工作原理
典型的熱管由管殼、吸液芯和端蓋組成,將管內抽成1·3×(10負1---10負4)Pa的負壓後充以適量的工作液體,使緊貼管內壁的吸液芯毛細多孔材料中充滿液體後加以密封。管的一端為蒸發段(加熱段),另一端為冷凝段(冷卻段),根據套用需要在兩段中間可布置絕熱段。
當熱管的一端受熱時毛紉芯中的液體蒸發汽化,蒸汽在微小的壓差下流向另一端放出熱量凝結成液體,液體再沿多孔材料靠毛細力的作用流回蒸發段。如此循環不己,熱量由熱管的一端傳至另—端。熱管在實現這一熱量轉移的過程中,包含了以下六個相互關聯的主要過程:
(1)熱量從熱源通過熱管管壁和充滿工作液體的吸液芯傳遞到(液---汽)分界面;
(2)液體在蒸發段內的(液--汽)分界面上蒸發;
(3)蒸汽腔內的蒸汽從蒸發段流到冷凝段;
(4)蒸汽在冷凝段內的汽·液分界面上凝結:
(5)熱量從(汽--液)分界面通過吸液芯、液體和管壁傳給冷源:
(6)在吸液芯內由於毛細作用使冷凝後的工作液體回流到蒸發段。
熱管分類
由於熱管的用途、種類和型式較多,再加上熱管在結構、材質和工作液體等方面各有不同之處,故而對熱管的分類也很多,常用的分類方法有以下幾種。
溫度區分
按照熱管管內工作溫度區分,熱管可分為低溫熱管(—273---0℃)、常溫熱管(0—250℃)、中溫熱管(250---450℃)、高溫熱管(450一1000℃)等。
回流動力區分
按照工作液體回流動力區分,熱管可分為有芯熱管、兩相閉式熱虹吸管(又稱重力熱管)、重力輔助熱管、鏇轉熱管、電流體動力熱管、磁流體動力熱管、滲透熱管等等。
組合方式劃分
按管殼與工作液體的組合方式劃分,(這是一種習慣的劃分方法)可分為銅—水熱管、碳鋼—水熱管、銅鋼複合—水熱管、鋁—丙酮熱管、碳鋼·榮熱管、不鏽鋼·鈉熱管等等。
結構形式區分
按結構形式區分,可分為普通熱管、分離式熱管、毛細泵迴路熱管、微型熱管、平板熱管、徑向熱管等。
功用劃分
按熱管的功用劃分,可分為傳輸熱量的熱管、熱二極體、熱開關、熱控制用熱管、仿真熱管、製冷熱管等等。
製造介紹
(1)熱管零部件及其加工
熱管的主要零部件為管殼、端蓋(封頭)、吸液芯、腰板(連線密封件)四部分。不同類型的熱管對這些零部件有不同的要求。
(2) 管殼
熱管的管殼大多為金屬無縫鋼管,根據不同需要可以採用不同材料,如銅、鋁、碳鋼、不鏽鋼、合金鋼等。管子可以是標準圓形,也可以是異型的,如橢圓形、正方形、矩形、扁平形、波紋管等。管徑可以從2mm到200mm,甚至更大。長度可以從幾毫米到l00米以上。低溫熱管換熱器的管材在國外大多採用銅、鋁作為原料。採用有色金屬作管材主要是為了滿足與工作液體相容性的要求。
(3) 端蓋
熱管的端蓋具有多種結構形式,它與熱管舶連線方式也因結構形式而異。端蓋外圓尺寸可稍小於管殼。配合後,管殼的突出部分可作為氬弧焊的熔焊部分,不必再填焊條,焊口光滑乎整質量容易保證。鏇壓封頭是國內外常採用的一種形式,鏇壓封頭是在鏇壓機上直接鏇壓而成,這種端蓋形式外型美觀,強度好、省材省工,是一種良好的端蓋形式。
(4)吸液芯結構
吸液芯是熱管的一個重要組成部分。吸液芯的結構形式將直接影響到熱管和熱管換熱器的性能。近年來隨著熱管技術的發展,各國研究者在吸液芯結構和理論研究方面做了大量工作,下面對一些典型的結構作出簡賂的介紹。
管芯型式
一個性能優良的管芯應具有:
(1)足夠大的毛細抽吸壓力,或較小的管芯有效孔徑
(2)較小的液體流動阻力,即有較高的滲透率
(3)良好的傳熱特性,即有小的徑向熱阻.
