變薄旋壓定義
概念定義:強力旋壓是在普通旋壓基礎上發展起來的一種近無餘量加工方法,其實質為利用旋壓輥子加高壓於坯料,旋轉坯料藉助外力沿成形模具進行局部逐漸輾壓產生塑性變形而變薄,從而得到高精度薄壁迴轉體零件。
研究範圍:強力旋壓研究範圍涉及毛坯、工藝裝備、工藝方法和工具機。毛坯包括材料、形式、狀態及結構設計;工藝裝備包括芯模、尾頂裝置、旋輪裝置和靠模;工藝方法包括旋壓方向、溫度,減薄率、進給率、轉速等因素,冷卻潤滑和分層錯距等。
變薄旋壓的工藝過程
變薄旋壓工藝主要包括剪下旋壓(錐形件的變薄旋壓)和擠出旋壓(筒形件的變薄旋壓),如下圖所示。
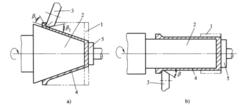
前者用於加工錐形、拋物線形和半球形等異形件,後者用於筒形件和管形件的加工。毛坯1被夾緊在壓桿5與成形芯模2之間並隨主軸一起旋轉,旋導輪3向毛坯作橫向程控,按仿形系統預定的軌跡移動,旋輪與成形芯模之間保持一定的間隙,此時,旋輪對毛坯在旋轉過程中逐點加力使其產生軸向變形,壁厚減薄,最後緊貼於成形芯模上,成為所需形狀的製品。
國外概況
發展過程
1、40年代~50年代末
需求動力:普通旋壓工藝已進入中批和大批生產階段,設備逐步機械化、自動化,強力旋壓工藝就是在普旋工藝的基礎上發展起來的。同時航空航天工業和火箭、飛彈生產的發展也需要更先進的旋壓方法的研究。
主要特點:強力旋壓於四十年代在歐洲民用制鍋、皿等行業中開始被採用,五十年代初傳入美國,首先由PrattWhitney公司與LodgeShipley工具機公司合作製成三台專用強力旋壓機並用於J57等噴氣發動機零件的成批生產,至五十年代末已在美國軍工部門大量套用並獲得迅速發展。在民用工業的套用方面前西德處於領先地位,其他國家如前蘇聯、前東德等則開始對強力旋壓有所研究。
在五十年代採用強力旋壓技術的已有波音、格魯門、通用電器、福特、萊康明、索拉、馬夸特等許多大公司,各公司在工藝方面積累了大量經驗並開始了工藝參數的系統研究,也總結出了一些計算旋壓力的經驗公式等。用強力旋壓加工的材料已經包括從鋁合金到沉澱硬化不鏽鋼等材料,強力旋壓的噴氣發動機零件包括J57、J75等型號的機匣、支承錐盤、空心軸、火焰筒襯套和尾噴管等;飛彈火箭零件則包括錐頭、鐘形及半球形封頭、筒形燃燒室、拉伐爾噴管等等。
2、60年代70年代末
需求動力:隨著飛機、飛彈、太空飛行器產品性能的不斷發展,所用新材料越來越難加工,並且產品尺寸不斷加大,為達到節省材料消耗、解決加工困難、降低成本、減少工時、提高生產率和產品質量的目的,需要進一步發展強旋工藝。
主要特點:六十年代初美國幾乎所有的航空公司都裝備了不同類型的強力旋壓工具機來改進原來的飛彈製造工藝,強旋工藝得到進一步的發展和完善。這個時期英國也開始採用強力旋壓用於噴氣發動機和民用工業。在美國、前東德、前西德、前蘇聯等國家則進一步開展了對強力旋壓的系統研究,包括材料可旋性、變形機理、旋壓力、旋壓件性能以及隆起與脹徑現象等等,而以對旋壓力的研究占比重最大。到了七十年代強力旋壓的材料擴展到了250-300級的馬氏體起高強時效鋼,用電渣重溶鑄造的D6AC超高強度鋼,以及雙金屬板材。重要的製件包括長12米,直徑600毫米的“阿波羅”筒形輸液管、用內旋壓法製造的直徑3米,高1米的“大力神ⅢC”的筒形殼體、用熱旋法製造的“北極星”鎢噴管等等。在其他行業強力旋壓工藝也有所發展,如美國Sargent公司旋制了直徑3米,長6.7米的原子反應堆零件,歐美許多汽車公司都設定了用強力旋壓生產載重汽車變厚度輪轂的自動線,有些公司還用強力旋壓直接生產了高精度細長的缸體。
典型成果和產品:美國研製的“綠色巨人”立式三旋壓輪旋壓機,高12.2米,可旋直徑2280到4060毫米,長到6100毫米的工件,成功地用於旋壓“民兵”、“北極星”飛彈殼體;“馬槍”飛彈氧化劑箱和燃料箱;“短跑”飛彈發射管以及民用金屬製品,化工壓力容器。
3、80年代初~至今
需求動力:航天產品零部件形狀變化範圍越來越廣,精度要求也不斷提高,使強力旋壓工藝需要進一步擴大功能、提高質量、降低成本,並與其他成形工藝相結合,向更高精度和自動化方向發展。
