簡介
翻滾式艙蓋通常採取從當中對分的布置,通過固定安裝的輪子和導軌分兩半滾到艙口的兩側或前後兩端。存鬆開夾扣之後,開始滾動之前,必須用裝在艙口蓋上或艙口圍板上的專用舉升機械設備或輕便可移式手動千斤頂把艙蓋頂升起來,使橡皮墊料同艙口圍板頂的承壓密封邊材脫離接觸。關閉艙蓋時則採取相反的操作程式。
結構組成
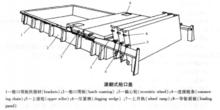
滾翻式艙口蓋由蓋板、水密裝置、滾輪裝置、導向曳行裝置和壓緊裝置5部分組成。各蓋板之間用鏈條連線,每一塊蓋板上都有一對行走滾輪(偏心輪),可沿艙口圍板兩邊的面板行走,還有一個平衡輪,它不設定在板寬的中點處。當蓋板進人艙口端的收藏坡道時,在重力作用下蓋板便翻轉成直立狀態而存放,艙口較長時可將全部蓋板分成兩半,開啟後,分別存放在艙口的兩端,如圖1所示。
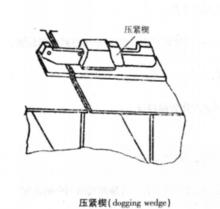
關閉時,將鋼索穿入在艙口正前方的開口導向滑車內,再用卸扣與收藏處的首端蓋板相連線。操縱起貨絞車或克令吊,絞動鋼索拖帶前面的一塊蓋板,導輪沿導板滾動,繼後蓋板之間相互由鏈條拉動。當蓋板後部滾輪與導板接觸後,則蓋板繞導輪軸轉動,直至其銜接輪與前塊蓋板上的銜接輪座吻合為止。以後繼續沿艙口圍板水平材上滾動,至首端蓋板與止動器相碰時為止。艙蓋就位後,翻轉偏心滾輪至偏心位置,艙蓋四周下面的橡膠水密條壓在艙口圍板上,保證艙口水密,打上壓緊楔及壓緊器以防艙蓋移動,如圖2和圖3所示。
滾翻式艙蓋最大優點是結構比較簡單,相對於其他類型的機械艙蓋它價格便宜,便於(分塊)維修,在尺度、布置和用途上限制較少,因而在各種類型的船上獲得最為廣泛的套用。它的不足之處是所需的存放空間較大,提升及壓緊作業所需的時間也較長。
以下介紹滾翻式艙蓋的開關操作及注意事項。
機械牽引式滾翻式艙蓋開關操作
開關艙操作人員由水手長或值班駕駛員調配,指定一人操縱起貨機,並按操作規程使起貨機處於使用狀態。
開艙操作
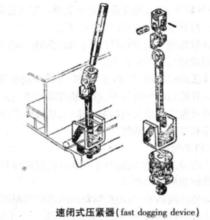
①將壓緊裝置(艙蓋上的壓緊楔和艙口周圍的壓緊器)打開。
②操縱兩側液壓千斤頂將艙蓋頂起,使滾輪頂板與軌道齊平,或用撬槓頂起將滾輪中心轉到上方。
③將曳艙蓋鋼絲繩穿過導向滑車後纏繞在起貨機的捲筒上或掛在起貨鉤上。
④在水手長或值班駕駛員的指揮下,操縱起貨機絞收曳艙蓋鋼絲繩,曳動首端蓋板及拉動其他蓋板向後移動,使蓋板全部滾至導板上,最後直立在艙口一端的艙蓋收藏處。
⑤扣住艙蓋制動索,整理好索具。
關艙操作
關艙操作步驟和開艙操作相反。
①將曳艙蓋鋼絲繩穿過導向滑車後纏繞在起貨機的捲筒上或掛在起貨鉤上。
②解脫艙蓋制動索。
③在水手長或值班駕駛員的指揮下,操縱起貨機絞收曳艙蓋鋼絲繩,曳動首端蓋板及拉動其他蓋板沿軌道滾動,直至首端蓋板與制動器相觸為止。
④艙蓋板合攏後,用千斤頂使滾輪落入槽內,蓋板便壓在艙口上。
⑤將兩側的壓緊器壓緊,蓋板上的壓緊楔插牢。整理好索具。
液壓啟閉式滾翻式艙蓋開關操作
開艙操作
①啟動油泵,空載運行5~10 min,使油溫升高到正常工作溫度。特別是在冬季,因油溫低,黏度較大,急於操作會使油泵的排出壓力過高,發生事故。
②打開壓緊器,打開導軌制動鎖。
③拔出制動銷,扳動控制箱內的換向控制閥右移,將導軌升起。將換向閥回到中間位置,並將制動銷插到制動板孔中。
④按動控制箱中“開啟”按鈕,開動驅動機開啟艙蓋。
⑤開艙後將導軌落下,以防裝卸貨時碰損。
⑥開艙完畢後關閉油泵停車後,應扳動手動旁通閥使管路釋壓。
⑦扣牢艙蓋制動鏈。
關艙操作
①啟動油泵,空載運行5~10 min,使油溫升高到正常工作溫度。
②解脫艙蓋制動鏈。
③拔出制動銷,扳動控制箱內的換向控制閥右移,將導軌升起。將換向閥回到中間位置。
④按動控制箱中“開啟”按鈕,開動驅動機關閉艙蓋。
⑤將導軌放下,將各壓緊器壓緊。
⑥當艙內裝壓載水或礦、油多用船艙內裝油時,應使用螺旋壓緊裝置。
⑦關艙完畢後關閉油泵停車後,應扳動手動旁通閥使管路釋壓。
開關艙注意事項
(1)操作者要聽從指揮,集中精力。
(2)艙口兩側的壓緊器拆下後,必須放置在一定位置,以免阻礙滾輪,開艙前必須仔細檢查,軌道上不能有障礙物。
(3)開關艙前,必須檢查蓋板頂部壓緊楔,並使其全部處於拆開位置,用鐵銷插牢,操作中插銷不能使自動脫出。如在操作中發現有插銷脫出,操作人員不得上艙蓋調整,應將艙蓋板平置於艙口後再上去調整,並用鐵銷插牢。
(4)操縱起貨機要緩、穩,要特別注意首部蓋板,曳行速度要慢。如操作不當,往往首部蓋板易脫軌而影響開關艙進行。
(5)蓋板之間相連的鐵鏈應保持兩面對稱,否則因兩側拉力不對稱,會使艙蓋板脫軌。
(6)船舶縱傾時,關艙要注意防止蓋板向下傾方向自由滑動。
(7)如船舶橫傾較大,要特別注意防止艙蓋板脫軌。必要時套用壓載水調整後再進行開關艙操作。
(8)開艙後,必須用固定鉤或鏈條將蓋板固定,防止滑脫。
(9)開關艙操作中如發生蓋板脫軌,可利用吊桿或機械差動絞轆,將蓋搬吊起調整好位置,重放在艙口上,移正後便可繼續操作。
(10)在開關艙時,所有操作人員要注意安全操作,防止發生事故。