熱熔直壓
指聚乙烯在塑化擠出機中熔融後經擠出機頭分流擴散形成薄膜,隨後與織物增強層一同進入三輥壓延機進行產品厚度確定的一種生產工藝,目前主要套用於SBC
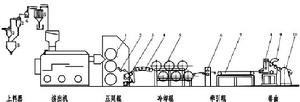
熱熔直壓工藝流程
SBC防水卷材擠出壓延生產工藝流程
主要由高速混合機、擠出機、壓延機和牽引機、捲曲機組組等組成。參見上圖
影響熱熔直壓工藝質量的因素
影響壓延製品質員的因素很多,一般說來,可以歸納為四個方面。即擠出壓延的操作因素,原材料因素,設備因素和輔助過程中的各種因素。所有這些因素對防水卷材的影響都是相同的。下面以聚乙烯丙綸防水卷材生產工藝(熱融直壓工藝)為例來說明各種因素的影響。
(一)、壓延機的操作因素
1、輥溫與輥速
物料在壓延成型時所需的熱量,一部分是壓延輥提供的,另一部分來自物料在擠出機內與螺桿壁的摩擦以及物料本身的剪下作用產生的熱量。產生摩擦熱的大小除與輥速有關外,還與物料的增塑程度有關,也即與其粘度有關。因此,不同的物料,在相同的輥速條件下,其溫度控制就不同,同樣,相同配方不同的轉速時,其控制溫度也不同。
2、壓延輥的速比 壓延機相鄰兩輥筒線速度之比稱為輥簡的速比。使壓延機具有速比的目的,不僅使壓延物依次貼於輥簡,而且還在於使塑膠能更好地塑化,因為這樣能使物料受到更多的剪下作用。此外,還可以位壓延物取得一定的拉伸與取向,從而使所制薄膜厚度減小和複合(聚乙烯與丙綸織物)質量提高。為了達到拉伸與取向的目的,輔機與壓延機輥簡速度也有相應的速比。薄膜冷卻後要儘量避免拉伸。
3、輥距與存料量 調節輥距的目的是為了適應不同厚度製品的要求,也是為了改變存料量。壓延機的輥距,除最後一道與產品厚度大致相等之外,其它各道都比這個數值要大,而且按壓延機輥筒的排列次序自上而下逐漸減少,藉以使輥筒間隙中有少量存料,輥隙存料在壓延成型中起儲備.補充的作用。存料過多對設備也不利,因為增加了輥筒的負荷。若存料過少,則因壓力不足造成薄膜表面毛糙。所以可知輥隙存料是壓延操作中需要經常觀察和調節的。
(二)、原材料因素
1、樹脂
一般說來,使用分子量較高和分子量分布較窄的樹脂較好,可以得到物理力學性能好的,熱穩定性高和表面均勻性好的製品,但會增加壓延溫度和對設備負荷,對生產較薄的膜更為不利,所以在設計配方時要進行多方面考慮,選用適用的樹脂。 近幾年來為了提高產品的質量,用於壓延成型的樹脂有了很大的發展,用本體聚合的樹脂產品透明度好,吸收增塑劑效果也好。此外通過樹脂與其它材料的摻合改性和單體接枝成段共聚,從而得到性能更好的樹脂。
2、其它組分
配方中對壓延成型影響較大的是增塑劑和穩定劑。增塑劑含量越多,物料的粘度就越低,因此在不改變壓延機負荷下,可以提高輥簡轉速或降低壓延溫度。
採用不適當的穩定劑經常使壓延輥筒(包括花輥筒)表面蒙上一層蠟狀物質,致使膜面不光,生產中發生粘輥現象或在更換產品時發生困難。壓延溫度越高,這種現象越嚴重。出現蠟狀物質的原因,是由於穩定劑與樹脂的相容性太差,而且其分子極性基團的正電性較高,以致壓延時被擠出而包在輥子表面,形成蠟狀物。顏色、潤滑劑及氈合劑等原料也有形成蠟狀層的可能,但不如穩定劑嚴重。
(三)設備因素
操作時,壓延輥受塑膠的反作用力,這種能使兩輥簡分開的力也稱為分離力或橫壓力,分離力導致輥筒變形,產品出現中間厚兩邊薄的現象。如果用高粘度的塑膠,增大壓延輥的直徑和寬度,提高線速度和生產簿型製品,都將導致分離力提高,產品厚度均勻性下降。解決的方法:中高度法、軸交叉法、預應力法。
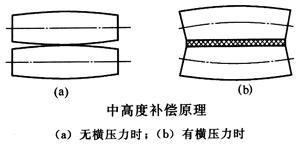
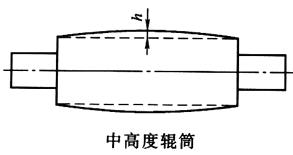

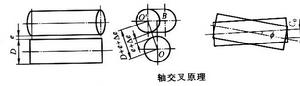
(四)、冷卻定型階段影響產品的因素
1、冷卻
冷卻必須適當,當冷卻不足時,卷材會發皺,卷取後收縮率也大;若冷卻過度,輥筒表面處會因溫度過低而有冷凝水珠也會影響製品質量。
2、冷卻輥流道的結構
冷卻輥進水端輥面溫度必然低於出水端,所以卷材兩端冷卻的程度不同,收縮率也就不一樣。解決的辦法是改進冷卻輥的流道流向結構,務必使冷卻輥表面溫度均勻一致。