本日立製作所於1982年開發並很快得到推廣套用。以後日本川崎鋼鐵公司又進一步開發套用了K-WRS技術,其不同點只是將工作輥做成錐形再進行軸向移動。竄輥技術都是除工作輥做軸向移動以外,還配有強力彎輥裝置以便能同時控制板形與厚度精度質量。
工作輥軸向移動的方法按其目的與效果可分3種:(1)周期移動法,即按一定周期移動工作輥,使軋輥磨損和熱凸度平滑地分散開。採用此種方法還可使軋輥凸度適當相互抵消,使軋輥凸度在一個軋制周期內變動很小,從而使板凸度可以限制在一定的目標值內,提高厚度精度質量。(2)板帶凸度控制法,即通過工作輥的移動,調節工作輥與支持輥輥身沿軸向的接觸長度,藉以消除板端外側部分的工作輥與支持輥之間的負荷分布,抑制作用在工作輥變輥裝置更有效地發揮作用,從而使板帶凸度控制能力得到增強。(3)單側錐形輥位置控制法,即工作輥輥身一端製成錐形,兩錐形工作輥呈反向對稱配置,根據軋件的厚度、寬度,沿軸向移動兩輥錐度位置到最佳值,使板帶邊部軋薄減少及板帶凸度得到改善。為了實現自由程式軋制,除採用移輥技術以外,還需採用板帶凸度與平直度同時控制的技術,高精度軋制技術和自動控制及快速換輥技術。由於連鑄坯直接熱裝工藝使軋鋼作業更趨複雜,這就要求有精確的設定和監視,要求全面計算機自動控制;同時為了維持連續而穩定的生產,必須儘量減少軋機設備的事故和停工時間,以儘快的速度換輥和變換產品規格及鋼種。快速操作也要求自動化,只有自動化才能保證快速度。
一體化生產管理系統
實現連鑄坯直接熱裝軋制,煉鋼→連鑄→熱軋都須準時而穩定地在相同的時序中進行,一處出事,則全線受影響。因此工序節奏匹配和生產計畫管理十分重要,需實行一體化生產管理。生產計畫控制分為生產計畫和實現控制兩個主要階段。在生產計畫階段通過研究訂貨目錄、工序限制條件、生產標準、訂貨和交貨時間等,制定出最佳生產計畫;要安排好煉鋼、連鑄和軋鋼等所有各機組的定期維修和零部件更換時間,做到停工時間最短,各項設備協調良好。現正通過引進人工智慧來開發更先進的生產計畫管理控制系統的技術。在實現控制階段有生產執行管理系統。由於在連鑄坯直接熱裝軋制工藝中從煉鐵、煉鋼直至軋鋼是一種動態的物料流程控制系統,這種生產執行管理系統應該能做到:(1)能預先綜合地制定計畫,控制物料流量;(2)以分鐘為單位精確顯示一組物料的時間表,並能模擬適當的物流線,從而能及時修訂或更換時間表;(3)針對執行時間表,對有關設備、操作和質量項目進行實現進展的實時檢查。通過對每一組物料制度的時間表,使我們能夠對於連續通過幾個生產工序的物料建立準確的控制制度。
改進工藝和設備可靠性的技術
為了穩定維持連鑄坯熱裝軋制生產線正常運行,必須保證每一工序的操作和設備事故降到最低限度,使各項電氣機械設備都能穩定可靠地連續運行。設備的可靠性比較容易理解。所謂工藝的可靠性包括了產量與質量的可靠性及生產持續時間的可靠性。所有這些都應靠設備診斷和工藝診斷技術來保證。要定期進行連鑄機離線設備診斷和維護。對於線上的各種機電設備,特別是支撐和冷卻設備都應經常進行細緻的線上診斷檢查,以便利用澆鑄間隙時間進行檢修。要利用安裝在關鍵部位的各種感測器直接檢查鑄流情況和進行工藝診斷。例如用振動感測器探測結晶器和鑄流的相互摩擦的異常現象等以預報拉漏事故;用電磁超音波法和輥子反作用力法探測鑄坯凝固終端等等。通過及時採取防治措施,保證產品質量和生產線正常進行。