簡介
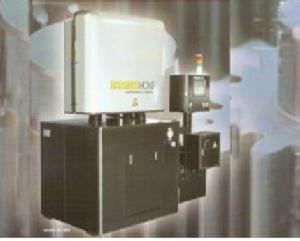
工件夾持在夾具中,把流動的介質導向工件所需磨掉的部位,而其它部分不受影響。夾具緊固在對置的介質圓柱筒間,讓磨料介質來回流動。
技術組成
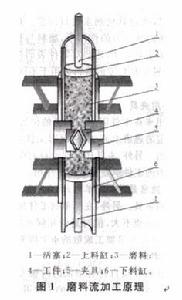
磨料流加工工具機是在加工過程中用來將零件和夾具固定在規定位置上,對研磨磨料施加擠壓力的裝置。它通常由主機、液壓系統及控制系統組成。主機的主要部分是兩個相對的料缸,在液壓系統驅動下兩料缸可以開合。液壓系統驅動各液壓執行元件,完成料缸分合以及擠壓推動研磨磨料各動作。控制系統除了用來完成對液壓系統各電磁閥的控制外,還要完成對各加工參數,如對溫度、壓力、流動速度等的檢測。磨料流加工工具機在將磨料從一個料缸擠壓到另一個料缸的過程中,完成了被加工零件表面的研磨,磨料流加工技術具有文明人作簡單、調節方便、多功能等優點。
2、研磨用磨料
研磨磨料是磨料流加工中的刀具,它是一種以高分子粘彈性體為載體,摻人各種規格磨粒的半固狀物質,具有一定的流動性。磨料通常使用碳化矽、氧化鋁、金剛石等,要求磨料具有一定的流動性,不粘、無毒、不掉砂。研磨磨料最主要的性能指標是粘度,粘度可以通過軟化劑來進行調整。在磨料流加工工具機產生的擠壓力的作用下,磨料與被加工零件的表面產生相對運動,達到對零件表面的研磨拋光效果,不同種類和粒度的磨料可用於不同的材料、形狀及要求。
3、工件用夾具
夾具用來將工件固定在規定的位置上,並導引磨料在指定的通道上流動,從而對工件表面進行拋光或倒圓角。另外,夾具還起到密封的作用,也對不能承受壓力的工件承受壓緊力的作用。在小批量生產中,夾具通常是比較簡單的,而大批量生產應設計一次多件的夾具。另外,在簡單的工件加工中,夾具起到的作用可能不大,但對複雜幾何形狀的工件加工來說,夾具往往是加工成敗的重要因素。
4、工件清理
由於磨料介質自身有很強的內聚力,客觀上它具有不粘金屬的性能。加工完的工件可以用手輕鬆地將大部分的磨料剝離下來,這些被剝離下來的磨料可收起來以備重複使用,殘留在工件上的磨料採用超音波振動、壓縮空氣吹、汽油清洗就可以除淨。
優點
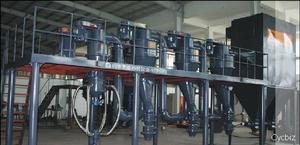
套用
磨料流加工是20世紀60年代由美國兩公司獨立發展起來的,最初套用於航空、航天領域的複雜幾何形狀合金工件的去毛刺加工。隨著科學技術的飛躍發展,在宇航、飛彈、電子、計算機等精密機械零件的工藝性能要求不斷提高的情況下,以前用手工、機械、化學等方法對零件表面進行拋光、倒角、去毛刺均有其局限性,特別是對零件內小孔徑、相互交叉的孔徑及邊棱進行拋光、倒角、去毛刺更是無能為力;而磨料流加工技術由於具有對零件隱蔽部位的孔、型腔研磨、拋光、倒圓角的作用,又有對外表面各種複雜型面研磨、拋光的能力,因而具有其它方法無法比擬的優越性。目前,這項技術已套用在宇航和兵器工業,同時也擴展到了紡織、醫療、縫紉、精密齒輪、軸承、模具製造等其它機械行業。關鍵技術
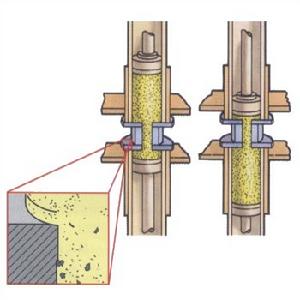
磨料流流體介質是由載流體(基體)和磨料組成,是一種在一定壓力下可流動的粘彈性半固狀物質,具有可塑性和彈性,無毒、無臭,不污染環境。磨料流流體介質的規格按基體的粘度、磨料材質、磨粒粒度和磨料含量來確定。
基體是由一種具有粘彈性的半固態的高分子聚合物加上凝膠(軟化劑)、潤滑劑等配製而成。基體的粘度是介質的主要特性,聚合物與凝膠的配製比例不同,基體的粘度也就不同,在配製時,可以按加工要求把高、低兩種標準粘度的基體均勻混合製成中間濃度的基體,不同的介質基體粘度對加工效果有較明顯的影響。
根據被加工工件材料和表面粗糙度要求的不同,磨料流體介質中混合的磨料種類、粒度以及所含磨料的濃度有所不同,選擇原則與磨削時砂輪粒度的選擇相近,磨料的粒度一般採用20號~50號,常用80號~150號。粗磨料用於去除毛刺,細磨料用於拋光、光整表面。在實際套用中,經常是幾種粒度的磨料混合使用。