主要特點:八十年代初國外強力旋壓工藝已進入完善提高階段,許多國家都廣泛地採用了強旋技術,其中美國在航空航天產品零部件加工領域套用得最多,前西德在民用工業上套用較多,但也用於軍事工業產品的加工。國外旋壓設備向大型化、強力化、多用途和自動化發展,生產旋壓工具機的主要國家有美國、前西德、日本、前蘇聯、法國和前東德等等,其中以美國生產的旋壓工具機為最多,製造能力最強,多為大型化、強力化設備,前西德製造能力僅次於美國,但使用小型旋壓設備較多。
強力旋壓材料包括鋁合金、銅合金、軟鋼、300系和400系不鏽鋼、鎳合金、超高強度鋼、高溫合金、鈦合金、鎢、鉬、鈮、鋯等難熔金屬等。強力旋壓工藝也廣泛而有效地套用於製造輕重量、高強度的圓筒、圓錐件、半球件、雙曲線形、環形、拉瓦爾管形以及帶凸筋的筒件和管件等等。
現有水平及發展趨勢
強力旋壓是近年來迅速發展的一種近無餘量加工方法,它無切削加工,無材料損耗,經濟效益十分顯著,在國外軍事和民用工業領域得到了相當廣泛的套用。
隨著飛機、飛彈、太空飛行器產品性能的不斷發展,強力旋壓技術在航空航天工業中越來越占據重要地位。美國早在六七十年代幾乎所有的航空航天公司就已裝備了不同類型的強力旋壓工具機來改進原來的飛彈製造工藝。如“宇宙神”洲際飛彈的Ti-6Al-4V鈦合金球形氣瓶的兩個半球件是熱旋壓成形的,每塊坯料的旋壓成形時間為3-5分鐘,採用旋壓方法與一般鍛造/機加方法相比,可降低成本25-35%,交付時間大大縮短。太空梭的多次起動的小型再生冷卻式發動機鎳殼體是由6.35mm×609.6mm×2438.4mm的TD鎳板經熱旋壓而成的,在其表面上用放電成形方法製冷卻液流槽並用電鑄法在槽上鑄成鎳外殼構成再生冷卻式燃燒室。與管束式發動機的工藝相比,該方法比較簡單。目前航空航天強力旋壓產品仍向筒形件、錐形件、半球件、異形件、燃燒室、尾噴管、管件發展,不斷提高精度、降低成本,並與其他工藝聯合套用,如衝壓-旋壓、擠壓-旋壓聯合工藝等。
國外強力旋壓設備正不斷向大型化、強力化、多用途和自動化發展。旋壓工具機先有臥式再有立式,臥式工具機由中、小型發展到大型,立式工具機則由中、大型發展到大型和小型,如前西德萊費爾德公司生產的最大的VDM6000E型立式旋壓機,主軸功率200/250千瓦,加工直徑6m,加工鋼板厚度30mm。旋壓機控制系統也在不斷發展,旋輪座操縱由液壓發展為數控,主軸變速從有級發展到無級,並開發了多旋輪迴轉架旋壓機。加工大直徑零件所需的電視監控系統和壁厚超音波自動測量裝置在旋壓機上得到套用,數控和計算機控制正逐步推廣套用於旋壓控制系統,示教錄返型旋壓機也將適當發展。
國外強力旋壓工藝套用較普遍的國家有美國、前西德、日本、前蘇聯、法國和前東德等。其中美國製造旋壓工具機的能力最強,產量最大,在航空航天領域套用也最多。如“民兵”固體飛彈第一級發動機殼體、“大力神ⅢC”固體發動機端蓋、登月艙燃料箱封頭、太空梭固體助推器殼體等均採用了強力旋壓工藝。美國生產旋壓工具機的公司主要有洛奇西普萊公司、辛辛那提公司、赫福德公司和Spinncraft公司,其旋壓設備傾向於大型化、強力化,如赫福德公司生產的大型立式240型旋壓機可旋壓直徑6米的封頭,並且主要套用於航空航天產品零部件的加工。
前西德的強力旋壓設備製造能力僅次於美國,主要生產廠家有萊費爾德公司和開靈毫斯公司等。前西德民用工業套用強力旋壓工藝較多,使用小型設備也較多,但也用於軍事工業產品的加工,如MBB航空航天公司曾旋壓出幾十種飛彈零件。
多旋輪迴轉架的旋壓機有蘇聯型、西德型和波蘭型。其中前蘇聯研製的多旋輪迴轉架強力旋壓薄殼零件的旋壓機可用於大量成批生產薄殼零件,成形能力大大提高。前蘇聯還開發了衝壓-旋壓聯合工藝等。
主要研究機構
前西德萊費爾德公司,主攻技術及工程:生產22種規格的旋壓工具機,包括各種CNC旋壓機及多旋輪迴轉架的旋壓機,同時開發研究計算機數控技術用於強旋工具機。
前西德開靈毫斯公司,主攻技術及工程:生產各種旋壓工具機,以及與旋壓床配套的各種自動裝置。