(4)良好的工藝重複性及可靠性,製造簡單,價格便宜。
管芯的構造型式大致可分為以下幾類:
(1)緊貼管壁管芯
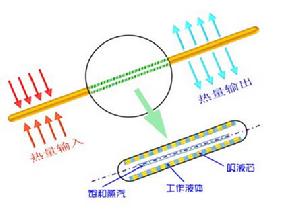
多層網的網層之間應儘量緊貼,網與管壁之間亦應貼合良好,網層數有l至4層或更多,各層網的目數可相同或不同,若網層多,則液體流通截面大,阻力小,但徑向熱阻大;用細網時毛細抽吸力大但流動阻力亦增加.如在近壁因數層用粗孔網,表面一層用細孔網,這樣可由表面細孔網提供較大的毛細抽吸壓力,通道內的粗孔網使流動阻力較小,但並不能改善徑向熱膽大的缺點.網芯式結構的管芯可得到較高的毛細力和較告的毛細提升高度,但因滲透率較低,液體回流阻力較大,熱管的軸向傳熱能力受到限制.此外其徑向熱阻較大,工藝重複性差又不能適應管道彎曲的情況,故在細長熱管中逐漸由其它管芯取代。
(2)燒結粉末管芯
由一定目數的金屬粉末燒結在管內壁面而形成與管壁一體的燒結粉末管芯,也有用金屬絲網燒結在管內壁面上的管芯.此種管芯有較高的毛細抽吸力,並較大地改善了徑向熱阻,克服了網芯工藝重複性差的缺點,但因其滲透率較差,故軸向傳熱能力仍較軸向槽道管芯及幹道式管芯的小。
(3)軸向槽道式管芯
在管殼內壁開軸向細槽以提供毛細壓頭及液體國流通道,槽的截面形狀可為矩形,梯形,圓形及變截面槽道,槽道式管芯雖然毛細壓頭較小,但液體流動阻力甚小,因此可達到較高的軸向傳熱能力,徑向熱阻較小,工藝重複性良好,可獲得精確幼兒何參數,因而可較正確地計算毛細限,此種管子彎曲後性能基本不變,但由於其抗重力工作能力極差,不適於傾斜(熱端在上)工作對於空間的零重力條件則是非常適用的,因此廣泛用於空間飛行器。
(4)組合管芯
一般管芯往往不能同時兼顧毛細抽吸力及滲透率,為了有高的毛細抽吸力,就要選用更細的網成金屬粉末,但它仍的滲透率較差,組合多層網雖然在這方面有所提高,可是其徑向熱陰大。組合管芯躍能兼顧毛細力和滲透率,從而能獲得高的軸向傳熱能力,而且大多數管芯的徑向熱阻甚小。它基本上把管芯分成兩部分,一部分起毛細抽吸作用,另一部分起液體回流通道作用。
重力熱管制作工藝
目前節能(餘熱回收)領域的熱管換熱器,常用熱管多為重力熱管。重力熱管主要由管殼、端蓋、工質三部分組成,其通常製作工藝如下:
1、機械加工(管殼、端蓋,或者直接採購)——2、前處理(管殼、端蓋除油除銹)——3、烘乾——4、端蓋焊接(氬弧焊,焊口打磨)——5、充裝工質——6、排空氣(烘烤)——7、封頭焊接(氬弧焊)——8、檢驗
關鍵工序為:6、排空氣,7、封頭焊接
製造工藝
吸液芯型熱管
如前所述,構成熱管的三個主要組成部分是管殼、管芯和工質。在設計過程中,對管殼和管芯的材料進行合理的選擇後就可以開始製作。通常熱管的製造過程包括下面的工藝操作,並按一定的程式進行。
1、機械加工---2、清洗---3、管芯製作---4、清洗---5、焊接---6、檢漏----7、除氣---8、檢漏---9、充裝---10、封接---11、烘烤---12、檢驗
實際製造的時候往往能達到20,甚至上百道的工序。這裡只是最簡單的一些必須工序。
重力熱管
節能(如 定型機餘熱回收)領域的熱管換熱器,常用熱管多為重力熱管。重力熱管主要由管殼、端蓋、工質三部分組成,其通常製作工藝如下:
1、機械加工(管殼、端蓋,或者直接採購)——2、前處理(管殼、端蓋除油除銹)——3、烘乾——4、端蓋焊接(氬弧焊,焊口打磨)——5、充裝工質——6、排空氣(烘烤)——7、封頭焊接(氬弧焊)——8、檢驗
關鍵工序為:6、排空氣 7、封頭焊接