在一定範圍內,增加磨料流體介質中的磨料含量有利於加工效率的提高;但隨著磨料含量的增加,介質的粘度也會產生一定的變化,故需要根據被加工工件的要求來配製不同濃度的磨料流體介質。
磨料流體介質的粘度應根據不同的工件加工要求來進行調配,粘度較低的磨料流體介質在受擠壓通過孔道時,會對工件棱邊部分形成急劇的滑動摩擦作用,去除毛刺和倒角的作用較強。而粘度較高的磨料流體介質,由於其流動性不好而形成一種受剪下的狀態,對孔壁有較強的滑動摩擦作用,拋光表面用較好。在調配磨料流體介質時,可根據需要加入不同的添加劑,如增塑劑、減粘劑、潤滑劑等,以滿足不同材料、不同形狀工件的加工質量要求。
磨料流體介質在常溫下長時間保存而不硬化,使用壽命一般為200h~300h。使用一段時間後,由於磨料會逐漸鈍化而失去切削能力,且在基體介質中也會產生過量的金屬碎屑,因此需要定時清除和更換。
2、加工工藝參數的選擇
磨料流加工時的工藝參數有擠壓力、循環次數和加工時間等。擠壓力對材料去除率和表面粗糙度的影響較大,在一定範圍內提高擠壓力會較明顯地改善加工效果。加工時的擠壓力一般為1MPa~3MPa,也有根據要求達到10MPa的。工件加工時的往復循環次數和加工時間應根據被加工工件的材料和表面粗糙度要求,經過多次加工試驗後最終確定,不同的加工工序需要有不同的工藝參數設定。
3、各種因素的綜合影響
由於影響磨料流加工的因素眾多,而這些因素在加工時又會相互影響,使磨料流加工時對工藝參數的設定就變得相當困難。目前在這方面也沒有可依據的公式和圖表,在具體加工時就需要通過多次加工試驗,來確定最佳的工藝參數設定。
在噴絲板微孔加工中套用
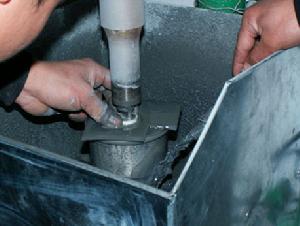
在對噴絲板進行微孔鑽削加工時,噴絲板的微孔內表面會留下毛刺,進而會影響到絲條的質量和正常生產。傳統進行處理的方法只是在紡絲熔體通過噴絲板微孔噴擠出的自然作用下,對噴絲板微孔進行去除毛刺和表面的拋光,這種方法會造成紡絲前期過程不穩定,纖維出現斷頭,紡絲質量不好。為了改進工藝,引入了國外磨料流加工技術。由於磨料流加工技術具有對零件隱蔽部位的孔及型腔研磨拋光、倒圓角的作用,因而在噴絲板微孔的加工中,特別對於長徑比大的微孔能起到很好的加工效果,具有其它加工方法無法比擬的優越性。
與一般的傳統拋光工藝比較,磨料流加工技術在對噴絲板微孔的加工中具有以下兩方面的優勢:噴絲板微孔的加工、特別是對於長徑比較大的深孔,是孔加工中較難進行的,由於尺寸上所受的限制,傳統的加工手段較難以勝任,而磨料流加工中的刀具---流體磨料具有隨機流動性,可添加軟化劑來進行調整,到達區域能夠不受限制;因此,用磨料流技術來加工微孔時能具有較大優勢。另外,用一般的拋光工藝進行加工時所採用的磨料,如金剛砂之類在對工件孔腔進行拋光加工時,會對小孔的孔口處產生一個較大的法向壓力,因而會在孔口處產生喇叭口形狀的加工誤差。而磨料流加工技術所採用的粘彈性磨料由於其具有入口收斂作用,即當粘彈性磨料流體從大截面流道進人工件孔道時,會由於流體的粘彈特性和流道截面的突然收縮,以及自身的粘彈力學特性,而在工件孔道流動中產生相應的彈性應變能的貯存及其粘性耗散,出現明顯的人口壓力下降,從而能夠較好地解決微孔拋光加工中易出現喇叭口的加工工藝問題。
在齒輪修緣中套用
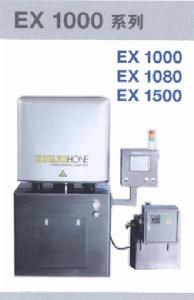
磨料流加工齒輪修緣技術屬於磨料流加工齒輪加工技術範疇, 一種用磨料流加工技術進行齒輪修形技術方案,主要包括工具機設計、磨料配製、專用夾具設計,其特徵 於專用夾具 設計,由上、下端蓋 夾具體組成,其夾具體 一個與被修形齒輪 模數、齒數、變位係數都相同 內齒輪, 夾具體齒根部,分別開啟三角形小槽與被加工齒輪形成三角形直通道。其該項技術,生產率高、設備簡單、操作方便、易於套用推廣。