美國洛奇·西普萊公司,主攻技術及工程:製造各種強力旋壓設備,對強力旋壓的工藝參數、變形機理、旋壓力、旋壓件性能等進行了系統研究。
美國赫福德公司,主攻技術及工程:製造各種大型旋壓工具機,不斷向強力化發展。
影響
強力旋壓是一種無切削加工,無材料損耗的工藝方法,可節約昂貴的材料費用達70~80%,製造費用和勞動力可節省60%,而且旋壓工具成本比其他方法使用的工具成本減少10~25%。強力旋壓的變形方式便於採用局部加溫進行熱旋,可用來成形稀有金屬、超高強鋼、粉末壓制或特種鑄造的坯料。強力旋壓後的工件一般可達到較高的精度和表面光潔度,材料機械性能明顯改善,強度可提高20~80%,硬度和疲勞強度也得到提高。
強力旋壓也存在局限性,如加工段須為薄壁空心迴轉體,並有一定長度以保證經濟上的合理性;工模具必須使用硬化的高質量材料並經特殊工藝方法處理以承受很大的壓力,因而成本較高;對大型件的旋壓需大型旋壓設備,設備的研製時間較長.投資較大;生產較短的或形狀複雜的零件,或小批量生產時成本比較高。
軍用效益:隨著飛機、飛彈、太空飛行器產品性能的不斷發展,強力旋壓技術在航空航天工業中愈來愈占據重要地位。強力旋壓常用於加工飛彈殼體、端蓋、貯箱封頭、鼻錐體、噴管、壓力容器的各種球形或園柱形氣瓶、管件以及航空發動機噴口、燃燒室錐體、整流罩、壓氣機盤和渦輪軸等零件,經過這種工藝加工後的零件精度高、光度好、壁厚均勻、回彈小,中小零件的直徑和壁厚公差可控制在0.03~0.05mm範圍內,表面粗糙度Ra可小於0.8μm,而且由於強力旋壓為無切屑加工,可提高材料利用率,降低成本。例如“民兵”固體飛彈第一級發動機殼體段改用強力旋壓法,便構成發動機殼體D6鋼環形鍛件由5個減到2個,即用2個經過強力旋壓成形的環形鍛件就可焊成一個完整的筒殼,使原材料費用降低75%,切削加工費節省80%;登月艙燃料箱封頭為2219鋁合金,直徑1270mm,採用強力旋壓工藝後研製周期減縮30%,直接勞動費用減少5%,工具費用減少80%,所需材料減少了80%,每個零件總的費用大約可節省85%。
強旋工藝的優越性使其不僅在飛機、飛彈、太空飛行器上得到廣泛套用,在兵器、艦艇、原子能等領域也日益普遍,包括魚雷外殼、潛望鏡罩、藥形罩、尾管、火箭彈殼體、炮管及反應堆零件等,如美國Sargent公司就採用強力旋壓工藝旋制了直徑3m,長6.7m的原子反應堆零件。
民用效益:強力旋壓技術在車輛、化工、冶金、農業等許多領域的套用日益普及,其典型的部件包括汽車輪緣、輪輻、皮帶輪;化工容器、封頭、氣瓶、真空泵器件;冶金採礦用超寬板、無縫管、礦井支柱以及壓力鍋、杯、盤、兌酒器等家用器皿。經強旋工藝加工後的零件精度高、光度好、壁厚均勻,中小零件的直徑和公差可控制在0.03-0.05mm範圍內,表面粗糙度可小於0.8μm,材料節約達20-50%。
技術難點
難點分析
由機械或液壓方式控制的強力旋壓工具機存在著調整費時,操作不便的問題,而且產品的表面質量有待提高,重複精度不高。
解決方法或途徑:1.採用電子監控裝置,使產品壁厚、直徑、橢圓度和平直度都達到最小公差;2.利用機器人上下料。3.推廣數控或計算機控制型工具機。4.進一步發展示教錄返型旋壓工具機
旋壓的特點是:用很小的變形力可成形很大的工件;使用設備比較簡單,中小尺寸的薄板件可用普通車床旋壓;模具簡單,只需要一塊芯模,材質要求低。旋壓適用於小批生產,因其只能加工旋轉體零件,局限性較大,生產率低。旋壓可用專門機械,採用仿形旋壓和數字控制旋壓。
優點
在旋壓成形的同時使板厚減薄的工藝稱為變薄旋壓,又稱強力旋壓,多用於加工錐形件、薄壁的管形件等,也可用以旋壓大直徑的深筒,再剖開後製成平板。
旋壓加工的優點是設備和模具都比較簡單(沒有專用的旋壓機時可用車床代替),除可成形如圓筒形、錐形、拋物面形成或其它各種曲線構成的旋轉體外,還可加工相當複雜形狀的旋轉體零件。缺點是生產率較低,勞動強度較大,比較適用於試製和小批量生產。
隨著飛機、火箭和飛彈的生產需要,在普通旋壓的基礎上,又發展了變薄旋壓(也稱強力旋壓)。